It may be true that “no good deed goes unpunished,” evidenced as members of the 3D printing community rushed to help with a lack of personal protective equipment and much-needed medical devices and parts around the world in response to the COVID-19 epidemic. Criticism ensued almost immediately regarding the lack of guidance for makers, along with the potential for toxicity; however, without standards or regulations, countless individuals could be creating designs for and 3D printing personal protection equipment (PPE) and medical devices with wildly varying outcomes.
Now, scientists from the Department of Neurosurgery, Hospital of the German Armed Forces and Helmut Schmidt University / University of the German Armed Forces have been working together to study the actual feasibility and efficacy of 3D printed face masks meant to thwart the spread of coronavirus. During their study, presented in the recently published “Potential Risks of a Widespread Use of 3D Printing for the Manufacturing of Face Masks during the SARS-CoV-2 Pandemic,” the German researchers evaluated 3D printed mask specimens, comparing them to standard protective face masks.
Both rigid and foldable designs were examined with a respirator fit test. The scientists downloaded free 3D designs from internet sites, and then printed some samples “as is,” while modifying others. The Bundeswehr Research Institute for Protective Technologies and NBC Protection (WIS) in Munster partnered with the researchers for testing the masks regarding efficiency and safety. Six prototypes were assessed in all, with only two designs modified by the researchers.
Masks for the study were created at the Laboratory for Manufacturing Technologies of the University of the German Armed Forces in Hamburg, using Fusion 360 and Cura. Desktop 3D printers like the Ultimaker 3 were set up at the Neurosurgical Department of the German Armed Forces Hospital in Westerstede for the project.
The open-source face masks included:
“The foldable Copper 3D NanoHack mask was further developed and adapted to the requirements of the physicians represented in the working group using the previously described design process,” explained the researchers. “This led to the production of two modified versions, the HSU/BwKWST FM V3 (V3) and HSU/BwKWST FM V4 (V4). The COVID-19 Mask V2 was available in different sizes. For comparison, printing of the large mask with thick wall diameter, which was provided in the downloadable file, was chosen.”
White PLA and black thermoplastic polyurethane were used on the masks which were then assembled according to instructions.
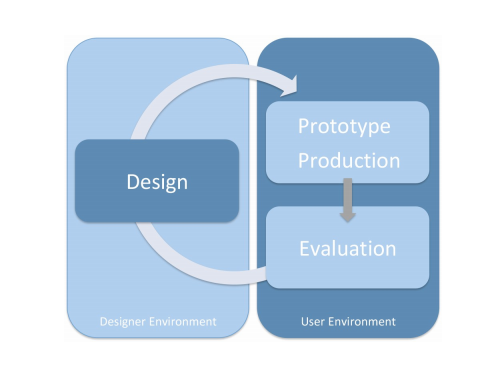
Mask design development was performed at the designer environment at the Laboratory for Manufacturing Technology at the University of the German Armed Forces in Hamburg. The design variants were then digitally transferred to the user environment at the Department of Neurosurgery at the Hospital of the German Armed Forces in Westerstede. After prototype production, the designs of the masks were evaluated. The requirements for the next design variant were then sent to the designer for further modification and development.
Users in the working group were able to make masks from design to printing within three to four hours. The researchers noted that for one day of work, three “iteration” loops were possible. Designs like HSU/BwKWST FM V1 were modified and improved in terms of filtering, allowing for an FFP3 filter to be used. The filtering area itself was also doubled. HSU/BwKWST FM V2 (V2) features replaceable filter materials. The HSU/BwKWST FM V3 (V3) model was designed with a TPU sealing lip around the outer contour for better tightness against the face.
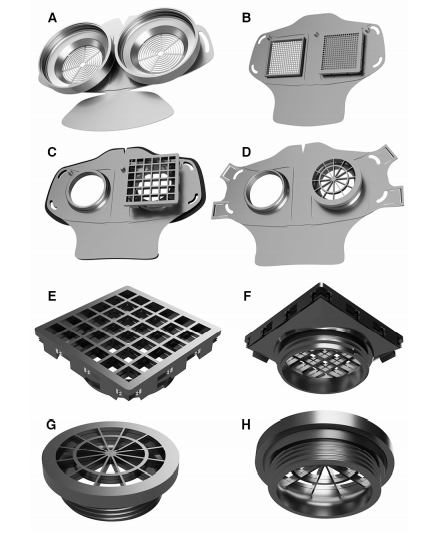
Four different variants of the HSU/BwKWST Face Masks were produced. The HSU/BwKWST FM V1 is shown in A. B depicts the HSU/BwKWST FM V2 with a new mask design at the chin area, fixation pins for an additional face shield and altered fixation holes for elastic bands. C HSU/BwKWST FM V3 with an additional inlay made from black TPU95A (black rim) and a novel design of the nasal cut. D shows the further developed HSU/BwKWST FM V4 with four fastening strips and without the TPU inlay that was previously incorporated to V3. E and F show the square filter design with a clip fastening mechanism and G and H the round filter design with a fastening thread.
