In the recently published ‘Bi-Layered Polymer Carriers with Surface Modification by Electrospinning for Potential Wound Care Applications,’ researchers from both Finland and Estonia are exploring electrospinning techniques in polymeric wound-care.
For this study, the researchers used a technique combining bi-layered carriers from a blend of polyvinyl alcohol (PVA) and sodium alginate (SA). These carriers were prepared through solvent casting and then either electrospinning or 3D printing. Further, they were characterized and tested regarding the safety and behavior of cells, along with physical and adhesive properties.
As they are ultimately meant to heal, wound dressings are also supposed to prevent infection through bacteria. Today, carriers are created via both artificial and natural polymers, and are meant to provide the following:
- Long-term functionality
- A moist healing environment
- Tissue regeneration
- Prevention of additional damage
- Minimal inconvenience to the patient
“Mechanical and adhesive properties of wound dressings determine their producibility and durability upon storage and usage,” stated the researchers. “In addition, bioactive wound dressings with biologically active ingredients and/or active pharmaceutical ingredients (APIs), such as antibiotics, anti-inflammatory agents, vitamins and growth factors, are continuously being developed.”
Here, wound dressings were created through 3D printing, electrospinning, and solvent casting—a method offering ‘structurally more robust’ films. Electrospinning is environmentally friendly and becoming increasingly popular among researchers. 3D printing, especially with bioprinting, is used for:
- Tissue engineering
- Customization of medical devices
- Drug delivery systems
“The aim of this study was to investigate a combinational technique for the fabrication of bi-layered carriers for the API delivery,” stated the researchers. “The designed systems with modified surface layers were based on a polymer blend of PVA and SA. An electrospun layer was added onto the surface of solvent cast films of the same composition. The physicochemical, mechanical, adhesive properties of the carriers were characterized and compared with similar bi-layered carriers with 3D printed macroporous surface layer.”
Solvent cast (SC) films were cast from Solution A onto transparent copier film or aluminum foil with a film applicator, while nanofiber (NF) mats were prepared from Solution A using the eS-robot© electrospinning machine. 3D printing was performed on the semi-solid extrusion type Biobots 1 3D printer. To test sustainability of cells on bi-layered crosslinked carriers and crosslinked SC film, the MTS cell proliferation assay was used, with 24-well plates using cell crown inserts.
Electrospinning was slow, with a low degree of merging fibers. The researchers reported ‘no visible changes’ in the fibers after crosslinking either.
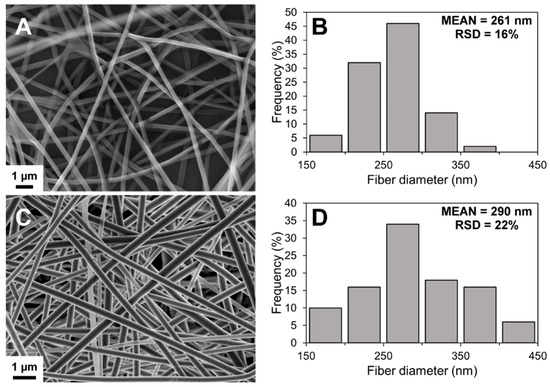
Scanning electron microscopy (SEM) image (A) and fiber diameter histogram (B) of non-crosslinked solvent cast/nanofiber (SC/NF) carriers, and SEM image (C) and fiber diameter histogram (D) of crosslinked SC/NF carriers with mean and relative standard deviation (RSD) values (n = 50).
3D printed mats were extruded onto a plastic liner with a honeycomb infill pattern, ‘clearly visible’ after fabrications.
“The 3D printed mats contained a patterned matrix with lemon-shaped pores with dimensions of approximately 990 × 1620 µm (n = 8),” stated the researchers.
