Matthias Schmidt-Lehr of Ampower is a 3D printing consultant with deep experience in manufacturing for 3D printing. He’s worked for technology development institute Laser Zentrum Nord (Fraunhofer IAPT), its manufacturing spinoff Bionic Production and has been involved with a number of notable projects in industrializing manufacturing for 3D printing. Together with his colleagues, he does strategy, training, part qualification and research on 3D printing for Ampower. Ampower a Hamburg based metal 3D printing focused consultancy firm with deep experience with some of the leading companies using metal 3D printing to manufacture. Ampower has been positioning itself as the team that gives you analysis based on real metal 3D printing experience in manufacturing. We interviewed Matthias to find out his vision on what is happening in 3D printing and what is holding the market back.
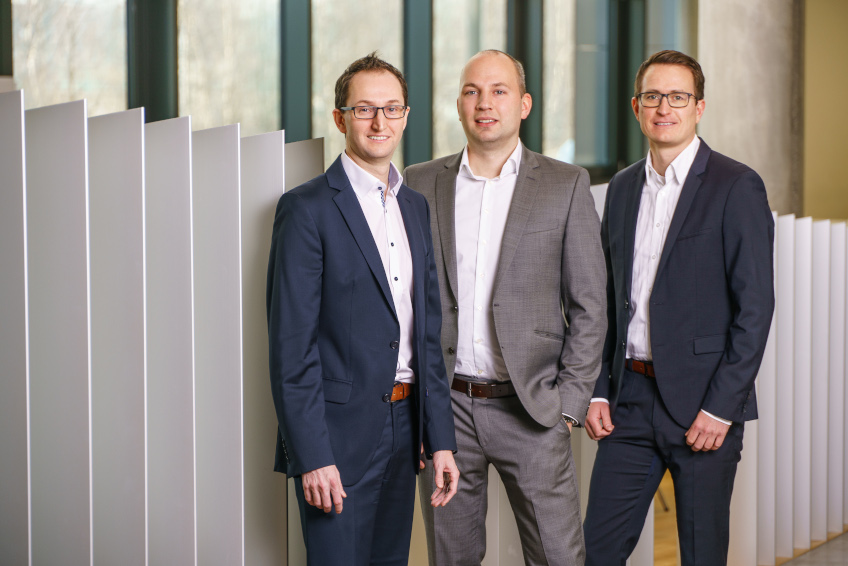
Dr. Maximilian Munsch, Matthias Schmidt-Lehr and Dr. Eric Wycisk
What is Ampower?
Ampower is the leading consultancy for Metal Additive Manufacturing. We are supporting SMEs as well as large cooperations on their way of adapting industrial Additive Manufacturing in the fields of corporate strategy and operational excellence.
Why should I work with you?
Our experts have more than 10 years of experience in industrial Additive Manufacturing applications. Our reference customers are leading market players like Trumpf, HP and Oerlikon as well as major industry OEMs such as Volkswagen or Airbus.
What kind of customers do you have?
Our customers include companies along the entire Additive Manufacturing supply chain from powder and system manufacturers to end users. Strongly represented industries are currently automotive, aviation and medical.
What are some of the major things holding back 3D printing?
Cost competitiveness is a major challenge that has to be tackled to create business opportunities. Also, industrial 3D Printing is still a niche technology and the lack of knowledge and experience leads to slow adaption rates.
If I am a company wanting to use 3D printing, what advice do you have for me?
Always start by building up knowledge and experience with first applications. Some successful AM players went through at least 2 years of learning before the first rollout of products. Secondly, team up with strong partners. Many of the obstacles on the road to success have been dealt with already and cooperation leads to a significantly accelerated adaption curve.
What about if I wanted to industrialize 3D printing for manufacturing?
Industrialization means that experimentation is over. Quality management, procurement, production and job floor planning have to be included into the team as well as personnel qualification becomes very important. Quality has to be priority No 1. Part failures due to lack of qualification efforts will lead to severe disappointment of internal and external stakeholders, especially with such a new technology.
What are some of the most exciting developments in 3D printing right now?
Emerging technologies with higher productivity and lower cost like HP MJF technology or the next level of Binder Jetting technologies are exciting to observe. At the same time, the amount of innovations is making it difficult for users to define and follow up with the right technology strategy. Over the years to come, we will see a further and steady increase in productivity. More 3D printed end user applications will become viable and will lead to overall significant growth of the technology.
What is the Additive Manufacturing market like in Germany?
In Germany, industrial Additive Manufacturing has a comparatively high market penetration. Of course, it is still overall a niche technology. But in many industries, German companies cannot compete as cost leader on a global market. They have to differentiate their products and services. Additive Manufacturing fits this business strategy and can help to provide new applications with added value.
Do you think that desktop 3D printers will be used to manufacture?
In certain applications with high degree of individualization, low volumes and low quantities, this is already the case. A good example are industrial drone manufacturers. User-customized components are manufactured overnight using desktop 3D printers and shipped the next day. As soon as high manufacturing volumes are required, cost effectiveness due to economies of scale will make desktop 3D printing less likely. Additionally, demanding industries require a qualified production in an industrial manufacturing environment.
What are some emerging applications in 3D printing that you are the most excited about?
In terms of industrial applications, I am still fascinated by just in time individual medical products. The fact that endoprosthesis for bone replacement, dental implants and hearing aids are now tailored to customers within a very short manufacturing time, is just the starting point of a more and more customized world we will live in.
