Bone Regeneration: Successful Bioprinting with Poly-Lactic-Co-Glycolic Acid/β-Tricalcium Phosphate Scaffolds
In ‘Poly(Dopamine) Coating on 3D-Printed Poly-Lactic-Co-Glycolic Acid/β-Tricalcium Phosphate Scaffolds for Bone Tissue Engineering,’ researchers from the School of Stomatology at Jilin University in Changchun, China are seeking improved methods for treating bone defects caused by health issues like osteoporosis, malignant tumors, and physical trauma. While currently there are numerous limitations for medical treatment, bioprinting and bone tissue engineering show great potential.
For this study, the researchers 3D printed polydopamine-coated poly-(lactic-co-glycolic acid)/β-tricalcium phosphate composite scaffolds, followed by characterization and biocompatibility tests.
The sample scaffolds created by the research team exhibited a regular shape, and pore size of ~500 μm, with a honeycomb structure—a form not uncommon in bioprinting.
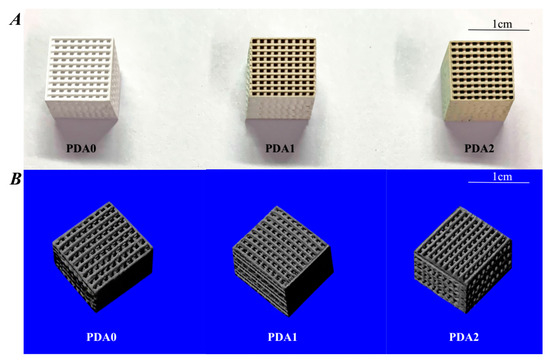
Overall appearance and structure of different scaffolds. (A) 3D-printed PLGA/β-TCP composite scaffolds with different PDA coatings; (B) reconstructed images from the micro-CT of the 3D-printed composite scaffolds with different coatings.
“The printed filaments are exhibited in a network structure, with a strong architectural integrity. The surface morphology of the fiber-aligned scaffolds, with or without PDA surface modification, can be characterized by SEM,” stated the researchers. “The results show that PDA0, PDA1, and PDA2 scaffolds have pores distributed over the internal walls, with a highly roughened structural coating layer and uneven micro-surface in comparison with non-coated scaffolds.”
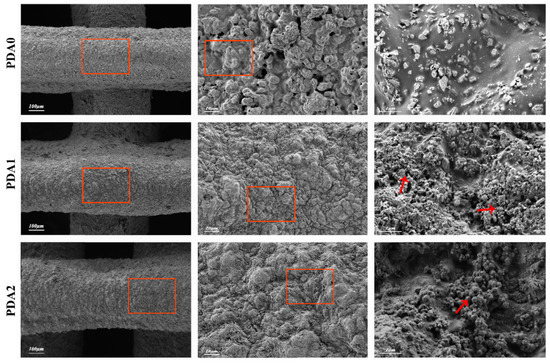
Surface morphology of different groups of scaffolds, observed under SEM. The images of different scaffolds show the surface features of the PDA0 group, PDA1 group, and PDA2 group at different magnifications. PDA is formed into a film-like coating on the surface of the scaffolds at a high magnification (red arrows).
PDA0, PDA1, and PDA2 were evaluated for surface wettability using water contact angle measurement, with PDA0 exhibiting the highest contact angle at 88.3°, 68.5°, and 55.1°, respectively (p < 0.05). Porosities were found to be 60.31%, 61.1%, and 59.67%, respectively. While porosity can be maintained during bone tissue engineering, density varies
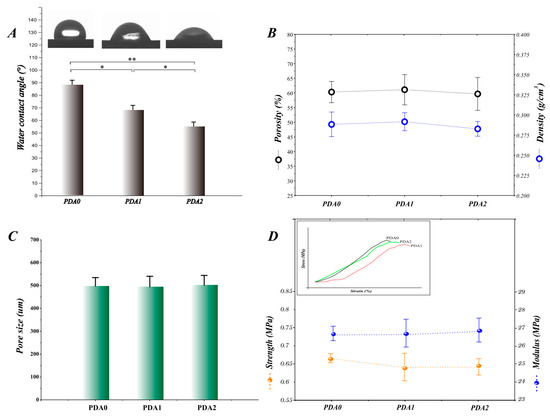
Characterization of the scaffolds from different experimental groups. (A) shows the water contact angle of the surface of the scaffolds of different groups; (B) shows the density and porosity of the scaffolds in different groups, where any differences in statistics are not indicated, and the scaffolds of different groups have a porosity of approximately 60% and density of approximately 0.28 g/cm3; (C) represents the average pore sizes of the scaffolds in each group, which are all approximately 500 μm, without differences; (D) indicates the mechanical properties, including the strength and modulus, and the affiliated figure denotes the trend of the scaffolds in each by a strain–stress curve. The results do not display any differences between the different groups, which are 0.65 MPa in strength and 26.5 MPa in modulus.
