3D printing with concrete is causing a shift in the construction industry, but as some experts have pointed out, we need to be careful not to get too caught up in the hype as opposed to the reality of the technology. One thing that many people forget is that 3D printed concrete still needs to be reinforced in some way, and no perfect solution has made itself available yet in terms of doing so. In a new paper entitled “Incorporating reinforcement into digital concrete construction,” which you can access here, a group of researchers discusses possible ways of reinforcing 3D printed concrete.
“Significant progress has been made in non-reinforced concrete printing in the recent years with research and industrial organizations producing geometrically complex structures as well as innovative rapid mass-customized buildings,” the researchers state. “However, the research on incorporating reinforcement into fully automated digital construction approaches is limited with the suggested solutions still being rudimentary…Since the use of reinforcement is mandatory in most structural applications, there is an urgent need to bring the technology of reinforcing 3d-printed structural elements forward.”
Several possible methods of reinforcement are discussed, including the placement of conventional, fiber or textile reinforcement with concrete deposition or between 3D printed concrete layers; enveloping concrete around steel reinforcement; using robotically produced reinforcement as a functional formwork in which concrete is placed subsequently; 3D printing with dispersed short fiber reinforced cement composites; and the advanced production of reinforcement and concrete robotically, “preferably in parallel.”
The researchers also discuss Mesh Mold technology, in which an industrial robot forms complex, free-form meshes that act both as formwork and reinforcement.
“Despite the encouraging concepts and prototypes, none of these approaches satisfies the entire spectrum of relevant requirements for wide ranging implementation of DC (digital construction), thus there should to be developed further,” the researchers continue. “The majority of the validated approaches are discontinuous, meaning concrete printing and reinforcement placement must be carried out one after other.”

Various DC approaches: a) extrusion based layer-deposition, b) Mesh Mold approach, c) schematic illustration of Smart Dynamic Casting process and d) numerous nozzle setup for selective binder deposition, setup by D-Shape
This means that longer construction times and higher costs will likely be required, and/or additional equipment will be needed for placing reinforcement.
“The pre-stressing of post-placed reinforcement is only possible if continuous conduits are formed during 3dcocnrete-printing, effecting the geometrical flexibility,” they add. “Further, the weak layer-to-layer interfaces may also function as easy passages for transport of aggressive fluids and gases into printed structures. This is an important concern if steel reinforcement is to be used in digital construction and the risk of corrosion could be enhanced if thin free-form structures are to be printed.”
Other possibilities discussed include strain-hardening cement-based composites (SHCC) and 3D printing of steel reinforcement using gas-metal arc welding (GMAW). Both are promising techniques that are currently being investigated.
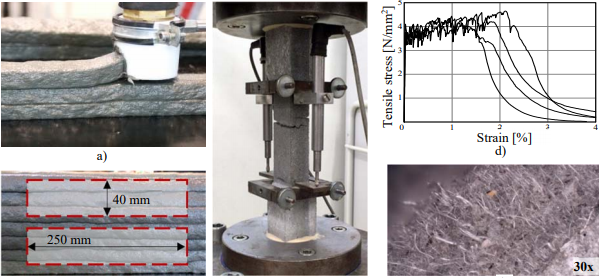
a) 3d-printed SHCC being extruded through nozzle, b) cutting location in the seven-layer printed wall, c) setup of uniaxial tension tests, d) stress-strain curves for printed SHCC and d) fractured cross-section, indicating both pronounced fiber-pullout and extrusion-induced preferential orientation of fibers.
In short, 3D printed construction isn’t as simple as it seems to be – you can’t just slap down layers of un-reinforced concrete and expect to create a safe building. Companies 3D printing buildings are coming up with creative ways to reinforce them, however, leading to safer, more permanent structures. The article argues that the methods being used for reinforcing 3D printed concrete are not perfect, but that with further development they could be made more effective.
Authors of the paper include Venkatesh N. Nerella, Hiroki Ogura, and Viktor Mechtcherine.
Discuss this and other 3D printing topics at 3DPrintBoard.com or share your thoughts below.
Subscribe to Our Email Newsletter
Stay up-to-date on all the latest news from the 3D printing industry and receive information and offers from third party vendors.
Print Services
Upload your 3D Models and get them printed quickly and efficiently.
You May Also Like
Titomic Opens New U.S. Facility in Huntsville to Boost 3D Printing for Defense
Australian company Titomic (ASX: TTT) has expanded into Huntsville, Alabama, opening a new U.S. facility that brings its advanced metal manufacturing technology closer to key defense and aerospace hubs. The...
Steadfast XO: Will USVs and UUVs Disrupt Existing Naval Power?
A quiet revolution is underway in Unmanned Surface Vehicles (USV) & Unmanned Underwater Vehicles (UUV). Ukraine didn’t have much of a Navy when Russia invaded, but has been able to...
Recipe for an AM Cluster: ADDIMAT’s Zubizarreta on the Making of the Spanish AM Ecosystem
One of the most significant themes in the global manufacturing sector throughout the last decade has been the nurturing of existing economic clusters and the seeding of new ones by...
Nikon Advanced Manufacturing & America Makes to Develop Aluminum Powder Dataset
Nikon Advanced Manufacturing Inc., the Long Beach-based end-to-end metal additive manufacturing (AM) firm, has announced that the company is partnering with the Manufacturing USA Institute America Makes to develop an...