Sometimes, when researching tissue engineering, scientists must combine different fabrication methods and materials to build scaffolds that meet multiple requirements at once – mimic native tissue’s mechanical response, have biocompatibility, degrade at a controlled rate to support regeneration of tissue, promote cell attachment, etc.
UK researchers from Loughborough University and the University of Nottingham published a paper, “Multi-layer Scaffolds of Poly(caprolactone), Poly(glycerol sebacate) and Bioactive Glasses Manufactured by Combined 3D Printing and Electrospinning,” about their work combining 3D printing and electrospinning to fabricate “multi-layered polymer/glass scaffolds that possess multi-scale porosity, are mechanically robust, release bioactive compounds, degrade at a controlled rate and are biocompatible.”
“TO date, electrospinning and 3D printing of PCL-PGS blends have been demonstrated separately to obtain scaffolds with controlled properties,” they explained. “Here, we investigate, for the first time, PCL-PGS constructs consisting of electrospun mats deposited onto 3D-printed scaffolds. Bioactive glasses have been incorporated into the 3D printed polymer matrix to achieve better control over mechanical properties, degradation profile and biocompatibility.”
After the researchers synthesized the PGS, they used a 3D-Bioplotter from EnvisionTEC to print three types of scaffolds, using PCL with a molecular weight of ~80,000 Da:
- PCL-PGS (3D PCL-PGS)
- PCL-PGS with 5 wt% bioactive glasses (3D PCL-PGS-5BGs)
- PCL-PGS with 10 wt% bioactive glasses (3D PCL-PGS-10BGs)
The scaffolds consisted of a 3D printed grid coated with a mat of electrospun fibers, and BG microspheres were added to the 3D printed layer to better control mechanical properties and degradation behavior.

Fig. 1: (a) 1H NMR spectrum of PGS in deuterated acetone. The typical chemical structure of PGS is at the top of the graph. (b) FTIR spectrum of PGS. The characteristic peaks are indicated. (c) XRD pattern of the 45S5 BG microspheres, and (inset) morphology analysed by SEM.
Barrels loaded with these solutions were “dispensed through smooth-flow tapered tips (340 µm internal diameter) from 12.7 mm” and extruded. After drying, the 4 × 4 cm2 samples were used as a collector for the electrospinning process in order to build multi-layer constructs.
“The fibres reached the collector (the 3D-printed scaffold) before complete solidification; the trapped solvent continued to diffuse out and determined coalescence at the fibre–fibre junctions and along the fibre length. Therefore, membranes consisting of interconnected fibre layers were created,” the team wrote.
PCL and PGS were mixed at a 1:1 weight ratio and dissolved in a dichloromethane-methanol mixture to create a 14 wt% solution, which “was electrospun only on one surface of the 3D-printed scaffolds” in order to achieve strong adhesion between layers.
“The fusion between adjacent PCL-PGS printed layers, due to solvent traces and low melting temperature of PGS (broad range between −20 and 40 °C) [16], was advantageous to create monolithic constructs with improved mechanical stability,” they explained.
“The BGs were exposed on the surface of the 3D-printed scaffolds but also embedded into the polymer matrix. The exposed BG microspheres and the surface micro-porosity of the scaffolds, caused by solvent evaporation, contributed to the erosion of the systems during degradation…”
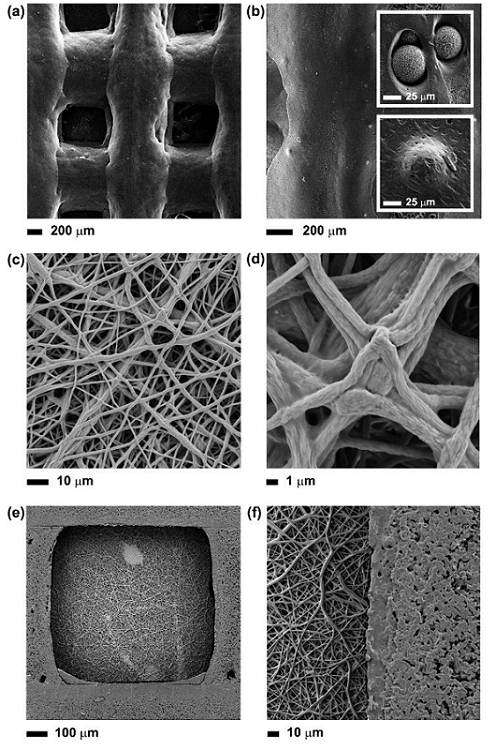
Fig. 2: SEM images at different magnifications of: (a) and (b) the 3D printed scaffolds, and the BG microspheres exposed onto the surface or embedded into the polymer matrix (insets); (c) and (d) surface of the composite scaffold covered with a layer of electrospun PCL-PGS mats, pointing out the fusion between fibers; (e) and (f) surface of composite scaffold without the layer of electrospun fibers.
