Anders Olsson is an all-round great person and a boon to the 3D printing community. His Olsson block gave us easy to exchange nozzles, with the Olsson Ruby we got a great nozzle and now with the Olsson Ruby High Temperature we have a high-performance nozzle for abrasive materials. The ruby material lasts long and is meant to withstand many hours of abrasive materials. The new Olsson Ruby High Temp can handle 500 C which means it can be suited for PEEK and other high-temperature applications.
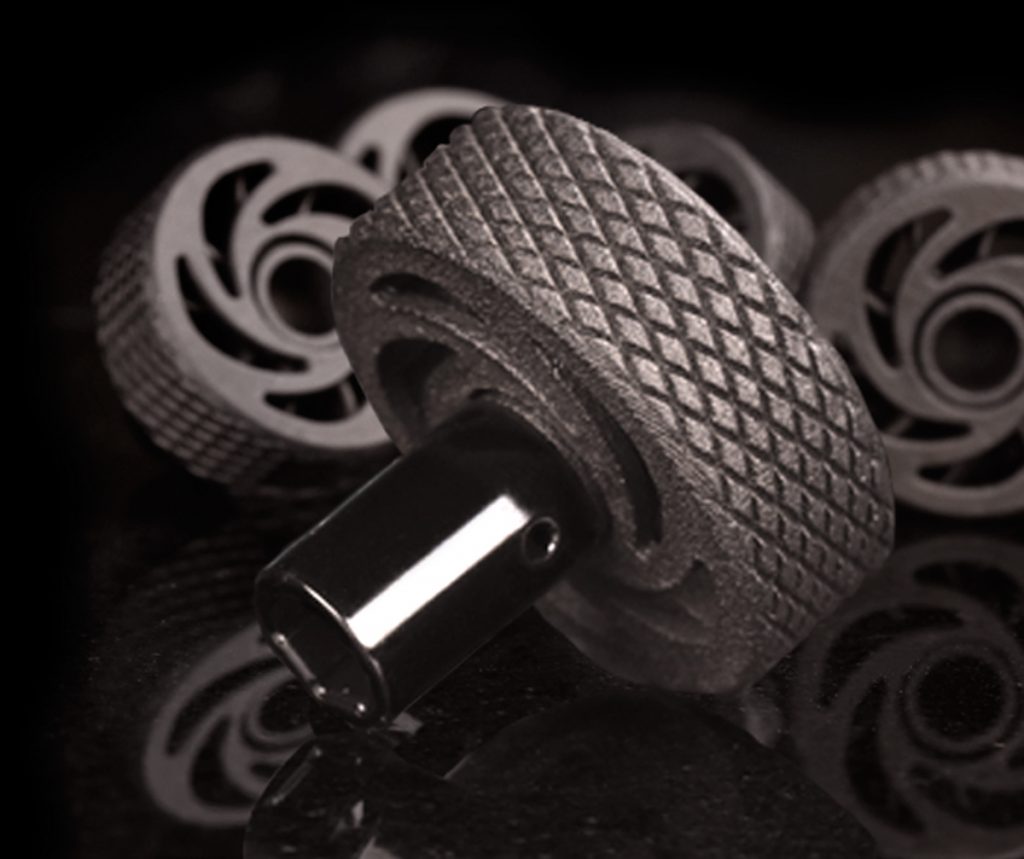
The Olsson Torque Wrench
Anders also designed a unique torque wrench which will be available soon. This 3D printed wrench-ling is part standard wrench head but augmented by a part 3D printed in HPs multijet fusion technology. Very easy to use it gives you the precise pressure needed to mount a new interchangeable nozzle. Another item developed by Olsson is the new Print Core CC Red from Ultimaker also used for abrasive materials. A wealth of new and exciting things at the Olsson stand and more than enough reason to interview him at the TCT Show where he was attending with his partners at 3DVerkstan which I think is a market leading reseller of 3D Skrivare and 3D Skrivare supplies in the Nordic countries.
