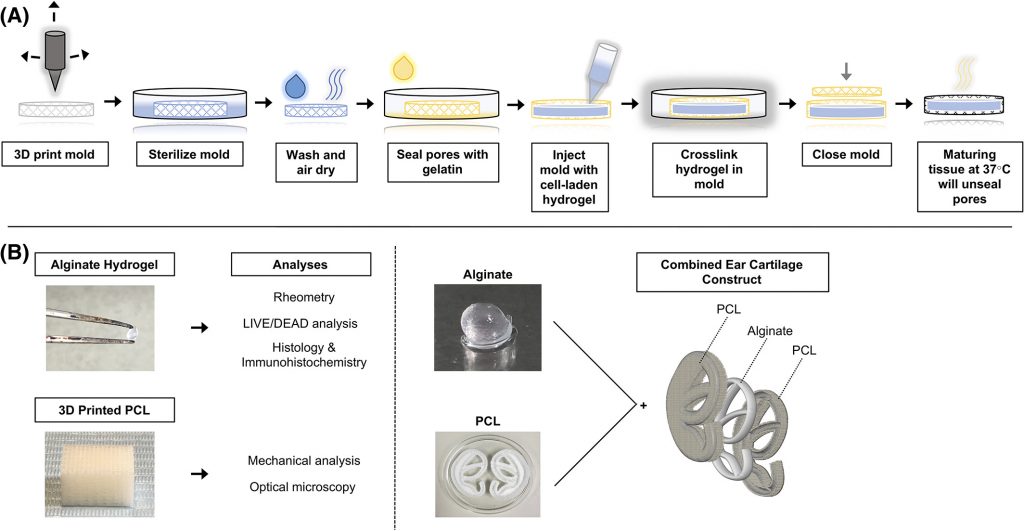
(A) Schematic of steps in the biofabrication of the implant model. (B) Schematic of the study methods. First, alginate hydrogel beads and 3D‐printed PCL scaffolds were analyzed individually. Next, alginate and PCL were combined in one construct to develop an auricular implant model. PCL: Poly‐ε‐caprolactone.
As users around the world embrace 3D printing, the impacts continue to grow in a wide range of industries—but particularly medicine as researchers make strides in their own labs with bioprinting, as well as creating medical devices, implants, prostheses, and more. And although 3D printing in the realm of hearing devices and bioprinting of ear tissue is not entirely new, researchers in the Netherlands have been working on a novel method for auricular reconstruction.
The Netherlands research team outlines their findings in ‘Design and fabrication of a hybrid alginate hydrogel/poly(ε‐caprolactone) mold for auricular cartilage reconstruction. ‘ With the challenging goal of creating a 3D printed cartilage implant, the researchers assessed whether the bioprinting materials they had in mind were actually viable as they worked to create poly‐ε‐caprolactone (PCL) scaffolds, using alginate as a cell carrier. Success with such technology could mean bypassing more conventional methods that present challenges to include:
- Morbidity at donor site
- Risky exposure of implants
- Difficulty in surgical procedures
“Tissue engineering, in combination with novel biofabrication strategies, is a promising solution to engineer auricular implants with patient‐derived donor cells. These biofabricated auricular constructs could ultimately function as patient‐specific implants for the reconstruction of a deformed auricle,” state the researchers in their paper.
The key for the these scientists was in finding a scaffold strong enough to bear cell growth as well as that of resulting tissue. This type of new scaffold must be durable but also porous and able to break down easily in terms of biodegradability. Bioink composed of synthetic or natural hydrogel could be used for 3D printing cells, or there is also the option of fabricating the support scaffolds and then adding the cell-hydrogel mixture. Poly‐ε‐caprolactone (PCL) is a plastic material used successfully to create scaffolds strong enough for such a purpose.
Scaffolds were created with differences in strands:
- 400 μm
- 600 μm
- 800 μm
- 1000 μm
- 1200 μm
Customized software created G-code, and medical-grade PCL was 3D printed on a 3DDiscovery. Afterward, the molds were cleaned, sterilized, and sealed. The researchers evaluated each sample’s structure using a microscope, digital camera, and fiber optic light. They then assessed cell viability, after which biomechanical analysis examined PCL scaffolds and the alginate hydrogel itself.