For cell attachment tests, the research team used mouse pre-osteogenic cells, demonstrating cell seeding efficiencies of the PDA0, PDA1, and PDA2 scaffolds at 56%, 76%, and 82%, respectively. They also noted that the PDA2 group ranked highest in adhesion (p < 0.05). As the PDA coating increased, cell membranes spread more expansively.
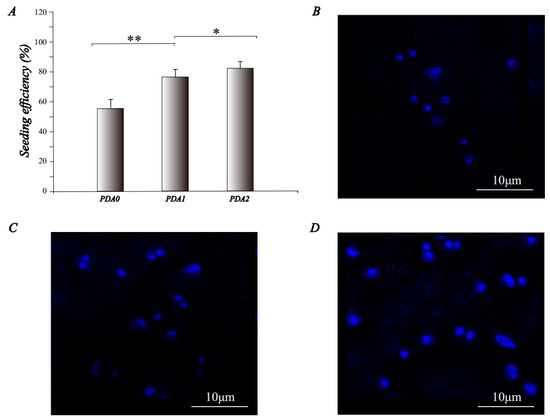
The cell-adhesion properties of the scaffold. (A) shows the adhesion efficiency, when cells were seeded into the scaffold; (B–D) are the pictures under a confocal laser microscope, stained by DAPI, which represent the PDA0, PDA1, and PDA2 groups, respectively.
Ultimately, the PDA-coated PLGA/β-TCP composite scaffolds were 3D printed successfully, according to the research team. Along with successful fabrication efforts, the researchers found that the sample scaffolds were ‘suitable’ as vehicles for bone tissue engineering. Using a one-way ANOVA analysis, the team evaluated the variations between the experimental groups. Results were ‘statistically significant’ at a p value <0.05.
“Furthermore, the in vitro cell biocompatibility test results show that the PDA coatings can improve cell adhesion and osteogenic differentiation. To further study the osteogenic effects of the PDA-coated scaffolds, we established a mouse skull defect model and implanted the scaffolds in the defects for a period,” concluded the authors.
“The bones with scaffolds were extracted to be analyzed for new bone formation, and the results show that the PDA-coated composite scaffolds perform a satisfactory repair effect. In conclusion, our results demonstrate that the simplified bio-inspired surface modification of PLGA/β-TCP scaffolds by PDA is a very promising method for effectively repairing bone defects.”
Because of the difficulties and challenges in bone tissue engineering, there is continued research into the subject, from studies regarding nanofiber tubular scaffolds to structures made with tricalcium phosphate, porous metallic biomaterials, and more.
What do you think of this news? Let us know your thoughts! Join the discussion of this and other 3D printing topics at 3DPrintBoard.com.
[Source / Image: ‘Poly(Dopamine) Coating on 3D-Printed Poly-Lactic-Co-Glycolic Acid/β-Tricalcium Phosphate Scaffolds for Bone Tissue Engineering’]Subscribe to Our Email Newsletter
Stay up-to-date on all the latest news from the 3D printing industry and receive information and offers from third party vendors.
Print Services
Upload your 3D Models and get them printed quickly and efficiently.
You May Also Like
Havaianas Collaborates with Zellerfeld to Launch 3D Printed Flip-Flops
The shoe of the summer is undoubtedly the flip-flop. Easy on, easy off, your feet won’t get sweaty because there’s not much material, and they’re available in a veritable rainbow...
UCLA Researchers Develop 3D Printed Pen that May Help Detect Parkinson’s Disease
Diagnosing Parkinson’s disease is difficult. Often, early symptoms of the progressive neurological condition may be overlooked, or mistaken for signs of aging. Early diagnosis can help save lives and improve...
Printing Money Episode 30: Q1 2025 Public 3D Printing Earnings Review with Troy Jensen, Cantor Fitzgerald
Printing Money is back with Episode 30, and it’s that quarterly time, so we are happy and thankful to welcome back Troy Jensen (Managing Director, Cantor Fitzgerald) to review the...
Heating Up: 3D Systems’ Scott Green Discusses 3D Printing’s Potential in the Data Center Industry
The relentless rise of NVIDIA, the steadily increasing pledges of major private and public investments in national infrastructure projects around the world, and the general cultural obsession with AI have...