I’ve known Patrik Ohldin for a long time as a supremely knowledgeable metal printing guy. He’s been working in metal 3D printing for over 14 years, 12 of those as an Area Sales Manager for Swedish EBM metal printing company and now GE subsidiary Arcam. He really knows a tonne about EBM and electron beam powder bed fusion technologies. He is also a stand-up guy that knows how to explain, educate and understand business cases in a wide array of areas. Patrik was instrumental in introducing EBM to new areas such as aerospace and orthopedic implants and helped many firms industrialize metal 3D printing. After more than 12 years of selling EBM machines worldwide and being a key player in EBM’s conquest of foreign markets, Patrik co-founded open source electron beam powder bed fusion company Freemelt.
I was flabbergasted. With a war for talent going on for experienced metal 3D printing salespeople (a complex subject that you can’t really learn from a course or book at the moment no matter how much time you have), Patrik didn’t end up joining one of the multi-million dollar VC funded metal printing firms. Experienced metal printing sales are worth their weight in titanium powder (at 2008 prices) and along with application development engineers for powder bed the most sought-after people in 3D printing. I figured he was going to lean back with a big paycheck and equity somewhere. Instead, he wanted to make an open source electron beam powder bed fusion machine. As far as challenges go this was a stupidly complex one to want to undertake. I can not stress enough just how insanely challenging and complicated such a challenge is. Metal printing is a step change more complex than industrial polymer powder bed fusion. The investments, skills, and difficulty would more than eclipse just about any startup out there. Additionally, they were trying to do a 30 million startup on a shoestring. Patrik was a very experienced and very smart man and he surrounded himself with a supremely experienced metal printing team. I was also almost certain that he would fail. Resigned that he would become some kind of quixotic Don Quixote of metal printing I thought I’d at least get a good anecdote out of knowing him. Surprisingly though Freemelt was able to make an open source metal printing platform and what’s more, it started to have traction as well. People kept coming to me saying that they were evaluating their platform and technology. People were excited by Freemelt’s goals to make new alloys for 3D printing possible. Manufacturers liked the fact that there was no lock-in and they had access to all of the technology. Powder metallurgy companies were excited about being able to control and account for all of the variables and use this as a platform to develop materials. The Freemelt ecosystem was growing and the technology was actually viable. Blown away, and sheepishly feeling a bit apologetic, I decided that it was time to interview Patrik about Freemelt.
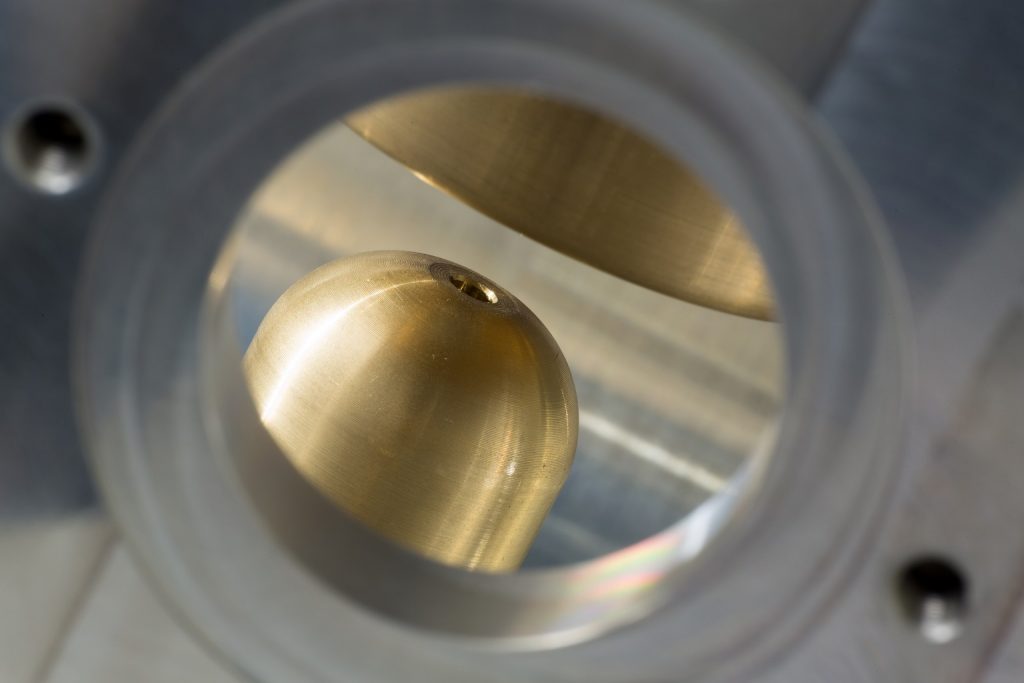
Freemelt’s Electron Beam Gun.