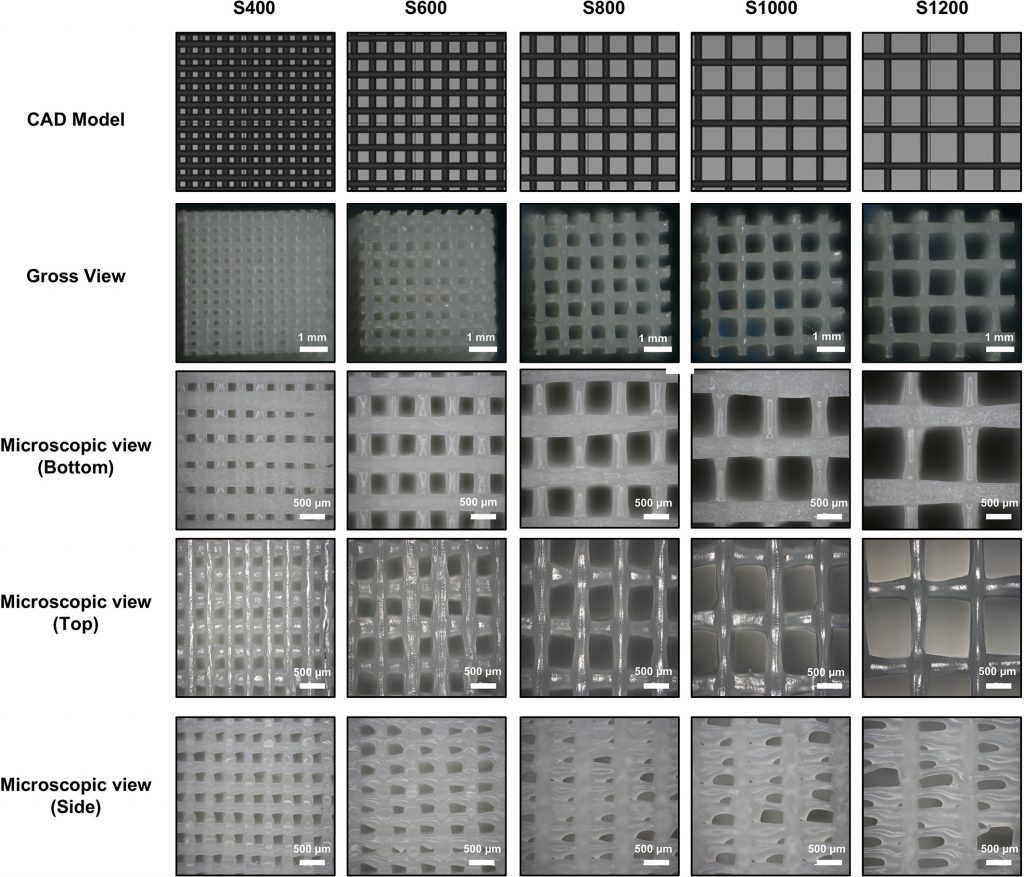
CAD view, gross view, and microscopic views of 3D‐printed PCL scaffolds with varying distances between strands. S represents the sample, with the number representing the distances between strands in micrometers (μm).
They then found that the scaffolds were viable:
“The structural properties of 3D printed PCL scaffolds were determined by examining the surface porosity and mechanical properties. Macroscopic analysis of the PCL scaffolds showed good printing quality,” stated the researchers. “However, microscopic analysis of individual PCL strands showed some variance in strand diameter over a short distance. In addition, the lateral view of the scaffold showed a large variety in pore width. Overall, the smaller the pore width, the more accurate the 3D printed scaffold.”
Overall results were examined further as the researchers considered the following:
- Structural properties of 3D‐printed PCL
- Cell viability and proliferation in alginate hydrogel beads
- Hydrogel biomechanical properties
- Neocartilage formation
- Auricular implant model
The researchers state that the 3D printed cartilage implant does indeed possess the type of mechanical properties required to withstand challenges during in vivo tissue maturation, as well as a natural core that is able to form tissue.