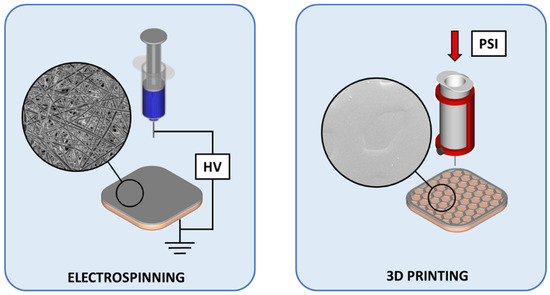
Preparation schematics of the designed bi-layered carriers for wound care. Key: HV—high voltage; 3D—three dimensional; PSI—pressure in pound per square inch.
With use of the bi-layered carrier devices, the research team was able to adjust the following:
- Physical properties
- Bioadhesion properties
- Call-carrier interactions
“The inkjet printing trial demonstrated a uniform liquid absorption profile in the bi-layered carriers with electrospun nanofibers. Furthermore, the surface modification provides a platform for the fabrication of advanced drug delivery systems with active substances (e.g., pharmaceutical and/or bioactive substances) for enhanced wound healing or drug delivery through various administration routes,” concluded the researchers.
“Further investigation aims at developing multilayered wound dressings with bioactive substances and in more biorelevant conditions. The relationship between the properties of the carriers and the composition of the nanofibrous layer will be evaluated and the physical properties and stability of advanced drug delivery systems will be studied. In addition, biodegradability and specific bioactivity behavior testing will be carried out to assess the applicability of bi-layered carriers with drug substances for clinical use.”
Electrospinning continues to grow in popularity from creation of biomimetic scaffolds to guided bone regeneration, and more. What do you think of this news? Let us know your thoughts; join the discussion of this and other 3D printing topics at 3DPrintBoard.com.
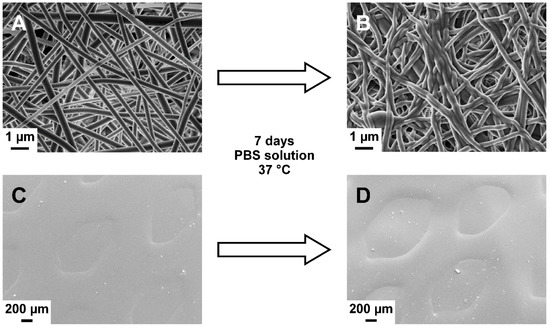
Scanning electron microscopy (SEM) images of crosslinked solvent cast/nanofiber (SC/NF) (A,B) and solvent cast/3D printed (SC/3D) (C,D) carriers before (A,C) and after (B,D) immersion in phosphate-buffered saline (PBS) solution at 37 °C for 7 days.
Subscribe to Our Email Newsletter
Stay up-to-date on all the latest news from the 3D printing industry and receive information and offers from third party vendors.
Print Services
Upload your 3D Models and get them printed quickly and efficiently.
You May Also Like
Nikon SLM Solutions Sells SLM 500 to Primary Weapon Systems to Expand Suppressor Production
Primary Weapons Systems (PWS) is a Boise, Idaho-based manufacturer of suppressors, firearms, and related components. A subsidiary of Vigilant Gear and a sister company to aftermarket Glock slide manufacturer Lone...
3DPOD 261: Tooling and Cooling for AM with Jason Murphy, NXC MFG
Jason Murphy´s NXC MFG (Next Chapter Manufacturing) is not a generalist service; instead, the company specializes in making tooling. Using LPBF and binder jet, the company produces some of the...
HP and Firestorm Labs Form Partnership to Use Multi Jet Fusion 3D Printers in Deployable Factories
HP Inc., maker of a range of additive manufacturing (AM) solutions including the Multi Jet Fusion (MJF) ecosystem, has announced a partnership with Firestorm Labs, a developer of containerized, deployable...
3D Printing News Briefs, July 2, 2025: Copper Alloys, Defense Manufacturing, & More
We’re starting off with metals in today’s 3D Printing News Briefs, as Farsoon has unveiled a large-scale AM solution for copper alloys, and Meltio used its wire-laser metal solution to...