Update: The new 4DFWD shoes from adidas, just worn on the podium by adidas athletes at the Tokyo Olympics, are now available to the public for purchase for $200.
adidas has worked with Carbon to 3D print midsoles using the start-up’s Digital Light Synthesis (DLS) technology for the past four years. This resulted in several limited release shoe lines featuring 3D printed midsoles. Now, the company has announced the newest product using 3D printing, the adidas 4DFWD, which the athleticwear giant claims actually bounces runners forward.
In a press event ahead of the release, Sam Handy, Vice President Design at adidas Running, explained how the company began moving from prototyping with 3D printing to end part production using selective laser sintering and harder materials:
“The first 3D printed shoe that we ever built was given to a selected group of athletes, specifically metal winners in the 2016 Rio Olympics. This shoe was built using the traditional 3D printing technology, where… you take a powder and you laser it into a hard material and then we were mechanically pushing that with our very first lattice technology. But really 3D printing was unlocked for us when, in Silicon Valley, we met Carbon and were able to experience their unique approach to 3D printing, using digital light synthesis technology, which was something that no one else had ever done before and really gave a radical perspective on the potential of 3D printing in the sporting goods industry.”
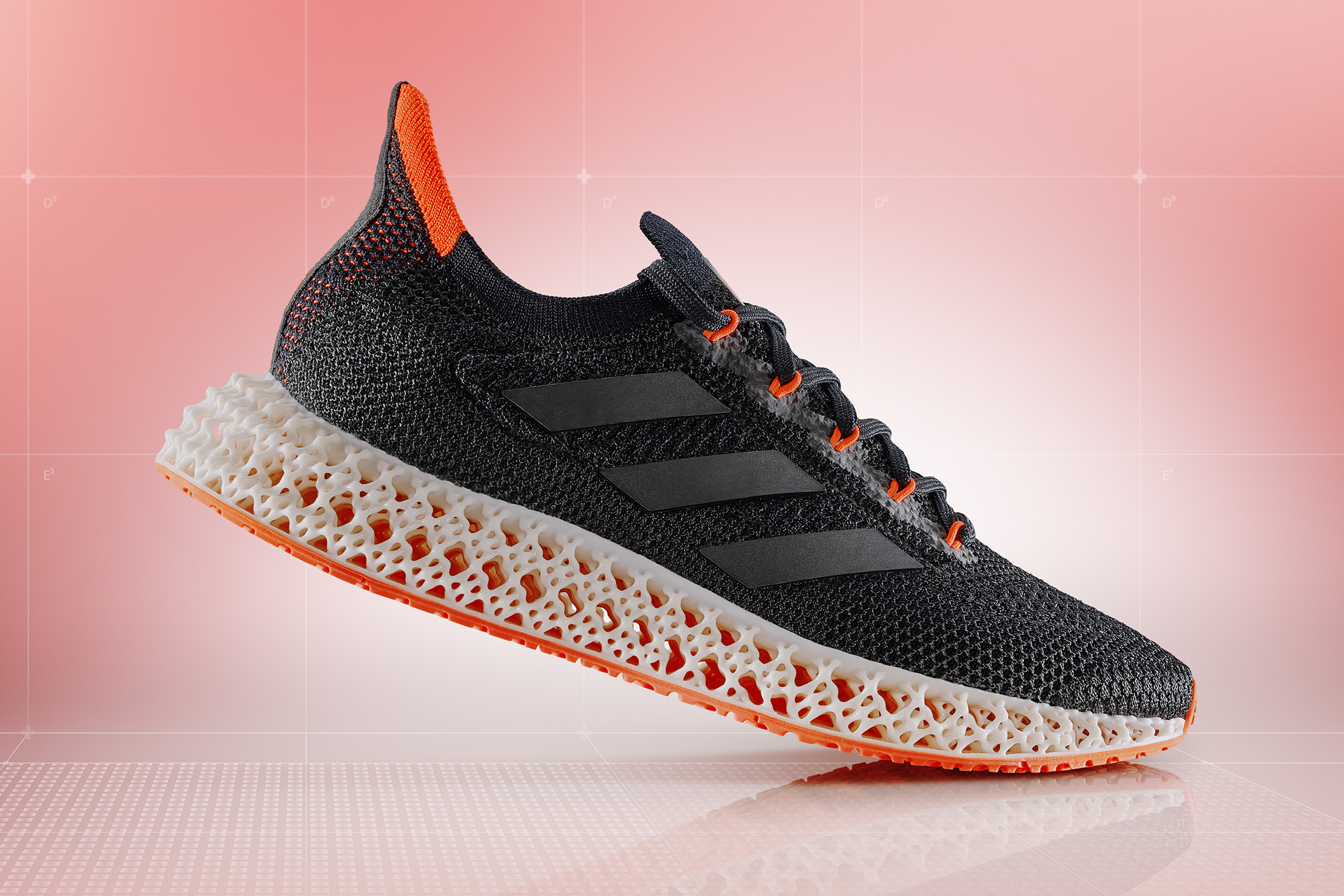
The 4DFWD line advances on the 4D Futurecraft and AlphaEDGE lines before it with a unique lattice structure design adidas described as a bowtie geometry. Rather than a helical or simple crisscross shape, the lattice cells of the 4DFWD midsoles resemble a bowtie that has been “coded to compress forward upon vertical impact.” Phil DeSimone, Carbon co-founder and chief business officer, told 3DPrint.com how the lattice structure was ultimately chosen:
“The adidas 4D 1.0 midsole was reviewed and completely re-coded. From 5 million new possible lattice structures, the adidas 4DFWD bowtie-shaped lattice midsole was born – informed by data to positively counter forces during the braking phase of running and adding a new dimension of benefits for runners. Upon impact with the ground, peak braking force is reduced compared to previous generations of 4D midsole, redirecting these vertical forces into horizontal forward motion. This results in a smoother transition shown by an on average reduction of peak braking force by 15% and running economy at the same level as Ultraboost – one of the most successful running shoes on the market,” DeSimone said. “Made of 39% bio-based 3D material, adidas 4DFWD offers 23% more cushioning and generates over three times as much forward motion than previous models under vertical loading in mechanical testing conditions.”

Sam Handy said of the result: “4D technology provides us with the opportunity to design in a way that conventional foam midsoles do not allow. We took inspiration from the first generation 4D lattice midsole and set ourselves the challenge to take it to the next level, coding millions of potential lattice structures to see if we could specifically design to counter negative mechanical forces experienced during running. Working closely with Carbon, our product teams, and testers we identified one perfect lattice midsole that is designed to compress forwards under loading and counter mechanical forces whilst delivering a unique gliding sensation for our runners.”

In turn, it offers 23% more cushioning and creates three times more forward motion under vertical loading in mechanical testing conditions. Additionally, the peak braking force by a runner is cut by 15 percent on average due to the fact that these vertical impact forces are converted into horizontal forward motion. The shoes were put through bio-mechanical testing University of Calgary, along with adidas runners, while “cognitive perception testing” was performed at Arizona State University.