The researchers recorded the 1H Nuclear Magnetic Resonance (NMR) and infrared spectra of the PGS, and analyzed a sample of the BG microspheres with X-ray diffraction. They also used scanning electron microscopy (SEM) to investigate the morphology of the 3D printed scaffolds, BG microspheres, and electrospun fibers.
After the samples were cut into 20 x 40 mm rectangular strips, the team analyzed the mechanical properties of the scaffolds with uniaxial tensile tests.
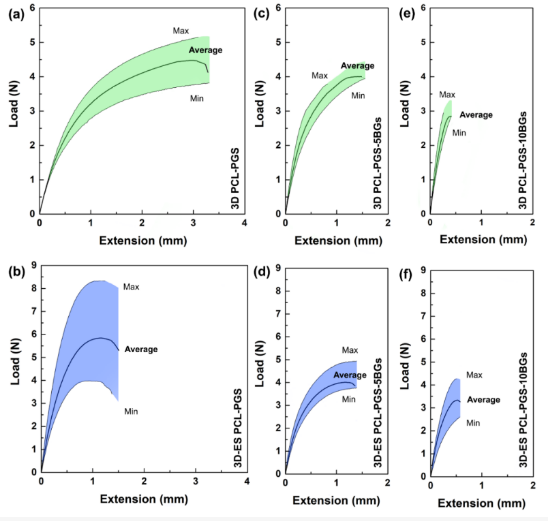
Fig. 3: Load vs. extension curves of: 3D printed PCL-PGS, without (a) and with (b) the electrospun PCL-PGS mat; 3D printed PCL-PGS with 5 wt% of BGs, without (c) and with (d) electrospun PCL-PGS mat; 3D printed PCL-PGS with 10 wt% of BGs, without (e) and with (f) electrospun PCL-PGS mat.
“The average sample thickness was (205 ± 4) µm for the composition 3D-ES PCL-PGS, (240 ± 9) µm for 3D-ES PCL-PGS-5BGs and (280 ± 9) µm for 3D-ES PCL-PGS-10BGs. The rate of extension was set at 10 mm/min. Ten samples for each scaffold composition were analysed and the data are given in the text as average ± standard deviation. The load vs. extension graphs show the average curve within a shaded region, which indicates the values measured for all replicates,” the team explained.
The 3D printed composite grids had an average maximum load of 4.5 N in tension, and a maximum extension of 3.5 mm. The 3D-ES PCL-PGS scaffolds, created by adding the electrospun layer, had a maximum 6.0 N load and extended to 1.5 mm. The patches were reinforced by the electrospun fibers, thanks to the strong adhesion between layers and solid fiber-fiber bonding.
“The incorporation of 5wt% of bioactive glass microspheres in the PCL-PGS matrix gave a significant reduction in the sample extension before failure, with no statistically significant changes in the maximum load (Figure 3c). Similar values of load and extension at the breaking point were recorded after the deposition of the fibrous layer (Figure 3d). By increasing the BGs concentration to 10 wt%, drops in both maximum load and extension were recorded for 3D PCL-PGS–10BGs (Figure 3e) and 3D-ES PCL-PGS–10BGs (Figure 3f),” they wrote.
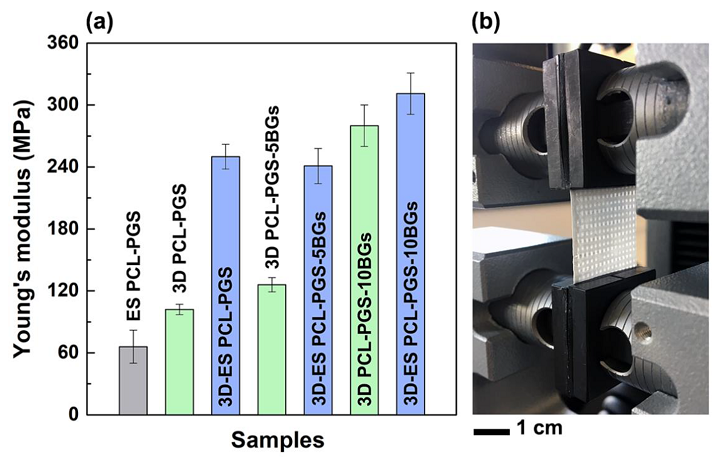
Fig. 4: Values of Young’s modulus for different scaffold types (a). The photograph (b) of one composite scaffold during the tensile test shows the 3D printed grid covered by the electrospun mat.