What is Freemelt?
We provide the world’s first open source electron beam powder bed fusion (E-PBF) metal 3D printer, designed for materials R&D. The metal 3D printing industry’s growth has been tremendous, but its dirty little secret is that only a small number of materials are actually available to use. We are convinced that metal 3D printing’s future lies in (more) materials, and that this is what will drive new applications and sustained growth. But to develop new materials for metal 3D printing as quickly as possible you need many heads and hands with full access to the appropriate tools. We have therefore created Freemelt ONE, an open source development toolbox that gives you complete control of beam paths and hardware, lets you make tests with small amounts of powder, build in vacuum at high process temperatures and attach auxiliary equipment for in-situ process monitoring.
How can I contribute or work with you?
We encourage all types of cooperation since we believe that collaboration is the way forward for metal 3D printing. The most straightforward way to contribute is of course to actually use Freemelt ONE to develop new materials for metal 3D printing. The fact that Freemelt ONE is open source also makes it possible for 3rdparty suppliers of software and hardware to interact with it. Our vision is the creation of a roadmap for metal 3D printing, with well-defined goals and roles that allow the participating companies and institutions to focus on their core competences, thereby moving the whole industry forward.
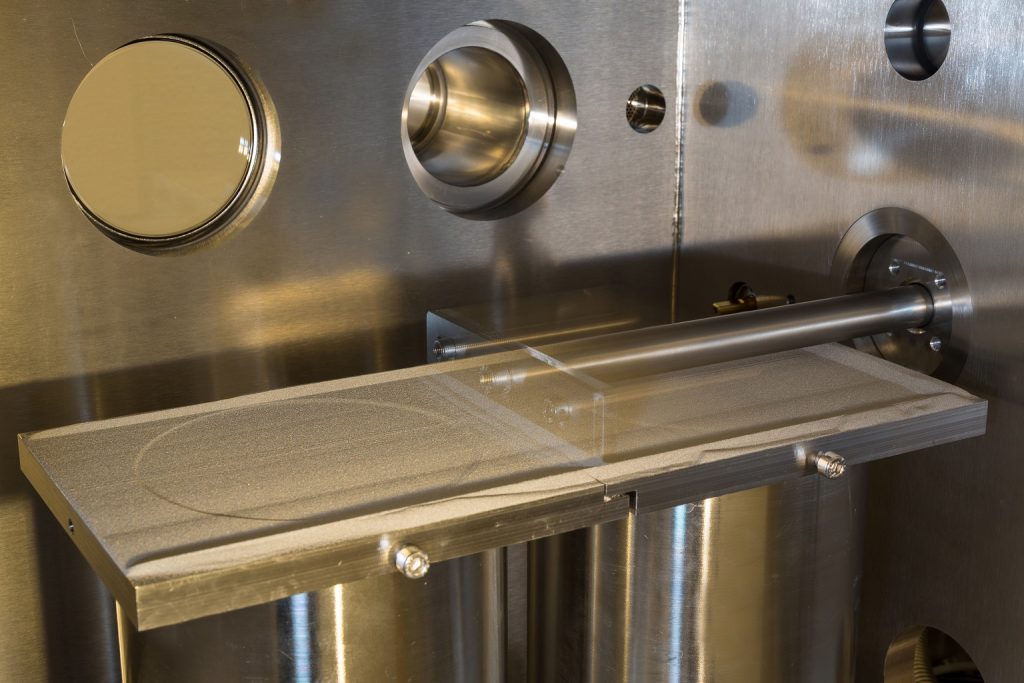
The powder distribution of the Freemelt One E-PBF 3D printer.