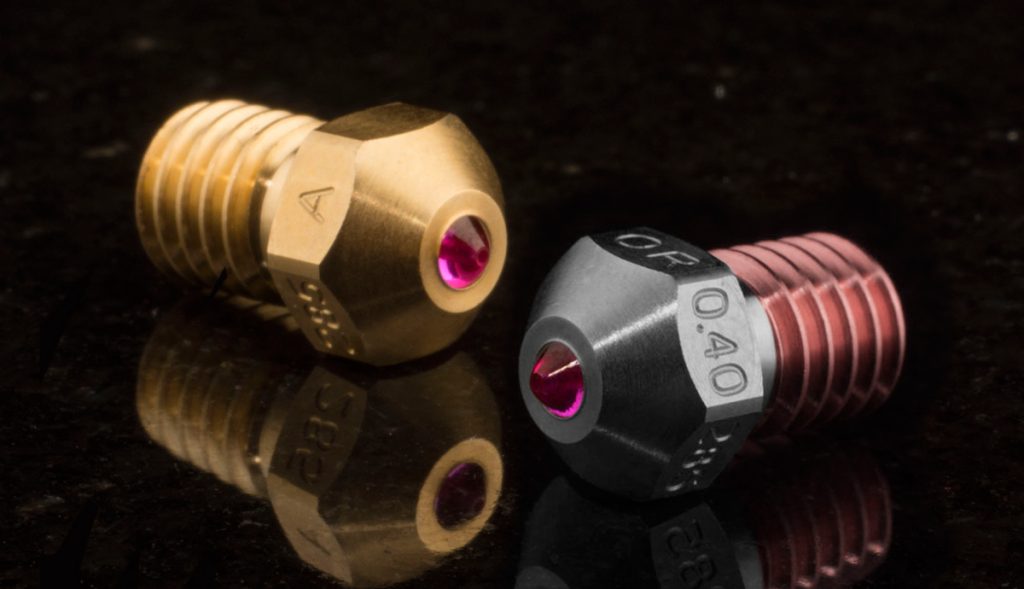
The Olsson Ruby, left and the new Olsson Ruby High-Temperature Nozzle
What is the Olsson Ruby?
It’s a unique nozzle for 3D Printers, designed to print highly abrasive materials while retaining the excellent heat conductivity of brass. It works equally well for printing common FDM (FFF, Material Extrusion) 3D printing materials up to 300C. There is also a high temp version of the Olsson Ruby, enabling the use of high temp materials up to 500C.
Why is it so successful?
Our customers are getting high performance and consistent results out of using the ruby nozzle when printing abrasive materials. The materials are composites with fillers such as carbon, boron carbide, and glass fiber among others. This lets them get a new type of functionality in materials that can bring improved mechanical properties as well as radiation shielding, electrical conductivity, ESD shielding and more.
How many have been sold?
We have sold more than 15000 units worldwide.
Wait you use real rubies for this?
Yes, for consistent results we use industrially grown rubies, which are also better for the application than natural rubies with their inherent flaws.
Why is wear resistance important in a nozzle?
Because when printing abrasives with common nozzles, they wear out fast and affect print quality in a negative way.
Why do nozzles always use brass and not copper or another material?
This is usually because brass has a combination of good properties:
- High machinability
- Excellent heat conductivity
- Relatively low cost
Other materials might have worse heat conductivity or worse machinability, and might be more expensive or a combination of these qualities. For copper alloys, they are a little harder to machine than brass and depending on the alloy they might also be too soft and start to anneal at common printing temperatures. That said, in our new High Temp version of the Olsson Ruby nozzle, we are using a special, high conductivity copper alloy which has excellent thermal conductivity and retains its mechanical strength at over 500 degrees Celsius.
Will you develop new nozzles?
Yes, we just launched a High Temp version of the Ruby Nozzle and are continuously developing new nozzles and other accessories. Some are in collaboration with 3D Printer manufacturers, such as the newly announced Print Core CC Red for the Ultimaker S5 3D Printer.
Subscribe to Our Email Newsletter
Stay up-to-date on all the latest news from the 3D printing industry and receive information and offers from third party vendors.
Print Services
Upload your 3D Models and get them printed quickly and efficiently.
You May Also Like
Reinventing Reindustrialization: Why NAVWAR Project Manager Spencer Koroly Invented a Made-in-America 3D Printer
It has become virtually impossible to regularly follow additive manufacturing (AM) industry news and not stumble across the term “defense industrial base” (DIB), a concept encompassing all the many diverse...
Inside The Barnes Global Advisors’ Vision for a Stronger AM Ecosystem
As additive manufacturing (AM) continues to revolutionize the industrial landscape, Pittsburgh-based consultancy The Barnes Global Advisors (TBGA) is helping shape what that future looks like. As the largest independent AM...
Ruggedized: How USMC Innovation Officer Matt Pine Navigates 3D Printing in the Military
Disclaimer: Matt Pine’s views are not the views of the Department of Defense nor the U.S. Marine Corps Throughout this decade thus far, the military’s adoption of additive manufacturing (AM)...
U.S. Congress Calls Out 3D Printing in Proposal for Commercial Reserve Manufacturing Network
Last week, the U.S. House of Representatives’ Appropriations Committee moved the FY 2026 defense bill forward to the House floor. Included in the legislation is a $131 million proposal for...