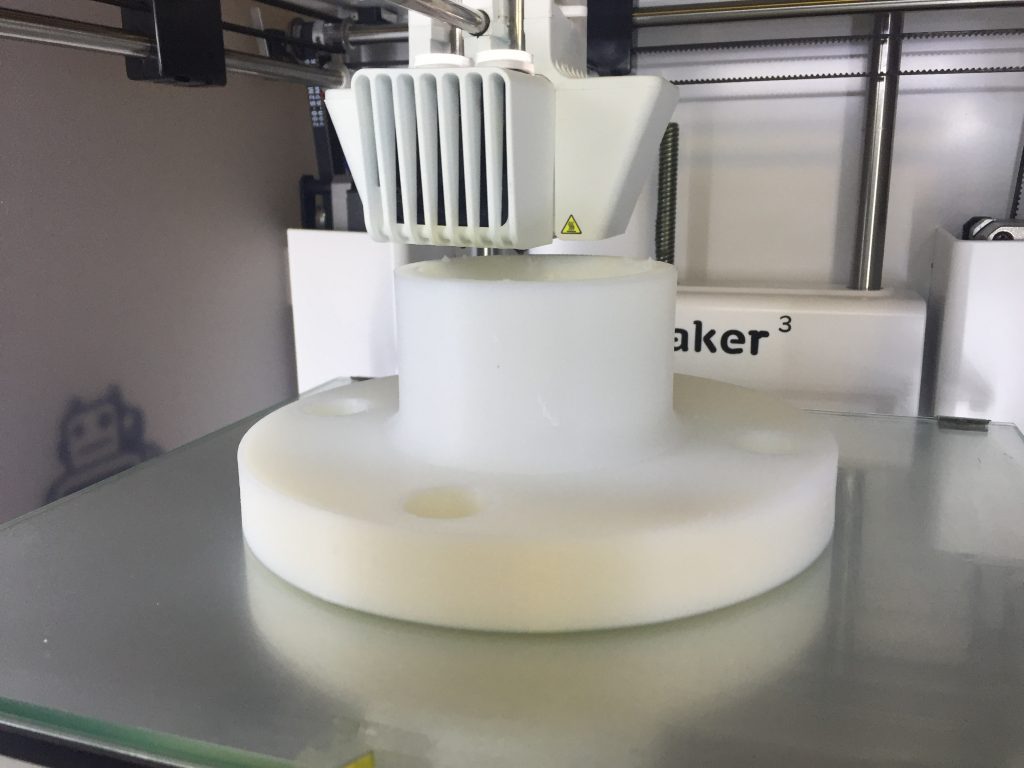
A 3D Printed PVDF part on an Ultimaker 3 by Nile Polymers.
Some of the most popular polymers in the manufacturing world as a whole are difficult to 3D print. Some, like PEEK and PEKK, have only become accessible for 3D printing recently, as 3D printers have advanced and become more capable of printing at high temperatures. PVDF is a material that is well known in many industries and is now being commercialized for 3D printing by several companies. PVDF is very promising because it doesn’t need a high-temperature 3D printer to print but does open up some very interesting capabilities for 3D printing. We took a deeper dive into the material and interviewed experts at different companies about so that you may be able to see if this material is right for your business.
What are the Applications for PVDF?
Polyvinylidene fluoride, or PVDF, has been around since the 1960s. Its resistance to nuclear radiation made it a material that could be used in the nuclear industry; it was also used in pulp and paper. Its uses then expanded into tubing and piping for chemical plants, underground fuel containment, offshore oil platforms, and more.
Until very recently, PVDF has not been seen in the 3D printing industry, but that’s changing. More than one company is now carrying filament made from Arkema’s Kynar PVDF material and some are rumoured to be working on other PVDF filaments from other suppliers which could include Solvay (Solef), Daikin (Neoflon or Polyflon), Kureha (KF Polymer) or 3M Dyneon. Brian Alexander, the Global Product Application Manager Business Incubation-Additive Manufacturing at Solvay told 3DPrint.com that, “We tailor our materials and develop a specific grade for the AM technology in question. We have a great deal of experience with a variety of Fluoropolymers, including PVDF, for which we are developing an optimised filament for the FFF/FDM process”
Nile Polymers, based out of Centerville, Utah, recently began offering what it is calling Fluorinar-H, a Kynar-based filament designed for industrial-grade 3D printing. They have a 100% Kynar grade while other products are blends, including Nile Polymers’ Fluorinar-C PVDF copolymer filament. Other companies offering Kynar-based products are 3DXTech and Convena Polymers.
What is special about PVDF?
So what’s so special about PVDF, and why is it likely to become a sought-after material for 3D printing? There’s the nuclear resistance factor, which should appeal to the growing number of applications for 3D printing in the nuclear power industry. It’s also highly chemical-resistant, performing well long-term in contact with a wide range of chemicals, including oil, gas, and lubricants, as well as fully halogenated hydrocarbons, alcohols, acids and bases. It’s UV-resistant as well and can be exposed to sunlight for years without losing its mechanical properties. It has excellent material release properties, can be sterilized with gamma rays without loss of tensile strength, and has low smoke and flame characteristics – the base resin is rated V-0. It also has a high continuous use temperature of up to 150ºC.
PVDF is non-hygroscopic, meaning that it does not absorb moisture and requires no special drying or storage, unlike materials such as PLA and nylon. It has long-term hydrolytic stability and is food-safe in its pure form.
