In the recently published ‘Evaluation of the Mechanical Properties of Porous Thermoplastic Polyurethane Obtained by 3D Printing for Protective Gear’ Korean researchers Hyojeong Lee, Ran-i Eom, and Yejin Lee explore the uses of 3D printing for high-performance equipment.
We have seen additive manufacturing and 3D printing at work over the years to create both prototypes and parts for a variety of sports gear, ranging from custom mouth guards to football helmets, to protective hockey gear, and more. Here, the authors are experimenting with the potential for using thermoplastic polyurethane (TPU) as a 3D printing material, testing features like tensile strength, shock absorption, and compressibility.
Six different samples were 3D printed in a variety of environments, using a Cubicon 3D printer at thicknesses of 5 or 10 mm, and 10%, 50%, and 100% infill. The research team created four copies of each of the six main samples so they could attempt four different trials, finding both average and standard deviations.
The researchers analyzed the structures using Solidworks 2016, assessing both shock absorption and compression capabilities—with TPU exhibiting:
- Elastic modulus 2410 N/mm2
- Poisson’s ratio 0.3897
- Shear factor 862.2 N/mm2
“A 12.7 mm diameter circle was drawn at the center of the surface of each model to set the area of the vertical load, to mimic the actual tests,” stated the researchers. “The load on each sample was set to 50 N, as in the shock absorption tests. After the analysis conditions were set, a mesh of the modeling data was created, and the simulation was executed.”
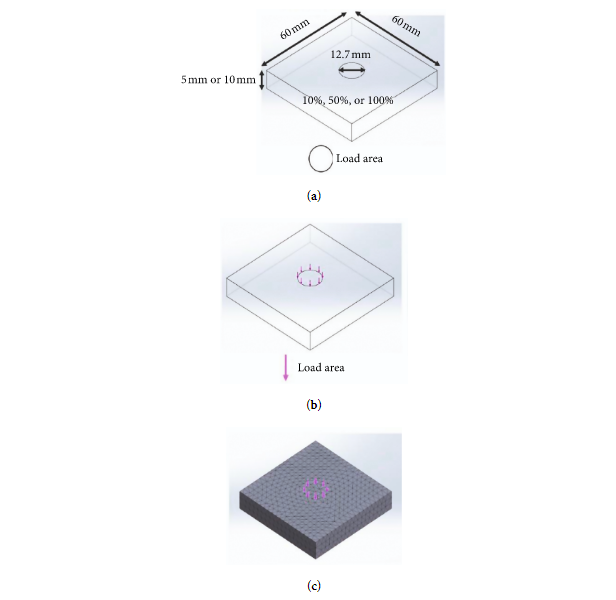
Location and dimensions of load area for the structural analysis. (a) Modeling. (b) Load value input. (c) Mesh creation.
The samples did not ‘fracture’ due to their rubberish material, rather than more fragile woven fibers:
“As the TPU fabric is printed directly (i.e., it is not made of woven fibers), the tensile strength is measured in MPa, and the property is different from general fibers. An increase in the TPU infill rate led to an increase in stress, regardless of the sample thickness. This makes the infill ratio an important factor for determining the tensile strength,” explained the researchers.
There were ‘discrepancies’ noted as infill percentages decreased, and thinner samples exhibited lower initial modulus. At 100% infill, TPU samples were around 10 MPa when stretched to 200 mm, showing less tensile strength in comparison to other plastics. Energy showed a decrease as infill was increased, with 100% infill samples exhibiting better impact resistance.
“All the specimens absorbed a total energy of at least 5 J. Therefore, it was confirmed that TPU material created using 3D printing could be used as personal protective equipment,” concluded the researchers. “Structural analyses showed that the thinner the material, the less deformation was caused by the impact, regardless of the infill condition. In addition, it was confirmed that the same tendency as the experimental results of the actual impact testing was shown. In the future, experiments are expected to be performed by simulating the properties of new materials, as well as different thickness and infill conditions.
“Although this study was restricted to the use of TPU, further studies will be conducted with the addition of newly developed materials to produce a continuously developed database. This can be applied as a fundamental basis for developing protective materials. Actual protective devices could also be produced to conduct wearing tests.”
What do you think of this news? Let us know your thoughts! Join the discussion of this and other 3D printing topics at 3DPrintBoard.com.
[Source / Images: ‘Evaluation of the Mechanical Properties of Porous Thermoplastic Polyurethane Obtained by 3D Printing for Protective Gear’]Subscribe to Our Email Newsletter
Stay up-to-date on all the latest news from the 3D printing industry and receive information and offers from third party vendors.
Print Services
Upload your 3D Models and get them printed quickly and efficiently.
You May Also Like
Reinventing Reindustrialization: Why NAVWAR Project Manager Spencer Koroly Invented a Made-in-America 3D Printer
It has become virtually impossible to regularly follow additive manufacturing (AM) industry news and not stumble across the term “defense industrial base” (DIB), a concept encompassing all the many diverse...
Inside The Barnes Global Advisors’ Vision for a Stronger AM Ecosystem
As additive manufacturing (AM) continues to revolutionize the industrial landscape, Pittsburgh-based consultancy The Barnes Global Advisors (TBGA) is helping shape what that future looks like. As the largest independent AM...
Ruggedized: How USMC Innovation Officer Matt Pine Navigates 3D Printing in the Military
Disclaimer: Matt Pine’s views are not the views of the Department of Defense nor the U.S. Marine Corps Throughout this decade thus far, the military’s adoption of additive manufacturing (AM)...
U.S. Congress Calls Out 3D Printing in Proposal for Commercial Reserve Manufacturing Network
Last week, the U.S. House of Representatives’ Appropriations Committee moved the FY 2026 defense bill forward to the House floor. Included in the legislation is a $131 million proposal for...