UK researchers continue to explore the benefits of creating new composites for 3D printing. Here, they discuss their findings regarding carbon composites used in SLA 3D printing and material extrusion, outlined in their recently published paper, ‘Fabrication of the continuous carbon fiber reinforced plastic composites by additive manufacturing.’
As authors Y. Lu, G.K. Poh, A. Gleadall, L.G. Zhao, and X. Han explain, composites are often created due to a need for stronger mechanical properties in 3D printed and additive manufactured parts. Carbon is a material relied on especially in applications like the automobile industry and aerospace because of incredible strength, but also the potential for making lightweight parts that may not have been possible previously.
The authors point out that while carbon fiber is useful for strengthening mechanical properties, it often still displays limited strength in tensile testing. This is due to a lack of control over short fibers, resulting in more unpredictable orientation and alignment during 3D printing. Beyond that, inferior bonding of the composite fibers and the matrix may also cause a lack of integrity in structures. In testing, the researchers used continuous-fiber-reinforced composites (CFRCs) in material extrusion and SLA processes.
Testing was performed through physical evaluation of the mechanical properties, along with examination by microscope. Samples were created specifically for tensile testing, with Accura60 resin used for SLA 3D printing (with carbon fiber filament obtained from Markforged) and nylon and carbon fiber filament, also supplied by Markforged, used for material extrusion on a MarkTwo 3D printer. Tensile tests were then completed on an Instron 3369 machine with a 50 kN load cell, and then analyzed further through a Primotech microscope, with the fiber-matrix interface examined via a Hitachi TM3030 Tabletop scanning electron microscope.
“The increase of elastic modulus after embedding carbon fiber is 110.49% and 23.69% for ME and SLA based composite samples, respectively. Compared with theoretical result, experimental results demonstrated a 73.3% lower tensile modulus for ME samples and a 42.06% lower tensile modulus for SLA samples,” reported the authors. “The microscopic analysis suggested a presence of porosity at the fibre-matrix interface of the composite specimens produced by both SLA and ME while SLA samples have a less percentage of porosity.”
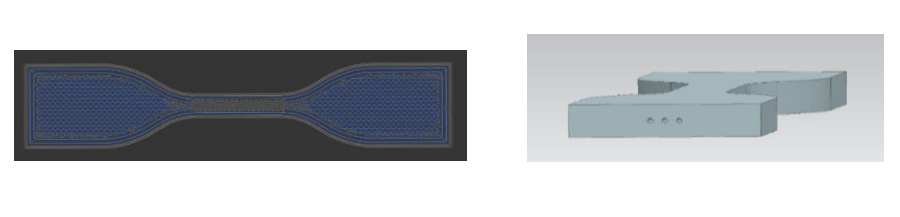
(a) 2D plane view of fibre distribution of ME-C sample; (b) Cross Section view of SLA-C matrix sample
While the elastic modulus was increased substantially with carbon fiber, the authors pointed out that it also significantly reduced elongation at break, due to a lower elongation-to-break—in comparison to the use of all nylon material. Because of this, the sample was brittle. They also noticed high porosity due to voids in the fiber/matrix layers—leading to decreased mechanical performance. It was noted that this could be due to inferior infill density, with printed fibers not being even distributed during 3D printing—leading to ‘compromised’ tensile properties.
“Compared with theoretical result, experimental results demonstrated a 73.3% lower tensile modulus for ME samples and a 42.06% lower tensile modulus for SLA samples. The microscopic analysis suggested a presence of porosity at the fibre-matrix interface of the composite specimens produced by both SLA and ME while SLA samples have a less percentage of porosity,” stated the researchers.
“Compared to commercially available composite ME based machine, SLA technology showed promising results for composite manufacturing, and further investigation is ongoing,” concluded the researchers.
One of the most fascinating parts of 3D printing is not only the innovations that spring forth from the technology continually, but also the ongoing refinements in machines and materials. And while one type of plastic or metal may be suitable for a range of applications, users often find that by adding another material or element, they can strengthen or stabilize parts further, whether in using metals like titanium or a mixture of graphene and alginate, or recycling wood into 3D printed composites. What do you think of this news? Let us know your thoughts! Join the discussion of this and other 3D printing topics at 3DPrintBoard.com.
[Source / Images: ‘Fabrication of the continuous carbon fiber reinforced plastic composites by additive manufacturing’]Subscribe to Our Email Newsletter
Stay up-to-date on all the latest news from the 3D printing industry and receive information and offers from third party vendors.
Print Services
Upload your 3D Models and get them printed quickly and efficiently.
You May Also Like
Making 3D Printing Personal: How Faraz Faruqi Is Rethinking Digital Design at MIT CSAIL
What if your 3D printer could think more like an intelligent assistant, able to reason through a design idea, ask questions, and deliver something that works exactly the way the...
Reinventing Reindustrialization: Why NAVWAR Project Manager Spencer Koroly Invented a Made-in-America 3D Printer
It has become virtually impossible to regularly follow additive manufacturing (AM) industry news and not stumble across the term “defense industrial base” (DIB), a concept encompassing all the many diverse...
Heating Up: 3D Systems’ Scott Green Discusses 3D Printing’s Potential in the Data Center Industry
The relentless rise of NVIDIA, the steadily increasing pledges of major private and public investments in national infrastructure projects around the world, and the general cultural obsession with AI have...
Formlabs Teams Up with DMG MORI in Japan
In late June, Nick Graham, Chief Revenue Officer at Formlabs, announced on LinkedIn that the company had partnered with DMG MORI, one of the world’s leading machine tool companies, to...