A lot of people are excited about binder jetting metals and MIM FDM but I see a lot of issues with shrinkage and deformation, you?
The sintering process remains the major challenge. Due to these issues, the mature MIM and PIM industry has restrictions in design and limits in size for sintering metal parts. Some players in binder jetting, such as Markforged and Desktop Metal, decided to develop their own debinding and sintering processes. While certainly risky, this route might lead to disruption and improvement of the sintering process. In any case, users who adapt those technologies should look into conventional sintering to gather experience.
Do you think that DMLS will continue to dominate orthopedics and aviation? Or will other technologies replace it?
Sinter technologies are now at the stage DMLS or laser powder bed fusion as we say, was 10 years ago. In short term, high investments in hardware, knowledge and established processes will prevent a fast substitution of laser powder bed fusion with other suitable new technologies. In the long run, sinter technologies will certainly cover applications in aviation and medical, if they prove to be better suited and more cost effective.
What about EB PBF?
Especially in medical and aviation, electron beam powder bed fusion is very successfully used for production of titanium alloys. However, the technology struggles with the dominant patent situation of the market leader and, consequently, lack of competition. Sole source generally hinders innovation and a broad adoption of a manufacturing technology. Once major patents expire, competitiveness in the EB-PBF market will certainly increase. In the meantime, other technologies progress fast due to the competition and make huge steps in an open environment.
What do you think of the prospects of the DED technologies?
Direct energy deposition technologies lack the enormous hype that LB-PBF and other 3D Printing technologies experienced. We notice a steady growth rate with little disappointments. DED technologies will revolutionize the casting, tooling and forging markets. However, we are still talking about a niche technology that will only be successful for demanding applications. We hope that some of the currently upcoming and very promising proprietary DED technologies will be open some day to enable disruptions in this field and prevent the same situation that EB-PBF is currently in.
How close are we to seeing 3D printing used at scale in automotive?
Still very far away! The productivity level of high-volume throughput technologies such as sheet metal forming, casting, forging or injection molding is on a completely different scale. The added value of 3D Printing to a component will not be enough to achieve cost competitiveness for large batch sizes. A game changer, however, can be the increased need for customization and even faster innovation cycles that will make conventional tool bound manufacturing more expensive than tool free production. We expect first applications in annual volumes above 100.000 in 10-15 years.
What polymer materials are you most excited about?
We see major industrial applications of polyamide materials by HP and EOS. The market entry of HP certainly had a huge impact and ends the lonely market leadership of EOS in this field. This development will bring new drive to the polymer material map. However, as long as we have no replacement for glass fiber reinforced polymers a wide adoption is still not to be expected.
Are there any emerging metals that you are excited about?
Lately, we have seen promising developments of copper processes with satisfyingly high process stability. The copper market is very interesting since it covers a great number of complex and high value applications which are suitable for Additive Manufacturing.
How do I start making qualified 3D printed parts?
A certain background knowledge is helpful, of course. First of all, you should start to think additive. This means you design the part with material only where it is needed. Topology optimization can help here. This way, you will reduce costs and generate a business case. Secondly, you have to understand your Additive Manufacturing process. It is the same as with any other manufacturing technology. The more you know about the specific process, the better the design will be. Finally, you need to produce the part on a qualified system and validate all manufacturing processes. But that’s where we start to get into detail.
How does your cost calculation tool work?
The cost calculation tool we put on our homepage is rather simple but gives good estimates of manufacturing cost for some LB and EB-PBF alloys. Since part complexity is almost for free in Additive Manufacturing, the tool is mostly driven by the total manufacturing volume. After entering volume, parts per batch and alloy, the tool calculates part cost range for low and high build jobs. For a more sophisticated tool, it is of course important to understand all cost factors that we describe in our make or buy study.
Why is it that when you ask a client to select a part for 3D printing that they always pick the wrong one?
First and foremost, lack of experience. And secondly, we tend to choose parts that we want to simply “replace” by 3D printed parts. This will usually not work. The best business cases evolve when designing a new assembly and having 3D Printing in mind – thinking additive.
Subscribe to Our Email Newsletter
Stay up-to-date on all the latest news from the 3D printing industry and receive information and offers from third party vendors.
Print Services
Upload your 3D Models and get them printed quickly and efficiently.
You May Also Like
3D Printing News Briefs, July 2, 2025: Copper Alloys, Defense Manufacturing, & More
We’re starting off with metals in today’s 3D Printing News Briefs, as Farsoon has unveiled a large-scale AM solution for copper alloys, and Meltio used its wire-laser metal solution to...
3DPOD 260: John Hart on VulcanForms, MIT, Desktop Metal and More
John Hart is a Professor at MIT; he´s also the director of the Laboratory for Manufacturing and Productivity as well as the director of the Center for Advanced Production Technologies....
3D Printing News Briefs, June 28, 2025: Defense Accelerator, Surgical Models, & More
In this weekend’s 3D Printing News Briefs, 3YOURMIND was selected to join an EU Defense Accelerator, and PTC has announced model-based definition (MBD) capabilities within Onshape. Finally, a study out...
EOS in India: AM’s Rising Star
EOS is doubling down on India. With a growing base of aerospace startups, new government policies, and a massive engineering workforce, India is quickly becoming one of the most important...