Chinese researchers are seeking new ways to create stronger cell growth and sustainability in scaffolds. With their findings outlined in the recently published, ‘Structure-induced cell growth by 3D printing of heterogeneous scaffolds with ultrafine fibers,’ the researchers explain more about their new 3D printing technique for creating heterogeneous structures with cells induced to elongate.
As with so many cellular constructions in the lab, in vitro research allows for incredible innovation. And the world of 3D printing and bioprinting is no exception as the field of tissue engineering continues to grow. Much of this is centered around creating scaffolds for regulating cells—and while many challenges remain, here the researchers are interested in using new materials to induce better growth.
Keeping cells alive in the lab is key for growing tissue, and scaffolds must be conducive such activity. Without the correct properties, however, they can affect:
- Cell attachment
- Proliferation
- Differentiation
- Migration
The team was inspired by the realization that cells were ‘exhibiting different morphological characteristics on different fibers and pores,’ meaning that great promise exists for better tissue engineering via scaffolding control. After reviewing previous studies, the team developed an EHD direct writing technique, accompanied by a melt electro-writing heterogeneous scaffold (MEWHS) presenting a high-performance level of control for sustaining cells.
MEWHS allows for a ‘quick response’ in prompting cell growth because the scientists were able to print different structures for different regions within one scaffold—encouraging an environment like that of an in vivo atmosphere. In 3D printing scaffolds with variable fiber spacing, three types were created:
- A heterogeneous rectangular structure with fiber spacing of 100, 200, and 500 μm and across angle at 90°.
- A parallelogram with fiber spacing of 100 and 200 μm and across angle at 45°.
- A triangle with fiber spacing of 100 and 200 μm and across angle at 60°.
Structures were 3D printed both by changing speed when the moving stage changed direction (useful for large structures that are mechanically different), or by changing speed during the printing line (useful in the presence of complex mechanical properties).
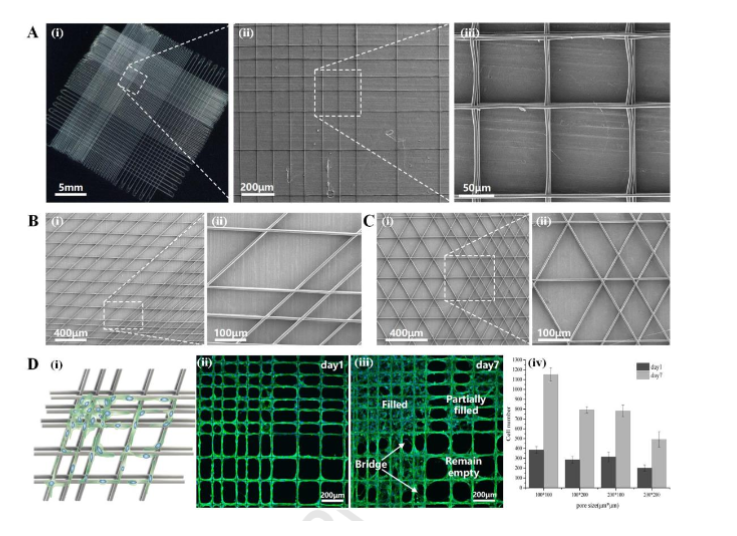
Characteristics of scaffolds with different pore shapes and sizes. A) Heterogeneous structure of a rectangle with a fiber space measuring100,200, and 500μm, crossangle at 90°.B) Heterogeneous structure of a parallelogram with a fiber space measuring 100 and 200 μm, crossangle at 45°.C) Heterogeneous structure of a triangle with a fiber space measuring100and200μm, crossangle at 60°.D)(i)Schematic diagram of cell growth induced by different pore sizes. (ii)HUVECs in the scaffold with pore sizes of 100 and 200 μm on Day1. (iii)HUVECs in the scaffold with pore sizes of 100 and 200 μm on Day7. The region with small pores were filled, whereas the region with large pores remained empty. All scaffolds were printed for 5 layers.(iv) Cell proliferation in regions of different pore sizes, cells were counted in four 600*600μm regions
“The areas consisting of thin fibers were transparent relative to the areas consisting of thick fibers,” stated the researchers, having produced three samples in the form of a pentagram, Tai Chi, and an eagle, which represents the logo of Zhejiang University.”
