In ‘Digital Design, Analysis and 3D Printing of Prosthesis Scaffolds for Mandibular Reconstruction,’ we learn more about strides in the medical field regarding mandibular surgeries, reconstruction, the potential for current and future improvements in implants, as well as understanding more about the obstacles today and how they can be overcome.
3D printing is invaluable to the medical field overall due to the ability to customize nearly everything—and offer patient-specific care to individuals who may have faltered under previous one-size-fits-all restrictions. Customized implants especially are offering new options to patients, as porous, lightweight structures can be created to aid in reconstruction and the eventual return to normal functions such as chewing and swallowing nutrients. For this study, Saudi researchers from King Saud University created two different customized scaffold designs (a top and bottom plate, and an inner porous plate) which they later evaluated regarding both usefulness and aesthetic appearance.
The authors describe the perfect scaffold as one that is highly porous, without cracks, and fully biocompatible. Previous studies have shown that titanium is highly effective as a material but may also lead to deterioration of mechanical properties and eventual resorption or failure of the implant. 3D printing has offered potential in reconstruction, but also rehabilitation, and surgery too.
“Among several 3D printing techniques, electron beam melting (EBM) has been regarded as the fast and successful method for the fabrication of titanium medical implants from computer-aided design (CAD) models with Food and Drug Administration (FDA) and Conformité Européene (CE) approval,” stated the researchers.
Until now, the researchers state that there has been no clear research regarding mandibular reconstruction or biomechanical properties, stability and integrity, or testing of related scaffolds and structures. Here, they studied a patient, at 40 years old, suffering from deformities and a ‘lesion in the left mandibular area.’ The patient was treated in an emergency department initially, beginning with a series of CT scans uncovering a mandibular continuity defect, and substantial loss of bone.
