In ‘Three-dimensional printed electrospun fiber-based scaffold for cartilage regeneration,’ Chinese researchers attempt to improve on processes for creating better materials and customized geometries in bioprinting. Here, they not only employ 3D printing but also freeze-drying processes to create ink made from electrospun fibers.
Much of the challenge in bioprinting is in keeping cells alive—and in most cases, such cells require a structure to offer the stability for survival, whether in the body or artificially in the lab. For scientists involved in tissue engineering, the key is to imitate the extracellular matrix (ECM) as closely as possible. Recent trends involve the use of fibrous networks to create scaffolds, with electrospinning proving to offer a successful mode of fabrication.

Schematic of various electrospun fiber scaffolds. (a) Traditional fiber scaffold-electrospun fiber membrane. (b) 3D fibrous scaffold constructed by dispersed electrospun fibers via freeze-shaping. (c) The synthetic steps of 3D-printed fiber-based scaffold.
Challenges occur though as fibers created through electrospinning processes often result in 2D membranes with insufficient pore size and inferior thickness, as compared to ‘bulk scaffolds.’ These obstacles have not deterred researchers in bioprinting, but as with the authors of this study, have garnered attention for further exploration.
Past research has included a variety of different techniques, such as multi-layering, liquid-assisted collection, and template-assisted collection. Still, they have not found success in 3D printing complex scaffolds with good poor size. The authors examined theory further, however, while also outlining how to meet previous challenges with short, single fiber structures, more efficient bonding and extrusion techniques, and improvement of mechanical properties. They then experimented with the following:
- Electrospinning, dehydrating, homogenizing, and evaporation drying to transform the fibers into a short single fiber powder
- Mixing of fiber powder, hyaluronic acid (HA) solution, and polyethylene oxide (PEO) solution to create a 3D printing ink
- Freeze-drying and cross-linking
Afterward, the team evaluated mechanical properties, pore size, and morphology, along with examining a cartilage regeneration model both in vitro and in vivo. Ultimately, the researchers did find their techniques to be successful, resulting in accuracy, large pores, and good mechanical properties. The study also showed that they were able to create the following:
- Suitable ECM biomimetic surface
- Elasticity
- Water-induced shape memory
- Good cartilage regeneration in vivo
Dry evaporation techniques led to greater success here for the researchers, in comparison to previous studies, along with the addition of HA and PEO aqueous solutions after crosslinking. In their research samples, the 3DP offered better mechanical strength in comparison to both their fiber gel scaffold and non-fiber gel/PLGA scaffold.
“Moreover, it was further confirmed that the 3D printed scaffold based on non-fibers exhibited a poor mechanical strength, which is not appropriate for tissue regeneration. However, printed scaffold based on composite fiber inks exhibited good mechanical properties. In general, composite inks (natural and synthetic polymers) are printed using different principles and methods, i.e., natural polymers are printed mainly based on gel or inks, whereas synthetic polymers are printed mainly by fused deposition modeling. Therefore, the printing of composite scaffolds based on natural and synthetic polymers typically requires multiple nozzles with the accurate alignment of each nozzle during processing,” explained the researchers.

Electrospun fibers, dispersed fibers, and 3D-printed scaffold. SEM image of (a) electrospun gelatin/PLGA fibers and (b) dispersed fibers. (c) Average lengths of different dispersed fibers obtained from treatment fiber membranes at different temperatures (25 °C, 160 °C, and 180 °C) (*p < 0.05, n = 3). (d) Image of dispersed fiber powders. (e) Image showing inks composed of fibers (treated at 180 °C), HA solution, and PEO solution, which could be squeezed out from the needle. (f) 3D-printed cuboid scaffolds.
They pressed on to overcome limitations in creating strong, viable structures, adding gelatin and PLGA into the fibers—creating a mechanically homogeneous composite scaffold produced in a room-temperature, one-nozzle, one-step process.
