“The 3D printing process is no longer a way to merely make a replica of the designed model,” Sun said. “Now we have a dynamic process that uses light to assemble all the layers but with a high degree of freedom to move each layer along the way.”To achieve this, Sun’s team used a photopolymer resin and a complex robotic arm. A photopolymer is a polymer whose properties change when exposed to light (probably most popularly-known outside of 3D printing for their use in UV-cured fillings at the dentist’s office). In this case, shining light on the polymer makes it crosslink, turning it into a solid. Sun’s team used a DLP-based printer with a liquid resin vat, using projected light to “freeze” the resin as it came out of the vat.
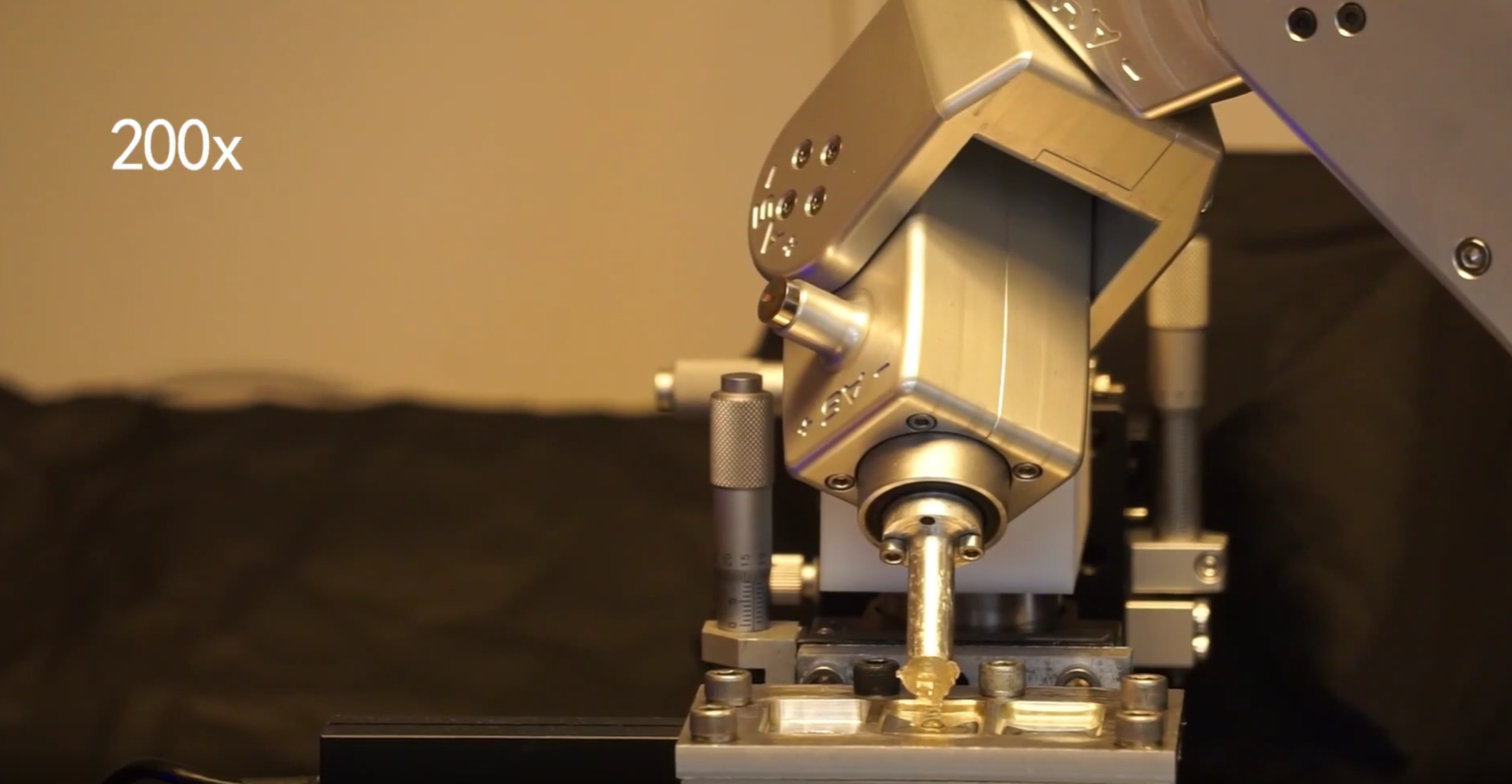
A robot arm with six degrees of freedom helped the Northwestern team change layers during the printing process. (Image via Additive Manufacturing).

Dynamic changes applied to a model of the Eiffel Tower show off the flexibility of this new printing process. (Image via Northwestern University)

A 3D double helix, one of the team’s prototypes, is pulled from a vat of liquid resin (Image via Additive Manufacturing).
“This is a very fast process, and there is no interruption between layers,” Sun said. “We hope the manufacturing industry will find benefit in it.”
Subscribe to Our Email Newsletter
Stay up-to-date on all the latest news from the 3D printing industry and receive information and offers from third party vendors.
Print Services
Upload your 3D Models and get them printed quickly and efficiently.
You May Also Like
Reinventing Reindustrialization: Why NAVWAR Project Manager Spencer Koroly Invented a Made-in-America 3D Printer
It has become virtually impossible to regularly follow additive manufacturing (AM) industry news and not stumble across the term “defense industrial base” (DIB), a concept encompassing all the many diverse...
Inside The Barnes Global Advisors’ Vision for a Stronger AM Ecosystem
As additive manufacturing (AM) continues to revolutionize the industrial landscape, Pittsburgh-based consultancy The Barnes Global Advisors (TBGA) is helping shape what that future looks like. As the largest independent AM...
Ruggedized: How USMC Innovation Officer Matt Pine Navigates 3D Printing in the Military
Disclaimer: Matt Pine’s views are not the views of the Department of Defense nor the U.S. Marine Corps Throughout this decade thus far, the military’s adoption of additive manufacturing (AM)...
U.S. Congress Calls Out 3D Printing in Proposal for Commercial Reserve Manufacturing Network
Last week, the U.S. House of Representatives’ Appropriations Committee moved the FY 2026 defense bill forward to the House floor. Included in the legislation is a $131 million proposal for...