In the recently published ‘Microstructure Control in 3D Printing with Digital Light Processing,’ researchers from the Technical University of Denmark are exploring control issues in 3D printing, to include an antialiasing option meant to improve problems with surface appearance, creating subvoxel growth control. This means that while geometric structures may be printed with high quality, surface appearance can match that now too, lessening the common ‘rough’ appearance.
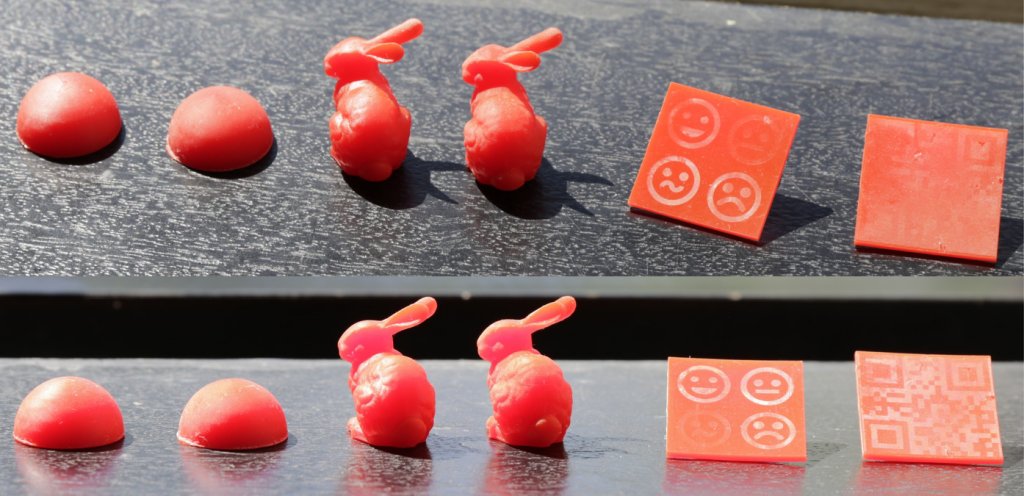
Hemispheres and bunnies with smooth and rough surfaces, and flat samples (smileys and QR code) with spatially varying anisotropic reflectance. The scene is observed from two different directions to exhibit the anisotropy. The sun is used as a directional light source. Each item was printed in a one‐step process using the presented technique.
While functionality may be uppermost in the minds of scientists and researchers, for many artists and designers the appearance is a priority too, often requiring extra finishing.

A desired circular print layer geometry (left), its rasterization according to the resolution of the projector (middle) and the same layer with greyscale values for antialiasing (right).
With greyscale patterns, the researchers were able to improve DLP 3D printing substantially, fabricating microfeatures and patterns for samples in this study, using a one-step process.
“By using this technique, we can modify the roughness and surface appearance of a print without changing materials or applying postprocessing to the sample,” state the researchers.
DLP printing usually offers a resolution of 15 to 100 µm, but this is dependent on the quality of the micromirror device of the projector, along with building plate precision. Solidification of resin relies on the level of UV light available, which can be increased through longer projection time or intensity of the light. Through increasing and decreasing intensity, the research team was able to control voxel growth, resulting in ‘very small features and patterns’ on the 3D printed sample. This also decreases the potential for aliasing and allows for fabrication of smooth, single-layer microfeatures.
“Slices are obtained by rasterizing the geometry, and if no measures are taken, spatial aliasing will be present along edges of the layers in the form of pixelated boundaries,” explained the authors. “Greyscale values based on supersampling (in all three dimensions) can be used to counteract this effect and produce a smoother surface. However, this is not enough to completely remove staircase artefacts in a surface. These artefacts lead to visible reflectance anisotropy and moiré patterns.”
The researchers completed experiments on a homebuilt, bottom-up DLP printer, verifying that they could 3D print several samples with a variety of textures and a smoother surface when using ‘sparse convolution noise with varying amplitude and frequency parameters.’
They printed one sample with different reflectance properties without changing any part of the DLP process, with reflection contrast due to use of BRDF models with no subsurface scattering.

Photos of the anisotropic smiley samples of Figure 13 (top row) with light incident from the directions shown in the bottom row. Reflection contrast predictions based on our analytic BRDF models are shown in the middle row. While the contrast seen in the printed samples is not as clear as in the predictions, the intensity variations are qualitatively similar.
For the next sample, the team 3D printed a hemisphere without any greyscale pattern applied and then compared it to others.
“The presence of a greyscale pattern produced by a smooth irregular noise function with low amplitude makes the surface smoother and removes the majority of the staircase aliasing artefacts introduced by the layered printing process. As the amplitude increases, the specular highlight becomes less visible and the surface appears to be more diffuse,” explained the authors.

