Fused deposition modeling (FDM) is a 3D printing method that can easily meet the requirements for small series industrial manufacturing. However, there aren’t a lot of commercially available materials that can work well with it other than PLA, ABS, TPU, PET, and a few others. FDM materials should have performance that makes 3D printing easier, better and more effective. Users are looking at things such as dimensional accuracy, high deposition speed, adhesion strength, and thermal and/or electrical conductivity. Beyond trinkets, new performance and quality are needed. Nanocomposites and polymer-based composites can be good choices to expand what 3D printing can do. A collaborative team of researchers is looking at high-temperature engineering polymers, like polyetheretherketone (PEEK), for FDM 3D printing to see if they can further expand the capabilities of these already high performing materials.
PEEK has good chemical resistance, a high glass-transition temperature, high continuous service temperatures, and excellent mechanical properties. Although complex to print and requiring a high-temperature 3D printer, PEEK gives hereto unparalleled performance in 3D printed polymer parts. The material is used in aerospace and in car racing and could change the way parts are made in manufacturing. What if you could take this strong material and also make it conductive? One could then build more complex functional parts that could be highly functional.
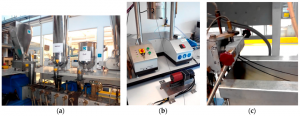
Manufacture of PEEK/CNT/GnP nanocomposites by melt compounding in a twin-screw extruder using separate feeding (a), and extrusion of the filaments using a capillary rheometer (b) or a twin-screw extruder (c).
The team, made up of researchers from the University of Minho in Portugal, the Leibniz Institute of Polymer Research Dresden, and the Netherlands-based European Space Research and Technology Centre, recently published a paper, titled “Electrically Conductive Polyetheretherketone Nanocomposite Filaments: From Production to Fused Deposition Modeling,” that discusses how they developed 1.75 mm electrically conductive PEEK-based filaments for FDM 3D printing through the use of melt compounding and plasticating extrusion methods.
The abstract reads, “The present work reports the production and characterization of polyetheretherketone (PEEK) nanocomposite filaments incorporating carbon nanotubes (CNT) and graphite nanoplates (GnP), electrically conductive and suitable for fused deposition modeling (FDM) processing. The nanocomposites were manufactured by melt mixing and those presenting electrical conductivity near 10 S/m were selected for the production of filaments for FDM. The extruded filaments were characterized for mechanical and thermal conductivity, polymer crystallinity, thermal relaxation, nanoparticle dispersion, thermoelectric effect, and coefficient of friction. They presented electrical conductivity in the range of 1.5 to 13.1 S/m, as well as good mechanical performance and higher thermal conductivity compared to PEEK. The addition of GnP improved the composites’ melt processability, maintained the electrical conductivity at target level, and reduced the coefficient of friction by up to 60%. Finally, three-dimensional (3D) printed test specimens were produced, showing a Young’s modulus and ultimate tensile strength comparable to those of the filaments, but a lower strain at break and electrical conductivity. This was attributed to the presence of large voids in the part, revealing the need for 3D printing parameter optimization. Finally, filament production was up-scaled to kilogram scale maintaining the properties of the research-scale filaments.”

Main steps for nanocomposite optimization and the selection of filament composition, for the production of electrically conductive filaments for 3D printing. PEEK—polyetheretherketone; MWCNT—multi-walled carbon nanotubes; GnP—graphene nanoplates.
Because of prior research showing that a morphology of carbon nanotubes (CNTs) place between graphene nanoplates (GnP) to form bridges had good properties but a much less effective electrical network, the team decided to prepare hybrid/ternary nanocomposites of PEEK/CNT/GnP with different compositions, using melt mixing, and measure their electrical conductivity.
“Selected nanocomposites were then extruded into filaments, which were also characterized. Finally, selected filaments were utilized to manufacture tensile bars using a commercial 3D printer. Although every step of processing produced composites with lower electrical conductivity, values of the order of 10 S/m were attained in the filaments produced. Due to this successful outcome, the European Research Agency tested these filaments in their satellites program,” the researchers wrote.
The team used PEEK material from UK company Victrex, which specializes in high performance, high-temperature materials. They manufactured and pelletized the nanocomposites – PEEK was fed in first, and after it was forced to melt, they added MWCNT and GnP. Then, the resulting composites were pelletized, and the researchers were able to obtain 1.75 mm filaments.
Testing of the PEEK tensile specimens, 3D printed on an INDMATEC HPP 155, included measuring the filament’s electrical conductivity, thermoelectric properties, and melt flow index (MFI), testing its tensile strength, and taking differential scanning calorimetry (DSC) measurements.
“The dumbbell specimens produced by 3D printing were tensile tested on a Zwick/Roell Z100 using a 2.5-kN load cell and a cross-head speed of 1 mm/min. The cross-sections of the tensile specimens were cut into 15-μm-thickness samples using a microtome, and were observed under an optical microscope, Olympus BH2, in transmission mode.”
By adding GnP to the nanocomposite with PEEK and MWCNT, a further increase in the electrical conductivity levels was induced.
“Interestingly, the incorporation of GnP into the matrix had a less adverse effect on the processability than that of MWCNT, as showed by the minor changes caused in the melt flow index, in the motor torque of the extruder, and in the melt temperature,” the researchers wrote.
Adding the MWCNT/GnP combination to PEEK was able to reasonably improve the material’s yield strength and Young’s modulus, though it lowered the PEEK filaments’ ductility.
“Although the electrical conductivity of the filaments was lower than that of the equivalent nanocomposites, at sufficiently high filler contents, values near to 10 S/m were still observed,” the researchers concluded. “The thermal conductivity was also enhanced. Moreover, the thermoelectric parameters were similar to or higher than those reported in the literature for other PEEK-based composites. In this case, the lubricating effect of graphite seen for the nanocomposites caused a noteworthy reduction in the friction coefficient. This behavior should be relevant for applications requiring tribological properties, such as gears.”
Co-authors of the paper are Jordana Gonçalves, Patrícia Lima, Beate Krause, Petra Pötschke, Ugo Lafont, José R. Gomes, Cristiano S. Abreu, Maria C. Paiva, and José A. Covas.
Discuss this research and other 3D printing topics at 3DPrintBoard.com or share your thoughts below.
Subscribe to Our Email Newsletter
Stay up-to-date on all the latest news from the 3D printing industry and receive information and offers from third party vendors.
Print Services
Upload your 3D Models and get them printed quickly and efficiently.
You May Also Like
3D Printing News Briefs, July 2, 2025: Copper Alloys, Defense Manufacturing, & More
We’re starting off with metals in today’s 3D Printing News Briefs, as Farsoon has unveiled a large-scale AM solution for copper alloys, and Meltio used its wire-laser metal solution to...
3DPOD 260: John Hart on VulcanForms, MIT, Desktop Metal and More
John Hart is a Professor at MIT; he´s also the director of the Laboratory for Manufacturing and Productivity as well as the director of the Center for Advanced Production Technologies....
3D Printing News Briefs, June 28, 2025: Defense Accelerator, Surgical Models, & More
In this weekend’s 3D Printing News Briefs, 3YOURMIND was selected to join an EU Defense Accelerator, and PTC has announced model-based definition (MBD) capabilities within Onshape. Finally, a study out...
EOS in India: AM’s Rising Star
EOS is doubling down on India. With a growing base of aerospace startups, new government policies, and a massive engineering workforce, India is quickly becoming one of the most important...