There is an expanding line up of 3D printers that fill many niches from $199 desktop machines to $1m industrial giants. At the same time, the limited material range of 3D printers is expanding from a few to a few dozen. What if the type of printer you wanted wasn’t available? What if your lab or your application needed a completely new kind of 3D printer? What if you needed to print a new material that no one else can print? That is where 3DFigo‘s Philipp Schlautmann comes in. His company can develop and make you the right printer for the right application. What’s more, Philipp has developed a Fused Feedstock Depositioning technology and has a big lead on many players in binder jetting. His custom machines and technologies are way ahead of the market in many applications and are built for some of the most discerning customers.
What is 3DFigo?
3d-figo is a company dedicated to the development of customized 3D printers. Mainly we deal with our self-developed processes “Fused feedstock depositioning” (FFD) and the binderjeting process. We develop 3D printers and, if necessary, new technologies to be able to process special materials. Our FFD process is suitable to process materials such as TPE with hardness from 5 Shore and harder plastics as well as metals and ceramic materials. So from the softest plastic to ceramics can be processed on one machine.
Our binderjeting machines are always customized, one system is for example able to process layer thicknesses of up to 10mm and grain sizes of 0 to 5mm. Another system can integrate three-dimensional conductor paths into a solid ceramic body, so induction coils or similar electronic components can be printed.
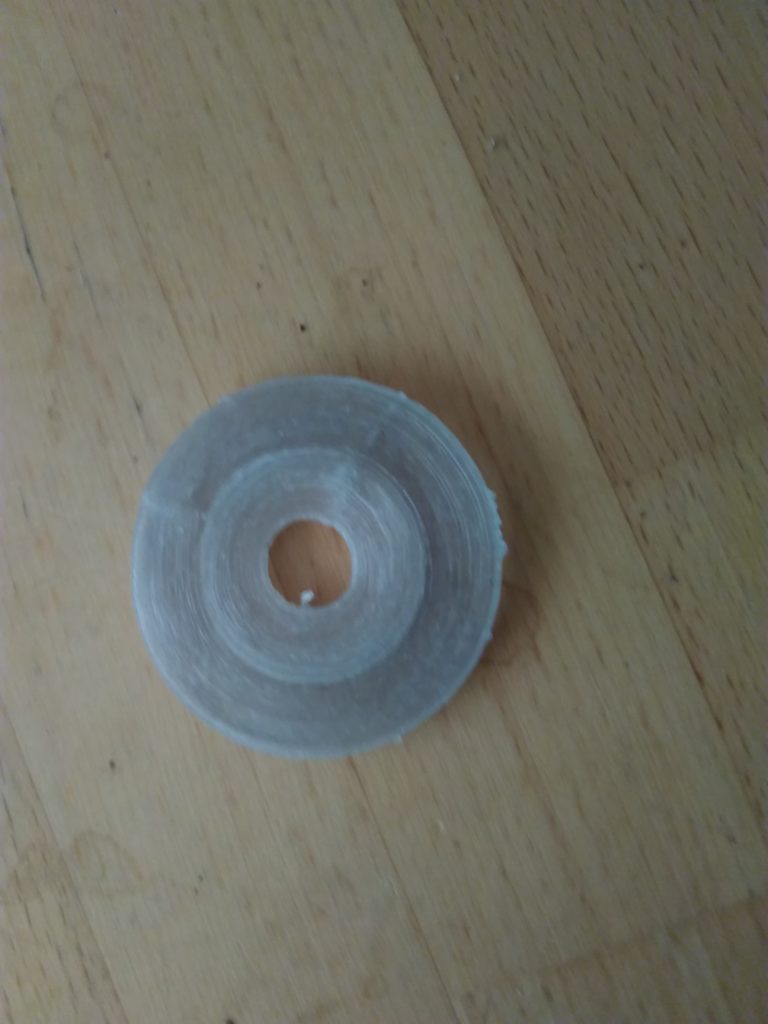
SteelTitaniumTPEZrO2, A Zirconium Steel Titanium 3D Print.
How did you start?
After completing my doctoral studies, in 2006 I founded MTplus as an engineering office for mechatronic product development. In 2009, I met Adrian Bowyer, the founder of the RepRap scene, and was inspired by him to develop my own 3D printers. My first FDM printer was built quickly, but the disappointment that the components did not stick to the build platform prompted me to develop the first MTplus permanent printing plate. It quickly proved to be extremely reliable and durable, which NASA also alerted us to. The ISS approval test series has shown that the plate is extremely safe and reliable. After that I worked on the development of my own extruder and developed the FFD technology. In 2014, together with my partner, I founded 3d-figo GmbH, which deals with the development of 3D printers. At the same time, the first binding jetting machines were built. I am currently planning to start my own printing shop in order to be able to produce parts for customers.
What kind of customers do you have?
Our 3D printers are designed for industrial customers and research institutions. The permanent printing plates are just as popular with private users as they are with industrial users. Our most prominent customer is certainly NASA.
