Researchers from Seoul, Korea have tried to refine spine surgery instruments via 3D printing, outlining their work in the recently published ‘3D Printer Application for Endoscope-Assisted Spine Surgery Instrument Development: From Prototype Instruments to Patient-Specific 3D Models.’
Exploring the realm of developing surgical instruments with innovative technology, the researchers used their study to reach beyond previous ‘limited’ attempts, producing both a prototype for an instrument as well as a functional 3D printed model. Realizing the benefits of 3D printing in terms of flexibility in production, affordability, and the ability to create models and devices that are patient-specific, the scientists designed a new system that can be used with one surgical instrument for endoscopic surgeries.
Four steps were required to create a new instrument:
- Developing a concept
- Designing a prototype based on the new concept and accompanying ideas
- 3D printing a patient-specific spine model
- Assessing the accuracy and efficacy of new surgical instruments

Workflow diagram of the development and evaluation of new surgical instruments. The solid arrow indicates the conventional application, and the dotted arrow indicates the application of endoscope-assisted spine surgery.
“3D printing technique was primarily applied in two parts: making the prototype instrument and the patient-specific model to test the new instrument,” stated the scientists in their research paper.
The researchers created a system with combined cannula, featuring one cannula for the endoscope and the other for surgical instruments, with major and minor axis diameters of 10.34 mm and 9.16 mm, respectively.

New endoscope-assisted spine surgery system. (A) Two tubes were joined together: one for an endoscope and the other for an instrument working cannula. The instrument working cannula could be blocked with a rubber cap to maintain proper saline pressure. (B) 3D-printed prototypes of the new endoscope-assisted spine surgery system. A 10-mm incision was needed for patient model application. (C) Photograph of a surgical test using the new endoscope-assisted spine surgery system. An endoscopic drill was inserted at the working cannula. (D) Operation field with the new system. Similar operational views with conventional endoscopic spine surgery. The arrow head is the ligamentum flavum at the inter-laminar space, and the arrows indicate the lamina of the superior and inferior vertebral body.
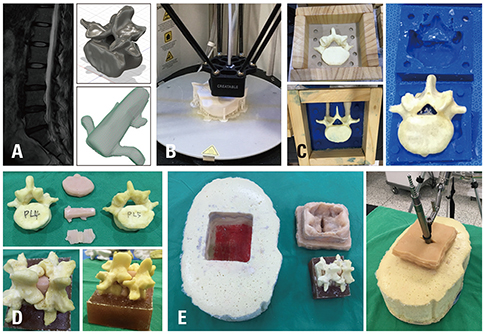
Patient-based model created with the 3D printing technique. (A) 3D modeling of spine components using patient MRI data. (B) Printing spine components using a 3D printer. (C) Making silicone molds for patient-based 3D-printed spine components. (D) Making spinal components considering physical properties (vertebra, discs, nerves, ligaments) using patient-based spine component molds. (E) Making a patient model after assembling the body frame, spine components, and skin with soft tissue.
To create the spine model, the researchers:
- Used 2D data from MRI and CT scans to create a 3D design
- 3D printed spine components
- Fabricated silicone molds with the 3D printed spine components
- Made spine components with required properties
- Assembled the patient-specific model
Imaging data was imported to slicing software, with models then 3D printed on a Creatable D3. The first group of samples consisted of parts that required exact replication:
- Bone
- Tissue
- Discs
- Nerves
- Ligaments
The team used a variety of silicones and polymers, and foam, for the fabrication of the spinal parts, including two sets of patient-specific spine models for lumbar 4–5 paramedian disc herniation and lumbar 4–5 foraminal disc herniation on the left.
The results were assessed as the researchers compared instruments and methods. The new system created in this study was compared with a 16mm tubular retractor. Two different approaches were used, both paramedian and foraminal discectomy, with results compared after the procedure.
