Because the technology can achieve complex shapes and structures and multifunctional material systems, a trio of researchers in Ireland – Umair Gulzar, Colm Glynn, and Colm O’Dwyer – were interested in using 3D printing to create a specific device for energy storage: electrochemical energy storage devices (EESDs), such as batteries and supercapacitors. With the support of a grant from the European Union’s Horizon 2020 program, they published “Additive manufacturing for energy storage: Methods, designs and materials selection for customizable 3D printed batteries and supercapacitors,” in which they explain “the important role of methods, designs and material selection for energy storage devices made by 3D printing.”
“For electrochemical energy storage devices such as batteries and supercapacitors, 3D printing methods allows alternative form factors to be conceived based on the end use application need in mind at
the design stage,” the paper’s abstract states. “Additively manufactured energy storage devices require active materials and composites that are printable and this is influenced by performance requirements and the basic electrochemistry. The interplay between electrochemical response, stability, material type, object complexity and end use application are key to realising 3D printing for electrochemical energy storage.”
EESDs are typically put together using electrode fabrication, electrolyte addition, and device assembly, and while the processes are, as the researchers put it, “well optimized” for assembly line work, 3D printing allows for more flexibility and customization.
“Electrochemical energy storage (EES) represents another important arena where unique building properties of AM and 3D printing can be exploited,” the researchers wrote. “Thoughtfully designed 3D structures are reported to show better performance in batteries and supercapacitors.”
There are many challenges when it comes to manufacturing EESDs, with even more to think about when you add in 3D printing, as each method works a different way – DIW and jetting need a liquid feed, powder bed fusion needs a solid feed, etc. So it’s good to know what each method, and its materials, are capable of before you start 3D printing EESDs.
For the most part, inkjet printing (IJP), FDM, and DIW techniques are used to fabricate EESDs. The researchers said that the selection of the proper 3D printing method is a “synergetic process,” where the materials are made “according to the demands of the printing process based on the projected use in an EESD.” For instance, really viscous inks make good continuous filaments for extrusion 3D printing, and low viscosity inks are better for inkjet technology, as they form better droplets. DIW inks need shear thinning behavior with high stress and storage modulus for shape retention during deposition, in addition to quick solidification and mechanical stiffness for supporting other layers.
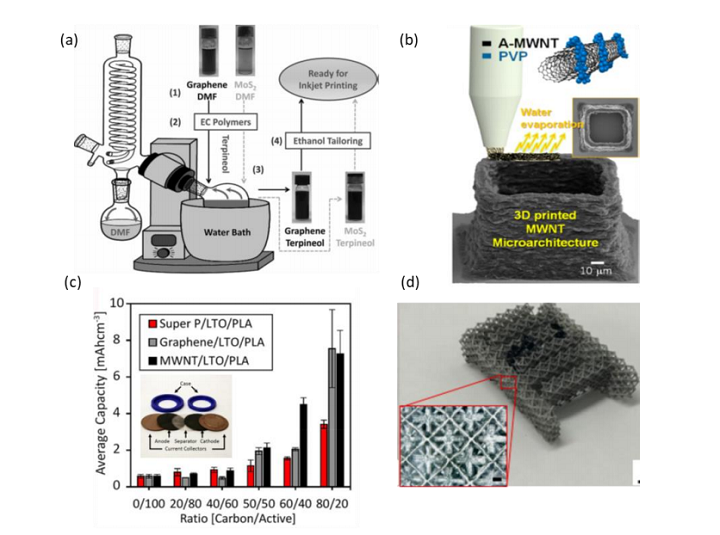
(a) Strategy for preparing IJP ink formulation. (b) DIW of PVP-MWCNTs based ink formulation, (c) Capacities & different composition of conductive additives for FDM printed EESD. (inset) FDM-based printed electrodes & casing. (d) SLA-based printed EESD after pyrolysis. Reprinted with the permission of Wiley publications & American Chemical Society.
Some of the additives used in the polymer matrix for EESDs made with FDM (extrusion-based) technology include conductive materials, like PLA/graphene and ABS/carbon, which are necessary for making electrodes in lithium ion batteries. There are currently efforts being made to increase the content of these conductive agents without negatively affecting the FDM process.
“Moreover, it is known that impurities in lower grade poly(lactic acid) and ABS plastics can influence some electrochemical activity, and any method to increase the surface area of graphite-containing thermoplastic by solvent[32]* or thermal decomposition[33] will obviously increase material-electrolyte interactions,” the researchers explained. “However, the intrinsic electronic and ionic conductivity in any printed electrode support material or active material composite is paramount, especially in the out-of-plane direction in sandwich design, and along the plane of in-plane designs. This is critical for intra- and inter-particle conductivity so that all active material in a composite, or active material are the surface is electrically and thus electrochemically addressable in a battery or supercapacitor.”
