We’ve recently covered LEAP and continuous liquid interface production (CLIP), as ultra-fast 3D printing technologies that are enabling production-level manufacturing output and speed for 3D printing. However, CLIP (41.4cm by 25.9cm) and LEAP are critically limited, with small build sizes, output volumes, and resin materials, and this is where High Area Rapid Printing (HARP) is breaking records.
Published first in Science in October 2019, HARP is a patent-pending continuous digital light processing (cDLP) method, in which build size and certain resin materials are no longer a limitation for cDLP. It can print objects the size of adult humans in two hours, and in one day it can print 300 6.5-inch sized ornaments or 1000, potentially 2000, face shields. With HARP, printing speeds exceed half a meter an hour, which is a record level in this printer class for the 3D printing industry. In fact, with its unique “tiling” mechanism, the size of objects printed is “theoretically unlimited” and the printer can be scaled without limit. In addition, although cDLP 3D printing is known to require secondary processing techniques, such as heat treatment and additional UV curing, with HARP, high-resolution light patterning produces final parts which require little post processing.
Interestingly, the inventor of HARP and founder of US-based Azul 3D, Dr. Mirkin, is a close colleague of Dr. DeSimone, the inventor of CLIP and founder of Carbon. A Professor of Chemistry at Northwestern University, Dr. Mirkin has led research to develop HARP to address many of the limitations with CLIP, in terms of heat and resulting build size, applicable resins, and is said to be ten times faster. An area where HARP fundamentally differs from CLIP, is that, where CLIP uses a thin layer of oxygen to inhibit resin curing, HARP uses a liquid interface to remove heat generated from the print process, eliminate or drastically reduce bed adhesion, and expand the use materials to include oxygen-insensitive resins as well. HARP can print with a broad range of photopolymers, including rubber-like, machinable, flexible, and high-temperature ceramics, expanding its scope and application for production across industries.
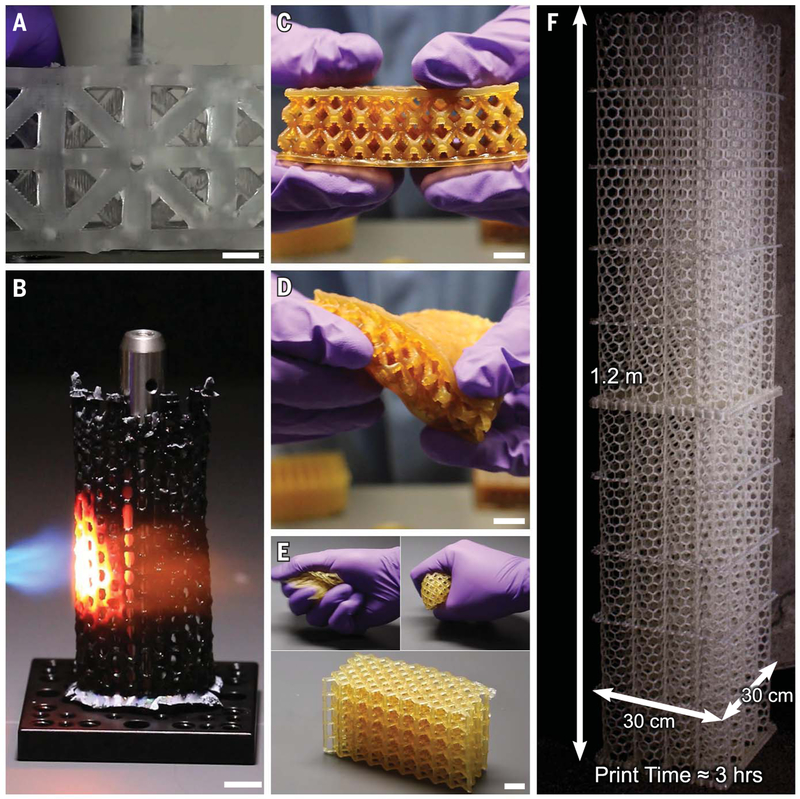
Image courtesy of Science, and Northwestern University
A critical limitation with DLP technology was addressing the heat released (often over 180 degrees Celsius) when the resin layers cure, often resulting in warped or cracked parts. With HARP, a liquid coolant (fluorinated oils) circulates below the resin, creating a mobile, non-stick interface (referred to as “liquid Teflon” by Northwestern University researchers) that directly extracts heat as the object prints vertically, keeping surface part temperatures at 100 to 120 degrees Celsius. The non-stick surface also means each resin layer does not adhere to the bottom of the VAT after curing—and does not have to be separated each time, allowing for a hundredfold increase in printing speed. This enables HARP printers, 13 feet tall with a 2.5 square foot bed size, to build at rates over 430 mm/hr and output over 100 liters/hr. With this, HARP fundamentally improves on CLIP in ways that could prove a game-changer for 3D printing production using SLA-based technologies.
To address the #PPE shortage, Northwestern researchers @CHADNANO and David Walker are generating 1,000 face shield components a day through a new #3Dprinting technique. pic.twitter.com/72TBH2cwEb
— Northwestern (@NorthwesternU) May 13, 2020
The technology has already been used in Chicago, US to print face shields during COVID-19, producing over 1000 per day. Newer versions of the printer are expected to double this capacity. In October 2019, research results regarding HARP were published in Science, followed by an announcement the technology would be commercially available in 18 months. Today, HARP is being commercialized by Azul 3D, and in May this year, the company received second stage seed financing of over $8 million, with recent cash infusions of $5.4 million to launch the first commercial HARP printers. Additionally, Jennifer Lewis, world-renowned pioneer in microscale 3D printing and bioprinting, and Wyss Institute Professor at Harvard University, has joined the Technical Advisory Board at Azul 3D, expanding its leadership team. Azul 3D plans for its early clients or beta partners to receive the first printers in the first quarter of 2021, with production-ready printers to be shipped by the end of 2021.
Subscribe to Our Email Newsletter
Stay up-to-date on all the latest news from the 3D printing industry and receive information and offers from third party vendors.
Print Services
Upload your 3D Models and get them printed quickly and efficiently.
You May Also Like
Reinventing Reindustrialization: Why NAVWAR Project Manager Spencer Koroly Invented a Made-in-America 3D Printer
It has become virtually impossible to regularly follow additive manufacturing (AM) industry news and not stumble across the term “defense industrial base” (DIB), a concept encompassing all the many diverse...
Inside The Barnes Global Advisors’ Vision for a Stronger AM Ecosystem
As additive manufacturing (AM) continues to revolutionize the industrial landscape, Pittsburgh-based consultancy The Barnes Global Advisors (TBGA) is helping shape what that future looks like. As the largest independent AM...
Ruggedized: How USMC Innovation Officer Matt Pine Navigates 3D Printing in the Military
Disclaimer: Matt Pine’s views are not the views of the Department of Defense nor the U.S. Marine Corps Throughout this decade thus far, the military’s adoption of additive manufacturing (AM)...
U.S. Congress Calls Out 3D Printing in Proposal for Commercial Reserve Manufacturing Network
Last week, the U.S. House of Representatives’ Appropriations Committee moved the FY 2026 defense bill forward to the House floor. Included in the legislation is a $131 million proposal for...