Finland: Aalto University Researchers Experiment with Paste Extrusion & UV Curing of 3D Printed Biocomposites
Researchers from Aalto University are taking 3D printing of biocomposites one step further, with a new technique combining UV curing and paste extrusion. Outlining their findings in ‘Mechanical Properties of Ultraviolet-Assisted Paste Extrusion and Postextrusion Ultraviolet-Curing of Three-Dimensional Printed Biocomposites,’ the Finnish scientists fill us in on new developments in hybrid manufacturing.
In offering an ‘ecologically advantageous’ alternative, authors Niklas Kretzschmar, Sami Lipponen, Ville Klar, Joshua M. Pearce, Tom L. Ranger, Jukka Seppälä, and Jouni Partanen are able to use novel high filler-ratio pastes to create complex shapes in 3D printing.
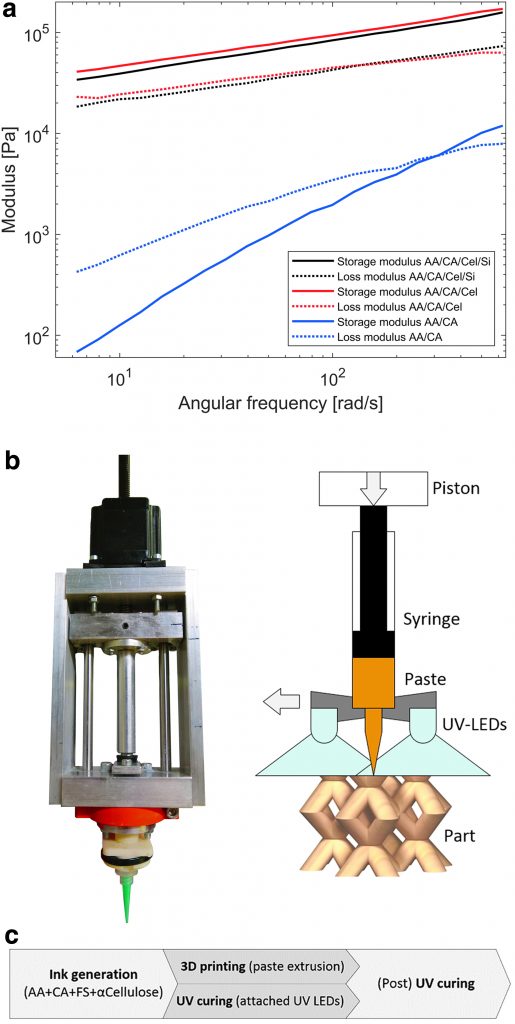
Rheological behavior of tested materials, (b) photograph and scheme of the extruder head equipped with a UV-curing device, (c) printing process of the UV-cured biocomposite. AA, acrylic acid; CA, cellulose acetate; FS, fumed silica; UV, ultraviolet.
This research is centered around a new biocomposite with the prerequisite mechanical properties for creating structures that are stable in structure. Extruded with a customized, on-site 3D printer, the new material is composed of:
- Acrylic acid
- Cellulose acetate
- A-cellulose
- Fumed silica
Photopolymers are widely used today in mainstream 3D printing, but for this study, the researchers wanted to improve on efficiency and complexity in design, generate better support materials, decrease cost, and lessen waste and impact on the environment. While many cellulose derivatives are already in use, the researchers continue to ‘probe the advantages’ of the material while also creating a new biocomposite that relies on a high wood content.
Ten different tensile testing bars were printed, both with and without UV light. They noted that less extrusion was required when using UV light, due to less collapse of layers and stability of shape. Results also showed that samples with UV-curing during the print exhibited substantially greater deformation, in comparison to the samples with UV-curing only afterward.
“Load at break and elongation at break are significantly higher when curing the samples during the print,” noted the researchers.
The team did encounter challenges during this study, but as they pointed out, extrusion with the paste can be difficult—and that had to be considered as they ran into failures:
“Pores and print failures might have led to statistical outliers, and an improved control over the printing process could result in significantly higher mechanical properties. In addition, increased curing durations would probably lead to higher tensile and compression testing values; the ideal curing duration for this material has not yet been investigated…”
They also discovered that UV doses needed to be plentiful enough to cure each layer before the next was deposited, along with finding the correct extrusion speed to decrease porosity issues. Ultimately, the researchers realized more testing would be required with a range of different parameters, along with tensile testing of samples printed vertically—an exercise they found impossible with their current build volume height limits.

(a) Extruding material with UV light, (b) extruding material without UV light and (c) view through a video recording system, (d) 3D scan of a tensile testing sample, (e) printed tensile testing bar when UV-curing after the print, (f) printed tensile testing bar when UV-curing during the print, (g) condensed tensile testing stress-strain curves for UV-curing during and after the print. 3D, three-dimensional.
Finally, future work is needed to explore the potential for higher cellulose contents as well as the addition of special materials such as carbon nanotubes to enhance the properties of the composites,” concluded the researchers. “In addition, further tests with varying key process parameters should be conducted to optimize the mechanical properties of the paste material. Eventually, this UV light assisted printing concept can be scaled up to be used in larger build envelopes with increased nozzle diameters to enable a faster production of large-scale biocomposite components.”
“These results can potentially be transferred to other extrusion materials, leading to new applications and more complex shapes. In particular for large components produced by extrusion of a resin with a low-degree translucency, UV-curing during the print is necessary following the system provided here.”
Bioprinting and associated techniques are of great interest to researchers today as they continue to make impressive strides in so many industries, with a focus on the medical realm. UV curing is common, and scientists, engineers, and a wide range of users continue to experiment with different methods and materials from stretchable elastomers to newly engineered resins or components with shape memory 4D features.
Find out more about UV-assisted paste extrusion here. What do you think of this news? Let us know your thoughts! Join the discussion of this and other 3D printing topics at 3DPrintBoard.com.
[Source / Images: ‘Mechanical Properties of Ultraviolet-Assisted Paste Extrusion and Postextrusion Ultraviolet-Curing of Three-Dimensional Printed Biocomposites’]
Subscribe to Our Email Newsletter
Stay up-to-date on all the latest news from the 3D printing industry and receive information and offers from third party vendors.
Print Services
Upload your 3D Models and get them printed quickly and efficiently.
You May Also Like
Reinventing Reindustrialization: Why NAVWAR Project Manager Spencer Koroly Invented a Made-in-America 3D Printer
It has become virtually impossible to regularly follow additive manufacturing (AM) industry news and not stumble across the term “defense industrial base” (DIB), a concept encompassing all the many diverse...
Inside The Barnes Global Advisors’ Vision for a Stronger AM Ecosystem
As additive manufacturing (AM) continues to revolutionize the industrial landscape, Pittsburgh-based consultancy The Barnes Global Advisors (TBGA) is helping shape what that future looks like. As the largest independent AM...
Ruggedized: How USMC Innovation Officer Matt Pine Navigates 3D Printing in the Military
Disclaimer: Matt Pine’s views are not the views of the Department of Defense nor the U.S. Marine Corps Throughout this decade thus far, the military’s adoption of additive manufacturing (AM)...
U.S. Congress Calls Out 3D Printing in Proposal for Commercial Reserve Manufacturing Network
Last week, the U.S. House of Representatives’ Appropriations Committee moved the FY 2026 defense bill forward to the House floor. Included in the legislation is a $131 million proposal for...