What kind of companies do you wish to work with?
We wish to work with companies and institutions that are interested in developing new powders, new materials and new processing algorithms for metal 3D printing. Universities and research institutes will most likely make up the lion’s share of our customers, but we also see that corporate research centers and powder manufacturers want to use Freemelt ONE to perform their own materials research.
What has changed in 3D printing since you’ve been involved with it?
I would say that the most important change is the industry’s focus on production applications. Major suppliers of CAD software and metal powders have established themselves in metal 3D printing, often via acquisitions. Large industrial corporations develop products to be manufactured with 3D printing and make major investments in their own production capacity. It is also noteworthy that the number of 3rd party suppliers of software and hardware for pre- and post-processing keeps increasing.
What advice would you give to an industrial company that wants to use 3D printing to manufacture?
That it doesn’t make sense to just try to produce existing products with metal 3D printing. The way to go is to use the technology to add product value, for example by redesigning the products to make them easier to produce or to give them increased functionality. The ability to produce parts in new advanced materials, including materials tailored for metal 3D printing with completely new chemical compositions, further increases the likelihood of success.
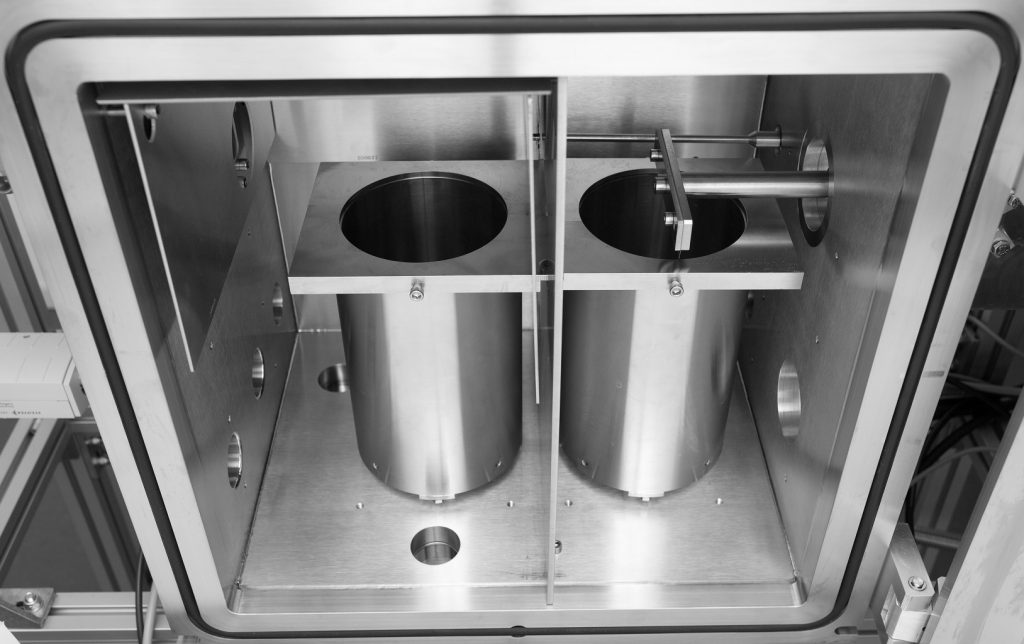
The Vacuum Chamber of the Freemelt System.
What are the advantages of E-PBF when compared to laser powder bed fusion (L-PBF)?
I would say that E-PBF’s main advantages are the high output power (currently up to 6 kW) that gives high productivity and enables high process temperatures (>1.000 ˚C), and the extremely clean process environment (equivalent to the parts per billion range for oxygen) that the high vacuum provides. Hot processing has proven successful to eliminate internal stresses and deformation of built parts, and also helps prevent crack formation. Furthermore, the electron beam’s high translation speed gives you excellent process temperature control and an unrivaled opportunity to tailor microstructures and material properties. It has for example been demonstrated that single crystal materials can be made with E-PBF. Yet another potential of E-PBF is the multitude of process monitoring technologies that require high vacuum to work. I am convinced that we will see new advanced solutions for E-PBF process monitoring in the future.
