In the recently published ‘Determining the tribological properties of different 3D printing filaments,’ Romanian researchers examine 3D printing filaments in-depth, with a focus on pinpointing suitable materials for fabricating parts that come into contact with one another. In this research, they study friction coefficients as materials are in contact with a metallic disc.
While ‘vast research’ has been performed in the area of friction coefficients and wear of 3D printing materials, here the researchers center their study around Zortrax filaments, analyzing eight polymers, with each printed on a Zortrax M200 Desktop 3D Printer. Ultimately, the team will choose a material for fabrication of a new shoe sole.
“Mass printing custom fit 3D soles is considered one of the future directions in athletic shoe manufacturing and Adidas in collaboration with Carbon have already started research and production in this area,” explain the researchers.
The following filaments were used:
- Z-ABS – optimal for beginners
- Z-GLASS – a translucent material
- Z-HIPS – meant for larger parts
- Z-PCABS – offers strength and durability
- Z-PETG – resistant to acids, solvents, alkalis, and salt
- Z-ESD – provides electrostatic protection
- Z-PLA PRO – reduces shrinkage to obtain fine details
- Z-ASA PRO – resistant to UV, humidity, heat, and is good for the outdoors
(Note from the researchers: the Z-ULTRAT sample filament broke before printing was completed, so this material was excluded from the study.)
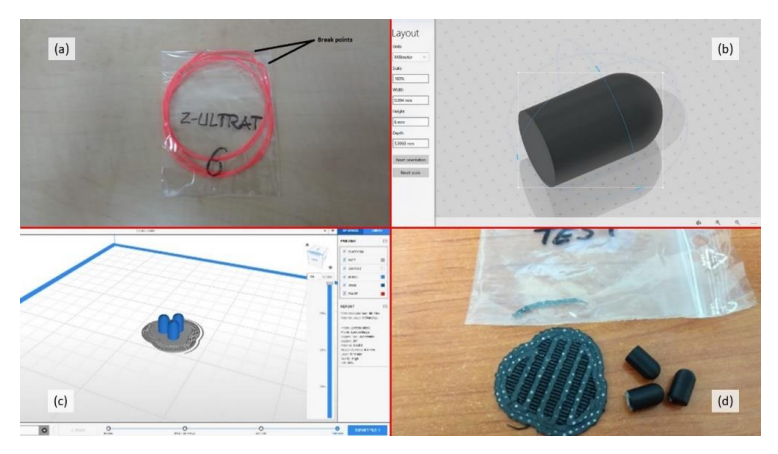
(a) Example of Z-ULTRAT filament (b) Pin modeled in SolidWorks and opened with Windows Print 3D (sideways orientation where width is actually the height) (c) Pre-production of 3D pins in Zortrax Z-Suite (d) Example of 3D printed test pins.
The pin-on-disc method was used in testing, as the researchers placed three pins in sockets on a disc, located 100mm from the center. This was rotated at 350rpm, and the disc was cleaned after each test due to continued residue.
“The first load was the disc itself that accounted for a loading force of 10.17 N. After that, a first weight was added, and the total load force was 11.72 N. The second weight was added after that to increase the load force to 14.91 N, then the third to increase the load force to 17.13 N, and finally the fourth for a total load force of 18.55 N,” explained the researchers.

(a) Rotating Disc and force sensor (b) Pin Slots (c) Weights and sensor pusher (d) Full test assembly – 3 pins on disk tribometer.
The same testing mechanism was used in analyzing wear behavior, as the metal disc rotated with the pins on it—at maximum force load of 18.55 N for 5 minutes, then 10 minutes, 15 minutes, and 20 minutes.
Sample 9 (Z-ASA PRO) proved to offer the highest wear percentage, while sample 7 (Z-ESD) demonstrated the lowest wear percentage. Sample 3 (Z-HIPS) offered the highest friction coefficient, ‘followed closely’ by sample 9 (Z-ASA PRO). Sample 5 (Z-PETG) demonstrated the lowest friction coefficient.
“In conclusion, if the interest is to develop soles with low wear behavior and high friction, one recommendation is to use the Z-GLASS material, if the mechanical behavior corresponds with the product requirements. If one needs a balance between friction and wear (like in the day-to-day shoes), then materials corresponding to the sample 1 (Z-ABS) and 8 (Z-PLA PRO) are recommended.
“For soles requiring low friction (for example sportive dancing) material nr 5 (Z-PETG) is recommended. If the wear is not considered a pressing issue, for good friction, material number 3 (Z-HIPS) is recommended,” concluded the researchers.
This study brings together two areas that are receiving substantial attention right now in the study of materials and their properties, as well as 3D printing and additive manufacturing processes in the production of shoes as companies like Adidas have announced a 4D running shoe, Nike has produced footwear with a 3D printed upper sole, and New Balance is getting in on the 3D printed footwear market too.
What do you think of this news? Let us know your thoughts! Join the discussion of this and other 3D printing topics at 3DPrintBoard.com.
[Source / Images: ‘Determining the tribological properties of different 3D printing filaments’]
Subscribe to Our Email Newsletter
Stay up-to-date on all the latest news from the 3D printing industry and receive information and offers from third party vendors.
Print Services
Upload your 3D Models and get them printed quickly and efficiently.
You May Also Like
Reinventing Reindustrialization: Why NAVWAR Project Manager Spencer Koroly Invented a Made-in-America 3D Printer
It has become virtually impossible to regularly follow additive manufacturing (AM) industry news and not stumble across the term “defense industrial base” (DIB), a concept encompassing all the many diverse...
Inside The Barnes Global Advisors’ Vision for a Stronger AM Ecosystem
As additive manufacturing (AM) continues to revolutionize the industrial landscape, Pittsburgh-based consultancy The Barnes Global Advisors (TBGA) is helping shape what that future looks like. As the largest independent AM...
Ruggedized: How USMC Innovation Officer Matt Pine Navigates 3D Printing in the Military
Disclaimer: Matt Pine’s views are not the views of the Department of Defense nor the U.S. Marine Corps Throughout this decade thus far, the military’s adoption of additive manufacturing (AM)...
U.S. Congress Calls Out 3D Printing in Proposal for Commercial Reserve Manufacturing Network
Last week, the U.S. House of Representatives’ Appropriations Committee moved the FY 2026 defense bill forward to the House floor. Included in the legislation is a $131 million proposal for...