The ES PCL-PGS mats had a Young’s modulus of (66 ± 16) MPa: higher than in other studies about “electrospun 1:1 PCL:PGS blends.” This is likely due to cross-linking of fusion and PGS between the electrospun layers and the fibers. This rose significantly – from (102 ± 5) MPa to (250 ± 12) MPa – when the fibers were deposited onto the 3D printed PCL-PGS scaffolds; again, this is thanks to the excellent layer adhesion.
“The effect of the electrospun fibres on the mechanical properties of the scaffolds was evident also for samples containing BG microspheres,” the team explained. “3D-printed scaffolds with 5 and 10 wt% of BGs had E values of (126 ± 7) MPa and (280 ± 20) MPa, respectively; the deposition of the electrospun mats determined an increase in Young’s modulus up to (241 ± 17) MPa for 3D-ES PCL-PGS-5BGs and (311 ± 20) MPa for 3D-ES PCL-PGS-10BGs.”
Then, in vitro tests were performed in a PBS solution to evaluate the degradation behavior of the scaffolds. PCL-PGS scaffolds with no BGs were the control, and the researchers recorded changes in water absorption, weight loss, and pH; after one and two months of degradation, they also analyzed the mechanical properties of 2 × 4 cm2 rectangular samples, incubated in PBS at 37 °C. The researchers explained that, by releasing PGS and BGs in vitro, the scaffolds degraded and lost ~14% weight “after 56 days of incubation in a buffer solution.”
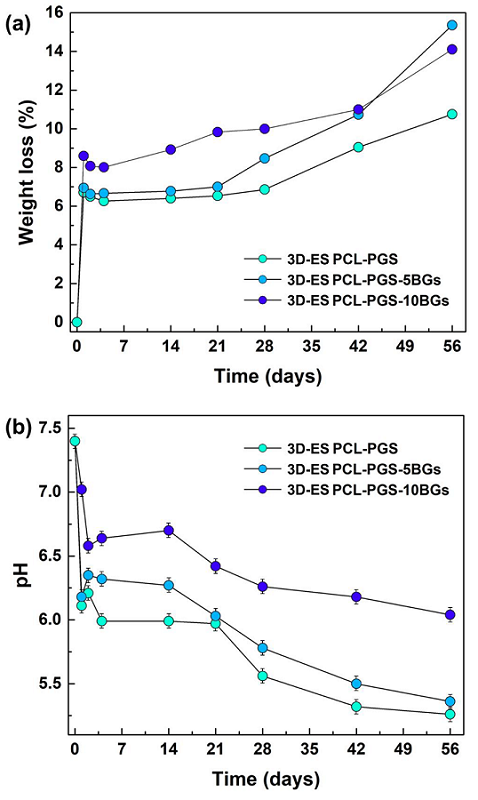
Fig. 5: In vitro degradation of composite scaffolds with and without BG microparticles: (a) percentage of weight loss and (b) pH changes at different timepoints. Data are represented as average ± standard deviation for five repeats (symbol size includes the error bar).
“The degradation was initiated by the hydrolysis of PGS and dissolution of the BGs microparticles,” they wrote.
“The weight loss experienced by scaffolds containing BGs indicates that both PGS and bioactive glass microparticles were released, as was also confirmed by the pH changes in the PBS medium, particularly for samples with 10 wt% BGs. As a consequence, a deterioration in the mechanical properties and morphology of the scaffolds was observed.”
The team detected defects and pores on the surface and in the cross-section of the 3D printed layer, which were caused by the release of PGS and BGs; this is why the scaffolds failed under tension.
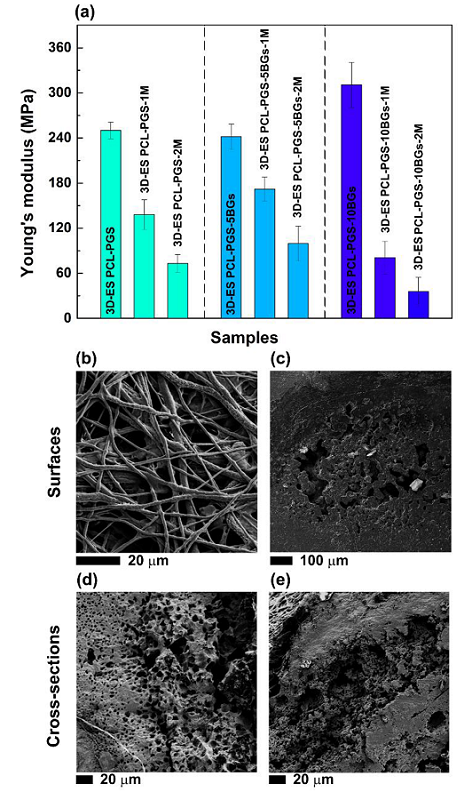
Fig. 6: (a) Values of Young’s modulus of the composite scaffolds after one month and two months of incubation in PBS at 37°C. SEM images, after two months degradation, of the surface (b) of electrospun layer and (c) 3D printed one; (d) and (e) cross-section of the 3D printed layer.