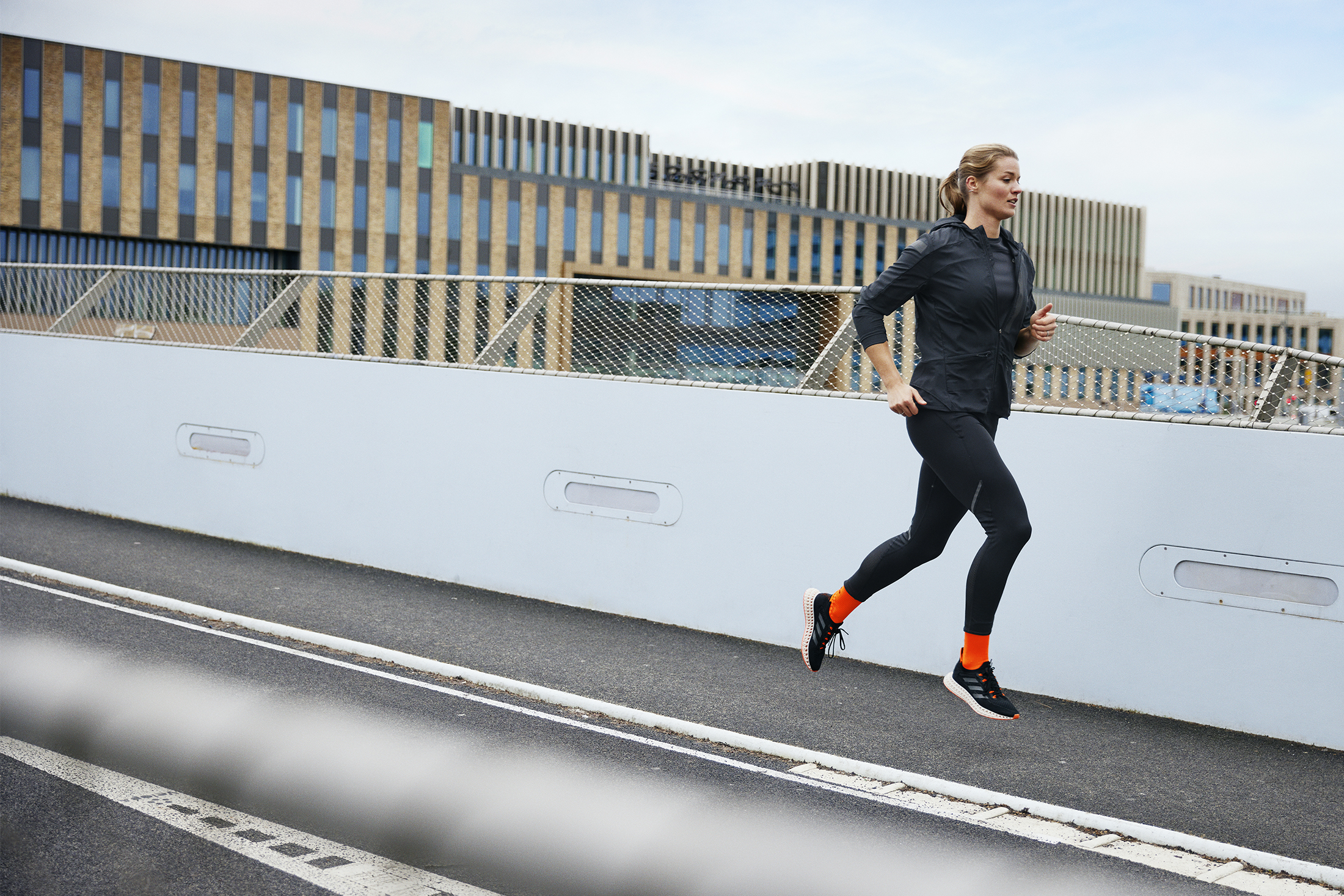
At the press event, Alberto Uncini Manganelli, SVP and General Manager for adidas Running & Credibility Sports, said that the new shoe line represents a step forward in the company’s sustainability goals:
“We are actively committed to our sustainability journey of helping to end plastic waste, seeking out the better solutions for high-performance materials that have minimal environmental compromises. Our first made to be remade running shoe, FUTURECRAFT.LOOP, has been in the test phase since 2019 and is scheduled to launch later this year. And, by 2024, we are aiming for all our products to be made from 100% recycled polyester.”
Moving toward that goal, the new PRIMEKNIT upper is made in part from recycled polyester and, as mentioned, the midsole is made from 39 percent bio-based material. Dr. DeSimone elaborated on the development of this new polymer:
“We designed the new material with this launch in mind, collaborating with adidas to develop the next generation of programmable resins that’s lighter and stiffer, optimized specifically for runners,” DeSimone said. “We knew we wanted to improve weight, cushioning capability, and energy return, but these factors are often at odds with each other. So the Carbon Materials team had to start completely from scratch. adidas has always wanted to be forward-thinking in terms of sustainability from the start, so we created the new material that not only increased the performance but also was derived sustainably — all within 18 months since the prior launch. The material has over 39% bio-based feedstock, derived from corn, which is something we’re extremely proud of.”
