For certain chefs in the alphabet soup that is the US government, all roads lead to 3D printing. So, too with hypersonics. Astro America, also sometimes called AstroA, aims to leverage new manufacturing technologies for the development of what they call the Hypersonic Production Accelerator Facility (HPAF).
3D printing research is an iceberg. There is the public information that we see and read about in the journals, press releases, and press. But, there is also a lot going on beneath the waterline. Especially in the United States, a lot of 3D printing research is being funded by the government. Fundamentally new technologies, classes of materials, and processes are being developed so that the U.S. can stay ahead. 3D printing as a technology is applicable to missile technology, nuclear warheads, military aircraft, munitions, ships, repair, making logistics more efficient, and upgrading weapons systems quickly. Where one technology may have a direct application, a new 3D printing material or process could find its way into numerous government applications.
Anywhere saving weight is a priority, low volume is a fact, and geometric freedom or timeliness or location make sense, 3D printing will make sense. And with these criteria there is again a huge overlap with military systems and their needs. They are often only very few, they are located in remote places, and weight savings are important, etc. 3D printing is therefore a key enabling technology to deliver future capabilities to planners while also repairing and upgrading current inventories.
At the same time, the exact same technology, same materials, same needs, and same critical success factors can be applied to commercial aviation in turbomachinery as well as aerostructures and potentially more parts, too. Simultaneously, additive manufacturing is also highly usable, in the same form, in satellites. And, at the same time as well, 3D printing can be extensively used in the development of governmental and commercial space propulsion and vehicles.
Hypersonics are a pipe dream that has been the crack of choice for a large part of the U.S. space, missile and aviation defense community for over three decades. Hypersonic planes and missiles go above a speed of Mach 5. What is Mach 5? It is five times the speed of sound, which is around 6,125 kilometers per hour.
The SR-71 Blackbird reportedly maxed out at Mach 3.5. In 1967, the North American X-14 went to Mach 6.7. The US’s X-51A Waverider went hypersonic for three minutes in 2010. The X-43 attained a top speed of Mach 9.6 in 2004. The Hypersonic Technology Vehicle 2 went Mach 17. That’s 21,000 kilometers per hour—London to New Zealand in an hour.
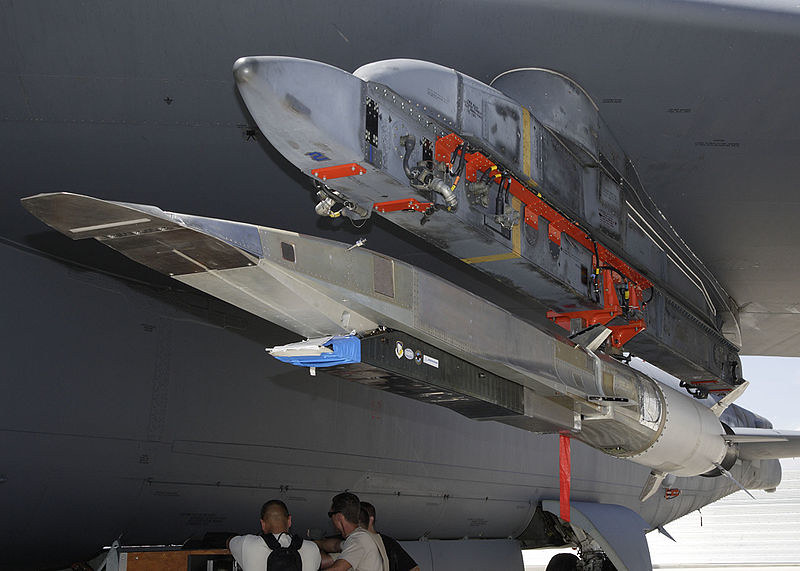
A waverider slung under a launch aircraft. It’s called the waverrider because it uses its own shockwave to lift itself.
The goal of many of these vehicles is ultimately to win on the ultimate high ground: space. You know that part of the spy movie when they task a satellite to come over the target house and it comes online in only a few minutes? They’re trying to make that a reality.
The relatively jargon and machismo term for the end goal is a Prompt Global Strike. Domino’s for missiles. The idea is that, within the hour, the U.S. could strike anywhere on the planet with precision-guided munitions. In all press, they continually use “conventional weapons” but—mmm…yeah right.
