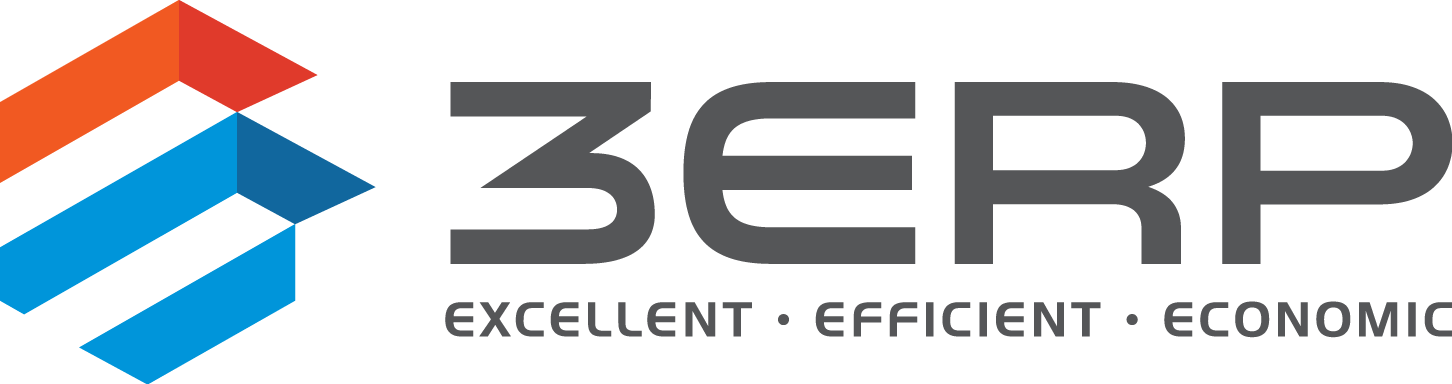
Several manufacturing technologies exist for making plastic parts. All over the world, injection presses, 3D printers and CNC machines are at this moment cutting, extruding and forming plastic into usable parts. All are highly useful machines, all of which offer their own particular advantages.
Injection molding — the process of injecting liquid plastic into metal molds — is the most widely used process for making plastic parts, but alternatives like vacuum casting and FDM 3D printing provide different benefits, giving designers and manufacturers a great deal of flexibility. After all, one project may require an injection molding press, while another may require a 3D printer.
In many instances, however, different technologies are used for different stages of manufacturing. 3D printing, for example, is frequently preferred for prototyping, since it is simple, transportable and comes with incredibly low start-up costs. Injection molding, meanwhile, is often the go-to process for huge volumes of end-use parts, since it is fast and highly repeatable. One technology serves the research and development phase; the other takes care of production.
But what happens when you create a 3D printed prototype and need to move to production with injection molding? How can you ensure a molded part will match the specifications of its printed counterpart, given the radical differences in the two manufacturing technologies? How do you plan ahead to ensure success in both prototyping and production?
3ERP, a global rapid prototyping company that provides on-demand 3D printing and injection molding services, has provided five key tips for companies looking to transition from 3D printing to injection molding.
Design for injection molding where possible
It’s not always easy to think ahead. When your immediate priority is making a 3D printed prototype, the natural instinct is to create the best possible printed part, which means applying DFM (design for manufacturing) principles to the 3D printing process.
But if you’re planning to eventually move from 3D printing to injection molding, 3D printed prototypes must be designed so they are not only printable, but also moldable.
In practice, this means following injection molding design principles — even during the 3D printing stage. Draft angles should be included, overhangs should be avoided and sharp corners should be rounded. Furthermore, complex infill patterns (which would actually improve the strength and efficiency of the 3D printed part) should be abandoned in favor of simple ribs, since a mold cannot replicate those complex infill patterns.
Designing for injection molding from the outset reduces the need for drastic changes ahead of production, simplifying the transition from one process to the other.