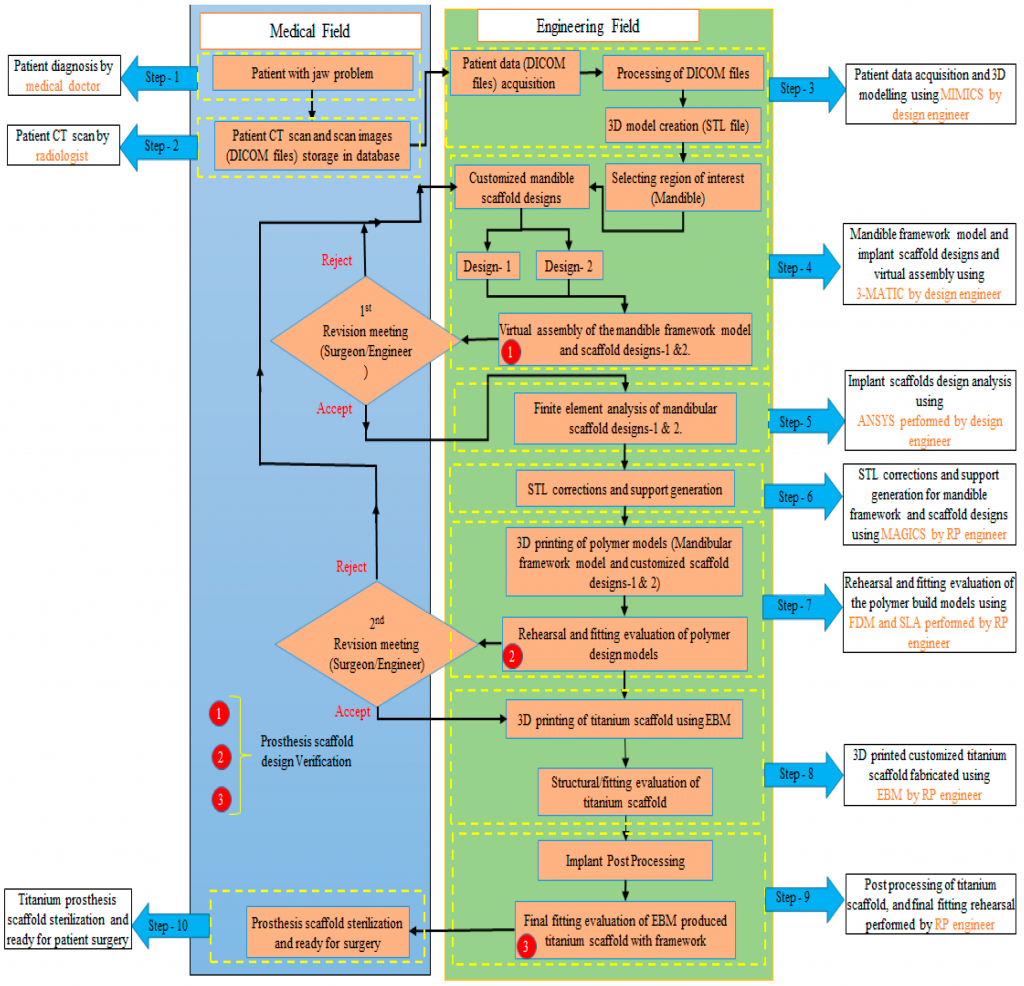
The proposed methodology for design, analysis and fabrication of customized mandibular prosthesis scaffolds. Note: The red circles indicate the formal meetings between the engineering and medical department for scaffold design verification and evaluation.
The images were converted into 3D files using Materialise Mimics software, and then an FDM 3D printer was used with ABS material to create the framework model. A Formlabs 2 SLA 3D printer was then used for fabrication of the mandibular prosthesis scaffold. The researchers evaluated the structures for weight, integrity, and accuracy, using a micro-CT scan.
“Eventually, depending on the FEA, weight analysis and fitting accuracy evaluation, it can be inferred that the scaffold with the top and bottom porous plate is more favorable for bone reconstruction as compared to scaffold with the inner porous implant and can successfully be employed in the reconstruction of the defective mandible. Indeed, it can be asserted that the employment of prosthesis scaffolds in mandibular reconstruction satisfies the sustained need of lighter implants with accurate fitting and lesser surgical time and minimal revisions,” concluded the researchers.
“It is mandatory that the research in this area should continue in the future for acquiring further innovative implant designs and reconstruction methods. The authors would like to expand this work by introducing new designs with different porous structures and analyzing them for their strength and accuracy in mandible restoration. In addition, the authors would like to extend this work by including an extensive clinical (in-vivo) study in the future.”
Mandibular reconstruction can be a challenging endeavor, but when successful it offers incredible value to patients who may be having trouble chewing, as well as enduring understandable self-consciousness due to a defect or tumor removal.
This is big topic of research and has also led to numerous innovations via 3D printing, from alveolar ridge augmentation to mandibular grafts, and implants for cancer patients. What do you think of this news? Let us know your thoughts! Join the discussion of this and other 3D printing topics at 3DPrintBoard.com.
