In our last installment, we began relaying comments from the maker community, including prominent RepRappers and Adafruit, about the status of the maker movement. In this article, we’ll continue the trend with comments from other leading makers.
A RepRapper of a different sort is Joshua Pearce, a professor at Michigan Technological University and the head of the school’s Open Sustainability Technology lab. Pearce believes that commercial ventures related to the maker goods should be distinguished from the movement itself. The former has the tricky task of trying to commercialize free ideas, which can turn off some people. The latter, however, continues to grow uninterrupted. As Pearce puts it:
[Y]ou walk down the hallway of any dorm at Michigan Tech and you will see RepRap after RepRap busily printing away. Many are Creality variants or one of our MOST deltas, but there are a lot of beautifully hacked RepRap derivatives. Our library, makerspace and the mechanical engineering department are full of Lulzbots. This doesn’t include the 50+ RepRaps in my lab or the Open Source Hardware Enterprise that can print everything from high temperature engineering polymers to metals and ceramics.Every high school in our region sports several RepRaps except for one, whose new superintendent just wrote this week to talk to me “as we consider adding electives in the areas of 3D printing and open source hardware/software.” My open source 3D printing class is always over-subscribed even this semester when I bumped it up to 100 seats (putting 100 more RepRaps into the distributed manufacturing ecosystem) along with more than 1000 open source 3D printable designs of varying value from toys to scientific tools and jigs worth thousands of dollars each.
Other indicators of the movement’s vitality include the increase of open source 3D printable designs, the reduction in price of RepRaps, low-cost Chinese manufacturers working to obtain OSHWA certification, the growing size of the Midwest RepRap festival, and the success of the open access journal that Pearce co-edits, HardwareX. The publication is currently ranked fourth in the instrumentation category and its format for publishing open hardware is being replicated by mainstream scientific journals.
“Open hardware in the sciences has moved in the past 6 years from a niche to the mainstream in academia!” Pearce says.
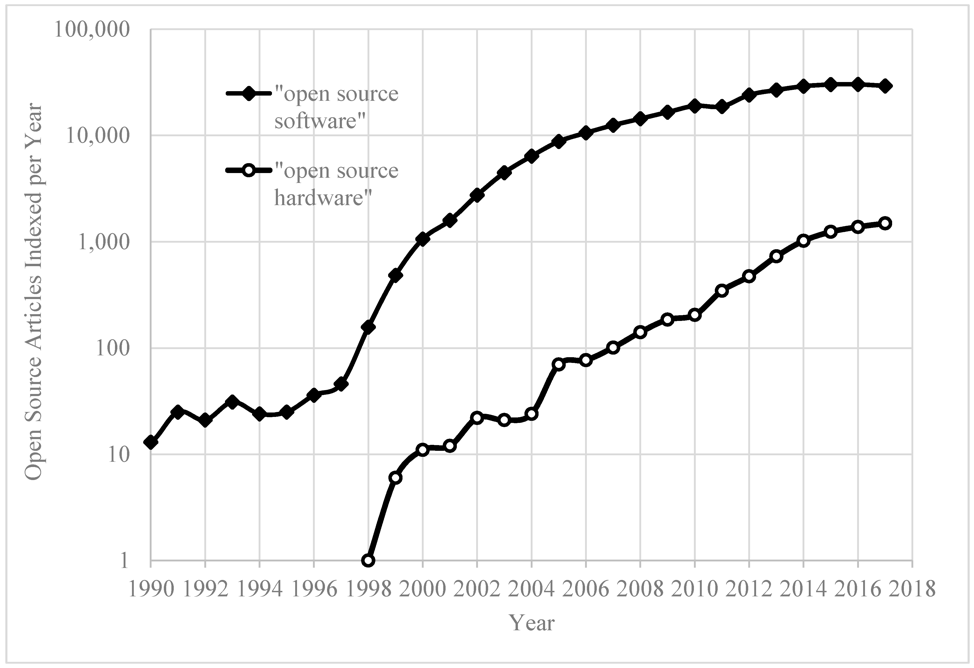
A figure published in an Inventions article about setting up “Sponsored Libre Research Agreements to Create Free and Open Source Software and Hardware”, provided by Professor Pearce. He indicates that “the interest in academia for open hardware is growing exponentially – roughly following the rise of free and open source software with a 20-year delay.” Image courtesy of Inventions.