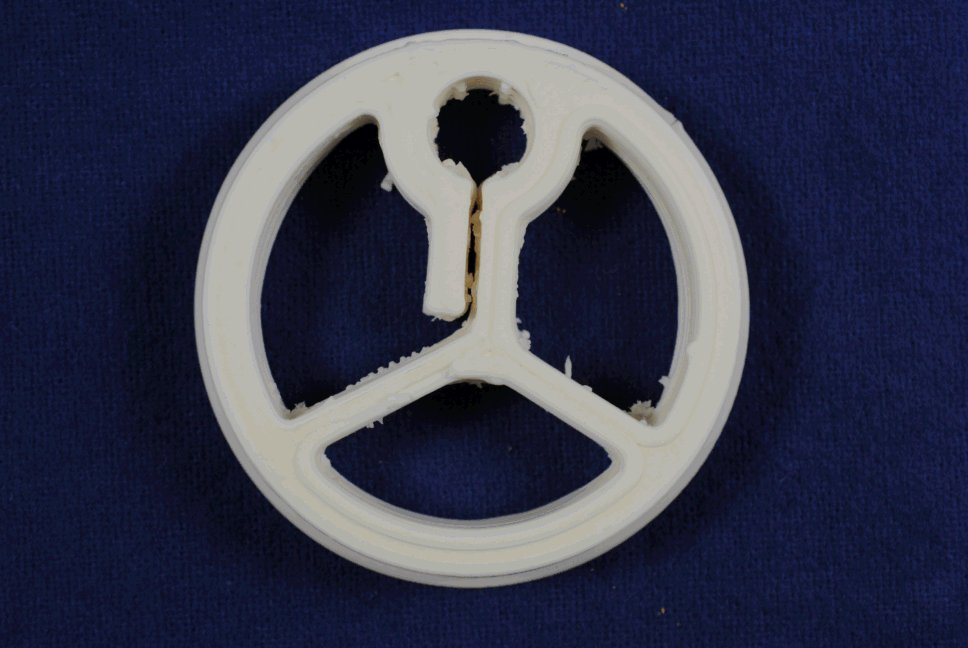
Al2O3 Aluminium Oxide
So would I come to you for a new type of printer, a new material, a new technology?
As a small innovative company, we are specialized in customer-specific solutions. We develop solutions that also process the most exotic materials. My concern is to advise the customer as openly as possible and, if necessary, also to recommend processes from competitors if it makes more sense for the customer. So it is always a good idea to come to me to develop something new.
3D printing MIM powder is currently very hot, what problems would you expect with these processes?
I’ve been working with MIM and CIM feedstocks and additive manufacturing every day for 9 years, I’ve experienced pretty much every problem with these materials. Many metallic and ceramic materials cause harmful emissions. Carbide and piezzo materials in particular can be exposed to extremely high levels of carcinogenic substances. I recommend everyone who is involved with 3D printing to study the material safety data sheets thoroughly. Thermoplastic extrusion processes in particular can cause major problems, both in the FDM and FFD processes. As far as the machines are concerned, we have solved all the major technical problems. Our print heads run reliably, our print bed works very well with most materials, and our filter system removes most emissions reliably. Some suppliers tend to simplify the technology, especially debinding and sintering is often simplified. Depending on the binder system, debinding in particular can require very complex technical equipment. The sintering furnace technology can also be very different and expensive depending on the material. I think it is a rumour that there is one furnace for everything.
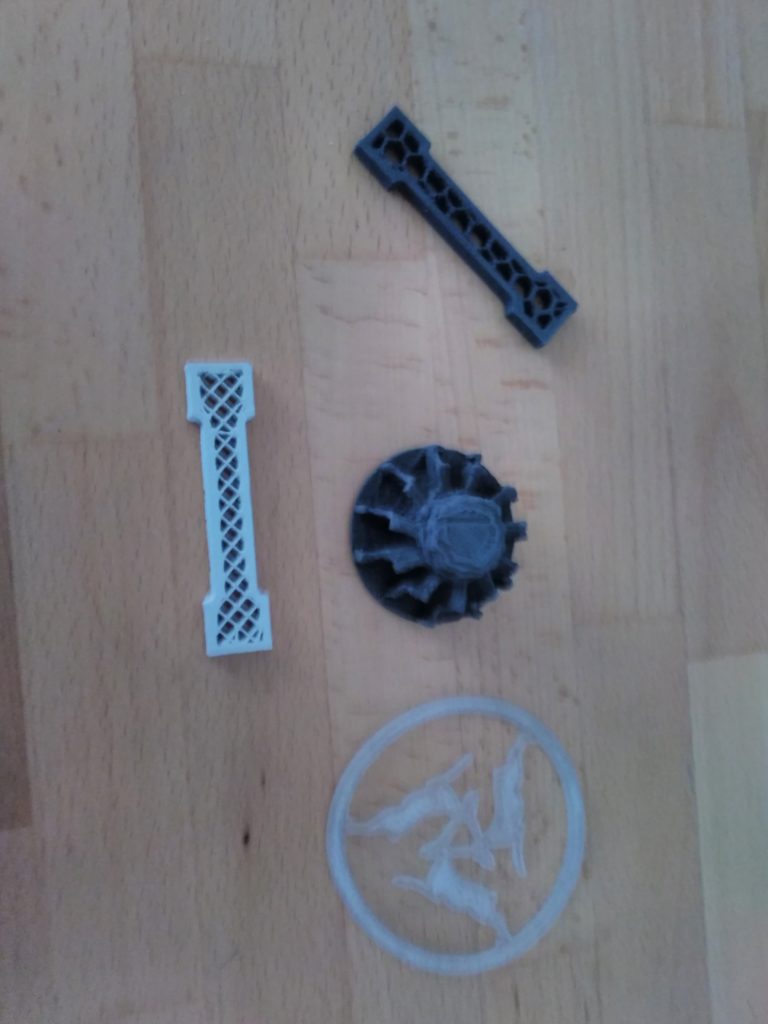
Steel Titanium Zirconium Parts
If we look at FDM for metal, what kind of problems do you see?
