A complex tibial plateau fracture, mainly caused by high-energy injuries, affects the knee and generally means the person is unable to walk. If that isn’t hard enough, all kinds of complications can happen if the fracture doesn’t heal right, like joint deformity, wound infection, and traumatic arthritis. If allowed to develop into an old fracture, it’s harder for orthopedic surgeons to fix. So pre-operative surgical planning is pretty important. For the most part, CT and X-ray images are used, but 3D printing can be used to achieve better personalized plate fixation. Four researchers from Henan Orthopedic Hospital in China hypothesized that using a 3D printed model in pre-operative simulation could help improve the outcomes of complex and old tibial plateau fracture surgery, and reduce the overall operation time.
The team wrote about the results of their study in a paper, “Pre-operative simulation using a three-dimensional printing model for surgical treatment of old and complex tibial plateau fractures.”
“Thus, the aim of the study was to compare the outcomes between patients treated with and without the assistance of the 3D printed models and to evaluate the feasibility and effectiveness of 3D printing model simulation for preoperative planning,” they wrote.
There are several advantages to using 3D printed models in pre-operative simulation:
- It helps surgeons understand the morphology of fracture collapse and fragments to determine the right surgical approach
- The correct plate can be chosen and shaped in advance, along with the length, direction, and fixation position of the screw
- Surgeons can bring the model into the OR and use it during the operation to improve efficiency
- Treatment plans can be more easily discussed with patients and create a better doctor-patient relationship
The researchers reviewed 42 patients with old and complex tibial plateau fractures over the course of four years. They all had verified old tibial plateau fractures and a complex fracture of type IV, V, or VI, and their pre-op planning was based on a 3D printed model or 3D-CT images.
“There were 27 males and 15 females with a mean age of 42.93 ± 7.69 years (ranged from 29 to 55 years). Mean body mass index (BMI) was 23.98 ± 5.08 kg/m2 (ranged from 20.76 to 28.04 kg/m2). The right knee was involved in 24 cases and the left knee in 18 cases,” the researchers explained. “Seventeen patients were caused by falling from height, 15 by traffic accident, and ten by other injury. The mean time from admission to hospital to surgery was 25.83 ± 5.15 days (ranged from 21 to 40 days).”

A 45-year-old female patient with an old & complex tibial plateau fracture. (a) Preoperative X-ray film showing the left tibial comminuted fracture (type V). (b) 3D-CT images of the fracture.
They were divided into two groups: whether their pre-op planning was based on 3D-CT images (conventional planning group) or 3D printed equal-ratio fracture models (planning with 3D printing group). For the second group, the tibia and fibular were scanned “from the distal part of the fracture to the tibial plateau surface,” and the CT data was imported into Materialise Mimics to build the 3D digital model.
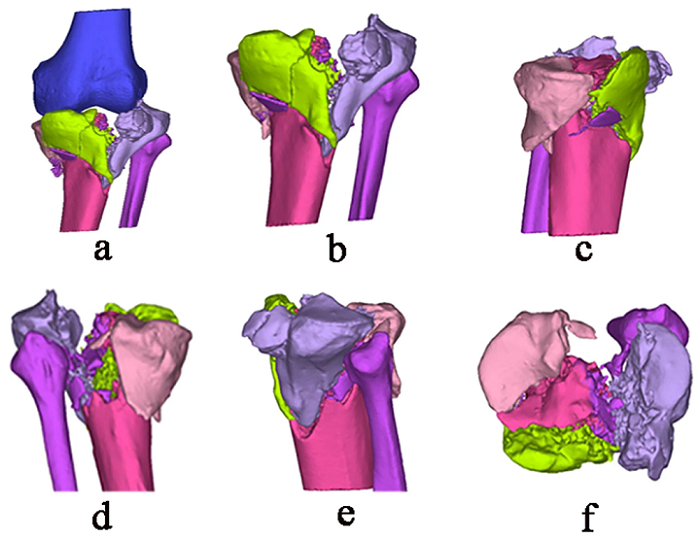
3D reconstruction of the old & complex tibial plateau fracture in Mimics software v10.01. (a) Whole view of the knee joint (blue, femoral condyle; other colors represent different fragment of tibial plateau fracture). (b) Anterior, (c) medial, (d) posterior, (e) lateral, and (f) cross-sectional views of fracture.
The patient-specific fracture models were printed with PLA. It was easy to see the structural characteristics of the fractures, which helped in designing the surgical plan, and the surgeon simulated the “steps for the reduction and fixation of the fragments” on the models ahead of time.

3D printing model with a 1:1 ratio of the original tibial plateau fracture for pre-operative evaluation. (a) Anterior, (b) medial, (c) posterior, and (d) cross-sectional views.
The orientation, type, location, and length of the screws were recorded after plate fixation on the models, so the information could be used during surgery. The 3D printed model of the original fracture and the one “after reduction and fixation using plates and screws” were also used in the OR.
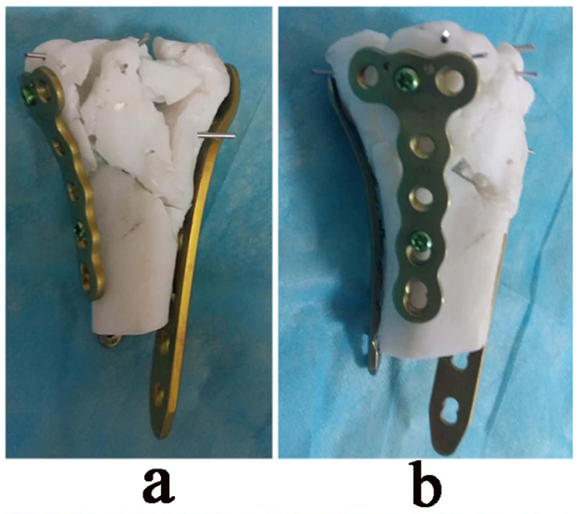
In vitro simulated reduction and plate fixation were performed on 3D printed model. (a) Anterior view of the model showing lateral and medial plate fixation. (b) Medial view showing medial and posterior plate fixation.

