International researchers have teamed up to improve the results of fused filament fabrication (FFF), releasing their findings in the recently published ‘Optimization of the 3D Printing Parameters for Tensile Properties of Specimens Produced by Fused Filament Fabrication of 17-4PH Stainless Steel.’
During this study, the authors experimented for the best outcome in optimized FFF 3D printing—a method originally created for polymeric materials; however, blends are now available for metal fabrication and the hardware has become much more accessible and affordable. For many applications, achieving suitable mechanical properties is impossible without the use of multicomponent polymeric binder systems.
The researchers used a proprietary binder system and 17-4PH stainless-steel powder for shaping samples based on optimized design. Samples were created on an Original Prusa i3 MK3 FFF 3D printer, using a nozzle with a diameter of 0.4mm.
“Central composite design is a design of first order (2k—where k is a number of adjustable parameters) extended with additional trials in the center of the design (mean values of parameters) and axis for each parameter, in order to be able to estimate parameters with models of second order,” stated the researchers. “Central composite design consists of 2k trials on the peak values of the observed parameters, 2k trials in axes of each parameter, and trials at the center of the design.”
The team continued, performing both tensile testing and scanning electron microscopy.
“In order to set the FFF parameters for the production of specimens with optimal properties, the criteria for optimization have to be determined,” stated the researchers. “Here, complex optimization based on multiple simultaneous criteria was used.”
In varying printing parameters, the researchers noted that the appearances of the samples changed.
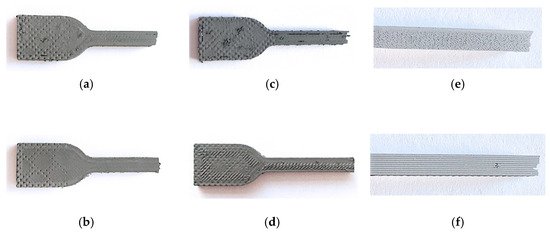
Top and side views of specimens printed at different conditions of the design of experiment (DoE) after tensile testing: (a) trial 7 (temperature 210 °C); (b) trial 5 (temperature 260 °C); (c) trial 10 (flow rate multiplier 95%); (d) trial 13 (flow rate multiplier 127%); (e) trial 2 (layer thickness. 0.12 mm); (f) trial 6 (layer thickness. 0.28 mm).

Morphology of three-dimensional (3D) printed parts investigated by scanning electron microscopy at different magnifications: (a) 39×; (b) 300×; (c) 2300×; (d) 2400×.
“A lower extrusion temperature interfered with material deposition, resulting in more air gaps and reduced minimal cross-section of the specimens and, therefore, lower tensile properties,” concluded the research team. “Extrusion at lower temperatures also negatively affected the bond between two different layers, which led to lower tensile properties. In this research, only the polymer components (45% vol.) were melted during FFF process; therefore, the effect of extrusion temperature on tensile properties was not as strong as in the case of FFF of pure polymer materials.
“The results of this analysis can be used in future research for comparison with properties of final parts obtained after green parts undergo debinding and sintering. This comparison will show if the same trend between tensile properties obtained after FFF and after sintering are present, and if the level of the effect of tensile properties obtained after the FFF process holds after the specimens are sintered.”
As 3D printing continues to impact nearly every industry today, researchers conduct a wide range of research with stainless steel, to include creating better grades of material, testing the effects of various gases, and testing different hardware.
What do you think of this news? Let us know your thoughts! Join the discussion of this and other 3D printing topics at 3DPrintBoard.com.
[Source / Images: ‘Optimization of the 3D Printing Parameters for Tensile Properties of Specimens Produced by Fused Filament Fabrication of 17-4PH Stainless Steel’]Subscribe to Our Email Newsletter
Stay up-to-date on all the latest news from the 3D printing industry and receive information and offers from third party vendors.
Print Services
Upload your 3D Models and get them printed quickly and efficiently.
You May Also Like
Reinventing Reindustrialization: Why NAVWAR Project Manager Spencer Koroly Invented a Made-in-America 3D Printer
It has become virtually impossible to regularly follow additive manufacturing (AM) industry news and not stumble across the term “defense industrial base” (DIB), a concept encompassing all the many diverse...
Inside The Barnes Global Advisors’ Vision for a Stronger AM Ecosystem
As additive manufacturing (AM) continues to revolutionize the industrial landscape, Pittsburgh-based consultancy The Barnes Global Advisors (TBGA) is helping shape what that future looks like. As the largest independent AM...
Ruggedized: How USMC Innovation Officer Matt Pine Navigates 3D Printing in the Military
Disclaimer: Matt Pine’s views are not the views of the Department of Defense nor the U.S. Marine Corps Throughout this decade thus far, the military’s adoption of additive manufacturing (AM)...
U.S. Congress Calls Out 3D Printing in Proposal for Commercial Reserve Manufacturing Network
Last week, the U.S. House of Representatives’ Appropriations Committee moved the FY 2026 defense bill forward to the House floor. Included in the legislation is a $131 million proposal for...