Print with production materials
A useful prototype is not necessarily one that looks and performs to the highest possible standard. Instead, a useful prototype is one that best represents the end-use part, including both its strengths and weaknesses.
This might mean making certain compromises, including in material selection.
Injection molding, a highly flexible process, is compatible with a huge variety of plastics, while 3D printing is more limited in terms of available materials. But when designing a 3D printed prototype, it is important to choose a material that matches or at least mimics the material to be used during production.
Importantly, this may not be the natural choice for a successful 3D printing job. Some effective molding materials are actually quite difficult to 3D print, requiring extra time and more thorough post-processing. However, choosing a representative material will produce a prototype that more truly represents the final part, allowing for a smoother transition to production.
Polish prototypes for a ‘molded’ finish
For mechanical or aesthetic parts, it is important to create prototypes with a surface finish that represents the finish of the final part. Mechanical parts may demand a certain level of friction or smoothness, so a prototype with a radically different texture will not be particularly useful. (Additionally, a professional-looking prototype may help a company to market or promote their product.)
Thankfully, surface finishing treatments can be applied to transform the exterior of a 3D printed prototype. With a professional polish, applied with a cloth or buffing wheel, the surface roughness of a printed part can be dramatically reduced, even producing a mirror-like shine.
The result is a 3D printed part that — free of its layer lines and rough texture — actually looks and feels like a molded part.
Go beyond FDM
FDM (Fused Deposition Modeling) 3D printers are a hugely popular choice for prototyping. They’re cheap, easy-to-use and compatible with a huge range of plastic filaments, and many businesses simply set them up in an office for lightning-fast iteration.
That being said, FDM 3D printing creates parts that are vastly dissimilar to molded parts. The structural composition and surface finish are totally unalike, so an FDM-made prototype is not easily transformable into a molded component.
On the other hand, more high-quality alternatives to FDM are capable of producing a more molded-like part. PolyJet 3D printers, for example, can produce parts with tight tolerances and smooth surfaces, as can light-based processes like Stereolithography (SLA). (SLA, however, may only be suitable for aesthetic prototypes, since it creates parts that are fairly weak and brittle.)
Seek specialist advice
It may seem obvious, but one of the easiest ways to ensure a smooth transition between 3D printed prototypes and injection molded final parts is to discuss the entire project with an expert.
If you plan to order a prototype through a professional service provider, be sure to let them know that the end-use part will be made using injection molding. Better still, use the same service provider for prototyping and production, allowing them to bridge the two processes with their expert know-how.
Contact 3ERP for a fast quote on prototyping, short-run production and getting from one to the other with ease.
Subscribe to Our Email Newsletter
Stay up-to-date on all the latest news from the 3D printing industry and receive information and offers from third party vendors.
Print Services
Upload your 3D Models and get them printed quickly and efficiently.
You May Also Like
Reinventing Reindustrialization: Why NAVWAR Project Manager Spencer Koroly Invented a Made-in-America 3D Printer
It has become virtually impossible to regularly follow additive manufacturing (AM) industry news and not stumble across the term “defense industrial base” (DIB), a concept encompassing all the many diverse...
Inside The Barnes Global Advisors’ Vision for a Stronger AM Ecosystem
As additive manufacturing (AM) continues to revolutionize the industrial landscape, Pittsburgh-based consultancy The Barnes Global Advisors (TBGA) is helping shape what that future looks like. As the largest independent AM...
Ruggedized: How USMC Innovation Officer Matt Pine Navigates 3D Printing in the Military
Disclaimer: Matt Pine’s views are not the views of the Department of Defense nor the U.S. Marine Corps Throughout this decade thus far, the military’s adoption of additive manufacturing (AM)...
U.S. Congress Calls Out 3D Printing in Proposal for Commercial Reserve Manufacturing Network
Last week, the U.S. House of Representatives’ Appropriations Committee moved the FY 2026 defense bill forward to the House floor. Included in the legislation is a $131 million proposal for...