In using both FEA and the stretching test, the researchers were able to show a range of different mechanical properties within the varying regions they designed. Afterward, they observed variances in both the growth and morphology of BMSCs and HUVECs on the scaffolding. Ultimately, they were able to induce cell growth on the new scaffolding.
“The heterogeneous scaffold can enhance its potential to mimic the environment of an in vivo tissue and provide a method to induce cell growth for tissue engineering in vitro,” concluded the researchers.
Cell sustainability in bioprinting is an ongoing challenge but researchers around the world continue to perform different studies and research, from creating new materials, to attempting procedures like cryotherapy, and even innovating in areas like bioprinting microbial fuel cells.
What do you think of this news? Let us know your thoughts; join the discussion of this and other 3D printing topics at 3DPrintBoard.com.
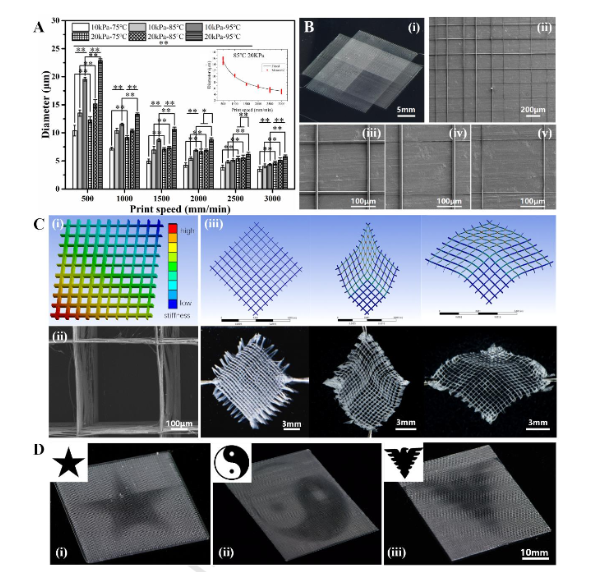
Fabrication and properties of scaffolds with different fiber diameters. A)Effects of temperature, air pressure, and collecting speed on fiber diameters by MEW. The inset is the fitted curve and the measured points, the fibers were printed at 85°C, 20kPa. B) Heterogeneous structure with different fiber diameters. Four parts consisting of fibers printed at 500 and 2000mm/min. (i) Photo of the heterogeneous scaffold. (ii)SEM image of the scaffold at the border of the 4 parts.(iii),(iv), and(v) are details of fibers in different parts.C)Comparison of mechanical analysis and stretching test results of the heterogeneous structure with different fiber diameters.i)Model of the scaffold, with different colors representing different levels of stiffness. ii) SEM image of one pore. (iii)Results of FEA and stretching test. D) Complex patterns with a heterogenous structure consisting of different fiber diameters. (i),(ii), and(iii)are the star, Tai Chi, and the eagle, respectively.
Subscribe to Our Email Newsletter
Stay up-to-date on all the latest news from the 3D printing industry and receive information and offers from third party vendors.
Print Services
Upload your 3D Models and get them printed quickly and efficiently.
You May Also Like
The Dental Additive Manufacturing Market Could Nearly Double by 2033, According to AM Research
According to an AM Research report from 2024, the medical device industry, specifically in dentistry, prosthetics, and audiology, is expected to see significant growth as these segments continue to benefit from...
Heating Up: 3D Systems’ Scott Green Discusses 3D Printing’s Potential in the Data Center Industry
The relentless rise of NVIDIA, the steadily increasing pledges of major private and public investments in national infrastructure projects around the world, and the general cultural obsession with AI have...
AM Research Webinar Explores Continuum’s Sustainable Metal Additive Manufacturing Powders
Metal additive manufacturing (AM) powder supplier Continuum Powders is working to develop solutions that empower industries to reduce waste and optimize their resources. An independent life cycle assessment (LCA) of...
3D Printed Footwear Startup Koobz Lands $7.2M in Seed Round
California-based Koobz is focused on reshoring the U.S. footwear supply chain with advanced manufacturing processes, including 3D printing. The startup just announced that it has added $6 million to its...