German researchers associated with the Integrated Research Platform for Affordable Satellites project are looking for new ways to produce satellites, releasing the details of a recently published study in “Production and planned in-orbit qualification of a function-integrated, additive manufactured satellite sandwich structure with embedded automotive electronics.”
Satellites, now being designed and manufactured by a wide range of companies, from those engaged in aerospace applications to offering Internet access, as well as ongoing scientific research, are becoming the source of much greater commercial focus. Affordability is the key though, with viability reliant on unit cost as well as expenses involved in transporting the structures to their particular operating orbits.
“In order to succeed in this increasingly dynamic and cost-driven competition, the space industry must break new ground in technology, development, production and cooperation,” explained the authors.
This means greater attention in the future will have to be paid to the quality and longevity of the satellites, as well as maintenance, repair, and replacement issues. In researching satellite cost, the researchers examined how much parts cost, along with the idea of using off-the-shelf (Commercials Off-The-Shelf [COTS]) automotive components.
Project leaders within the Integrated Research Platform for Affordable Satellites (IRAS) project include a consortium made up of the following:
- German Aerospace Center (DLR)
- Fraunhofer Institute for Manufacturing Engineering and Automation (IPA)
- Institute for Space Systems of the University of Stuttgart (IRS)
Together, the group is looking into affordability, series production of satellites for “mega-constellations,” and studying the potential for the use of automotive electronics, as well as 3D printing.
While it may be surprising for some to hear that the consortium is looking toward the auto industry for inspiration, it makes sense when you consider the enormous range of innovative electronics and parts that they must generate to keep consumers interested in a fiercely competitive market. Not only that, COTS have actually been used for a long time by aerospace engineers due to benefits like better performance, smaller volume, and better energy efficiency.
Magnetic sensors are a good example of components that could translate to space applications, along with different types of material compounds. Most likely, miniaturization would be required; however, that is advantageous in terms of savings on the bottom line.

Left: board with space components and space manufacturing guidelines; middle: board with automotive components (space manufacturing guidelines), right: board with automotive components and adapted manufacturing guidelines
“In order to improve the functional density of satellites and their structural elements, the integration of electronics into structural elements is now to be investigated. Therefore, typical automotive components are used, and their suitability for satellite construction is evaluated,” explained the researchers.
The benefits of additive manufacturing processes have already been explored by previous researchers creating a variety of different satellites from large to small, and including other parts, like filters. Affordability figures into these designs, but also a host of other classic benefits arising from 3D printing like speed in production, the ability to create lightweight but strong components—and most importantly, the potential for creating designs and prints that would not be possible with conventional technology.
A variety of different thermoplastics can be used in space, including polyetheretherketone (PEEK) and polyetherimide (PEI). For most parts to be used in space, the goal is to fabricate structures that are able to withstand heavy loads as well as being fitted with other parts like cables.
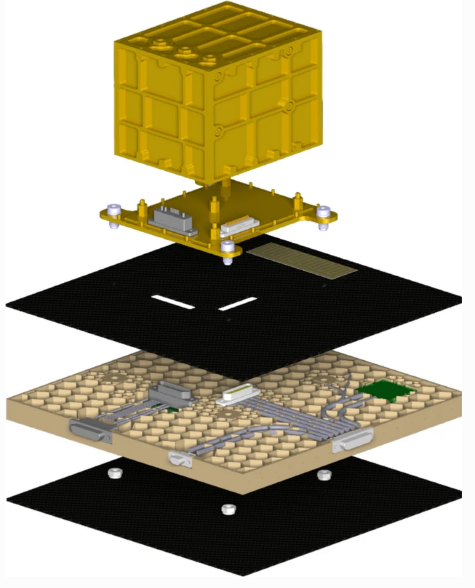
Corresponding demonstrator design developed by the German Aerospace Center (DLR). This design was the base for further test models. The approach envisages printing a honeycomb core between two fiber composite panels, which are designed to withstand high loads and can be fitted with cavities for cable harnesses and electronic components.
Settling on PEI as the preferred choice of materials, the researchers experimented further, 3D printing three samples. They were assessed in terms of accuracy, potential for warping, oozing, and imaging of structures consisting of thin walls. Filament by 3DXTech was chosen for fabrication during the study as the researchers printed directly onto a fiber composite board. Sandwich panels were then 3D printed with PEI into a honeycomb core structure.
Samples were failed in the first tests, destroyed by the high load. This was attributed to gas inclusions inside the material.
“These inclusions remain during solidification of the polymer in the component and significantly reduce its mechanical properties. This effect is likely to be responsible for the failure of the samples in the vibration and thermal vacuum tests. Further investigations with sufficiently dried polymer filament are still pending,” explained the researchers.
In-orbit experimentation consisted of measuring the 3D printed “sandwich” by measuring vibration via an integrated piezo actuator. In the second experiment, the researchers observed the performance of the automotive electronics, measuring the activity of a MEMs sensor and an analog-to-digital converter.
For future studies, the researchers are also hoping to improve affordability with alternative polymers—saving energy and cost with the use of lower processing temperatures.
[Source / Images: “Production and planned in-orbit qualification of a function-integrated, additive manufactured satellite sandwich structure with embedded automotive electronics”]Subscribe to Our Email Newsletter
Stay up-to-date on all the latest news from the 3D printing industry and receive information and offers from third party vendors.
Print Services
Upload your 3D Models and get them printed quickly and efficiently.
You May Also Like
3D Printing News Briefs, July 2, 2025: Copper Alloys, Defense Manufacturing, & More
We’re starting off with metals in today’s 3D Printing News Briefs, as Farsoon has unveiled a large-scale AM solution for copper alloys, and Meltio used its wire-laser metal solution to...
3DPOD 260: John Hart on VulcanForms, MIT, Desktop Metal and More
John Hart is a Professor at MIT; he´s also the director of the Laboratory for Manufacturing and Productivity as well as the director of the Center for Advanced Production Technologies....
3D Printing News Briefs, June 28, 2025: Defense Accelerator, Surgical Models, & More
In this weekend’s 3D Printing News Briefs, 3YOURMIND was selected to join an EU Defense Accelerator, and PTC has announced model-based definition (MBD) capabilities within Onshape. Finally, a study out...
EOS in India: AM’s Rising Star
EOS is doubling down on India. With a growing base of aerospace startups, new government policies, and a massive engineering workforce, India is quickly becoming one of the most important...