Do you see a less expensive generation of E-PBF machines emerging?
As the metal 3D printing industry matures and more companies enter the arena it will undoubtedly lead to increasing price pressure and demand for less expensive machines, both for E-PBF and L-PBF. But ultimately it is the cost and value of the produced parts that drive the decision to invest in and manufacture with metal 3D printing.
Can we do gradient materials with E-PBF? What’s so exciting about that?
Gradient materials are exciting because sometimes it is advantageous to have different material properties in the same part. One such example is turbine blades, where you want different mechanical properties at the root and at the tip. Gradient materials have been attempted with powder bed fusion by gradually mixing different metal powders as the build progresses. Meanwhile, with E-PBF it is possible to obtain gradient material properties with only one metal powder, by using the technology’s precise beam and temperature control to create different microstructures within one single component.
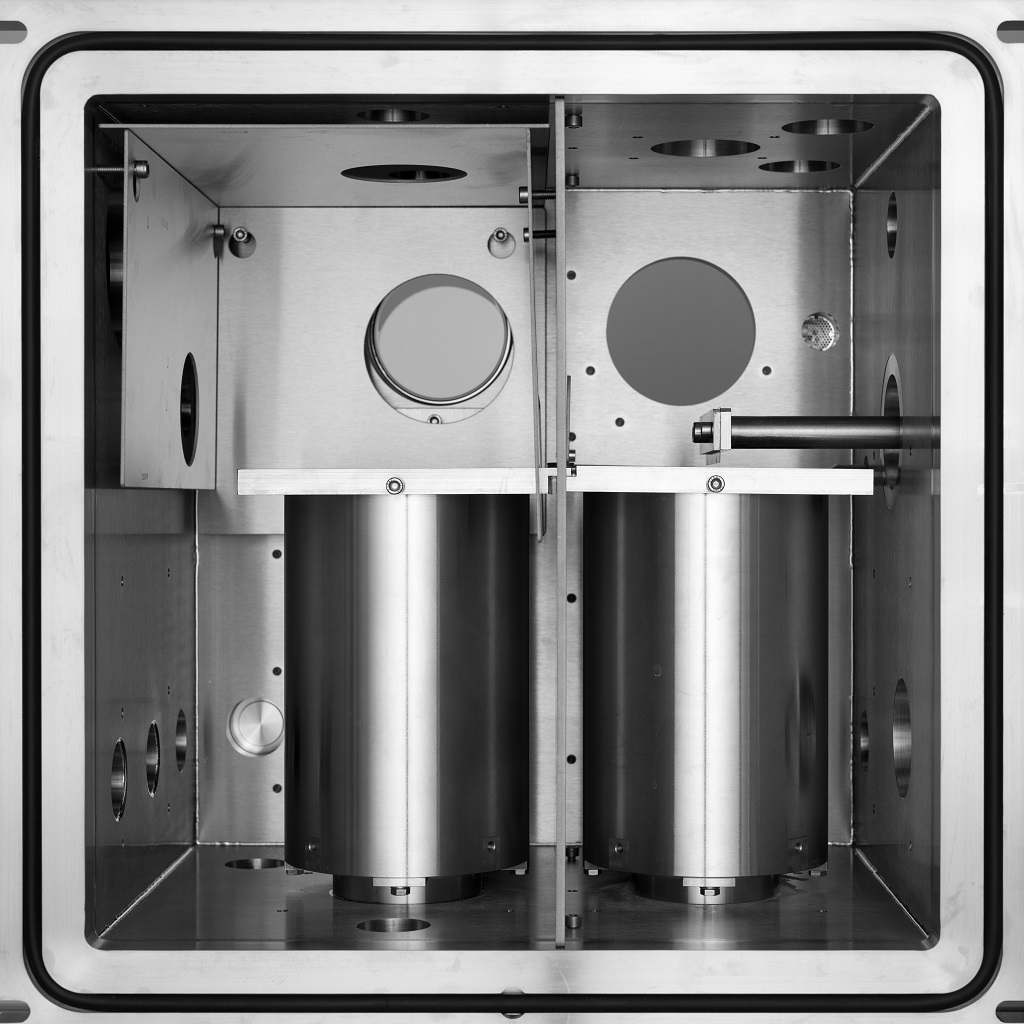
Side view of the Freemelt One vacuum chamber.