After harvesting mice 3T3 cells by trypsinization, they were passaged every two days at 80–90% culture confluence, and seeded in 96-well flat-bottomed plates. After being sterilized, the team tested three samples for each scaffold type, which were incubated at 37 °C and 5% CO2 after being covered with 2.5 mL of media. 0.2 mL of this media were taken after one, three, and seven days and placed on the cells. After 24 hours of incubation, they measured the cells’ viability and assessed the results with fluorescence measurements. The plate was agitated for five seconds, and measurements that corresponded to the negative control “were considered as 100% cell viability.”
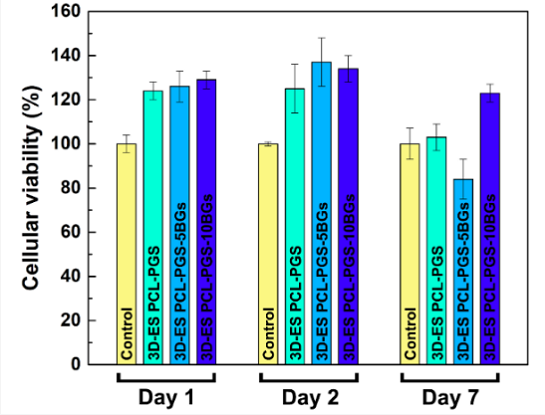
Fig. 7: Percentage of 3T3 cell viability for 3D-ES PCL-PGS scaffolds without and with bioactive glasses for three times points (1, 2 and 7 days).
“All three material compositions exhibited cell viability results above 80% for all timepoints, indicating satisfactory biocompatibility. High survival rates (higher than the control sample) were recorded for all scaffolds: 3D-ES PCL-PGS (124 ± 4%), 3D-ES PCL-PGS-5BGs (126 ± 7%) and 3D-ES PCL-PGS-10BGs (129 ± 4%) at day 1. The highest viability was measured at day 2 with values of 125% ± 11%, 137% ± 11% and 134% ± 6% for 3D-ES PCL-PGS, 3D-ES PCL-PGS-5BGs and 3D-ES PCL-PGS-10BGs, respectively,” they wrote. “A decrease in cell survival was observed for all scaffold types at day 7, particularly for 3D-ES PCL-PGS-5BGs (84% ± 9%). The results of the biocompatibility tests can be linked to the degradation of PGS, the release profile of BGs and corresponding pH changes.”
The viability results show that adding BGs in the 3D constructs had a positive effect, as most the cell survival rates were higher than the 3D-ES PCL-PGS sample with no BGs.
“The compsite scaffolds can find potential applications in tendon and ligament tissue engineering, since they meet the mechanical requirements of native tissues (elastic modulus in the range of 100-300 MPa) 43], in agreement with previous studies [44],” the researchers concluded.
Discuss this and other 3D printing topics at 3DPrintBoard.com or share your thoughts below.
Subscribe to Our Email Newsletter
Stay up-to-date on all the latest news from the 3D printing industry and receive information and offers from third party vendors.
Print Services
Upload your 3D Models and get them printed quickly and efficiently.
You May Also Like
Reinventing Reindustrialization: Why NAVWAR Project Manager Spencer Koroly Invented a Made-in-America 3D Printer
It has become virtually impossible to regularly follow additive manufacturing (AM) industry news and not stumble across the term “defense industrial base” (DIB), a concept encompassing all the many diverse...
Inside The Barnes Global Advisors’ Vision for a Stronger AM Ecosystem
As additive manufacturing (AM) continues to revolutionize the industrial landscape, Pittsburgh-based consultancy The Barnes Global Advisors (TBGA) is helping shape what that future looks like. As the largest independent AM...
Ruggedized: How USMC Innovation Officer Matt Pine Navigates 3D Printing in the Military
Disclaimer: Matt Pine’s views are not the views of the Department of Defense nor the U.S. Marine Corps Throughout this decade thus far, the military’s adoption of additive manufacturing (AM)...
U.S. Congress Calls Out 3D Printing in Proposal for Commercial Reserve Manufacturing Network
Last week, the U.S. House of Representatives’ Appropriations Committee moved the FY 2026 defense bill forward to the House floor. Included in the legislation is a $131 million proposal for...