In ‘Synthesis, characterization and 3D printing of linear and star-shaped poly(propylene fumarate) for medical applications,’ Yuanyuan Luo offers a PhD dissertation for The University of Akron on the subject of additive manufacturing and new polymer synthetics for use in the medical realm.
As materials science continues to expand, researchers are drawn to exploring the uses of 3D printing for complex geometries in regenerative medicine like cranial facial bone defect repair. Features like the following are required:
- Purity
- Suitable molecular weight
- Molecular mass distribution
- Proper glass transition temperature properties
“The failing to reliably and reproducibly produce a material may cause final device failure in tests like mechanical, biocompatible and/or pre-clinical animal studies, let alone to pass FDA regulations,” explains Luo, focusing on Poly(propylene fumarate) (PPF)—a non-toxic polyester material that is also amorphous, degradable, and can be cross-linked.

Three main types of manufacturing processes. a. additive manufacturing method where an object is built in a “layer-by-layer” style. b. subtractive manufacturing method where an object is built via removing excess material from a bulk object by machining. c. formative manufacturing method where an object is formed inside prefabricated molds
Luo explains how PPF can be synthesized for 3D printing and used in high-resolution applications for bone regeneration. The star-shaped PPF was also capable of achieving higher molecular mass and offering ‘significant improvements’ in comparison to other methods.
The author continues to discuss the challenges historically encountered, however, in the use of 3D printing to create implants for bone regeneration, along with benefits such as better reproducibility in scaffold fabrication, improved accuracy, and better mechanical properties.

General 3D printing flow chart diagram of a wearable customized oral delivery mouthguard in a clinical case16 Data acquisition, using a digital scanner to scan the customer’s maxillary anatomy. 3D manufacture, using computer aided design and modeling software to guide an extrusion-based 3D printer print this product with desired compound. Last, performance evaluation of the customer-matched 3D-printed mouthguard on each customer. (Reprinted from Liang, K.; Carmone, S.; Brambilla, D.; Leroux, J.-C., 3D printing of a wearable personalized oral delivery device: A first-in-human study. Science advances 2018, 4 (5), eaat2544. ©Liang, K.; Carmone, S.; Brambilla, D.; Leroux, J.-C., some rights reserved; exclusive licensee American Association for the Advancement of Science. Distributed under a Creative Commons Attribution NonCommercial License 4.0 (CC BY-NC) https://creativecommons.org/licenses/by-nc/4.0/)
Some ‘resorbable polymers’ have been used thus far in regenerative applications, listed in the table below.
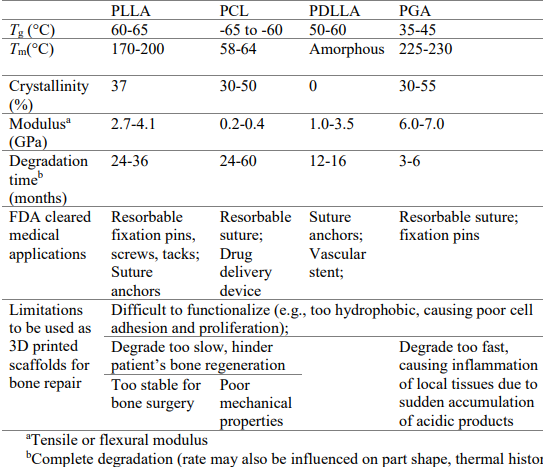
Physical properties of commercially available resorbable polyesters, examples of their applications in regenerative medicine and limitations of these materials to be used in 3D printing for patient-matched bone defect repair
“Although these resorbable polyesters have been clinically used in several degradable medical devices, they are not suitable for bone tissue regeneration due to some of their inherent physical and chemical properties,” explains Luo, emphasizing the need for new resorbable polymers.
PPF is considered suitable due to the many beneficial features it offers, along with biocompatibility and tunability. It can also be crosslinked with itself and reactive diluents like diethyl fumarate, a critical quality in bone tissue engineering since the materials must be similar in properties to the tissue being replaced. PPF materials can also be used effectively as drug delivery systems.
PPF has also been used in several pre-clinical studies, but the author reports some ‘significant barriers,’ due to issues with step growth polymerization—one of the methods that can be used, along with ring opening copolymerization (ROCOP). With the use of PPF-based resins, the researchers were able to 3D print at higher molecular mass level, achieving more ‘diverse’ mechanical properties.
“Such reproducible synthetic methods and resin viscosity tuning techniques not only paved the road to further identify the potential of using 3D printed PPF scaffolds in regenerative medicine field, but also can be adapted for the developing other related biomaterials,” concluded the researchers.
3D printing and bone regeneration are a hot topic these days, with researchers experimenting with titanium in additive manufacturing, exploring with electrospinning and 3D printed scaffolds, and studying issues like annealing. What do you think of this news? Let us know your thoughts! Join the discussion of this and other 3D printing topics at 3DPrintBoard.com.

Diagrams of 3D printing techniques commonly used in research and clinical medical applications. a, extrusion-based 3D printing method known as fused deposition modeling.26 b, One type of ink-based based 3D printing method, known as powder-binder 3D printing.26 c, One type of light-based 3D printing method known as stereolithography.40 d, one type of light-based 3D printing method known as digital light processing. (Figure 1.3.c and 1.3.d were reprinted from Biomaterials, 33(26), Billiet, T.; Vandenhaute, M.; Schelfhout, J.; Van Vlierberghe, S.; Dubruel, P., A review of trends and limitations in hydrogel-rapid prototyping for tissue engineering, 6020-6041, Copyright (2012), with permission from Elsevier)40 e, one type of light-based 3D printing method known as selective laser sintering. (Figure 1.3.a, 1.3.b and 1.3.e were adapted from Advanced Healthcare Materials, 4(12), Do, A. V.; Khorsand, B.; Geary, S. M.; Salem, A. K., 3D printing of scaffolds for tissue regeneration applications, 1742-1762, Copyright (2015), with permission from John Wiley and Sons) 26
Subscribe to Our Email Newsletter
Stay up-to-date on all the latest news from the 3D printing industry and receive information and offers from third party vendors.
Print Services
Upload your 3D Models and get them printed quickly and efficiently.
You May Also Like
Reinventing Reindustrialization: Why NAVWAR Project Manager Spencer Koroly Invented a Made-in-America 3D Printer
It has become virtually impossible to regularly follow additive manufacturing (AM) industry news and not stumble across the term “defense industrial base” (DIB), a concept encompassing all the many diverse...
Inside The Barnes Global Advisors’ Vision for a Stronger AM Ecosystem
As additive manufacturing (AM) continues to revolutionize the industrial landscape, Pittsburgh-based consultancy The Barnes Global Advisors (TBGA) is helping shape what that future looks like. As the largest independent AM...
Ruggedized: How USMC Innovation Officer Matt Pine Navigates 3D Printing in the Military
Disclaimer: Matt Pine’s views are not the views of the Department of Defense nor the U.S. Marine Corps Throughout this decade thus far, the military’s adoption of additive manufacturing (AM)...
U.S. Congress Calls Out 3D Printing in Proposal for Commercial Reserve Manufacturing Network
Last week, the U.S. House of Representatives’ Appropriations Committee moved the FY 2026 defense bill forward to the House floor. Included in the legislation is a $131 million proposal for...