In late 2018, Avio Aero, acquired by GE Aviation several years ago, inaugurated its second additive manufacturing plant in Brindisi, Italy, which, after a lot of structural work, was transformed into a more modern factory in order to 3D print aviation parts using direct metal laser melting (DMLM) technology (also called Laser Powder Bed Fusion, DMLS, Selective Laser Melting etc). The plant is specifically focused on 3D printing parts for the GE Catalyst engine, which will eventually be used in the lightweight Cessna Denali.
This will be the world’s first turboprop engine with almost 30% of its internal parts fabricated by metal 3D printing, and the technology has made it possible to reduce the total number of engine parts from a whopping 855 all the way down to just 12. Up to ten of these components will be 3D printed at Avio’s new facility in Brindisi, which employs a team of 12 operators, process material experts, production engineers, and additive designers led by Additive Manufacturing Leader Dario Mantegazza. As the plant adds more Concept Laser DMLM systems, the number of Catalyst components produced there could increase, which will also result in the team growing.
“The number of people on our team will double, and when we’ll be at full capacity, we expect volumes to exceed 300 engines per year,” Mantegazza said.
There are currently three DMLM printers operating at the Brindisi plant, with two systems for post-processing. By the end of 2020, this number is expected to double, and the facility will reach full capacity – 15 more DMLM machines – between 2022 and 2023.
Mantegazza learned about electron beam melting (EBM) 3D printing at Avio’s Cameri plant, which 3D prints turbine blades for the largest commercial engine in the world – the GE9X.
“When I was at Cameri, we facilitated the introduction of EBM technology to GE, as well as learning and coaching for industrialization. For the last couple of years, we have also been learning how to optimize and industrialize DMLM technology,” Mantegazza explained. “Now we are finally ready to apply it in production for the first products.”
The two Italy plants collaborate often with the team at the modern 150,000-square-foot Additive Technology Center (ATC) near Cincinnati, Ohio, not far from GE Aviation’s headquarters.
At the ATC, AM processes are developed for internal and external customers using EBM and DMLM technologies, as well as for materials and digital capabilities, since the plant is dedicated to, as GE Aviation puts it, “the technology that has disrupted the traditional paradigms of industrial production.”
“We are currently working on products for about 10 military and civil aircraft programs, including the newest and most advanced ones, such as the LEAP, GE9X and of course GE Catalyst,” said ATC Plant Leader Antroine Townes. “In addition to production, Digital IT, R&D and Engineering teams work here, too.”
Townes and Mantegazza met while the latter was visiting the ATC in 2018.
“We began working together about two years ago and will continue to do so for about five years in all. It is absolutely to our mutual benefit. We exchange knowledge and nurture our trust in each other,” Townes stated. “Our work on the Catalyst program is to transfer the production of all additive parts from Ohio to Brindisi. We started with the smaller ones and we will eventually get to the bigger ones. At that point, Brindisi will be self-reliant and dedicated to Catalyst. Then we will continue to deal with other aircraft engines that already have additive parts and those that will have them in the future.”
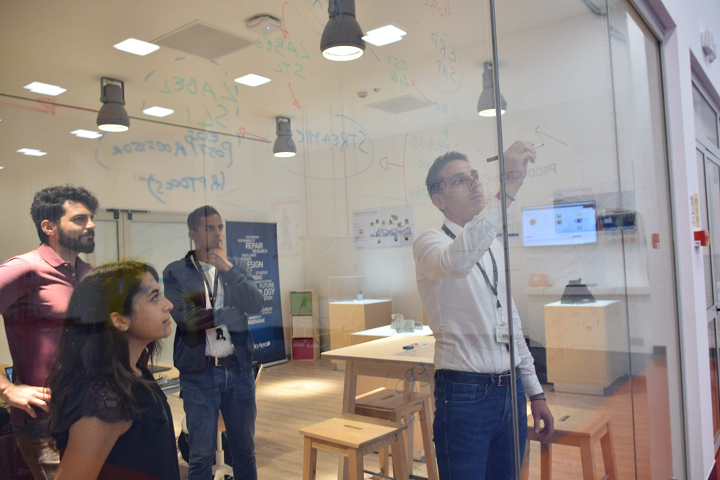
Dario Mantegazza, Additive MFCTG Leader at Avio Aero Brindisi, during a meeting inside the new factory.
“ATC is a key partner, a great Lean Lab. During this transfer process we collaborate daily with Antroine and our American colleagues. This is the only way we can guarantee the full maturity of the products that enter production in Brindisi,” Mantegazza said. “Furthermore, in Avio Aero, we can also rely on the industrial optimization and development activities performed within our laboratories that have partnered with universities—just like they do, for instance, at TAL.”
About 85% of the products processed at the ATC will be used in aviation applications, including parts for the Catalyst.
“The engine program in question is brand new. There are numerous challenges and the technological content is highly complex because no one has ever ventured into this industrial enterprise before,” said Sandra Babylon, the Transition Leader in Brindisi, who makes certain during the transition that production processes, shapes, and quality fit.
“From the very beginning, everyone I worked with at Avio Aero seemed to be highly motivated, eager to fully integrate technology and products. The Cameri experience is certainly useful, but at this level of innovation, the solutions to problems, and therefore the opportunities to learn, are continuous.”
Manufacturing processes aren’t the only things that change when AM is adopted, as workers continue to learn in this modern environment to grow their skill sets.
“Awareness of the capabilities that additive offers is growing continuously. Operators are also maintenance personnel with enhanced digital programming skills. The synergy in factory management is also greatly improved and the team intertwines its individual skills,” Mantegazza notes. “EBM and DMLM are not competing technologies; on the contrary, each has its own unique advantages. And the beauty of it is that we have not discovered them all yet.”
Originally, the GE Catalyst was scheduled to have its first flight by the end of 2019. But GE has not yet delivered the engine to Textron Aviation, which means that no test flights have taken place. The company is now projecting that the first flight won’t happen until sometime this year.
(Source/Images: GE Aviation)
Discuss this and other 3D printing topics at 3DPrintBoard.com or share your thoughts below.
Subscribe to Our Email Newsletter
Stay up-to-date on all the latest news from the 3D printing industry and receive information and offers from third party vendors.
Print Services
Upload your 3D Models and get them printed quickly and efficiently.
You May Also Like
Consolidation in AM: How 2025 Is Shaping the Industry’s New Normal
The first half of 2025 has been marked by a clear shift in the additive manufacturing (AM) industry. Companies are no longer just focused on developing new tech by themselves....
Etsy Design Rule Change Reduces Selection of 3D Printed Goods
Online marketplace Etsy has implemented a rule change requiring all 3D printed goods on the site to be original designs. The update to the site’s Creativity Standards states, ¨Items produced using...
U.S. Congress Calls Out 3D Printing in Proposal for Commercial Reserve Manufacturing Network
Last week, the U.S. House of Representatives’ Appropriations Committee moved the FY 2026 defense bill forward to the House floor. Included in the legislation is a $131 million proposal for...
Transforming From Tourist to Native: Duro CEO Michael Corr Explains Why the Company Rebuilt its PLM Software on AI
In these early innings of the AI boom, many market analysts have expressed concern that AI spend has gotten too far ahead of the technology’s proven ability to deliver significant...