At the same time, if you have that capability, you could put a satellite plane anywhere in an hour, as well. Or you could put a J-Stars command-and-control capability, a Rivet Joint style plane, or some kind of satellite killer drone anywhere. Or, of course, you could have a technology capable of launching many little satellites from anywhere within the hour. Or you could use it to out-Elon Elon Musk.
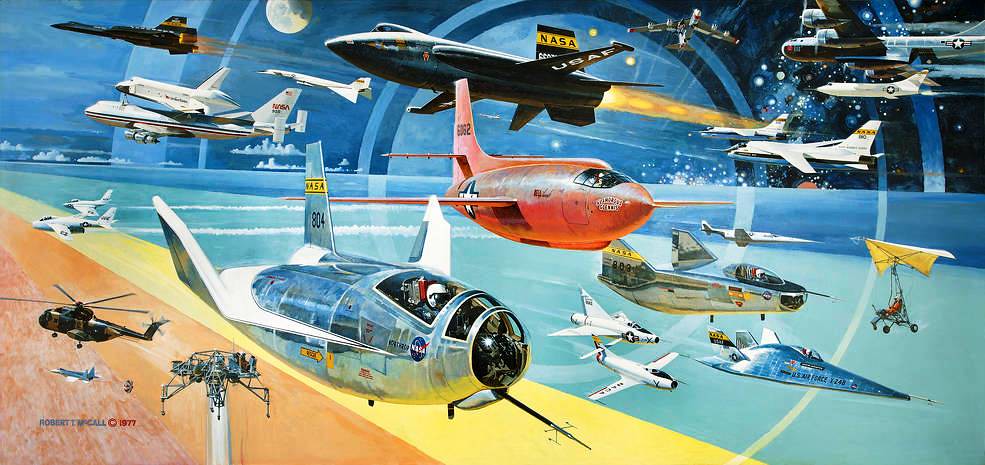
Various US X Planes
The U.S. continued working on Blackswift—which sounds cool, but also like it should be a K-pop band or a 90’s soul group. “Blackswift flight demonstration vehicle will be powered by a combination turbine engine and ramjet, an all-in-one power plant,” according to the Director of DARPA. That project was canceled, but the overall DARPA Falcon Project has continued.
Now, what was formerly known as the Hypersonic Weapon System (HWS) has been given the gentler title, the Hypersonic Cruise Vehicle (HCV), which makes it seem like something that will give you COVID while you play shuffleboard. Imagine the world ends and half the people that know beforehand are thinking of Gopher, Isaac, and Merill Stubing. “Wait, Martha, they have cruise ships in space? Why didn’t our agent tell us, we could have used our Princess Points to go to the moon instead of Cozumel.”
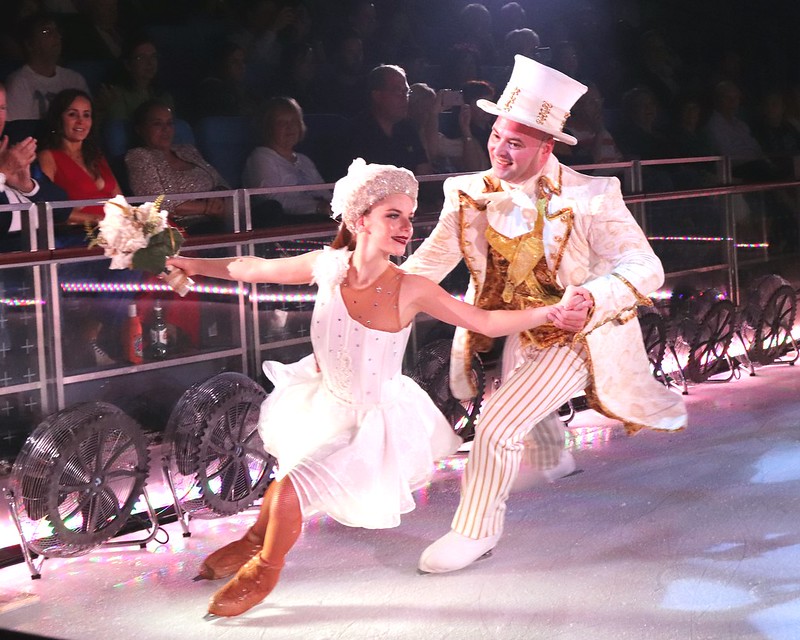
Life Aboard the Hypersonic Cruise Vehicle.