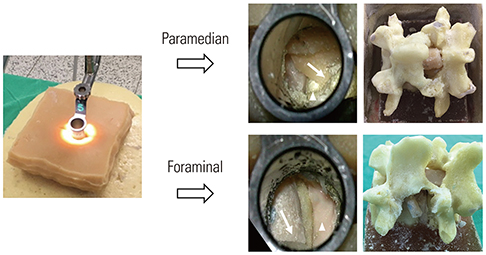
Discectomy with a tubular retractor. A paramedian approach is shown above, and a foraminal approach is shown below. The arrows indicate the nerve root, and arrowheads show the discs.
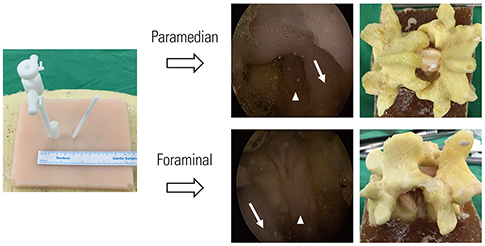
Discectomy with the new endoscope-assisted spine surgery system. A paramedian approach is shown above, and a foraminal approach is shown below. The arrows indicate the nerve root, and arrowheads show the discs. Less bone destruction was observed with the new system, compared to the conventional tubular retractor in the foraminal approach.
“Our new endoscope-assisted spine surgery system and trial with a 3D-printed patient-specific model involved many limitations. Postoperative outcome analysis using a 3D-printed model could be different from using actual patients. Also, the surgical trial was conducted only once, and it was not compared to conventional endoscopic spine surgery. Since we could not confirm whether the magnetic connector would be adequately bonded when it is inside a real human, a cadaver trial is needed to confirm this matter. However, the purpose of this study was to show the usefulness of 3D printers for the development of complex surgical instruments,” concluded the researchers.
“The authors are well-aware that the new endoscope-assisted spine surgery system needs further improvements, and future studies with more complicated degenerative spinal diseases and deformed patient-specific models are required. Nevertheless, we were able to make and test a new idea on surgical instruments quickly, in addition to introducing the possibility of a new endoscope-assisted spine surgery system using 3D printing technology.”
3D printing continues to be helpful to researchers, medical scientists, and both patients and surgeons as the realm of 3D printing models, devices, and surgical guides is refined further for diagnosing, treating, training, and operating. What do you think of this news? Let us know your thoughts; join the discussion of this and other 3D printing topics at 3DPrintBoard.com.
[Source / Images: ‘3D Printer Application for Endoscope-Assisted Spine Surgery Instrument Development: From Prototype Instruments to Patient-Specific 3D Models’]Subscribe to Our Email Newsletter
Stay up-to-date on all the latest news from the 3D printing industry and receive information and offers from third party vendors.
Print Services
Upload your 3D Models and get them printed quickly and efficiently.
You May Also Like
Reinventing Reindustrialization: Why NAVWAR Project Manager Spencer Koroly Invented a Made-in-America 3D Printer
It has become virtually impossible to regularly follow additive manufacturing (AM) industry news and not stumble across the term “defense industrial base” (DIB), a concept encompassing all the many diverse...
Inside The Barnes Global Advisors’ Vision for a Stronger AM Ecosystem
As additive manufacturing (AM) continues to revolutionize the industrial landscape, Pittsburgh-based consultancy The Barnes Global Advisors (TBGA) is helping shape what that future looks like. As the largest independent AM...
Ruggedized: How USMC Innovation Officer Matt Pine Navigates 3D Printing in the Military
Disclaimer: Matt Pine’s views are not the views of the Department of Defense nor the U.S. Marine Corps Throughout this decade thus far, the military’s adoption of additive manufacturing (AM)...
U.S. Congress Calls Out 3D Printing in Proposal for Commercial Reserve Manufacturing Network
Last week, the U.S. House of Representatives’ Appropriations Committee moved the FY 2026 defense bill forward to the House floor. Included in the legislation is a $131 million proposal for...