Advances in space technology and manufacturing processes have helped to lower costs and reduce entry barriers to space. Still, space is expensive. Today, all spacecraft are developed, tested, and assembled on Earth before being launched to orbit, and getting components and technologies flight-ready is difficult and pricey.
For years, experts have proposed 3D printing and in-situ manufacturing as a viable solution to avoid these costs. However, besides the advanced additive manufacturing (AM) technologies deployed for research on the International Space Station (ISS), we still have not seen spacecraft built in orbit. A group of university students hopes to change after successfully demonstrating a 3D printing process that could be used to produce structures for solar panels, antennas, and other installations in orbit.
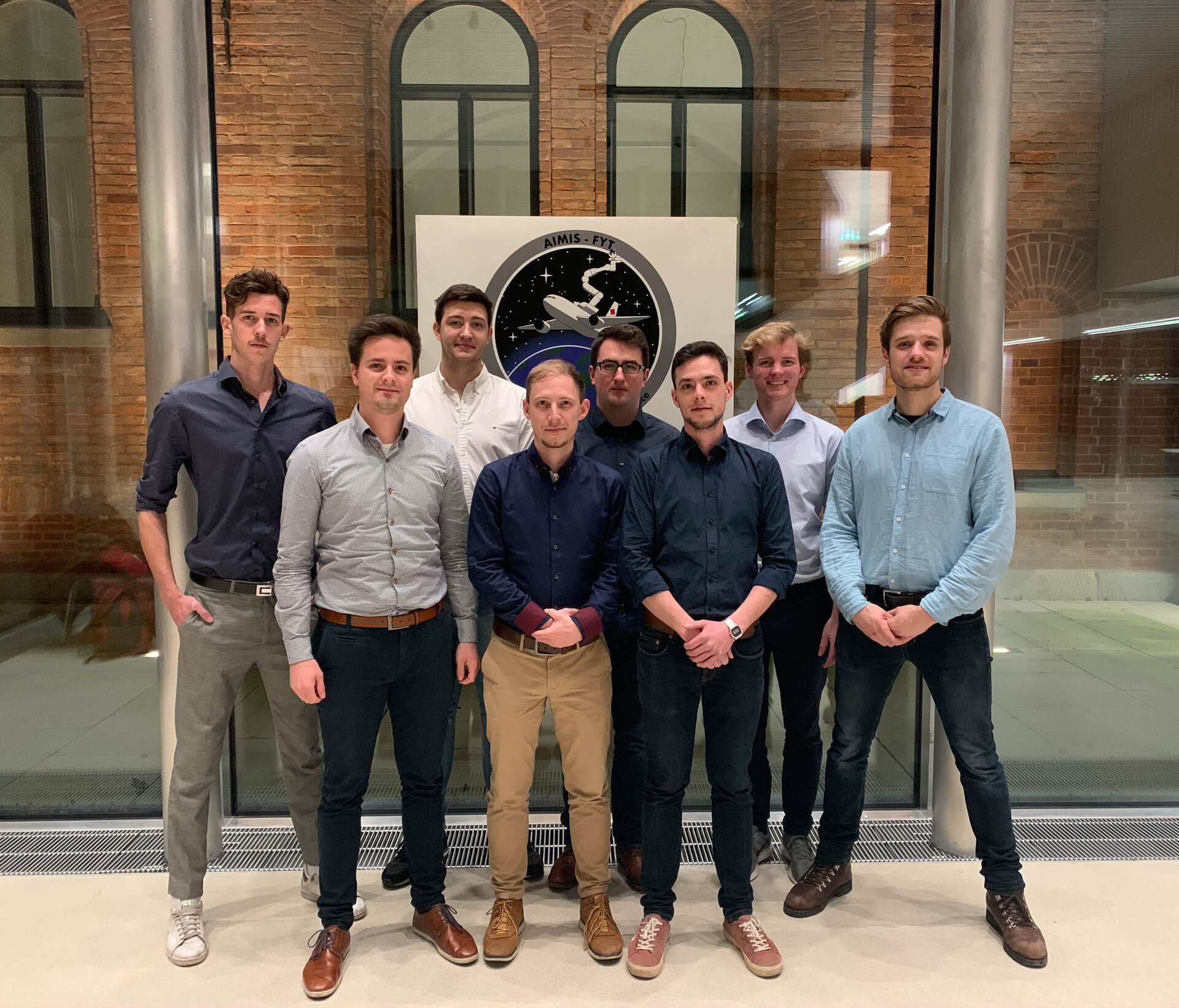
AIMIS-FYT team of students: Michael Kringer, Nils Torben Schaefer, Christoph Boehrer, Moritz Frey, Fabian Schill,Julius Frick, Manuel Kullmann and Maximilian Strasser. Image courtesy of ESA/AIMIS-FYT.