Something with unmatched speed and time on target that could deliver different payloads and capabilities anywhere on the planet in an hour or so is a war winner. A few of these and you can sniff out the other guy’s radar system (this is great too), get real-time imagery of his bases, kill his satellites, scout for landing locations, get meteorology for the place you want to land, and get over-the-horizon coverage from missiles and the like. All with the same plane. Strategically and tactically, it would be like the other guy is stuck in aspic while you’re zooming around in real-world Command and Conquer.
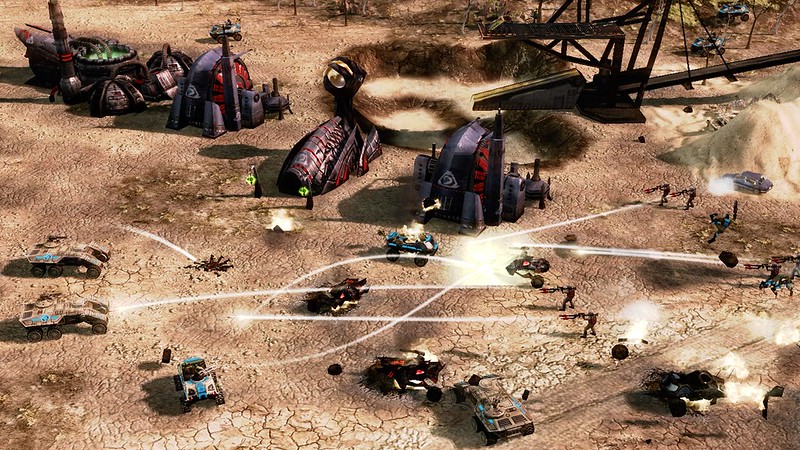
It’s like Theater Intelligence Assessment for all the afghan weddings.
Making functional hypersonic vehicles a reality, however, is a challenge that is incredibly complex. In many cases, projects have been done with ATK, Boeing and Lockheed working together. A lot of materials science is required to make parts feasible. Developments such as Bulk Metallic Glasses and new composites will be needed to make this a reality, as well. This is where nonprofit ASTRO America comes in.
Neal Orringer leads it and was the Director of Manufacturing at the Department of Defense. Chief Technology Officer for AstroA is Michael “Mick” Maher, a former DARPA official who was instrumental in bringing a lot of 3D printing technologies center stage in their Open Manufacturing project. Crucially for us, their Board of Directors includes Jim Williams, former President and CEO of Paramount Industries.
Paramount was bought by 3D Systems and was a major force in the use of 3D printing for drones and much more. The American drone boom meant that a lot of companies used 3D printing for prototyping and, thereafter, some went into production with 3D printed parts.
This was a live-fire demo of what our technology is capable of in front of the Air Force and other officials. Here we saw quick development times, fast iterations, and things like fuel tanks that went from 30 parts to eight. All the claims and advantages for aerospace were laid bare, while our inadequacies were exposed as well. This development is one of the key reasons that the U.S. government is so bullish about 3D printing.
Further along Paramount helped develop polymers and applications for military aircraft, as well. The company, along with others, printed parts for operational military aircraft. And the company’s president is now the president of All Points Additive which aims to scale up 3D printing.
AstroA’s HPAF is an idea that mimics ORNL’s Additive Manufacturing demo center, but goes further toward the bright lights of the factory floor. The idea in short is that,
“With a new hypersonic production accelerator facility (HPAF), the United States would co-locate teams of experts and industries currently scattered across the country. This solution would save considerable time, money, and resources to build hypersonic vehicles and eventually help scale-up factory output.”
They will have common tools such as metrology and separate lines, for security’s sake, because Boeing will be ostensibly building its X75 next to Lockheed’s Skunkworks line for their X76, while sharing the same lunchroom. Imagine the Boeing X-32 and the Lockheed Martin X-35 JSF teams using the same parking lot and bathrooms. Who is doing the security for this? The angel Gabriel?
