Researchers from Italy and Sweden add to the ongoing trend for improving bioprinting techniques and materials. Upon developing bio-based photocurable materials for 3D printing and bioprinting with hydrogels, the authors released the details of their study in ‘DLP 3D Printing Meets Lignocellulosic Biopolymers: Carboxymethyl Cellulose Inks for 3D Biocompatible Hydrogels.’
Modified carboxymethyl cellulose was at the center of this experiment for bioprinting with digital light processing (DLP). While more commonly used as a filler, cellulose has been used in other inks. Beginning the research with the study of lignocellulosic biopolymers, the authors explained that they present a range of options for printing with DLP, while carboxymethyl cellulose (CMC) is often used in food, paint, and detergents. For this reason, it is a sustainable material with particular utility in bioprinting.
Approved by the FDA, and deemed biocompatible, CMC is water-soluble, versatile, and considered “an ideal candidate for the preparation of novel photocurable resins for DLP.” These types of formulations can also imitate cell microenvironments because of their similar makeup to glycosaminoglycan found within the extracellular matrix.
“Due to its versatility, its advantageous properties, water-solubility, and susceptibility to further functionalization, we also expected CMC would be an ideal candidate for the preparation of novel photocurable resins for DLP,” explained the authors. “However, the use of light-assisted printing techniques requires reactive photocrosslinkable functional groups, which means CMC needs functionalization to produce ink formulation for the production of 3D photocured hydrogels.
“CMC was therefore methacrylated and its photorheology and DLP printability was investigated in two formulations, namely, M-CMC/Dulbecco’s Modified Eagle Medium (DMEM) and M-CMC/water, in presence of a fixed amount of lithium phenyl-2,4,6-trimethylbenzoylphosphinate (LAP) photoinitiator.”
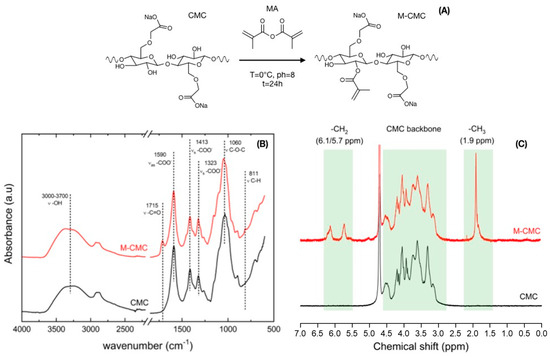
(A) Scheme for the methacrylation of carboxymethyl cellulose (CMC). The presented product only presents one of the possible reaction products. (B) FTIR and (C) 1H NMR spectra for methacrylated CMC (M-CMC, red) and neat CMC (CMC, black).
During evaluation, the authors also investigated compatibility for hydrogels, with M-CMC solubilized in a culture medium (DMEM). Rheological properties (storage modulus, G′, and loss modulus, G″) were evaluated during UV curing for CMC/DMEM/LAP and M-CMC/water/LAP:
“Although the formulation M-CMC/DMEM/LAP showed a slight delay with respect to the onset of the curing process, the DMEM medium still allowed sufficient light penetration for the photocuring process in view of 3D printing,” said the researchers.
Both the CMC/DMEM/LAP and M-CMC/water/LAP formulations proved to be stable after 90 s of UV irradiation. Hydrogels were created from both formulations, and deemed “extremely promising” in comparison with other DLP biocompatible materials.
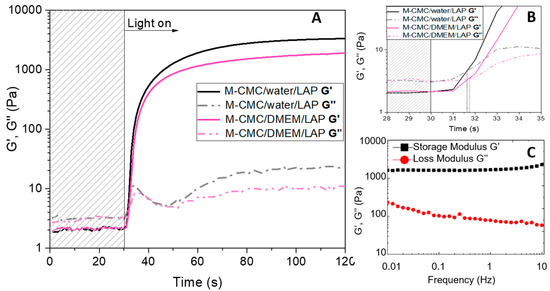
(A) Photorheology of methacrylated carboxymethyl cellulose (M-CMC) 20 mg/mL (2 wt% lithium phenyl-2,4,6-trimethylbenzoylphosphinate (LAP)) solubilized in water (black) or in culture medium (pink). (B) Gel point. Film thickness 300 m. (C) Frequency sweep. Strain rate 1% and oscillation frequency from 0.01 to 10 Hz.
The researchers created a variety of 3D printed samples, to include cylinders, parallelepipeds, and other complex structures—all stemming from the M-CMC/DMEM/LAP and M-CMC/water/LAP formulations. On further evaluation, the hydrogels were stable, flexible, and the photocrosslink reaction was completed. Although dyes can be helpful in limiting light diffusion, there is also the risk of cytotoxicity, leading the authors to avoid such use in this study.

3D printed M-CMC hydrogels. (A) Simple cylinders and parallelepipeds (solvent: water). (B) The hydrogel exhibited good flexibility and handleability. (C) SEM analysis performed on the freeze-dried hydrogel. (D–F) 3D objects printed from water (D) and from culture medium solution (E,F).
Crosslinking and reactivity were further evaluated, along with compression tests, assessment of swelling ability, and cytotoxicity testing to investigate lack of cell death due to release of LAP photoinitiator or unreacted polymer chains. Ultimately, the team of researchers reported that there were no signs of cytotoxicity, and overall, their work was successful with cells exhibiting viability similar to control samples.

3D-printed M-CMC hydrogels. (A) Simple cylinders and parallelepipeds (solvent: water). (B) The hydrogel exhibited good flexibility and handleability. (C) SEM analysis performed on the freeze-dried hydrogel. (D–F) 3D objects printed from water (D) and from culture medium solution (E,F).
Subscribe to Our Email Newsletter
Stay up-to-date on all the latest news from the 3D printing industry and receive information and offers from third party vendors.
Print Services
Upload your 3D Models and get them printed quickly and efficiently.
You May Also Like
Johns Hopkins University Researchers Develop HyFAM Technology
Two scientists from Johns Hopkins University, Nathan C. Brown and Jochen Mueller, have developed a hybrid manufacturing technology they call HyFam, or Hybrid Formative Additive Manufacturing. Their work on this technology...
3D Printing G-Code Gets an Upgrade: T-Code
Good old G-Code still manages many 3D printers, great and small. Just like the STL, it’s a standard that enables collaboration while also holding the additive manufacturing (AM) industry back....
AM Rewind: The Biggest News and Trends of 2024
After a sluggish 2023, driven by persistent inflation and geopolitical tensions, 2024 has seen some recovery. Economic growth climbed from about 2.8 percent in 2023 to a modest 3.2 percent...
Metal Wire 3D Printer OEM ValCUN Announces Plans for 2025 Expansion
ValCUN, a Belgian original equipment manufacturer (OEM) of wire-based metal additive manufacturing (AM) hardware, has announced that the company has entered the next phase of its growth trajectory, making key...