“The HSU/BwKWST FM V1 and V2 were designed, shipped, printed and evaluated according to the described design process between the Laboratory for Manufacturing Technologies at the University of the German Armed Forces and the Department of Neurosurgery at the German Armed Forces Hospital in Westerstede. Only the HSU/BwKWST FM V3 and V4 were released for further tests,” explained the researchers.
The Maker Mask stood out as requiring the most material and time, as well as a more complex assembly. Users must be prepared to melt and super glue filter boxes and valves, for example. Other issues arose in terms of masks like the foldable HSU/BwKWST FM V3 and V4 as small folds appeared during thermoforming.

A Depiction of the individual parts of the foldable HSU/BwKWST FM V4 made from
thermoplastic PLA. B HSU/BwKWST FM V4 test fitted to the experimenter’s face.
“Next to that an investigation of whether the folding of the previously flat masks affects the filament and fiber structure of the PLA within the HSU/BwKWST FM V3 and V4 is necessary, as it could have led to micro leakages,” stated the researchers. Filter fixation was noted best in the Montana and Maker Masks, with the others appearing to be prone to leakage.
Overall, the results were fairly poor, with the authors emphasizing the enormous popularity of 3D printing masks; however, in reality, the methods and materials used currently are not sufficient enough for them to recommend the use of FDM 3D printed masks:
“Regarding the problem of safety of a widespread use of 3D printed face masks in a pandemic, we conclude that in spite of their sometimes overly euphoric presentation in the press and the online media, none of the currently advertised 3D printed face mask designs looked at in our study are suitable as a reliable personal protective equipment. Main reasons for this are the low flexibility of the material and the thin sealing line preventing the necessary sealing performance on the face and leakages related to the connection of the masks with the filter material caused by the simplified filter and filter box construction.”

The Protective Factor (PF) was calculated from the particle concentration outside the mask divided by the particle concentration inside the mask. Data is presented as mean ± standard deviation of the mean. The best single value calculated for each mask is represented as x in the corresponding, group specific, color.
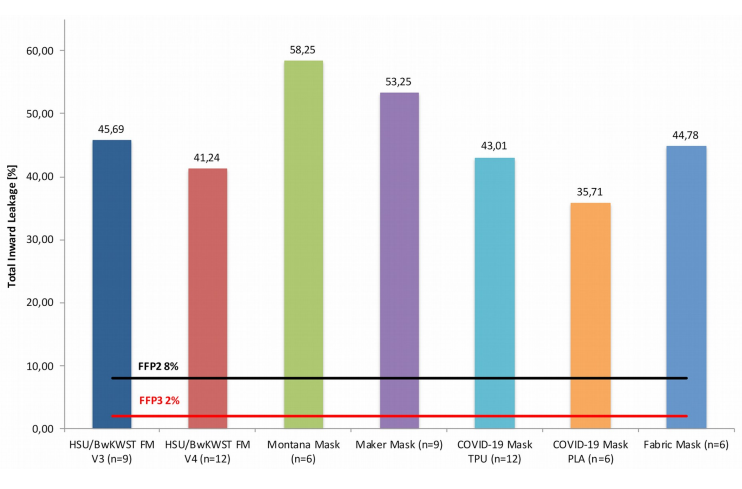
The Total Inward Leakage (TIL, %) was calculated from 100 divided by the PF and is presented in %. Reference parameters are Filtering Face Piece 2 (FFP2, red line, 8%) and Filtering Face Piece 3 standards (FFP3, black line, 2%) according to the DIN EN 149 regulation.
Find out more about 3D printed PPE over the past year, from open-source ventilators to face shields and other masks, as well as opinion regarding cautions during the pandemic.
[Source / Images: “Potential Risks of a Widespread Use of 3D Printing for the Manufacturing of Face Masks during the SARS-CoV-2 Pandemic”]Subscribe to Our Email Newsletter
Stay up-to-date on all the latest news from the 3D printing industry and receive information and offers from third party vendors.
Print Services
Upload your 3D Models and get them printed quickly and efficiently.
You May Also Like
Havaianas Collaborates with Zellerfeld to Launch 3D Printed Flip-Flops
The shoe of the summer is undoubtedly the flip-flop. Easy on, easy off, your feet won’t get sweaty because there’s not much material, and they’re available in a veritable rainbow...
UCLA Researchers Develop 3D Printed Pen that May Help Detect Parkinson’s Disease
Diagnosing Parkinson’s disease is difficult. Often, early symptoms of the progressive neurological condition may be overlooked, or mistaken for signs of aging. Early diagnosis can help save lives and improve...
Printing Money Episode 30: Q1 2025 Public 3D Printing Earnings Review with Troy Jensen, Cantor Fitzgerald
Printing Money is back with Episode 30, and it’s that quarterly time, so we are happy and thankful to welcome back Troy Jensen (Managing Director, Cantor Fitzgerald) to review the...
Heating Up: 3D Systems’ Scott Green Discusses 3D Printing’s Potential in the Data Center Industry
The relentless rise of NVIDIA, the steadily increasing pledges of major private and public investments in national infrastructure projects around the world, and the general cultural obsession with AI have...