In a paper the AstroA team explains that,
The problems are laid out as:
“The speed at which hypersonic vehicles travel necessitates extreme heat stress testing and access to critical testing infrastructure such as wind tunnels, which often have long queues… [D]efense and aerospace manufacturing practices involve qualification processes that often can take 10 to 15 years and millions of dollars to introduce new state-of-the-art materials. In almost every case, the manufacturing workflow is disconnected by skills and applied technologies… [T]he manufacturing workflow is disconnected by skills and applied technologies. This has resulted in an inflexible, outdated, and highly disaggregated supply chain for critical defense platforms.” The paper adds, “This results in higher costs, long lead times, and inconsistency of practices across multiple skillsets. Because of these challenges, hypersonic vehicles are stuck in a constant start-and-stop loop that doesn’t efficiently move from development to production.”
This is spot on, but the solution is a dreamy one:
“Every tier of the hypersonic supply chain, including the Air Force customer, working together under the same roof will reduce the iteration time required for scaling up hypersonic vehicle manufacturing.”
The shorter development time because of this integration will result in:
• Design problems being addressed early, rather than the current norm of late in the timeline;
• Analysis has shown that manufacturing processes could decrease by up to 73 percent; and
• Result in approximately 45 percent cost savings.”
AstroA also wants to do this:
“This concept entails a unique method of leasing state-of-the-art manufacturing technology for a period of three years. At the end of this period, stakeholders then have multiple options to adapt and improve if necessary, including:
• Renew Leases: Keep the same equipment in-house for another three-year term;
• Equipment Refresh: Additive manufacturing machines are removed and replaced with newest models, representing the most capable commercially available technology in repeatable, large format printing with concurrent quality management systems; or
• Technology Reset: Additive manufacturing machines and auxiliary equipment are removed and replaced with other manufacturing processes”
This means that, every three years, you’re going to have to re-qualify everything and not be able to make the stuff you used to make in the same way. In the current state of 3D printing technology, this approach would be bonkers. ORNL’s “born certified” additive manufacturing frameworks could accelerate this. And, yes, in the future we’d have some artificial intelligence/finite element analysis/qualification magic but…when?
I cannot stress just how much of a disadvantage it would be to get everyone’s new equipment every three years. Even if qualification was automatic and easy, it would be a nightmare to use all new equipment. You’d have all the teething problems every three years and, by the time it worked well, you’d have to replace it. Working here would be hell. It would be like a mad scramble to develop the atom bomb punctuated by continual firmware updates.
Also, how could you ensure that materials would be ready for the new machines with their new settings? Idle time would abound and you’d have many more breakdowns. The waste of waiting would be Godot-like. It could only work if you had a separate facility that would bring all the new stuff into working order before you switched over and even then I doubt that it would be efficient.
So, on the practicality front, I really do wonder if it will all work. But, from a long term perspective, a helicopter view or, perhaps more appropriately, a hypersonic spy plane view, this could be a Manhattan Project kind of an effort to commercialize this technology. Let’s hope that there are fewer Russian spies this time.
Image: Johnathan Cutrer, Mark Jones Jr., Numbers Station, Ausdew, Prayitno, Klaus Kunha.
Subscribe to Our Email Newsletter
Stay up-to-date on all the latest news from the 3D printing industry and receive information and offers from third party vendors.
Print Services
Upload your 3D Models and get them printed quickly and efficiently.
You May Also Like
Reinventing Reindustrialization: Why NAVWAR Project Manager Spencer Koroly Invented a Made-in-America 3D Printer
It has become virtually impossible to regularly follow additive manufacturing (AM) industry news and not stumble across the term “defense industrial base” (DIB), a concept encompassing all the many diverse...
Inside The Barnes Global Advisors’ Vision for a Stronger AM Ecosystem
As additive manufacturing (AM) continues to revolutionize the industrial landscape, Pittsburgh-based consultancy The Barnes Global Advisors (TBGA) is helping shape what that future looks like. As the largest independent AM...
Ruggedized: How USMC Innovation Officer Matt Pine Navigates 3D Printing in the Military
Disclaimer: Matt Pine’s views are not the views of the Department of Defense nor the U.S. Marine Corps Throughout this decade thus far, the military’s adoption of additive manufacturing (AM)...
U.S. Congress Calls Out 3D Printing in Proposal for Commercial Reserve Manufacturing Network
Last week, the U.S. House of Representatives’ Appropriations Committee moved the FY 2026 defense bill forward to the House floor. Included in the legislation is a $131 million proposal for...