Space technology pioneer Maxar has been using additively manufactured parts in orbit since 2016. Since then, the company has launched more than 20 spacecraft with 3D printed parts made from aluminum, titanium, and plastic, totaling more than 2,500 components. As part of its successful strategy to incorporate 3D printed parts in its manufacturing process, Maxar recently celebrated a successful five-year partnership with New Zealand-based titanium 3D printing manufacturer Zenith Tecnica. The companies announced they have printed 260 titanium parts for five spacecraft and are currently producing more than 270 additional components for eight new satellites.
Recognized as one of the leading satellite manufacturing companies worldwide, 50-year old Maxar is seriously incorporating additive technologies to streamline its spacecraft manufacturing, increasing its 3D printed parts exponentially in just three years. During this time, the company has partnered with several AM-leading businesses. Aside from Zenith Tecnica, Maxar also used Stratasys machines to develop its GEO communication satellites, different AM applications, and materials specifically for space. Recently, Maxar collaborated with SWISSto12 to leverage the company’s innovative and complex 3D printing technology to create filters for the space market.
As the hype surrounding the commercial space industry continues to grow, this new milestone with Zenith Tecnica shows how increased adoption of AM technologies unlocks significant benefits for spacecraft manufacturing, such as enhanced performance and more efficient designs. 3D printed components are now standard for all satellites build by Maxar, with roughly 1,000 3D printed parts flying on any one of its spacecraft. The Westminster, Colorado-based business was an early adopter of 3D printing technologies, establishing its Additive Center of Excellence in 2012. It validated AM as an innovative and valuable approach for spacecraft manufacturing and identified a process for qualifying AM components for spaceflight.
As a result, electron beam melting (EBM) titanium was qualified for flight, and by 2016, the first EBM titanium components were on-orbit. Zenith Tecnica says it undertook a validation and qualification process to ensure the AM techniques and material were reliable. Eventually, the 3D printed titanium parts were built using GE Additive Arcam EBM machines and then heat-treated, while the critical assembly features were machined. Finally, to ensure all parts conform to specifications, 3D scanning inspections were performed.
“The team at Zenith Tecnica operates as an extension of Maxar’s team, and they always go the extra mile to ensure parts are delivered to a high standard of quality,” says Gina Ghiglieri Additive Manufacturing Technology Manager at Maxar. “Zenith Tecnica has been with us since the first metal additive manufacturing programs at Maxar and has performed a critical role in helping define and qualify these production processes.”
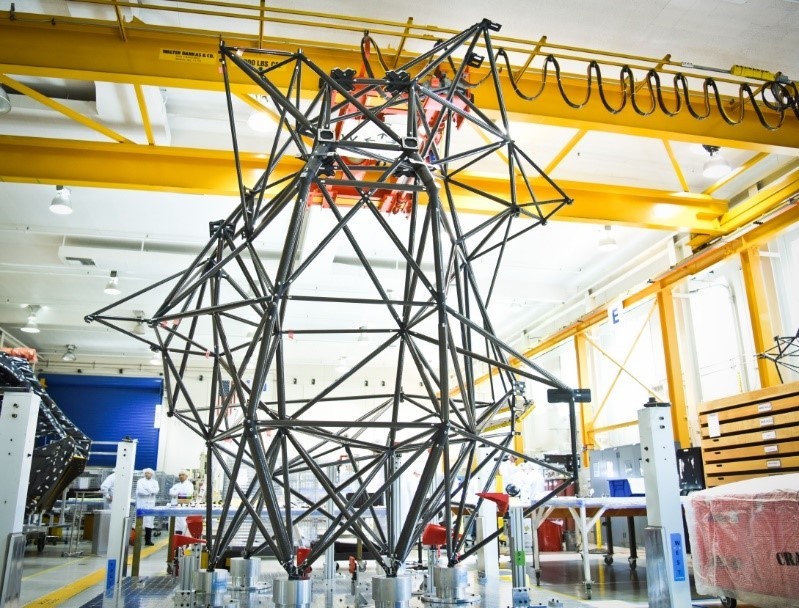
The Maxar-built Hispasat 30W-6’s antenna tower is comprised of over 200 additively manufactured parts. Image courtesy of Maxar.
Focused on manufacturing titanium hardware for many industries, Zenith Tecnica is taking advantage of AM’s mass customization and geometrical freedoms. Its 3D printed titanium parts can be found in everything from satellites, Air New Zealand aircraft, medical instruments, knee, and hip implants, even in America’s Cup yachts and Formula One race cars.
The company’s 15 mechanical engineers work with at least five GE Additive Arcam EBM machines at its Auckland facility to optimize hardware geometry and thermal characteristics for specific satellite features and payloads that customers, like Maxar, need. As we have seen happen in many industries, AM enables previously impossible designs through traditional manufacturing methods, plus additional benefits, like reduced part mass, fewer pieces of hardware, and improved life on-orbit.

Maxar has built and launched more than 280 satellites with a combined 2,200 years of on-orbit service. Image courtesy of Maxar Technologies.
Since introducing AM into its spacecraft component production, Maxar has improved schedule agility, reduced manufacturing costs, and increased the performance of satellites. It has described short manufacturing timelines for spacecraft, about two to three years, and 3D printed tooling to support the spacecraft during assembly and test. Another critical advantage of the technology is churning out customized parts with geometries specific to each satellite, reducing mass and hardware count. Maxar understands that it can improve life on-orbit via lower mass and improved thermal distortion and performance by taking advantage of this technology for production.
With so many benefits to the space industry, AM technology plays a significant role in spacecraft production. As companies and startups continue to build up their on-site 3D printing capabilities and partner with service bureaus to scale 3D printed parts, it becomes ever so clear that the disruption of AM in this sector is not only inevitable but could thrive in the next decade.
Subscribe to Our Email Newsletter
Stay up-to-date on all the latest news from the 3D printing industry and receive information and offers from third party vendors.
Print Services
Upload your 3D Models and get them printed quickly and efficiently.
You May Also Like
The Dental Additive Manufacturing Market Could Nearly Double by 2033, According to AM Research
According to an AM Research report from 2024, the medical device industry, specifically in dentistry, prosthetics, and audiology, is expected to see significant growth as these segments continue to benefit from...
Heating Up: 3D Systems’ Scott Green Discusses 3D Printing’s Potential in the Data Center Industry
The relentless rise of NVIDIA, the steadily increasing pledges of major private and public investments in national infrastructure projects around the world, and the general cultural obsession with AI have...
AM Research Webinar Explores Continuum’s Sustainable Metal Additive Manufacturing Powders
Metal additive manufacturing (AM) powder supplier Continuum Powders is working to develop solutions that empower industries to reduce waste and optimize their resources. An independent life cycle assessment (LCA) of...
3D Printed Footwear Startup Koobz Lands $7.2M in Seed Round
California-based Koobz is focused on reshoring the U.S. footwear supply chain with advanced manufacturing processes, including 3D printing. The startup just announced that it has added $6 million to its...