3D printing opens up infinite new realms of creativity to innovators around the world, whether they are bioprinting or making surgical implants, cars, rocket engine components, or running shoes. Along with all that wonderful opportunity for invention, however, comes pressure. While it is understandable that some objects are still works in progress, most of us want the end product to be as perfect as possible—not only out of self-respect, but also out of respect for a technology just coming into its own in the mainstream, and a need for proper aesthetics, functionality, and productivity.
Now, researchers from the Russian Academy of Sciences have found ways to improve upon 3D printing, outlined in ‘Improvement of quality of 3D printed objects by elimination of microscopic structural defects in fused deposition modeling,’ by Evgeniy G. Gordeev, Alexey S. Galushk, and Valentine P. Ananikov. Porosity issues are a reason for many failures in FDM 3D printing, despite its usefulness in so many different applications, to include medicine, biochemistry, engineering, chemical sciences, and more. Issues with structural weakness and porosity often make the use of FDM 3D printing challenging though, whether just in prototyping or other manufacturing processes.
In assessing FDM 3D printing, the research team used materials such as PLA, ABS, PETG, PP, Nylon (polyamide), and carbon-filled Nylon while they examined the following:
- Filament feed rate
- Wall geometry
- G-code defined wall structure
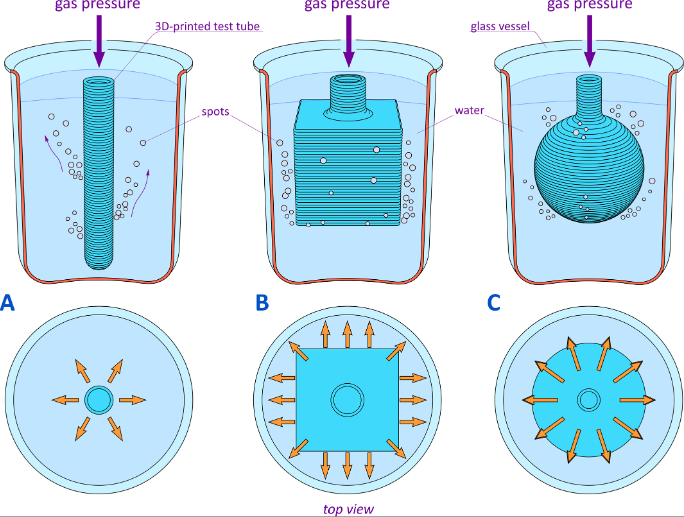
(A) cylindrical test tube, (B) hollow entity of cubical shape, (C) spherical flask. In the top view, arrows indicate outgassing.
As they optimized feed rate and structure, the researchers were able to significantly improve 3D printing quality—even with more basic hardware and materials. In evaluating, they printed with a Picaso 250 Designer Pro (PICASO 3D) with a 0.3 mm diameter nozzle, creating objects like cylinders, cones, spheres, pyramids, and cubes—all of which they performed numerous experiments on.
“It turned out that under standard conditions cylindrical objects had the minimum number of pores and the best quality of 3D printing,” stated the researchers. “Conical objects had larger pores uniformly distributed over the surface. For a spherical shape, the largest number of pores was observed in the region of poles lying on the axis perpendicular to the planes of the layers, while the equatorial region retained impermeability.”
“A combination of cylindrical and conical shapes in one object resulted in a uniform distribution of a small number of pores in the wall of the cylindrical portion, and a much larger number of pores in the conical portion. In plane-faced products (e.g. hexagonal pyramid and cube), the most porous areas were found at the edges, that was, in the neighborhood of the joints between the faces. The observed dependence of porosity on the geometric shape or its specific area is explained by the corresponding differences in the mode of layer positioning: in cubical and cylindrical products, the layers are arranged exactly one above the other, so the interlayer contact is most effective. In conical products, the layers are arranged with a certain offset, that is, stepwise, which makes the interlayer contact less effective.”

Functional assessment of 3D printing quality for objects of different shapes.
All objects are printed with identical parameters at k = 0.9 from PLA: (A) cylinder, (B) cone, (C) sphere, (D) compound shape, (E) pyramid, (F) cube. The diagrams below show the distribution/densities of the pores. Red areas have maximal porosity/permeability; green areas are relatively impermeable; blue color designates junctions with the air compressor.
The team states that they found ‘edges and vertices’ to have more defects than other shapes in the experiments.
“Among the shapes with smooth outlines, conical and spherical elements of irregular curvature are most vulnerable, whereas flat and cylindrical surface areas are most resistant to the pore formation,” stated the researchers.
The researchers also discovered that thin-walled objects became ‘untenable’ in terms of sealant. Reversing this with thicker walls allowed for less pores and better success in 3D printing:
“Thus, to minimize the porosity, the proper filling of the inner space should be additionally controlled by verification of the G-code suggested by the slicer software. The more homogeneous the intermediate layer of the wall is, the more impermeable the wall of the product will be, since all the seams will be securely insulated from each other.”
Permeability was shown to be greatly affected by the following conditions:
- Extrusion multiplier
- Wall thickness
- Internal filling
- Temperature
- Materials
- Shape
“The product properties can be affected by the feeder construction, presence/absence of a closed case, heating mode of the working platform, extruder cooling system, etc.,” concluded the researchers. “Despite that, with proper optimization of printing conditions, commercial desktop 3D printers can be suitable for the production of sealed containers for various applications. The proposed quality assessment procedure allows the gradual improvement of the quality of 3D printed objects by elimination of structural defects.”
Find out more about the research conducted at the Russian Academy of Sciences here.

PP tubes as chemical reaction vessels in comparison with conventional glass test tubes. Values of k are given below for each 3D-printed tube. Performance in the studied chemical transformation is illustrated by product yield (in %) in each studied case, where ≥ 90% efficiency corresponds to excellent performance.
What do you think of this news? Let us know your thoughts! Join the discussion of this and other 3D printing topics at 3DPrintBoard.com.
Subscribe to Our Email Newsletter
Stay up-to-date on all the latest news from the 3D printing industry and receive information and offers from third party vendors.
Print Services
Upload your 3D Models and get them printed quickly and efficiently.
You May Also Like
Johns Hopkins University Researchers Develop HyFAM Technology
Two scientists from Johns Hopkins University, Nathan C. Brown and Jochen Mueller, have developed a hybrid manufacturing technology they call HyFam, or Hybrid Formative Additive Manufacturing. Their work on this technology...
3D Printing G-Code Gets an Upgrade: T-Code
Good old G-Code still manages many 3D printers, great and small. Just like the STL, it’s a standard that enables collaboration while also holding the additive manufacturing (AM) industry back....
AM Rewind: The Biggest News and Trends of 2024
After a sluggish 2023, driven by persistent inflation and geopolitical tensions, 2024 has seen some recovery. Economic growth climbed from about 2.8 percent in 2023 to a modest 3.2 percent...
Metal Wire 3D Printer OEM ValCUN Announces Plans for 2025 Expansion
ValCUN, a Belgian original equipment manufacturer (OEM) of wire-based metal additive manufacturing (AM) hardware, has announced that the company has entered the next phase of its growth trajectory, making key...