What kind of materials are you excited about?
You can use Freemelt ONE’s combination of open source software, high process temperature and high vacuum to develop a wide range of materials for metal 3D printing, for example non-weldable Ni-based superalloys, intermetallics such as titanium aluminide, high-alloyed steels, refractory metals and oxygen-free high-conductivity (OFHC) copper. But at the end of the day, it is our customers who themselves decide which materials to develop with their Freemelt ONE printers.
Recently I’ve seen a lot of excitement about BMG’s (bulk metallic glasses) and intermetallics?
Intermetallics such as titanium aluminides have good material properties in high operating temperatures and weigh only about half as much as superalloys do. They are therefore of great interest to for example manufacturers of aero engines. At the same time intermetallics are challenging since they are generally brittle at room temperature, which makes them difficult and expensive to manufacture with conventional methods. But turbine blades in titanium aluminide are now being manufactured with E-PBF, by taking advantage of the technology’s high process temperature and excellent temperature control. These titanium aluminide turbine blades have already been flight-tested.
BMG’s or amorphous metals are basically alloys with a disordered, non-crystalline microstructure. BMG’s have many interesting applications, but to obtain the glassy state rapid cooling is required in the manufacturing process. L-PBF and E-PBF offer very high cooling rates as compared to traditional manufacturing methods, which is the reason for the recent excitement. BMG manufacturing with E-PBF has indeed been demonstrated. Just keep in mind that the build temperature must be kept well below the “glass transition temperature” to prevent crystallization.

R&D Manager and E-PBF veteran Ulric Ljungblad.
What’s so special about superalloys?
Superalloys retain strength also in very high operating temperatures and are therefore used in, for example, aero engine turbines, where higher temperatures translate to improved fuel efficiency. However, with increasing temperature capability these alloys become more challenging to manufacture as they require high process temperatures and precise temperature control. This makes the E-PBF technology a suitable choice to produce parts in such superalloys.
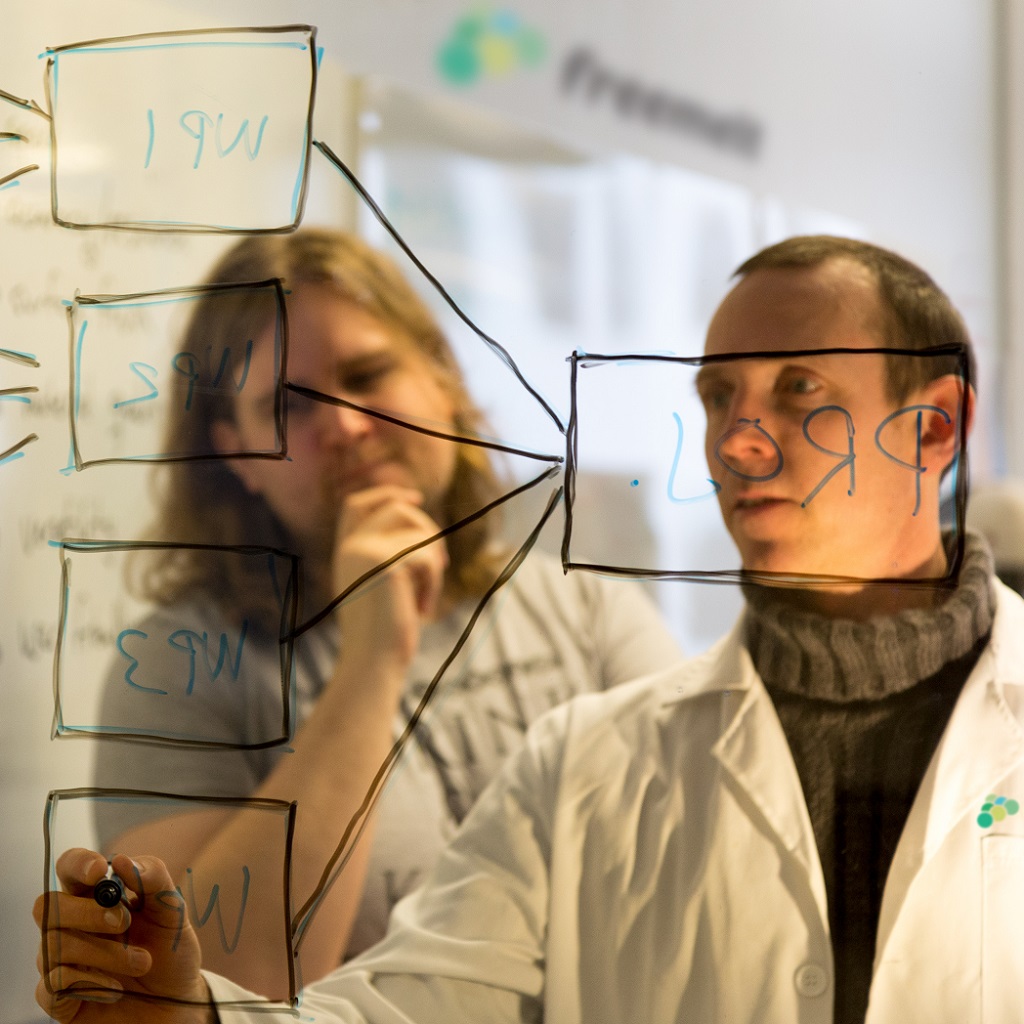
Two Freemelt Team Members Robin Stephansen Systems Designer (left) and Martin Wildheim Senior Mechanical Designer
What was it like working at Arcam for such a long time?