Hemisphere printed without applying a greyscale pattern to the surface, leftmost, and from second to rightmost when using noise with amplitude. Mesh slicing was done with ray tracing. The light‐view configuration is the same within each row.
Greyscale patterns were used in creating the Stanford Bunny, with a more complex structure. For this sample, no patterns were applied to the surface, and they also had better results through using sparse convolution noise in the right and rightmost columns.
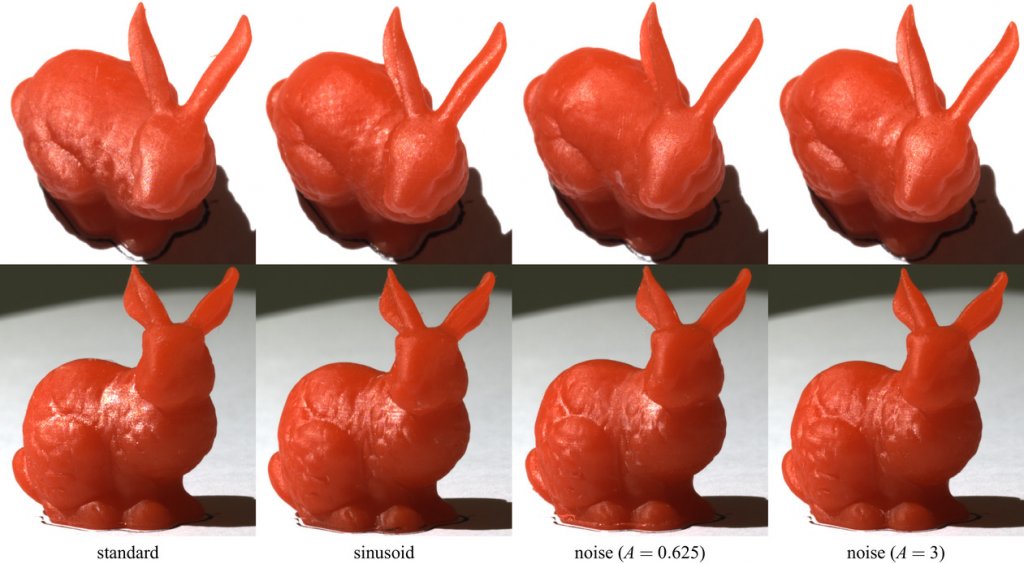
Stanford Bunny printed and photographed in two different light‐view configurations (rows). The bunny was printed without any greyscale pattern applied (standard), with an isotropic 2D sinusoid function applied (sinusoid, urn:x-wiley:01677055:media:cgf13807:cgf13807-math-0051µm), and using sparse convolution noise with low and high amplitudes (A) and frequency urn:x-wiley:01677055:media:cgf13807:cgf13807-math-0052 (noise). The glean due to anisotropic reflection caused by layering artefacts is clearly observable for the standard technique. The sinusoid pattern reduces the problem but introduces regularity artefacts. The noise function more effectively reduces the problem. As compared with the rough bunny (urn:x-wiley:01677055:media:cgf13807:cgf13807-math-0053), the smooth bunny (urn:x-wiley:01677055:media:cgf13807:cgf13807-math-0054) is brighter in the highlight regions and darker outside those regions as expected. Mesh slicing was done with rasterization.
“We have described a pipeline for applying greyscale patterns to surface voxels during the slicing of mesh geometry. Finally, we included a procedure for calibrating the parameters of a DLP printer and for estimating the ground noise added to the surface by the printing process,” concluded the researchers. “Our results demonstrate that by modulating the UV light intensity of a DLP projector with greyscale images, we can print samples with spatially varying reflectance properties, such as anisotropic effects and surface roughness.”
Researchers around the world continue to improve on many 3D printing processes, to include DLP 3D printing, whether using faster, higher-resolution techniques, reinforced nanocomposites, multi-material processes, or more. What do you think of this news? Let us know your thoughts! Join the discussion of this and other 3D printing topics at 3DPrintBoard.com.
[Source / Images: ‘Microstructure Control in 3D Printing with Digital Light Processing’]
Subscribe to Our Email Newsletter
Stay up-to-date on all the latest news from the 3D printing industry and receive information and offers from third party vendors.
Print Services
Upload your 3D Models and get them printed quickly and efficiently.
You May Also Like
Reinventing Reindustrialization: Why NAVWAR Project Manager Spencer Koroly Invented a Made-in-America 3D Printer
It has become virtually impossible to regularly follow additive manufacturing (AM) industry news and not stumble across the term “defense industrial base” (DIB), a concept encompassing all the many diverse...
Inside The Barnes Global Advisors’ Vision for a Stronger AM Ecosystem
As additive manufacturing (AM) continues to revolutionize the industrial landscape, Pittsburgh-based consultancy The Barnes Global Advisors (TBGA) is helping shape what that future looks like. As the largest independent AM...
Ruggedized: How USMC Innovation Officer Matt Pine Navigates 3D Printing in the Military
Disclaimer: Matt Pine’s views are not the views of the Department of Defense nor the U.S. Marine Corps Throughout this decade thus far, the military’s adoption of additive manufacturing (AM)...
U.S. Congress Calls Out 3D Printing in Proposal for Commercial Reserve Manufacturing Network
Last week, the U.S. House of Representatives’ Appropriations Committee moved the FY 2026 defense bill forward to the House floor. Included in the legislation is a $131 million proposal for...