GE has announced a five year agreement with the University of Sydney to bring metal 3D printing training and machines to their Darlington campus. This campus is a part of the university’s Sydney Manufacturing Hub, which can now train people in additive manufacturing skills, as well as incubate businesses. The hub also will “enable advanced alloy design and applications to support a range of sectors including aerospace, defence, medicine and agriculture.”
The five year agreement builds on an earlier Memorandum of Understanding with the University, as well as agreements with the government of New South Wales to help bring 3D printing to the region.
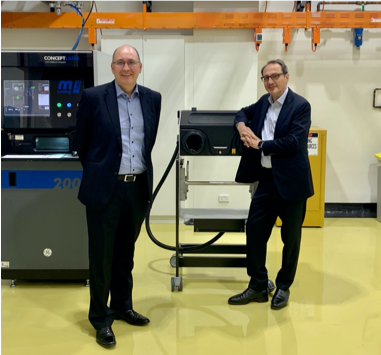
GE’s Sam Maresh and Professor Simon Ringer
Sam Maresh, country leader of GE Australia, noted:
“This is a breakthrough for Australia’s advanced manufacturing industry. Via the Sydney Manufacturing Hub, Australian manufacturers and small to medium enterprises (SMEs) will now have ready access to GE’s own production-grade additive technology.”
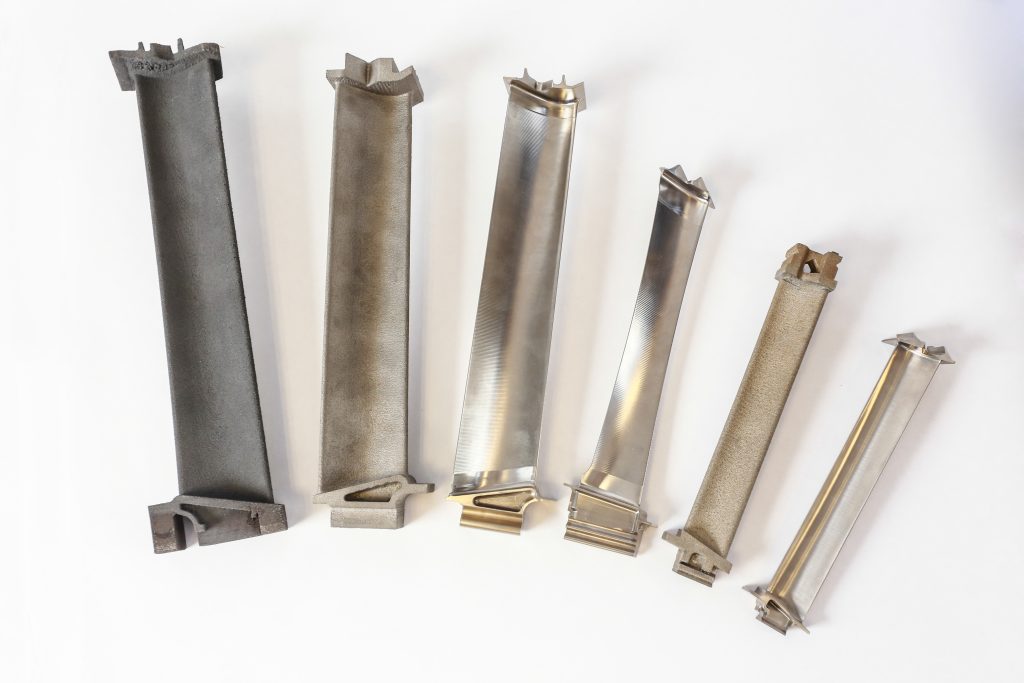
Low-Pressure Turbine Blades made with EBM
University of Sydney Director of Core Research Facilities Professor Simon Ringer, relayed how the agreement relates to the ongoing pandemic.
“Pre-COVID-19, a national focus on manufacturing resilience was generally regarded as a nice thought. We have long believed this needs to be a critical national priority, and COVID-19 has raised the stakes. GE Additive and the University of Sydney, working alongside government and Australian SMEs, will be at the forefront of delivering this capability. A manufacturing renaissance is coming and for Australia to lead in this space, there must be an investment in skills. Through the use of a smart facility, the University of Sydney is best placed to develop them and bring forward a new era of innovation.”
The focus on skills and skill training is spot on here. Often firms and governments are focused on machines, but, in reality, the big hold up is in training. Experts in Design for Additive Manufacturing, machine operators, and application development specialists simply do not exist yet. Laser powder bed fusion and electron beam melting are difficult technologies to understand and to execute dial-in for manufacturing. Most firms take at least six months of work to get to a level where they can coherently make parts. There’s a lot of understanding, training and practical experience that goes into comprehending what the variables, problems, and errors are in 3D printing. Even tasks like support generation and part planning are extremely difficult and vary due to many factors, such as part geometry.
Furthermore, such tasks as powder handling, qualification, application development, certification and actual production are also complex skillsets that few people master. By letting this be a focus area, the University of Sydney will really help local industry. Individual operators and especially application development engineers that can take conventional parts and make them into working additive ones, and then develop new applications, are key bottlenecks all over the world.
By focusing on training, New South Wales really is grabbing the bull by the horns here. In making more additive people, they can tackle more deployments more quickly and spread the technology faster around the country. I really like that they’re opening up the technology to small-to-medium enterprises, as well. Bigger firms will probably want to keep everything to themselves anyway and small companies are real job engines. To have a university train these people and help get small businesses access to the technology could therefore be a very positive development.
For a country rich in natural resources, including the metals used in additive, metal 3D printing would seem a tantalizing shortcut to space programs, military programs and advanced manufacturing applications. To make more out of what Australia has and let its people have access to higher value jobs through training is again a very tempting prospect for a government. Due to Australia’s remoteness and vast resources in this case, this could be a very successful implementation. Here much of the money invested by the government would tend to flow back to the country. Along with CSIRO, SPEE3D and Titomic, Australia has a few strong pillars to stand on additive-wise. Now with this program, they can help train a new generation of Australian entrepreneurs, technicians, and scientists to help make Australia’s additive journey a success.
Subscribe to Our Email Newsletter
Stay up-to-date on all the latest news from the 3D printing industry and receive information and offers from third party vendors.
Print Services
Upload your 3D Models and get them printed quickly and efficiently.
You May Also Like
Printing Money Episode 30: Q1 2025 Public 3D Printing Earnings Review with Troy Jensen, Cantor Fitzgerald
Printing Money is back with Episode 30, and it’s that quarterly time, so we are happy and thankful to welcome back Troy Jensen (Managing Director, Cantor Fitzgerald) to review the...
3DPOD 260: John Hart on VulcanForms, MIT, Desktop Metal and More
John Hart is a Professor at MIT; he´s also the director of the Laboratory for Manufacturing and Productivity as well as the director of the Center for Advanced Production Technologies....
Etsy Design Rule Change Reduces Selection of 3D Printed Goods
Online marketplace Etsy has implemented a rule change requiring all 3D printed goods on the site to be original designs. The update to the site’s Creativity Standards states, ¨Items produced using...
3DPOD 259: AM at Stratasys with Rich Garrity, Chief Business Unit Officer
Rich Garrity is the Chief Business Officer of Stratasys. Rich shares Stratasys´ vision and future with us. We talk about machines, applications, clients, and the market in general. What technologies...