Both Pearce and Gael Langevin, the original inventor of the 3D printable InMoov robot, believe that the current political and economic climate may negatively impact the progress of open hardware. Pearce underscores the fact that the recent trade war with China made it “hard to run a RepRap-related business” do the high tariffs required to ship components.
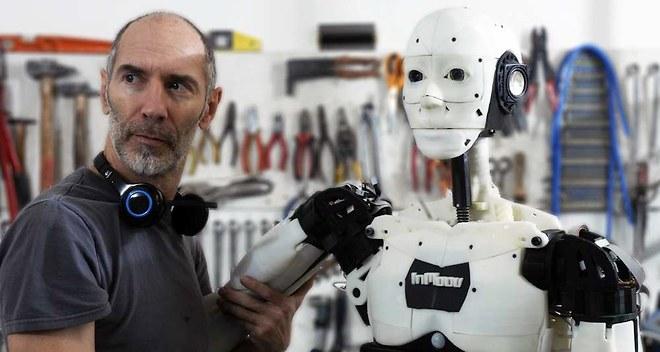
Gael Langevin with InMoov. Thanks to the open source nature of the InMoov project, the 3D printable robot has been replicated numerous times.
Langevin attributes some slowing down of the movement to the fact that, while the previous U.S. presidential administration put a spotlight DIY/hacking culture, such an open attitude does not seem to be present any longer from a national standpoint. As for the commercialization of open source hardware, the French designer argues:
“Makerfaire propose every year some new Makers with new projects, but in order to get a wider public every year, those projects need to be even more amazing and new. They have reached a level of projects that were really amazing, but it is hard to keep growing up every year. Makerfaire is based on ‘permanent’ exponential ability which is one of the fundamental problem of our current economy/society. Until how big can we grow?”
Nevertheless, Pearce’s lab continues its amazing work on open source hardware, including the 3D printing of recycled polycarbonate waste and the operation of open source industrial equipment at green FabLabs. This year, some of his PhD students will be publishing work related to “very high-end scientific and medical tools along with a level of automation that does not yet exist in industry.” The journal Additive Manufacturing will be including an article from his team on how to use a RepRap to make custom ceramic printed objects with hollow cores measuring less than 100 microns.
We also spoke to Carl Bass, who was once closely associated with the maker movement for much of the work he was doing at Autodesk. Bass’s advocacy for the movement was translated into actions by the company, which acquired the online DIY site, Instructables, as well as the development of an open source 3D printer. According to Bass, these endeavors were about connecting the design software that Autodesk makes and the reality of making. Bass recalled:
We have a beautiful rendering of it on the screen, but our challenge and our business opportunity is how to, how did we make this thing? We used to talk about how these objects existed on the other side of the screen. And the idea was to reach beyond the screen and bring them into the physical world and to enable customers to do that as quickly as possible.
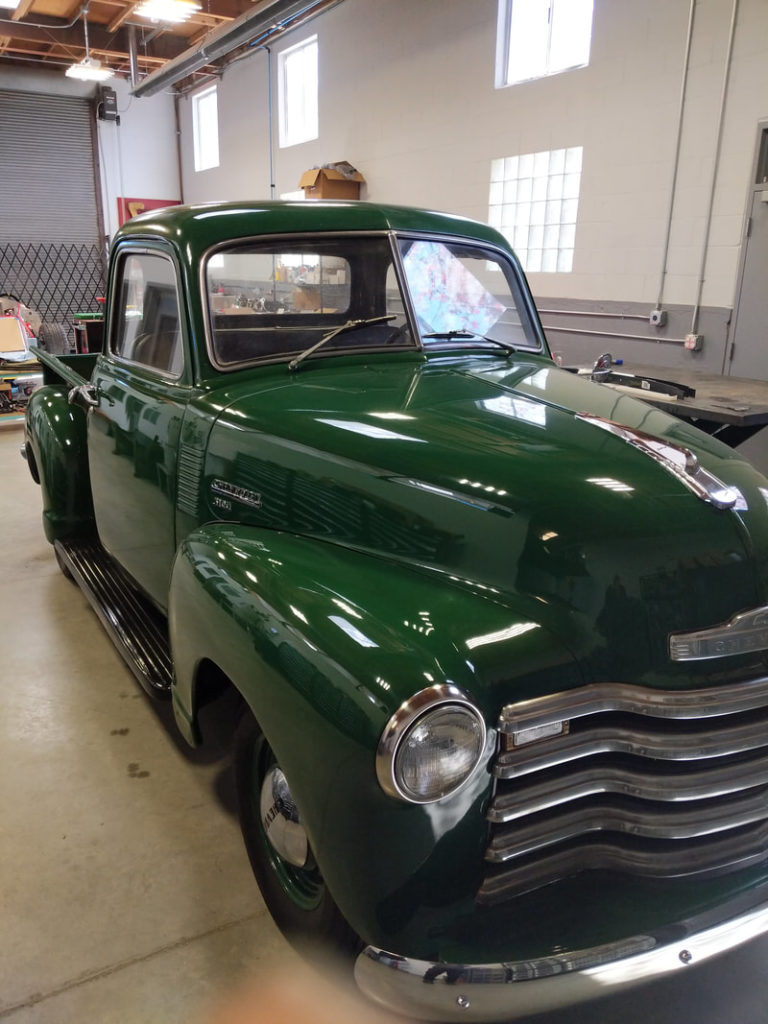
A 1950 Chevy pickup that Carl Bass is retrofitting with an electric motor. Image courtesy of Carl Bass.
Bass argued that the press has a limited attention span, in which it focuses on a particular topic before moving on, an idea that he was not critical of. At the same time, the media’s definition of “making” was a narrow one:
I think [the maker movement has] definitely lost the hype, but I think that’s a good thing. We saw this with Instructables. Half the stuff on there was cooking and sewing. It wasn’t all Arduinos. We were trying to embrace users who were actually making. It didn’t really have to be just playing with Arduinos. We thought that was a particularly limiting definition. And, in some ways, I think the maker movement as covered by the press got it wrong. They were really fascinated by two things, you know, small, cheap electronics like Arduinos and 3D printing for personal use. I thought at the time and certainly with the benefit of hindsight, you realize how narrow that definition of making was.
The media may have lost interest in the maker movement as a concept, according to Bass, but the idea of learning by doing has become popular in the education system and even in corporate settings.
Bass has since left Autodesk, amid the software industry’s shift to the cloud and subscription pricing. In his retirement, he is advising some small startups while also relaxing and spending time in his shop. He also continues to embrace the concept of making. Most recently, he has been working on converting a 1950 Chevy Pickup into an electric vehicle
What this series seems to have demonstrated is that people on the ground and the world of business, marketing and media are two distinct things. Businesses come and go, with some attempting to merge the idea of sharing and open source hardware with an economic system that is inherently one of competition and private property. As Langevin argued, however, endless economic growth may be an outdated mode of living and one that is not consistent with the limits of our ecosystem.
In the final installment of this series, we will be speaking with Dale Dougherty, CEO of Maker Media, about the transformation of the company to Make: Community.
Join the discussion of this and other 3D printing topics at 3DPrintBoard.com.
Subscribe to Our Email Newsletter
Stay up-to-date on all the latest news from the 3D printing industry and receive information and offers from third party vendors.
Print Services
Upload your 3D Models and get them printed quickly and efficiently.
You May Also Like
The Dental Additive Manufacturing Market Could Nearly Double by 2033, According to AM Research
According to an AM Research report from 2024, the medical device industry, specifically in dentistry, prosthetics, and audiology, is expected to see significant growth as these segments continue to benefit from...
Heating Up: 3D Systems’ Scott Green Discusses 3D Printing’s Potential in the Data Center Industry
The relentless rise of NVIDIA, the steadily increasing pledges of major private and public investments in national infrastructure projects around the world, and the general cultural obsession with AI have...
AM Research Webinar Explores Continuum’s Sustainable Metal Additive Manufacturing Powders
Metal additive manufacturing (AM) powder supplier Continuum Powders is working to develop solutions that empower industries to reduce waste and optimize their resources. An independent life cycle assessment (LCA) of...
3D Printed Footwear Startup Koobz Lands $7.2M in Seed Round
California-based Koobz is focused on reshoring the U.S. footwear supply chain with advanced manufacturing processes, including 3D printing. The startup just announced that it has added $6 million to its...