Eight aerospace engineering students of the Munich University of Applied Sciences have explored new approaches for manufacturing directly in space thanks to a European Space Agency (ESA)-supported program called “Fly your Thesis!” (FYT), which offers students a once in a lifetime opportunity to propose, design, build, test and fly their research in microgravity conditions during parabolic flight. For the project, the Additive Manufacturing In Space (AIMIS)-FYT team built a 3D printer with an extruder to dispense a liquid photopolymer. Rather than creating components layer by layer as conventional 3D printers do, the components are created directly via the 3D movement of a printing head from dosing technology developer ViscoTec and cured within a short period by applying UV light.
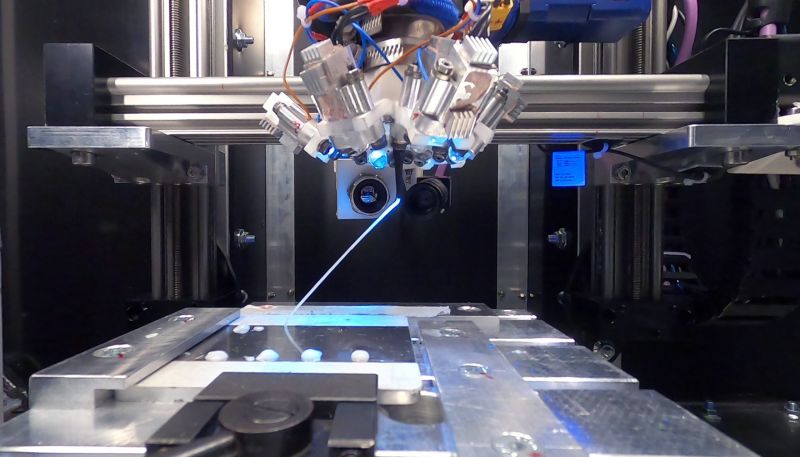
3D printing in zero gravity during the ESA’s parabolic flight campaign. Image courtesy of AIMIS-FYT.
In November 2020, eight experiments took off on the ESA’s 74th parabolic flight campaign from Paderborn-Lippstadt Airport in Germany. Almost all the experiments worked, some even better than expected, according to AIMIS-FYT team members Michael Kringer and Christoph Böhrer. More importantly, they were able to show that the printing process works under zero-gravity conditions successfully. For ViscoTec, the experiment also revealed that the vipro-HEAD 5 printhead used – described by the students as “the heart of the printer” – is suitable for use in microgravity.
During the 90 parabolas, the experiments were divided into different basic operation types to create straight rods, straight rods with start and stop points, free-floating rods, and connections between rods. For the first six operation types, a conventional printing plate was used as the starting point for the print. Kringer and Böhrer said that they also printed rods at an angle and tested different approaches for the nozzle during the straight rod experiments. They wanted to see “to what extent a shear flow at the nozzle outlet affects the printing process.” Even though they reported that rods at an angle with overhang are much more difficult to print under normal gravity conditions, in zero gravity, printing operations at an angle “have proven to be very successful.”
In addition, certain parameters of the printing process were systematically changed from trial to trial to identify deteriorations and improvements in the printing process. The main parameters of the printing process are the extrusion speed of the resin, UV-light intensity, UV-light time, and trajectory of the printer. The number of parameters and the possibilities of how a rod can be printed showed that even a simple straight rod could quickly become complex.