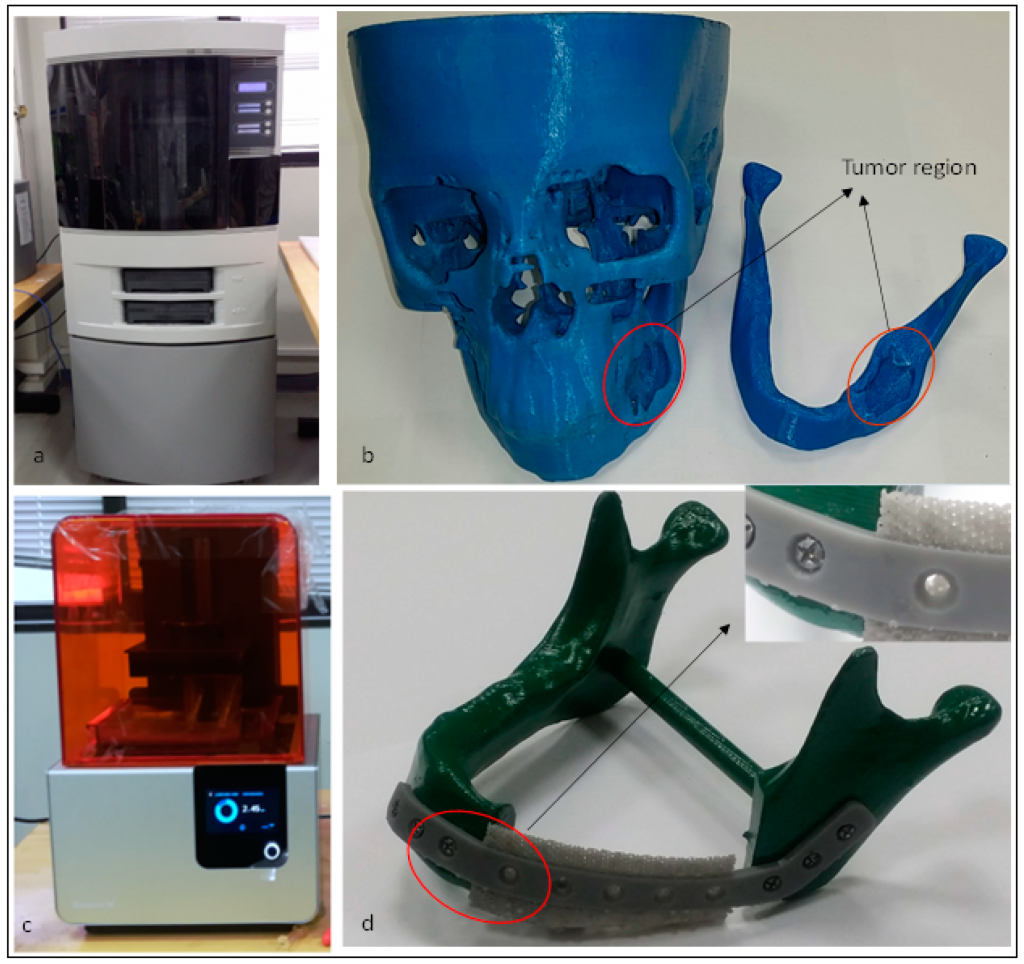
(a) Fused Deposition Modeling machine with its fabricated polymer model (b) indicating the tumor region and (c) SLA machine and its produced mandibular scaffold (d) with a close-up view.
Subscribe to Our Email Newsletter
Stay up-to-date on all the latest news from the 3D printing industry and receive information and offers from third party vendors.
Print Services
Upload your 3D Models and get them printed quickly and efficiently.
You May Also Like
Reinventing Reindustrialization: Why NAVWAR Project Manager Spencer Koroly Invented a Made-in-America 3D Printer
It has become virtually impossible to regularly follow additive manufacturing (AM) industry news and not stumble across the term “defense industrial base” (DIB), a concept encompassing all the many diverse...
Inside The Barnes Global Advisors’ Vision for a Stronger AM Ecosystem
As additive manufacturing (AM) continues to revolutionize the industrial landscape, Pittsburgh-based consultancy The Barnes Global Advisors (TBGA) is helping shape what that future looks like. As the largest independent AM...
Ruggedized: How USMC Innovation Officer Matt Pine Navigates 3D Printing in the Military
Disclaimer: Matt Pine’s views are not the views of the Department of Defense nor the U.S. Marine Corps Throughout this decade thus far, the military’s adoption of additive manufacturing (AM)...
U.S. Congress Calls Out 3D Printing in Proposal for Commercial Reserve Manufacturing Network
Last week, the U.S. House of Representatives’ Appropriations Committee moved the FY 2026 defense bill forward to the House floor. Included in the legislation is a $131 million proposal for...