Fig. 5: (c) Posterior view showing posteromedial and lateral plate fixation. (d) Plates and screw length were determined and recorded.
The blood loss, number of fluoroscopy, and duration were recorded for all the operations; if you’re interested in the specifics, check out the research paper. All of the operations were performed by the same orthopedic team with one senior orthopedic doctor: co-author Dr. Honglue Tan. Allogeneic and autogenous bone grafts were implanted into the bone defects if necessary, and incisions were closed after a “satisfactory fracture reduction and fixation under “C” arm X-ray fluoroscopy.”
Post-op rehab began once the patients recovered from anesthesia, and passive and active flexion and extension of the knee joint started ASAP. Two weeks post-op, the patients could use a crutch to help in “ambulation without weight-bearing,” and then, depending on how their fracture was healing, they could begin partial and complete weight-bearing. Follow-up appointments occurred at one, three, six, and twelve months, and then annually.

(a) Post-op X-ray showing satisfactory fracture reduction and internal fixation, which were consistent with the pre-op simulation. (b) X-ray at 14 months post-op showing bone-union with no implant displacement or joint surface collapse. (c) X-ray at 6 months post-op after plate removal showing normal shape and structure of tibial plateau. (d) This patient had satisfactory knee function with an HSS score of 85.
The quality of fracture reduction and complications, such as poor incision healing, implant failure, deep venous thrombosis, and bone nonunion, were recorded at follow-up appointments, and the hospital used a special surgery (HSS) scoring system to evaluate knee function; a score of ≥ 85 points is excellent, while 70-84 is good, 60-69 is fair, and ≤59 points is poor. SPSS statistical software was used to analyze the results for the study.
“The operation time, blood loss and the number of fluoroscopy during operation in the planning with 3D printing group were less than that in the conventional planning group (P < 0.01),” the researchers explained.
“The rate of excellent fracture reduction in the planning with 3D printing group and conventional planning group was 75% and 45.45%, respectively (P = 0.05). The complication rate was 15% in the planning with 3D printing group and 31.82% in the conventional planning group. At the final follow-up evaluation, the mean HSS score was 86.05 ± 7.67 in the planning with 3D printing group and 79.09 ± 6.75 in the conventional planning group (P = 0.003). The rate of excellent results in the planning with 3D printing group was 70% and in the conventional planning group was 45.45% (P = 0.083).”
These results show that a patient-specific, 3D printed solid model of the fracture, “with an equal ratio to the actual fracture,” can help surgeons in the pre-operative planning stage. The surgeons participating in this study were able to accurately find, and record, “the reduction steps of the fragments, placement and pre-reshaping of the plates, and the measurement of the screw length” using the 3D printed model during pre-op surgical simulation. Additionally, they were able to successfully perform fragment fixation and anatomical reduction according to the pre-op planning design they made.
“Postoperative follow-up results also showed that the articular surface and plateau height remained viable, and the excellent rate of function was higher than that in the conventional planning group,” the team stated. “Taken together, the results suggest that 3D-printed fracture models facilitate the treatment of old and complex tibial plateau fractures via a more accurate and personalized approach, thus confirming its effectiveness for this type of fracture.”
However, it’s not a totally foolproof plan. Using 3D printing in pre-op planning isn’t cheap, and can increase hospitalization costs, and these 3D printed models only display the bone shape – no blood vessels, cartilage, or ligaments. However, when combined with MRI and vascular imaging, this issue could be solved.
“In conclusion, pre-operative simulation using a 3D printing model may be helpful for the treatment of old and complex tibial plateau fractures, which may be conducive to the pre-operative planning and to making the surgical procedure accurate and personalized. However, its clinical effectiveness need to be further assessed by a prospective randomized-controlled study.”
Discuss this and other 3D printing topics at 3DPrintBoard.com or share your thoughts below.
Subscribe to Our Email Newsletter
Stay up-to-date on all the latest news from the 3D printing industry and receive information and offers from third party vendors.
Print Services
Upload your 3D Models and get them printed quickly and efficiently.
You May Also Like
3D Printing News Briefs, July 2, 2025: Copper Alloys, Defense Manufacturing, & More
We’re starting off with metals in today’s 3D Printing News Briefs, as Farsoon has unveiled a large-scale AM solution for copper alloys, and Meltio used its wire-laser metal solution to...
3DPOD 260: John Hart on VulcanForms, MIT, Desktop Metal and More
John Hart is a Professor at MIT; he´s also the director of the Laboratory for Manufacturing and Productivity as well as the director of the Center for Advanced Production Technologies....
3D Printing News Briefs, June 28, 2025: Defense Accelerator, Surgical Models, & More
In this weekend’s 3D Printing News Briefs, 3YOURMIND was selected to join an EU Defense Accelerator, and PTC has announced model-based definition (MBD) capabilities within Onshape. Finally, a study out...
EOS in India: AM’s Rising Star
EOS is doubling down on India. With a growing base of aerospace startups, new government policies, and a massive engineering workforce, India is quickly becoming one of the most important...