In ‘Inversely 3D-Printed β-TCP Scaffolds for Bone Replacement,’ German researchers predefined pore structures in scaffolding to explore different cell growth behaviors. Using FDM 3D printing and PLA, the team of scientists created molds to direct bone growth.
Although 3D printing is lending new technology and techniques for bone regeneration, the researchers remind us that there are still many challenges, and mainly because bone tissue engineering is a difficult area of science regardless of method or material. Most importantly, biomechanical systems are complex and must encompass biocompatibility, suitable mechanical properties, and pore size.
While historically scaffolds have been 3D printed, here the researchers endeavor to define the pore structure within a 3D construct. They printed the scaffolds with PLA, using calcium phosphate (CaP) as biomaterial due to its biocompatibility, after which the β-TCP scaffolds with preset pore structure were characterized.
“To obtain the final bioceramic scaffolds, a water-based slurry was filled into the PLA molds. The slurry contained 70 wt% of β-TCP and 1 wt% based on solid content DOLAPIX CE64 (Zschimmer & Schwarz, Lahnstein, Germany) as a dispersant. The grain sizes of the β-TCP powder ranged from 0.6 to 40 µm (d10 = 2.0 ± 0.04 µm; d50 = 5.27 ± 0.08 µm, and d90 = 14.84 ± 0.09 µm),” explained the researchers.
“Samples with strand widths of 500, 750, and 1000 µm were produced with the 3D printer, filled with ceramic slurry, and sintered according to the above protocol. In the following, the designations 500, 750, and 1000 µm remained, which herein refer to the empty spaces between the β-TCP strands for the differentiation of the samples.”
β-TCP scaffold samples were weighed and measured, with surface roughness averaged from all values.
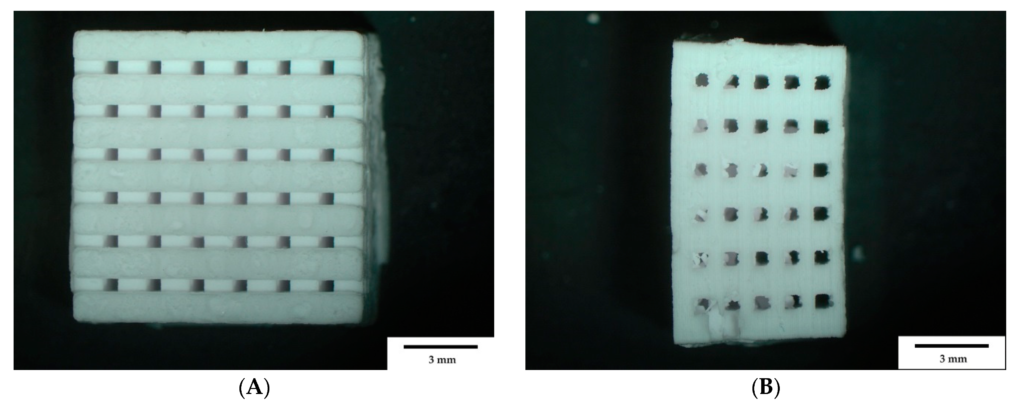
β-TCP scaffold (500 µm) through a stereomicroscope (Olympus SZ61). A: Top view; and B: Side view. Scale bar = 3mm; magnification: 0.67×.
“The scaffolds with a strand width of 1000 µm showed the highest roughness on the surface of 9.61 ± 2.02 µm. The 750 µm scaffolds has the lowest surface roughness of 7.97 µm ± 1.54 µm. With p > 0.05 the surface roughness values showed no significant differences,” explained the researchers.
Overall, the team was able to prove that different strand distances do influence scaffolds, with the 500 µm scaffolds showing the greatest compressive strength and exhibiting the best potential for being used in bone replacement.
“The biocompatibility of β-TCP was also successfully tested. The cells showed a high proliferation rate on the scaffolds, and no cytotoxicity was measured from the material. In addition, the degradation of the material, which is important for bone replacement, could be demonstrated with the help of simulated body fluid,” concluded the researchers.
“β-TCP showed an incipient degradation of the material after a 28-day incubation in an SBF solution, which could be detected by the formation of HA crystals on the samples. In conclusion, it can be said that β-TCP is biocompatible and thus a suitable material, and the inverse FDM printing process with subsequent slip casting is a suitable method for use in bone replacement.”
Although researchers soldier on within the bioprinting realm—amidst all the challenges found there—bone regeneration continues to be fraught with obstacles; however, scientists continue to create a variety of scaffolds, experiment with materials like hydroxyapatite, as well as coatings. What do you think of this news? Let us know your thoughts! Join the discussion of this and other 3D printing topics at 3DPrintBoard.com.

Macro and microstructure of the scaffolds; stereomicroscopic images of all three sizes: (a): 500 µm empty space; (b): 750 µm; and (c): 1000 µm. microstructures taken with FEI QUANTA 250 FEG, 20 kV, 3200x magnification of the surface from sample: (d): 500 µm; (e): 750 µm; and (f): 1000 µm.
Subscribe to Our Email Newsletter
Stay up-to-date on all the latest news from the 3D printing industry and receive information and offers from third party vendors.
You May Also Like
Gorilla Sports GE’s First 3D Printed Titanium Cast
How do you help a gorilla with a broken arm? Sounds like the start of a bad joke a zookeeper might tell, but it’s an actual dilemma recently faced by...
Nylon 3D Printed Parts Made More Functional with Coatings & Colors
Parts 3D printed from polyamide (PA, Nylon) 12 using powder bed fusion (PBF) are a mainstay in the additive manufacturing (AM) industry. While post-finishing processes have improved the porosity of...
$25M to Back Sintavia’s Largest Expansion of Metal 3D Printing Capacity Since 2019
Sintavia, the digital manufacturing company specializing in mission-critical parts for strategic sectors, announced a $25 million investment to increase its production capacity, the largest expansion to its operations since 2019....
Velo3D Initiates Public Offering in a Bid to Strengthen Financial Foundations and Drive Future Growth
Velo3D (NYSE: VLD) has been among a number of publicly traded 3D printing firms that have attempted to weather the current macroeconomic climate. After posting a challenging financial report for 2023,...