“The mold can be easily printed and assembled, while the design makes it easy to inject any suitable hydrogel for tissue formation,” concluded the researchers. “While long‐term in vivo experiments are required to test its preclinical applicability, the work presented in this study provides a possible strategy for the use of biofabricated tissue constructs in the clinic.”
What do you think of this 3D printing news? Let us know your thoughts! Join the discussion of this and other 3D printing topics at 3DPrintBoard.com.
[Source / Images: ‘Design and fabrication of a hybrid alginate hydrogel/poly(ε‐caprolactone) mold for auricular cartilage reconstruction’]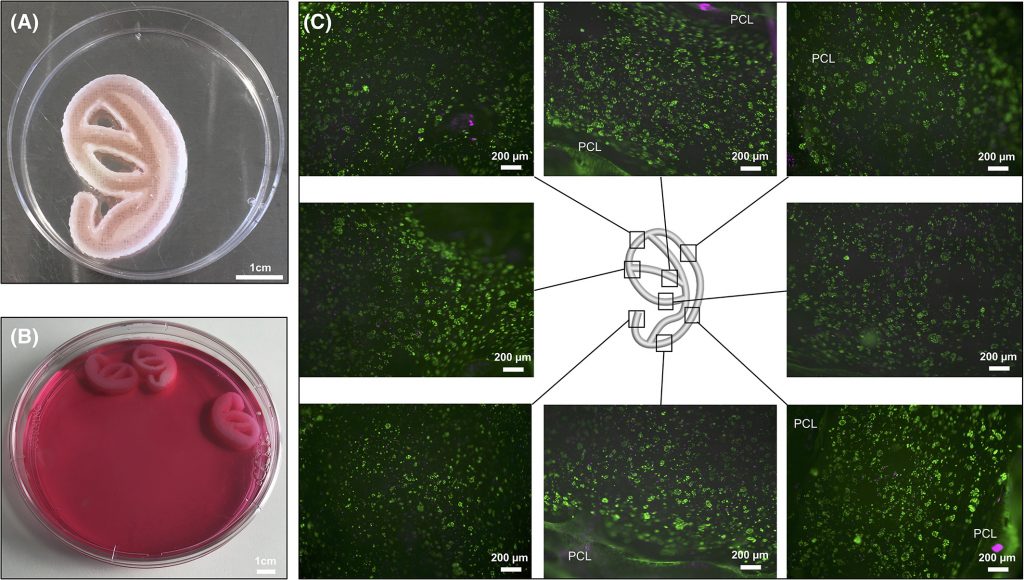
A) Gross view of the PCL‐alginate auricular implant model. Alginate can be found inside the grooves of the PCL mold. Note that one part of the 2‐part mold has been taken off for viewing. (B) in vitro cultured PCL‐alginate auricular implant models. (C) LIVE/DEAD stain of alginate taken out of the PCL mold after 21 days of culture. High‐cell survival was seen throughout the entire implant model.
Subscribe to Our Email Newsletter
Stay up-to-date on all the latest news from the 3D printing industry and receive information and offers from third party vendors.
Print Services
Upload your 3D Models and get them printed quickly and efficiently.
You May Also Like
3D Printing News Briefs, July 2, 2025: Copper Alloys, Defense Manufacturing, & More
We’re starting off with metals in today’s 3D Printing News Briefs, as Farsoon has unveiled a large-scale AM solution for copper alloys, and Meltio used its wire-laser metal solution to...
3DPOD 260: John Hart on VulcanForms, MIT, Desktop Metal and More
John Hart is a Professor at MIT; he´s also the director of the Laboratory for Manufacturing and Productivity as well as the director of the Center for Advanced Production Technologies....
3D Printing News Briefs, June 28, 2025: Defense Accelerator, Surgical Models, & More
In this weekend’s 3D Printing News Briefs, 3YOURMIND was selected to join an EU Defense Accelerator, and PTC has announced model-based definition (MBD) capabilities within Onshape. Finally, a study out...
EOS in India: AM’s Rising Star
EOS is doubling down on India. With a growing base of aerospace startups, new government policies, and a massive engineering workforce, India is quickly becoming one of the most important...