It was a great experience and a privilege to contribute to the E-PBF journey, and gave us a thorough understanding of the technology’s capabilities and potential. We also took part in successful industrial applications of the technology, such as orthopaedic implants in titanium and turbine blades in titanium aluminide. Going forward, Freemelt’s mission is to continue to develop the E-PBF technology and enable our customers to launch additional successful industrial applications in new materials.
Why is E-PBF such a good technology for space vehicles and rocket engines?
Space vehicles operate under extreme conditions and the space industry, therefore, uses many advanced materials, for example, different high-temperature materials in the rocket engines, and lightweight materials in structural components. There are also many new space companies that manufacture smaller rockets, where the components are small enough to fit nicely inside the build envelope of PBF systems.
Do you see E-PBF being used as the main technology for space vehicles? Or along with L-PBF?
E-PBF and L-PBF are complementary technologies which means that E-PBF will be the technology of choice for some space applications and L-PBF for others. I would say that E-PBF will be used predominantly for high-temperature applications such as rocket engines.
Subscribe to Our Email Newsletter
Stay up-to-date on all the latest news from the 3D printing industry and receive information and offers from third party vendors.
Print Services
Upload your 3D Models and get them printed quickly and efficiently.
You May Also Like
Reinventing Reindustrialization: Why NAVWAR Project Manager Spencer Koroly Invented a Made-in-America 3D Printer
It has become virtually impossible to regularly follow additive manufacturing (AM) industry news and not stumble across the term “defense industrial base” (DIB), a concept encompassing all the many diverse...
Inside The Barnes Global Advisors’ Vision for a Stronger AM Ecosystem
As additive manufacturing (AM) continues to revolutionize the industrial landscape, Pittsburgh-based consultancy The Barnes Global Advisors (TBGA) is helping shape what that future looks like. As the largest independent AM...
Ruggedized: How USMC Innovation Officer Matt Pine Navigates 3D Printing in the Military
Disclaimer: Matt Pine’s views are not the views of the Department of Defense nor the U.S. Marine Corps Throughout this decade thus far, the military’s adoption of additive manufacturing (AM)...
U.S. Congress Calls Out 3D Printing in Proposal for Commercial Reserve Manufacturing Network
Last week, the U.S. House of Representatives’ Appropriations Committee moved the FY 2026 defense bill forward to the House floor. Included in the legislation is a $131 million proposal for...