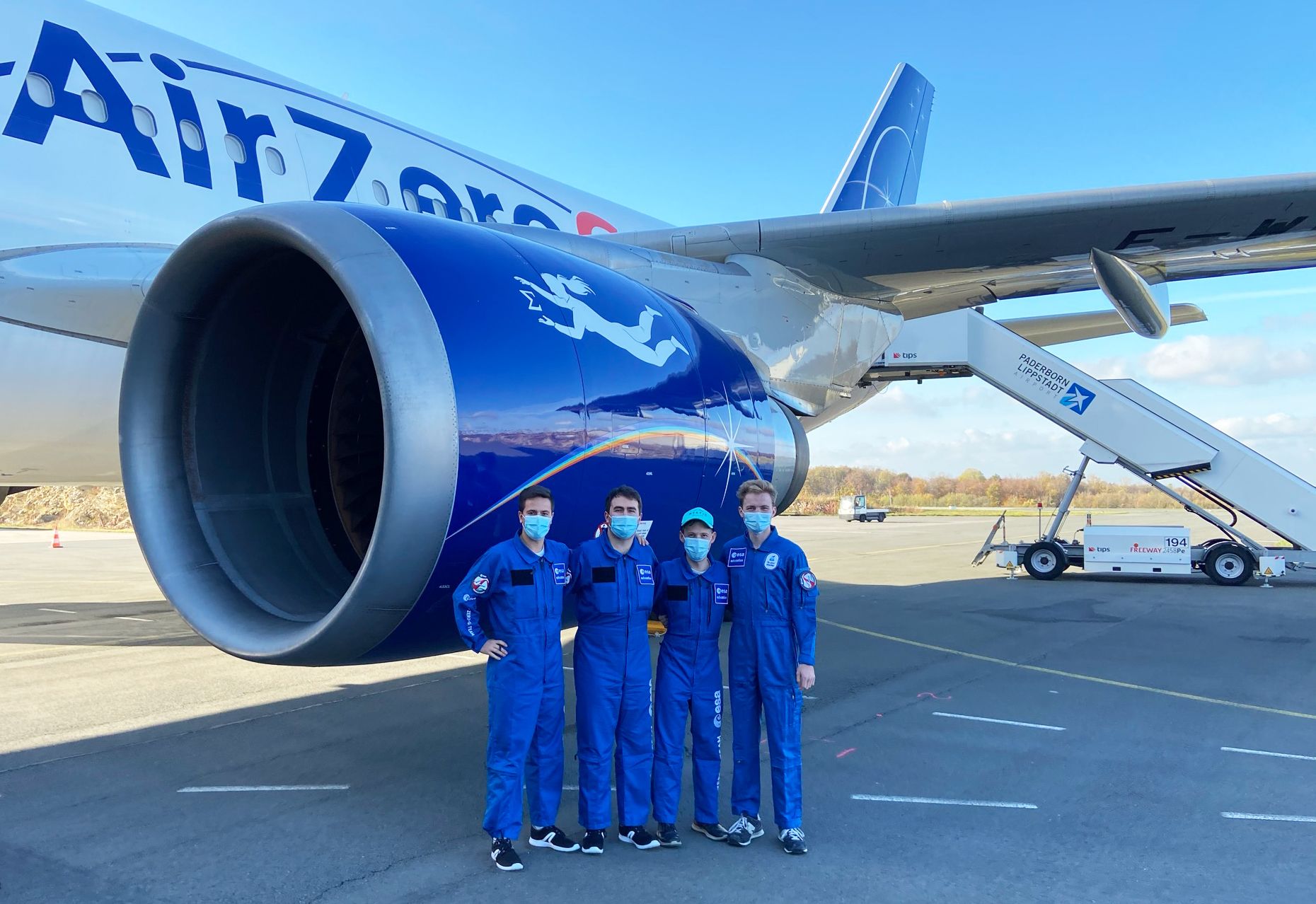
The AIMIS-FYT team, before taking off on ESA’s parabolic flight campaign to explore new approaches for manufacturing directly in space. Image courtesy of ESA/AIMIS-FYT.