“In the 3DP group, regenerated cartilage (like concrete) and scaffold strands (like steel bar) were uniformly integrated throughout the sample; therefore, the regenerated cartilage efficiently enhanced the mechanical strength of the sample and maintained the original shape,” concluded the researchers regarding the 3DP group.
“Due to the composited fiber-based inks, the 3DP exhibited a good elasticity in wet state, which was significantly superior to that of 3D-printed scaffold fabricated using non-fiber powders. Most importantly, the novel scaffold combined with chondrocytes achieved satisfactory cartilage regeneration and shape maintenance in vivo. This study provides a research model for the design and fabrication of multiple biomimetic scaffolds.”
Bioprinting and the use of scaffolds and a variety of different structures is one of the fastest-growing areas of research in 3D printing today, with scientists getting ever-closer to the ultimate goal of being able to fabricate a human organ that would be suitable, and sustainable, for transplant. Studies are wide-ranging, from examining the effects of annealing in bone regeneration to exploring composites for coating scaffolds with nanofibers, as well as implanting cells without scaffolds.
Find out more about the use of electrospinning in bioprinting processes here. What do you think of this news? Let us know your thoughts! Join the discussion of this and other 3D printing topics at 3DPrintBoard.com.
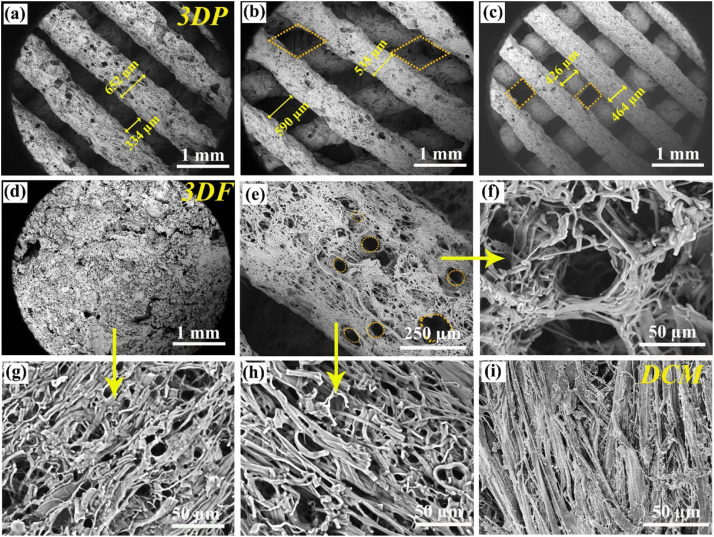
Microstructures of 3DP, 3DF and DCM. (a–c) SEM images of 3D-printed scaffolds with different pore structures. (d, g) SEM images of 3DF at different magnifications. (e, f, and h) SEM images of 3DP at various magnifications corresponding to the image in (a). (i) SEM image of DCM.
Subscribe to Our Email Newsletter
Stay up-to-date on all the latest news from the 3D printing industry and receive information and offers from third party vendors.
Print Services
Upload your 3D Models and get them printed quickly and efficiently.
You May Also Like
Johns Hopkins University Researchers Develop HyFAM Technology
Two scientists from Johns Hopkins University, Nathan C. Brown and Jochen Mueller, have developed a hybrid manufacturing technology they call HyFam, or Hybrid Formative Additive Manufacturing. Their work on this technology...
3D Printing G-Code Gets an Upgrade: T-Code
Good old G-Code still manages many 3D printers, great and small. Just like the STL, it’s a standard that enables collaboration while also holding the additive manufacturing (AM) industry back....
AM Rewind: The Biggest News and Trends of 2024
After a sluggish 2023, driven by persistent inflation and geopolitical tensions, 2024 has seen some recovery. Economic growth climbed from about 2.8 percent in 2023 to a modest 3.2 percent...
Metal Wire 3D Printer OEM ValCUN Announces Plans for 2025 Expansion
ValCUN, a Belgian original equipment manufacturer (OEM) of wire-based metal additive manufacturing (AM) hardware, has announced that the company has entered the next phase of its growth trajectory, making key...