The figure below shows an example of how solvent or thermal decomposition can modify the intrinsic surface of an FDM 3D printed graphite-loaded PLA composite material, which can essentially turn on reversible galvanostatic charging and discharging in the 3D printed electrodes of a PLA/ABS battery.

(a) SEM images of graphite-PLA printed with FDM. Inset is porous morphology after acidic porosification of the surface. (b) Click 3D printed batteries. (c) SEM of LiCoO2/CNT coated FDM printed PLA electrode [black region in (b)]. (d) Cyclic voltammograms of activated & as-printed graphite-PLA electrodes at scan rate of 0.5 mv s-1 in a flooded solution of aqueous LiNO3 electrolyte showing redox activity once PLA surface is porous. (e) Galvanostatic charge-discharge profiles of as-printed & activated PLA electrodes in full battery cell displaying over 2 orders of magnitude improvement in specific capacity post activation. (f) Section of FDM printed PLA on ABS (green) & corresponding SEM image of PLA cross-section. σꞱ & σ‖ represent perpendicular & parallel electrical conductivity.
SLA 3D printing requires conductive agents to make EESDs, which can be achieved by adding one inside photocurable resins, or depositing a metal layer after the desired shape has been printed. In fact, some researchers have reported that adding silver nitrate and MWCNTs in polyethylene glycol diacrylate (PEGDA) and acrylic based resin can achieve limited electrical conductivity. Vat-photopolymerization can also be used to 3D print complex EESDs, and what it lacks in material choice, it makes up for in layer resolution. The feedstock’s viscosity can affect the object’s quality and print speed, but controlling temperature or diluents can help.
“Other methods like powder bed fusion, laminated object manufacturing and direct energy deposition are rarely been used to fabricate a complete EESD, nevertheless, some reports have shown manufacturing metal current collectors for EESDs,” the researchers wrote.
There are also design considerations to take into account when 3D printing EESDs. For the most part, an in-plane or sandwiched design is used to assemble 3D printed batteries and supercapacitors. Sandwiched-type EESDs have the potential for mass production and are cost-effective, while in-plane is good for tailored applications, like supercapacitors, because it allows a “minimum footprint with enhanced ionic transport.”
“One observation worth noting during our literature search was that in-plane designs are preferred (or at least more common) when EESDs are fabricated using DIW and IJP, while sandwich designs is readily used for FDM and SLA-based 3D printing,” the researchers wrote. “We believe that FDM and SLA uses insulating polymer matrix and principles behind these printing methods allow limited choice for making conductive composites which are essential for constructing an EESD. A second more fundamental reason is that FDM and especially SLA-based 3D printing can create objects in full form factor directly (coin cells, thin film cells, outer casing as well as complex electrodes) in a single or multistep print.”
Along with the method and materials, the charge storage process also has to be considered. A higher surface to volume ratio, completed through etching or selective decomposition of the photocurable resin or composite thermoplastic, will be good for surface pseudocapacitive storage and electrochemical double layer capacitance. However, a high surface area material capable of capacitive charge storage only works if the material has enough electrical conductivity.
“For EESD applications, and to some extent other electrochemical system…the choice of material, the nature of the final print in terms of composition, together with the attributes of the print specific to the application, will dictate the printing method used,” the researchers concluded.
Discuss this and other 3D printing topics at 3DPrintBoard.com or share your thoughts below.
Subscribe to Our Email Newsletter
Stay up-to-date on all the latest news from the 3D printing industry and receive information and offers from third party vendors.
Print Services
Upload your 3D Models and get them printed quickly and efficiently.
You May Also Like
U.S. Navy Lab Uses 3D Printing to Reduce Tooling Lead Time By Over 90%
The F-35 Lightning II Joint Program Office (JPO), responsible for life-cycle management of the key fifth-generation joint strike fighter (JSF) system used by the U.S., its allies, and its partners,...
Etsy Design Rule Change Reduces Selection of 3D Printed Goods
Online marketplace Etsy has implemented a rule change requiring all 3D printed goods on the site to be original designs. The update to the site’s Creativity Standards states, ¨Items produced using...
Honeywell Qualifies 6K Additive’s Nickel 718 for 3D Printed Aerospace & Defense Parts
6K Additive is renowned for manufacturing sustainable additive manufacturing (AM) powder, and offers a wide portfolio of premium metal and alloy powders that include titanium, copper, stainless steel, and nickel,...
MetalWorm Sells WAAM Systems to Research Institutes in Brazil and Malaysia
Turkish WAAM firm MetalWorm has sold a system in Malaysia and another in Brazil. This is an excellent example of a few emerging trends in additive. Firstly, WAAM was experimented...