According to DeSimone, Carbon attempts to reduce its ecological impact as much as possible, in part by using plant-based materials that require less energy:
“Carbon already reduces the carbon footprint associated with the development of our resins by using plant-based materials. Plant-based polymer processing is 50% less energy intensive than petroleum-derived materials. For example, RPU 130 which fills the need for a tough, rigid, and high temperature additive manufacturing material suitable for rigorous applications in industries such as automotive, is comprised of 30% Susterra propanediol, a bio-based material that combines performance and sustainability,” DeSimone explained.
adidas is expanding its use of 3D printing technology, but is no longer focusing on the use of the Carbon SpeedCell. An adidas representative told 3DPrint.com:
“As part of adidas‘ Own the Game strategy’ for 2025, creating a unique consumer experience is a strategic focus for the brand. Core processes across the entire value chain will be digitalized: from the creation process with 3D design capabilities, via the sourcing of its products to selling it to customers and consumers. To achieve this, the company will expand its data and technology expertise internally and increase the size of its tech team. SpeedCell is no longer a strategic focus as the brand is investing into new areas such as ERP system S/4HANA next to several new tech platforms in Running, and a swipe mechanism for product feedback incorporated into the adidas app.”
Though adidas and Carbon weren’t able to comment on the exact number of pairs that will be produced, Dr. DeSimone mentioned that adidas’s 4D midsoles may become the highest volume 3D printed product yet produced:
“adidas was the first vendor to show 3D printing at-scale, paving the way for 3D printing to come into its own around consumer product goods. Over 1 million 4D midsoles have already been produced on Carbon’s L1 3D Printer and using the Carbon Digital Light Synthesis™ process — we believe this shoe will be the highest volume 3D printed product ever produced,” DeSimone said.
“This wouldn’t be possible without Carbon’s breakthrough Digital Light Synthesis™ process, making it possible for industry-leading companies like adidas to reduce their typical go-to-market timelines significantly, and at scale. Given the rapid nature of the Carbon DLS™ process, once a design exists, a production-quality part or product can be immediately manufactured. This is the latest example of 3D printing technology disrupting product design and manufacturing at-scale and comes on the heels of the launch of Carbon’s Design Engine software.”
I was not only surprised to learn that over one million adidas midsoles had been 3D printed so far, but also that the 4D product was projected to exceed other markets in terms of unit volume. 3D printed hearing aids have long been held up as the success story for 3D printed goods, with the claim made that “millions” of 3D printed hearing aids are in the world today. Some estimates have the number of 3D printed devices out in the world at 10 million.
The difference between midsoles from a powerful business like adidas and hearing aids is that the hearing aid market is only a fraction (~$10 to $14 billion) of the athletic footwear market (~$56 billion to $64 billion). This is obviously due to the fact that many more people wear shoes than use medical devices. According to SmarTech’s report on 3D printed footwear, “3D-Printed Footwear 2020-2030, an Analysis of the Market Potential of 3D Printing in the Footwear Industry“, the market for AM in footwear is projected to exceed $4.2 billion in annual revenues in 2025, with Carbon and adidas listed as major players in that segment. So, the idea that adidas will use Carbon technology to 3D print more midsoles than there are hearing aids isn’t surprising in itself. I will just be surprised to see it take off so quickly.
The new shoe line was first released in limited series from May 5 to 16, with three color combinations. This included a Tokyo Collection variety to celebrate the Tokyo Olympics. Now, the shoes are available to the public for purchase here.
Subscribe to Our Email Newsletter
Stay up-to-date on all the latest news from the 3D printing industry and receive information and offers from third party vendors.
Print Services
Upload your 3D Models and get them printed quickly and efficiently.
You May Also Like
3D Printing News Briefs, July 2, 2025: Copper Alloys, Defense Manufacturing, & More
We’re starting off with metals in today’s 3D Printing News Briefs, as Farsoon has unveiled a large-scale AM solution for copper alloys, and Meltio used its wire-laser metal solution to...
3DPOD 260: John Hart on VulcanForms, MIT, Desktop Metal and More
John Hart is a Professor at MIT; he´s also the director of the Laboratory for Manufacturing and Productivity as well as the director of the Center for Advanced Production Technologies....
3D Printing News Briefs, June 28, 2025: Defense Accelerator, Surgical Models, & More
In this weekend’s 3D Printing News Briefs, 3YOURMIND was selected to join an EU Defense Accelerator, and PTC has announced model-based definition (MBD) capabilities within Onshape. Finally, a study out...
EOS in India: AM’s Rising Star
EOS is doubling down on India. With a growing base of aerospace startups, new government policies, and a massive engineering workforce, India is quickly becoming one of the most important...