Metal FDM has the disadvantage that you have to develop special binder systems that have to allow a sufficiently high admixture of powder and then still have sufficient strength for filament production and filament handling. Many well-known and established binder systems are unable to meet these requirements, which limits the variety of materials available. Of course, the FFD process also poses the risk of harmful emissions.
Why is it so difficult to control the sintering step?
No furnace heats uniformly, hardly any geometry shrinks uniformly and debinding with different wall thicknesses is difficult to control. So there are many reasons for sintering errors, which is why sintering requires a lot of experience.
Can’t we just calculate the shrinkage for each geometry, wall thickness or size?
Theoretically, this is possible, but it is a difference in how I put the part into the furnace, also it is a difference how I curve the temperature. I have not yet seen a system that allows for a reliable simulation of the sintering process.
Ceramics is a small area in 3D printing today, would you expect it to grow?
Ceramic materials have fascinating properties such as temperature resistance, abrasion resistance, biocompatibility, piezo properties… However, due to their low elastic deformability, ceramic materials are not suitable for constructing larger structures or machine parts. All currently known processes for additive processing of ceramics have technological limits, the Lithoz process produces brilliant components with fantastic surface qualities and extremely fine structures and dense microstructures. The FFD process produces relatively coarse surfaces and structures with a dense microstructure. The binder jetting produces finer structures than the FFD, but is coarser than the Lithoz process. However, the structures that can be produced are generally not dense. In contrast to the possibility of forming fine structures, the construction rates of the processes that allow extrusion processes both cold and hot are orders of magnitude higher than the binder jetting, which is again orders of magnitude faster than the Lithoz process.
For every application, it is always important to choose the right procedure or the right combination of procedures. So it is possible to combine a Lithoz component with a FFD component and sinter together to form a component. So can combine the advantages of both methods.
The expensive and complicated sintering process restricts ceramic components to small, highly specialized components, which means that their diffusion will be less pronounced than that of metals and plastics.
What is FFD? How does it work?
The “Fused Feedsock Depositionig” processes injection molding granules in a thermoplastic extrusion to form components. The granules are poured into the top of the machine, melted and formed by a nozzle into a strag which then forms the component. It works much like the FDM method only without first generating a filament. As a result, the raw material costs are much lower and the quality of the molecular chains is better than with filaments.
Which materials can you print?
We can process thermoplastics, elastomers, metals and ceramics with the same machine. The softest plastic has a hardness of 5 shore of course, all harder plastics can also be processed, softer plastics are also conceivable. For the metals, all MIM feedstocks can be processed, so we processed aluminum, steel, copper but also tungsten carbide. For the ceramic materials, the bandwidth ranges from Al2O3, ZrO2, SiC, or SiNi and many more. In the binder systems, we have not found any that could not be processed.
Subscribe to Our Email Newsletter
Stay up-to-date on all the latest news from the 3D printing industry and receive information and offers from third party vendors.
Print Services
Upload your 3D Models and get them printed quickly and efficiently.
You May Also Like
The Dental Additive Manufacturing Market Could Nearly Double by 2033, According to AM Research
According to an AM Research report from 2024, the medical device industry, specifically in dentistry, prosthetics, and audiology, is expected to see significant growth as these segments continue to benefit from...
Heating Up: 3D Systems’ Scott Green Discusses 3D Printing’s Potential in the Data Center Industry
The relentless rise of NVIDIA, the steadily increasing pledges of major private and public investments in national infrastructure projects around the world, and the general cultural obsession with AI have...
AM Research Webinar Explores Continuum’s Sustainable Metal Additive Manufacturing Powders
Metal additive manufacturing (AM) powder supplier Continuum Powders is working to develop solutions that empower industries to reduce waste and optimize their resources. An independent life cycle assessment (LCA) of...
3D Printed Footwear Startup Koobz Lands $7.2M in Seed Round
California-based Koobz is focused on reshoring the U.S. footwear supply chain with advanced manufacturing processes, including 3D printing. The startup just announced that it has added $6 million to its...