An exciting and potentially revolutionary slow-burn development in 3D printing is that of gradient materials (also called Functionally Graded Materials, or FGMs). With FGMs, we can mix materials in such a way as to obtain different densities, hardnesses, and material compositions at the level of any voxel. Electron beam melting, various directed energy deposition processes, and PolyJet are just some of the technologies potentially capable of gradient materials.
The idea of controlling properties at every voxel is hugely inspiring to me. We cannot begin to imagine how gradient parts could change how things can be made. We could put crumple zones in objects, design for wear so that particular parts could be replaced at set intervals, make items conductive or magnetic in certain areas or imbue differing degrees of magnetism across a part.
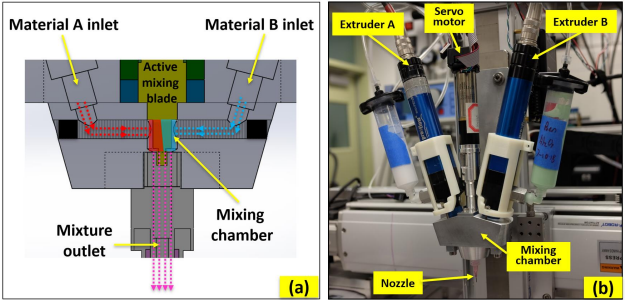
A FGM mixer using the CODE process.
Stratasys has a shaver that they use to illustrate the concept. The grippy parts are printed soft, other areas are more like cushions, the handle itself is rigid and hard, but there is flexibility in the neck. All of these different qualities on the same part with the same printer.
Imagine an armored tank where you print a soft wall and an air gap while you multiplex or mix different materials on top like the layers of a cake. You could generate new configurations of reactive armor or sandwich materials. Some bulletproof vests suck against knives because they are made to dissipate bullet impact and not stop the sharp cut of a blade. If you took Dyneema or other Kevlar and made it printable to allow for gradient structures, you could remedy this in the same production step.
A lot of the 3D printing research going into the NFL helmet challenge is based on trying to create structures that can stop fast, sharp impacts and larger, blunt ones. With gradient structures we can achieve similar feats, not just for safety gear but for many other things. Picture absorbing layers or flexible materials for industry. Or imagine of your dashboard, which could be hard, rigid and smooth but be designed to flex upon impact. Or think of sound insulation or vibration reduction and already many applications can pop up. FGMs are exciting and there is a great deal of research going on.

The Aerosint print, combines copper alloy with steel. Image courtesy of Aerosint.
People are making functionally graded glasses on powder bed systems that mix as they print. Others are trying to mimic natural functionalities by making gradient composites and they are not alone. Some papers seem revolutionary in their own right, with this ETH team looking at gradient materials with sub-micrometer resolution. Fabrisonic, Formalloy, MELD, GE, DMG Mori, Sciaky, Aerosint and Optomec are just some of the machine vendors on whose equipment these gradient materials are made. You can even print with gradient materials using digital light processing.

Applications of g-DLP–printed composites for sequential SMP components and 4D printing. Photo credit: Xiao Kuang, Georgia Tech
So, what is holding the development of gradient materials back? Once, when talking to John Barnes, he lamented that it was already so hard to get static parts right and that gradient parts would be very difficult to qualify and control.
Indeed quality control would be hard on such a part. How could you monitor or verify the Shore hardness of something with multiple hardnesses? What would the test even be? How can you verify that a thing like that can work for 10 years? What would the simulation look like? How do you safety test such a thing? What is the fatigue strength of something if it has differing fatigue properties? Or how do we find out that this part may actually have a lower continuous service temperature than the material it is made of? How might you monitor that the right property is being made? Then, we have another problem, how do we design these parts? How can you do it in CAD? 3MF could support a design for a gradient part, but how would we design that part exactly?
