Production-grade 3D printing solutions supplier Optomec is well-known for its patented Aerosol Jet Systems for printed electronics and LENS printers, using DED technology, for making high value metal parts. In December of 2018, Optomec acquired Huffman in an effort to increase its reach in the gas turbine market, which has used additive manufacturing to fabricate components. Now, Optomec has announced a new tool that will allow customers repairing gas turbine parts to acquire more insight into how much money they can save by using an automated manufacturing process like 3D printing.
The tool is a calculator that provides an ROI (return on investment) assessment for the automated repair of turbine blades. It calculates the payback that gas turbine maintenance and repair operations (MRO) will receive when using Optomec’s automated laser cladding equipment, which is certified in 15 countries, for this application in the energy and aviation markets.
By using Optomec’s vast experience in producing and repairing 10 million industrial turbine blades for just about every major manufacturer of industrial gas turbines and aircraft engines, the company’s clients can quickly and easily determine if the capital equipment cost is worth it with the ROI calculator.
“Despite the fact that many MROs have moved to automated processes, the majority of turbine and compressor blade repair is still done manually today. In our work with customers, we recognized that a wide range of factors contribute to building the business case for automated laser cladding and that is why we felt the need to develop this tool,” Mike Dean, Marketing Director at Optomec, stated in a press release sent to 3DPrint.com. “With our ROI calculator we can help more MROs understand the real value and impact automation can have. In addition to the cost savings, there are huge benefits in terms of higher repeatability and superior metallurgy from automated laser cladding.”
Terry VanderWert PE, a laser processing expert in the aerospace, aviation, medical and power industries, developed the new MRO ROI calculator for Optomec, which piggybacks off of research that he completed while writing a white paper, titled “The Business Case for Automated Laser Cladding in Aviation Component Repair: Five Lessons Learned,” for Optomec.
“The cost of repairing high value gas turbine engine (GTE) components is around 70% lower than that of purchasing new ones. This has created a strong business case for repair. However, the high difference in cost between new and repaired components has also fostered tolerance for inefficient, labor-intensive manual repair processes,” the white paper states.
“As with most investments, it is critical to invest in the correct equipment and technology.”
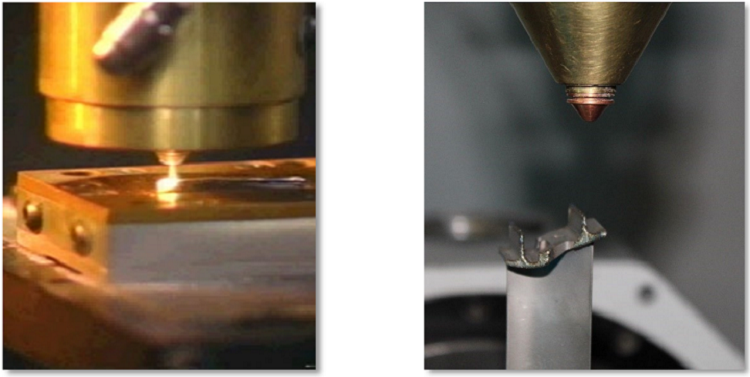
(L-R) Laser beam focusing and metal powder delivery head for automated laser cladding; Laser cladding-
based repair of a Z-notch before hard-facing alloy is added.
Optomec’s new calculator collects customer-specific data in specific, important areas, which allows it to create a report that will calculate how much more money automated laser cladding technology the customer will save compared to its current manufacturing process, often manual TIG welding. The tool also calculates internal rate of return, cost per part, net present value, and payback period.
You can try out Optomec’s new MRO ROI calculator for yourself here.
(Images courtesy of Optomec)
Subscribe to Our Email Newsletter
Stay up-to-date on all the latest news from the 3D printing industry and receive information and offers from third party vendors.
Print Services
Upload your 3D Models and get them printed quickly and efficiently.
You May Also Like
3D Printing News Briefs, July 2, 2025: Copper Alloys, Defense Manufacturing, & More
We’re starting off with metals in today’s 3D Printing News Briefs, as Farsoon has unveiled a large-scale AM solution for copper alloys, and Meltio used its wire-laser metal solution to...
3DPOD 260: John Hart on VulcanForms, MIT, Desktop Metal and More
John Hart is a Professor at MIT; he´s also the director of the Laboratory for Manufacturing and Productivity as well as the director of the Center for Advanced Production Technologies....
3D Printing News Briefs, June 28, 2025: Defense Accelerator, Surgical Models, & More
In this weekend’s 3D Printing News Briefs, 3YOURMIND was selected to join an EU Defense Accelerator, and PTC has announced model-based definition (MBD) capabilities within Onshape. Finally, a study out...
EOS in India: AM’s Rising Star
EOS is doubling down on India. With a growing base of aerospace startups, new government policies, and a massive engineering workforce, India is quickly becoming one of the most important...