Italian researchers from the Department of Mechanical and Aerospace Engineering, Politecnico di Torino, explore the use of sensors in 3D printing for medical applications. Authors G. De Pasquale, A. Buffon, and L. Bongiorni have recently published the results of their study in a short white paper, “Sensors integration in additive DMLS metal parts.”
The researchers integrated 3D printed thermal and inertial sensors inside steel samples using direct metal laser sintering (DMLS) which could have potential in both medical and clinical settings where monitoring (and thus sensors) is required, along with usefulness in promoting biomechanical parameters. Conventional methods for integrating sensors into parts usually involves drilling (via milling procedures), encasing them, or through surface adhesion.
In this study, one sensor was considered for both “high temperature exposure and even high cost,” while the other was meant for basic, more affordable use. The researchers experimented with encapsulating the sensors into specimens fabricated during the study, with the goal of:
- Calibrating the 3D printing process with accurate parameters and operations
- Optimizing integration of the sensor during 3D printing
- Supporting validation of sensing performances afterward
“The first sensor type is piezo-resistive thermal sensor PT100 with cylindrical probe with 5.90 mm diameter and 30.3 mm length,” explained the authors. “The probe is connected by wire with special thermal insulation protection based on silicon. The second sensor type is general purpose piezo-resistive accelerometer with standard electric cable.”
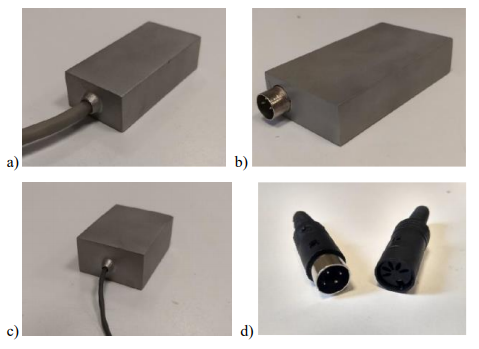
Samples of 17-4PH parts with integration of thermal sensor (a, b) and inertial sensor (c) and 3-poles connector (d).
During the study, the researchers found that with SLM optimization, they were able to prevent material alterations sometimes caused to the structure of the part when foreign bodies were introduced into the metal. The 17-4PH samples were polished and finished, and then evaluated by using a 12.5x magnification factor to examine the density of the materials, as well as a 200x magnification factor to analyze surface microstructure.
Density was found to be at 100%, with no sign of pores or “discontinuities.” The researchers reported a minor shift between surface layers during printing, but the problem was easily fixed through additional mechanical surface tooling; otherwise, the metal part was found to be “homogenous, and without defects.”
The thermal sensors were tested for functionality, focusing on performance in terms of precision, sensibility, and repeatability. The authors used an analog-to-digital converter, along with a heating plate to perform tests. Ultimately, they concluded that while users could feasibly integrate any type of electronics, applications could be improved with more advanced configurations.
“In particular, the sensing of wearable systems customized on the characteristics of the individual subject is an attractive application for the near future.”
Find out more about 3D printing with sensors, from different types of materials being used to unique techniques being developed by researchers, and more.
[Source / Images: Sensors integration in additive DMLS metal parts]Subscribe to Our Email Newsletter
Stay up-to-date on all the latest news from the 3D printing industry and receive information and offers from third party vendors.
Print Services
Upload your 3D Models and get them printed quickly and efficiently.
You May Also Like
Reinventing Reindustrialization: Why NAVWAR Project Manager Spencer Koroly Invented a Made-in-America 3D Printer
It has become virtually impossible to regularly follow additive manufacturing (AM) industry news and not stumble across the term “defense industrial base” (DIB), a concept encompassing all the many diverse...
Inside The Barnes Global Advisors’ Vision for a Stronger AM Ecosystem
As additive manufacturing (AM) continues to revolutionize the industrial landscape, Pittsburgh-based consultancy The Barnes Global Advisors (TBGA) is helping shape what that future looks like. As the largest independent AM...
Ruggedized: How USMC Innovation Officer Matt Pine Navigates 3D Printing in the Military
Disclaimer: Matt Pine’s views are not the views of the Department of Defense nor the U.S. Marine Corps Throughout this decade thus far, the military’s adoption of additive manufacturing (AM)...
U.S. Congress Calls Out 3D Printing in Proposal for Commercial Reserve Manufacturing Network
Last week, the U.S. House of Representatives’ Appropriations Committee moved the FY 2026 defense bill forward to the House floor. Included in the legislation is a $131 million proposal for...