Researchers from the University of Jyvaskyla in Finland are exploring SLS 3D printing techniques, outlined in the recently published ‘Fabrication of Porous Hydrogenation Catalysts by a Selective Laser Sintering 3D Printing Technique.’ For this study, the team used porous, solid objects for easy attachment with the active component Pd/SiO2. To manipulate the properties, they varied printing parameters.
Realizing the benefits of using porous SLS 3D printed objects over powder-based catalysts, the team of researchers has been able to SLS 3D print solid but porous flow-through filters for selective capturing of Au, Pd, and Pt from acidic leachate of electronic waste. Palladium on silica (Pd/SiO2 with 5 wt % palladium) is commercially available and was mixed with polypropylene (PP). The research focused on how the porous material affected catalytic activity, while also examining hydrogenation activity.
In ‘introducing the catalysts,’ the researchers used 3D printed magnetic stir bar covers, but they point out that such a project could easily be elevated with different samples of more complex geometries. They began by taking images of the 3D prints to check out the pores caused by the voids in between the layers which were only partially melted.
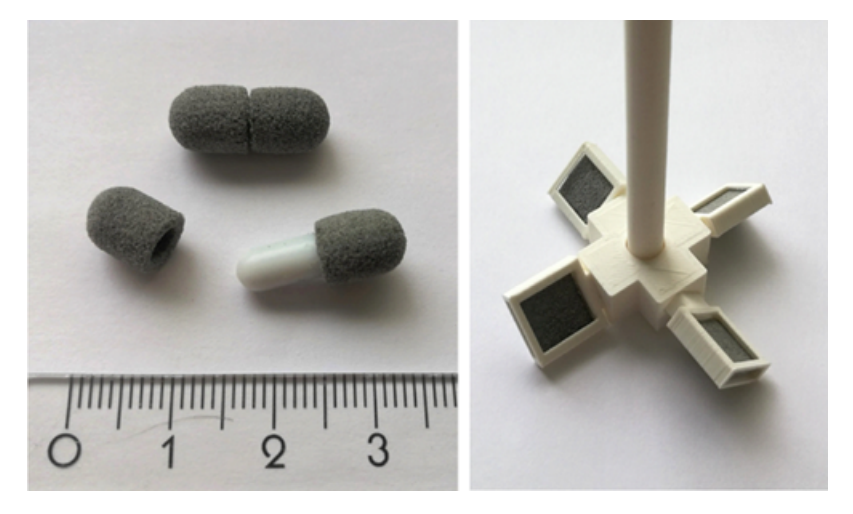
Left: SLS 3D-printed stir bar sleeves (diameter of 6.5 mm and length of 8.5 mm) used in hydrogenation experiments. Right: A concept of an alternative catalysts design for the mechanical stirrer.
“The porosity and the dispersion of SiO2 particles within the 3D-printed objects was also confirmed by using X-ray tomography and SEM−energy-dispersive system (EDS) analysis which further showed the even distribution of the particles,” stated the researchers.
They also noted that the material is ‘fully comparable’ to pure PP plastic, causing no effect at all on thermal properties. X-rays showed peaks of both PP and Pd, and while they were not able to see SiO2, the researchers attributed the absence to its amorphous nature. Good thermal and mechanical properties were noted, along with good resistance to leaching.
“The results also showed that the employed printing process does not have a significant impact on the catalytic performance of the catalytically active additive. Furthermore, SLS sets only minimal requirements for the printing materials, and both the catalytically active component, as well as the supporting matrix, can be altered in almost any fashion imaginable,” concluded the researchers.
“We believe that 3D printing can change the way we produce our catalysts in the future.”
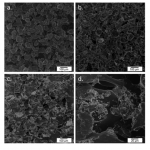
HIM images of the break surface of SLS 3D-printed pure PP (a) and top and break surfaces of SLS 3D-printed stir bar covers (b− d). The Pd/SiO2 catalyst can be seen as pale colored areas with sharp edges in images (b−d)
While SLS 3D printing is one of the most classic forms of 3D printing, it is still one of the most useful and popular, leaving scientists to expend a great deal of research time attempting to refine materials and techniques, from creating bone tissue scaffolds to creating high-performance polymers for use in manufacturing as well as more flexible materials for creative endeavors like making costumes.
What do you think of this news? Let us know your thoughts! Join the discussion of this and other 3D printing topics at 3DPrintBoard.com.
Subscribe to Our Email Newsletter
Stay up-to-date on all the latest news from the 3D printing industry and receive information and offers from third party vendors.
Print Services
Upload your 3D Models and get them printed quickly and efficiently.
You May Also Like
Reinventing Reindustrialization: Why NAVWAR Project Manager Spencer Koroly Invented a Made-in-America 3D Printer
It has become virtually impossible to regularly follow additive manufacturing (AM) industry news and not stumble across the term “defense industrial base” (DIB), a concept encompassing all the many diverse...
Inside The Barnes Global Advisors’ Vision for a Stronger AM Ecosystem
As additive manufacturing (AM) continues to revolutionize the industrial landscape, Pittsburgh-based consultancy The Barnes Global Advisors (TBGA) is helping shape what that future looks like. As the largest independent AM...
Ruggedized: How USMC Innovation Officer Matt Pine Navigates 3D Printing in the Military
Disclaimer: Matt Pine’s views are not the views of the Department of Defense nor the U.S. Marine Corps Throughout this decade thus far, the military’s adoption of additive manufacturing (AM)...
U.S. Congress Calls Out 3D Printing in Proposal for Commercial Reserve Manufacturing Network
Last week, the U.S. House of Representatives’ Appropriations Committee moved the FY 2026 defense bill forward to the House floor. Included in the legislation is a $131 million proposal for...