As 3D printing continues to infiltrate the mainstream, captivating new enthusiasts around the world daily, it is obvious that the potential for innovation is almost infinite. In tandem though, the ability to create new software, hardware, materials, and processes is also following suit. Researchers in Singapore recently detailed their findings regarding new fabrication techniques in ‘3D printed fittings and fluidic modules for customizable droplet generators.’
Sindhu Vijayan and Michinao Hashimoto of Singapore University of Technology and Design embarked on a project to create customized droplets in 3D printing, furthering high-tech fabrication processes in both the chemical and biological sciences, to include:
- Analytical chemistry
- Food chemistry
- Biological assays
- Drug delivery
- Imaging
- Materials synthesis
During this foray into production of droplet microfluidics, the team used fittings that were 3D printed with commercially made needles and tubes. In recent years, droplet generators have been made through soft lithography, 3D printing, or basic, low-cost assembly of fluidic units. Historically, each process has had its challenges; today, however, the main obstacle lies in creating droplet generators that offer versatility in size and complexity of emulsions.
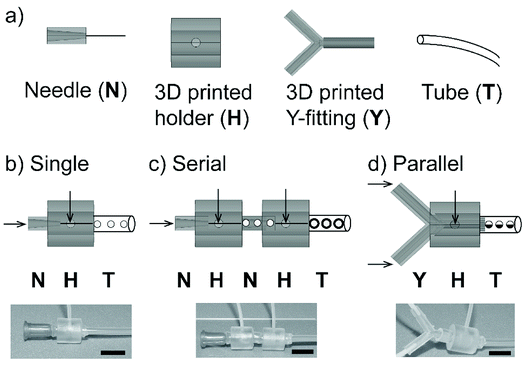
(a) Modules used for the fabrication of microfluidic axisymmetric flow-focusing device: needle (N), 3D printed holder (H), 3D printed Y-fitting (Y) and tube (T). Schematics and optical images of (b) a single flow-focusing device formed by co-axial arrangement of the 3D printed connector and a needle, (c) serially connected, two flow-focusing devices to produce double emulsions, and (d) a flow-focusing device with a parallel laminar flow to produce compartmented particles. Scale bar = 10 mm.
Vijayan and Hashimoto used 3D printed nodules and parts with a smaller dimension as they made axisymmetric droplet generators. This allowed for more spacious microchannels and better fluidic connections—all in a plug and play device—resulting in high-performance emulsions. Stability in droplet production occurred through their new method, which is simpler, creates better resolution in channels, and customization.
Production was easier for the researchers due to their new modular approach:
“Rigid fittings fabricated by 3D printing was readily assembled with other modules, while the elasticity of the tube naturally provided conformal contact to avoid leakage of the fluids,” stated the researchers. “Other than connecting different modules together, no additional procedure was involved to make the flow-focusing device. The 3D printed fitting was designed with large hollow spaces so that resin clogging should not occur, unlike fully 3D printed devices with embedded microchannels.”
The team used AutoCAD for designing the high-performance fittings, 3D printed on a Form 2 using Formlabs Clear resin. For post-processing, they created an isopropanol wash for eliminating leftover resin. They also achieved better resolution by using standard needles, specifically those with smaller internal diameters than the channel widths.
Customization features also included ease in using multiple devices as well as other 3D printed fittings, like Y channels. They were also able to change the size of droplets just by alternating needles. Modules allowed for a variety of different emulsions with two generations manipulating flow and creating double generation. Janus particles (colloidal particles ranging in surface chemistry and size) were also created via a laminar flow with two different fluids.
“The method of fabrication we developed offers several characteristics that would complement existing methods to fabricate flow-focusing generators. We took an advantage of well-defined, small size of features that the standardized materials (i.e. needles and tubes) offered, which were not achievable in desktop 3D printers. 3D printed fitting added the route to design the configuration of the multiphase flows (i.e. concentric and co-laminar) to achieve generation of intended emulsions. As the fabrication can be done in a simple plug-and-play manner, we believe that the method we developed in this work benefits non-experts to perform generation of emulsions using microfluidic devices for various applications,” concluded the researchers.
What do you think of this news? Let us know your thoughts! Join the discussion of this and other 3D printing topics at 3DPrintBoard.com.
[Source / Images: 3D printed fittings and fluidic modules for customizable droplet generators]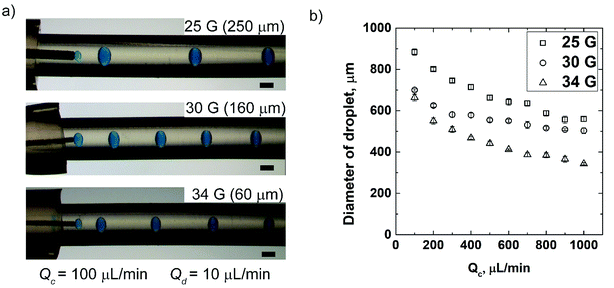
(a) Optical micrographs showing the controlled generation of W/O emulsions using three different dispensing needles of varying IDs. (b) A plot showing the diameter of droplets obtained for three different dispensing needles against varying Qc at Qd = 10 μL min−1. The dispersed phase was 1% v/v blue dye in water, and the continuous phase was 2% v/v Span 80 in hexadecane. Scale bar = 600 μm.
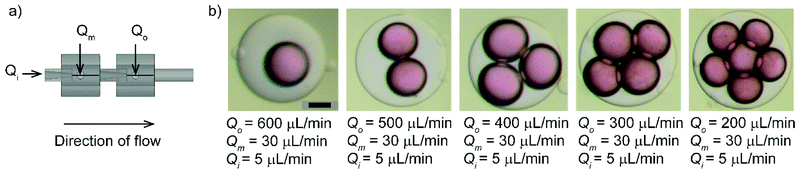
(a) A schematic illustration of serially connected flow-focusing devices for producing double emulsions. (b) Optical micrographs of produced W/O/W double emulsions with varying numbers of inner droplets obtained for a range of Qo with Qm = 30 μL min−1 and Qi = 5 μL min−1. The inner, middle and outer phases were 0.25% v/v red dye in water, 3% v/v Span 80 in hexadecane and 0.1% v/v yellow dye in 90% glycerol in water solution. Scale bar = 600 μm.
Subscribe to Our Email Newsletter
Stay up-to-date on all the latest news from the 3D printing industry and receive information and offers from third party vendors.
You May Also Like
3D Printing Financials: Protolabs’ Q1 3D Printing Revenue is Flat, Company Advances in Technology Push
Protolabs (NYSE: PRLB) has kicked off 2024 with a mild boost in revenue, revealing how the Minnesota-based company manages to adapt and thrive even in uncertain market conditions. While the...
NASA Backs Project for 3D Printing Space Sensors
NASA granted $300,000 to Florida State University (FSU) and Florida Agricultural and Mechanical University (FAMU) to pioneer a project using 3D printing to develop cutting-edge sensors capable of withstanding the...
Further Understanding of 3D Printing Design at ADDITIV Design World
ADDITIV is back once again! This time, the virtual platform for additive manufacturing will be holding the first-ever edition of ADDITIV Design World on May 23rd from 9:00 AM –...
Daring AM: Rocket Lab Shoots for the Stars, Astrobotic Wants to 3D Print on the Moon
Once again, space exploration teams up with the 3D printing industry, launching projects that could change how we explore space. Pioneering space manufacturer Rocket Lab (Nasdaq: RKLB) secured a $14.49...