Aside from the ViscoTec print heads, the team also relied on conical UV-blocking dispensing needles from Vieweg; power supplies from PULS, including the highly efficient and compact 24V, 10A CP10.241 and 24V, 5A CS5.244, and an adhesive from Delo, also contributed to the success of the experiments. The team tested the resin long before the campaign and compared it with other adhesives, choosing for their experiment a catatonically. At the same time, fast curing resin with little volume shrinkage adhesive proved.
The entire printing process was monitored through cameras and sensors. AIMIS-FYT mounted a detailed camera and a thermal imaging camera to parallel the movement of the vipro-HEAD 5. At the same time, a high-resolution camera was used to observe the resin coming out of the nozzle permanently. The thermal imaging camera was used to document the exothermic reaction of the resin at the nozzle exit and along the rod. With the help of this data, the team expects to control better and optimize the printing process in future experiments.

The AIMIS-FYT team designed the schematic diagram of the experimental setup of the 3D printer. Image courtesy of AIMIS-FYT.
Even though all the operations were proven successful in zero gravity, 3D printing free-floating rods worked only to some extent. Without a printing plate as a fixed point, the printing process was unstable and prone to failure. Any slight deviation in microgravity immediately affected the direction of extrusion of the resin from the nozzle. According to the students, a more stable process would still have to be developed for the free-floating printing operation.
Once the first flight campaign was over, the ESA invited the team for another flight, this time a “Partial-g Campaign,” which allowed them to carry out the same experiments under lunar and Martian gravity conditions on another 90 parabolas. Kringer and Böhrer said that, in general, the 3D printing experiments showed that all pressure operations could be performed at any gravity, concluding that “there are not really any big differences” between Zero-G, lunar and Martian gravity.
The team also announced they would be developing an application for space systems based on the fundamentals gathered throughout the flight parabolas. The focus will be on further research. For example, one of the biggest challenges will be finding new material for printing in orbit that can be hardened in a vacuum while retaining its properties at both high and very low temperatures, and that is not attacked by atomic oxygen in the Earth’s residual atmosphere.
We have seen several 3D printing technologies launched to the ISS, like Made In Space‘s extrusion-based commercial platform, the Additive Manufacturing Facility (AMF), or its ceramics manufacturing facility. However, with so many missions planned to low Earth orbit, the Moon and Mars, developing more successful AM technologies that can be used directly in orbit could benefit off-Earth exploration in the future, reducing costs, offering more design flexibility, and increasing the lifetime of any space project. Team AIMIS-FYT’s successful experiment is a wonderful step forward, further proving that in-space manufacturing is possible and could help shape the future of spaceflight.
Subscribe to Our Email Newsletter
Stay up-to-date on all the latest news from the 3D printing industry and receive information and offers from third party vendors.
Print Services
Upload your 3D Models and get them printed quickly and efficiently.
You May Also Like
Reinventing Reindustrialization: Why NAVWAR Project Manager Spencer Koroly Invented a Made-in-America 3D Printer
It has become virtually impossible to regularly follow additive manufacturing (AM) industry news and not stumble across the term “defense industrial base” (DIB), a concept encompassing all the many diverse...
Inside The Barnes Global Advisors’ Vision for a Stronger AM Ecosystem
As additive manufacturing (AM) continues to revolutionize the industrial landscape, Pittsburgh-based consultancy The Barnes Global Advisors (TBGA) is helping shape what that future looks like. As the largest independent AM...
Ruggedized: How USMC Innovation Officer Matt Pine Navigates 3D Printing in the Military
Disclaimer: Matt Pine’s views are not the views of the Department of Defense nor the U.S. Marine Corps Throughout this decade thus far, the military’s adoption of additive manufacturing (AM)...
U.S. Congress Calls Out 3D Printing in Proposal for Commercial Reserve Manufacturing Network
Last week, the U.S. House of Representatives’ Appropriations Committee moved the FY 2026 defense bill forward to the House floor. Included in the legislation is a $131 million proposal for...