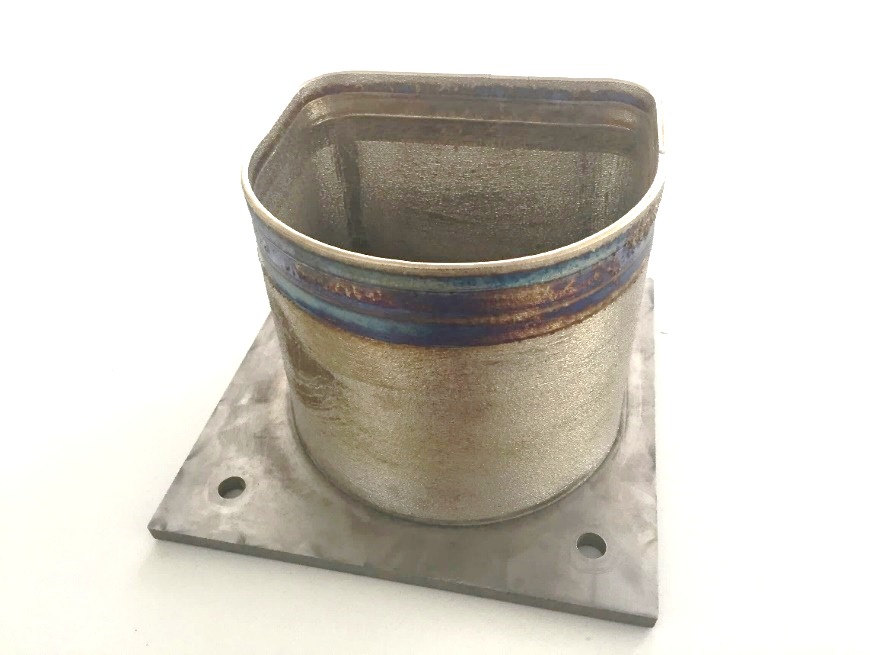
An example of a FGM part made using DED by Irepa Laser
We have enough trouble teaching everyone to think in design for additive manufacturing (DfAM), but how to think in gradients? When can we even determine that this would make sense? A gradient 3D-printed shoe sounds like a spectacular idea, but, perhaps it would be much more expensive than a conventional one. At the same time, a Croc is already a shoe made of one material and would be much less expensive than our printed variant.
While there is real excitement with regards to FGMs, we do find ourselves at an impasse. If we don’t understand something’s implications, don’t know how to design for it, and can’t conceive of its uses, we can be enthusiastic, but nothing more really. It would be like watching the nuclear or steam age approach realizing that you’re either going to dream too little or too much. On the one hand, you won’t get faster than “faster trains, I guess,” but on the other, you’ll think of nuclear-powered hairdryers and washing machines.
So, if we want to enable an enabling technology, what do we do? We have to create an example that is abundantly clear, concise, and showcases the merits of this technology well. The GE bracket is my favorite example of this. It showcases our Geiger-like topology optimized design language. It illustrated that our technology could have broad applications and clearly showed that it can save weight, which is clearly important. To pitch FGMs, we need such an example. So, a generally demonstrable, recognizable, useful item that is improved specifically by being a gradient part. Any ideas on what this should be? Because what seems to be holding back this generation of materials is lack of understanding and sufficient inspiration, not technology.
Subscribe to Our Email Newsletter
Stay up-to-date on all the latest news from the 3D printing industry and receive information and offers from third party vendors.
Print Services
Upload your 3D Models and get them printed quickly and efficiently.
You May Also Like
Reinventing Reindustrialization: Why NAVWAR Project Manager Spencer Koroly Invented a Made-in-America 3D Printer
It has become virtually impossible to regularly follow additive manufacturing (AM) industry news and not stumble across the term “defense industrial base” (DIB), a concept encompassing all the many diverse...
Inside The Barnes Global Advisors’ Vision for a Stronger AM Ecosystem
As additive manufacturing (AM) continues to revolutionize the industrial landscape, Pittsburgh-based consultancy The Barnes Global Advisors (TBGA) is helping shape what that future looks like. As the largest independent AM...
Ruggedized: How USMC Innovation Officer Matt Pine Navigates 3D Printing in the Military
Disclaimer: Matt Pine’s views are not the views of the Department of Defense nor the U.S. Marine Corps Throughout this decade thus far, the military’s adoption of additive manufacturing (AM)...
U.S. Congress Calls Out 3D Printing in Proposal for Commercial Reserve Manufacturing Network
Last week, the U.S. House of Representatives’ Appropriations Committee moved the FY 2026 defense bill forward to the House floor. Included in the legislation is a $131 million proposal for...