PVDF is well-suited to a wide variety of applications. Due to its high mechanical strength, chemical resistance and low permeability, Kynar is used as a contact surface for the production, storage and transfer of corrosive fluids. It’s also used in mechanical components, fabricated vessels, tanks, pumps, valves, filters, heat exchangers, tower packing, piping systems and more. Its resistance to fire, chemicals, impact and abrasion makes it a good candidate for wires and cables, and it also has a number of applications in electricity and electronics such as protective sheathing, insulation for plenum and communications cables.
In the automotive industry, Kynar is used as a barrier liner for fuel line and gas station fuel pumps, in decorative films, as a binder in HEV/EV batteries, as molded and thermoformed body components, and as tank trailer linings for corrosion protection.
What are the 3D Printing Applications of PVDF?
Those are some of the general applications for PVDF, but what about in 3D printing? As a 3D printing material, pure PVDF is so new that it hasn’t yet proven itself on a widespread basis, but its aforementioned characteristics make it a promising candidate for 3D printed applications in the aerospace and automotive industries, as well as electronics, building materials, and nuclear applications. It may be a good material for prototyping and small volume production especially in things requiring chemical resistance such as industrial valves.
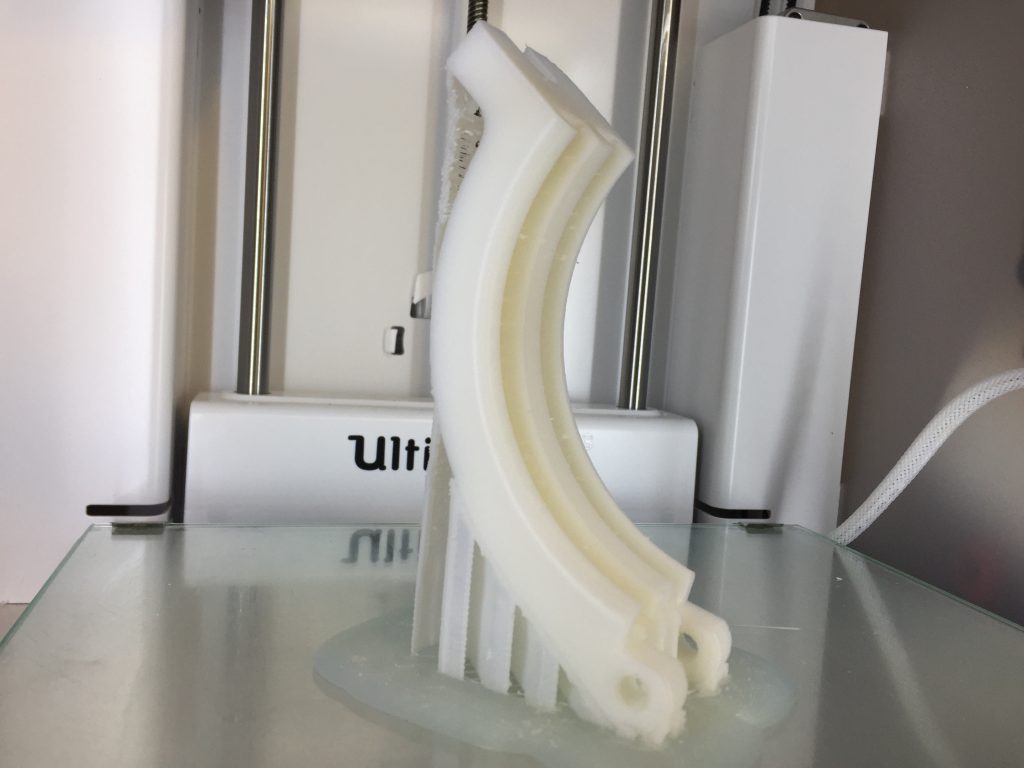
A PVDF 3D Printed Part on an Ultimaker 3 by Nile Polymers.
3DPrint.com reached out to the producers of PVDF filament to find out more. Arkema‘s Guillaume de Crevoisier told us that,”filaments, based on Arkema’s Kynar® PVDF, are exceptional because they are stronger and more isotropic than many other extrusion printing materials.”
Howard Fisher of Nile Polymers responded to us with some real-life examples of using PVDF in 3D printing:
“Last week we printed a three-part clamp for an automated bottle filling station where the requirement was for high-purity polymer with lot traceability back to the point of manufacture.We also completed a series of 1, 2 and 3 inch diameter flange prints on 6 inch pipe stubs. These will be inserted into a PVDF/FRP dual laminate acid storage tank and hot gas welded to the tank interior lining which is also manufactured from PVDF. Our prints are used as linings for chemical resistance and then over wrapped with a fiberglass composite to provide mechanical strength. We are printing a number of filters for a hand-pumped water purification system. The PVDF filters will allow aggressive chemical cleaning. We are designing chemical storage containers used in pharmaceutical applications. raditionally these have been made from stainless steel but are susceptible to biofilm growth which require CIP (clean in place) procedures. The CIP results in rouging or rust contamination on the stainless steel surface and possible downstream process contamination. We will print these vessels in Fluorinar-C and incorporate the sanitary fittings directly into the print.”
“When we first produced the Fluorinar-H filament we had issues with warping on the base plate. This limited our prints to small low-stress shapes which still often required large brims. Printing was possible but not optimal. We began to experiment with different varieties of PVDF copolymer and found a filament that bonded well to the polyvinyl acetate (PVA) glue stick applied to the heated glass print bed. We have printed a large variety of parts in our Ultimaker 3 and our only limitation is the print volume size. Zero warpage. No heated chamber required. No expensive printer required. Now chemists and engineers are able to create functional practical parts on consumer grade printers. I’m concerned that so much of the output from 3D printers is junk. It is often hard to find exciting real world applications for plastic 3D prints beyond prototyping because the available plastics are worthless. I want to change this with Fluorinar-C PVDF.“
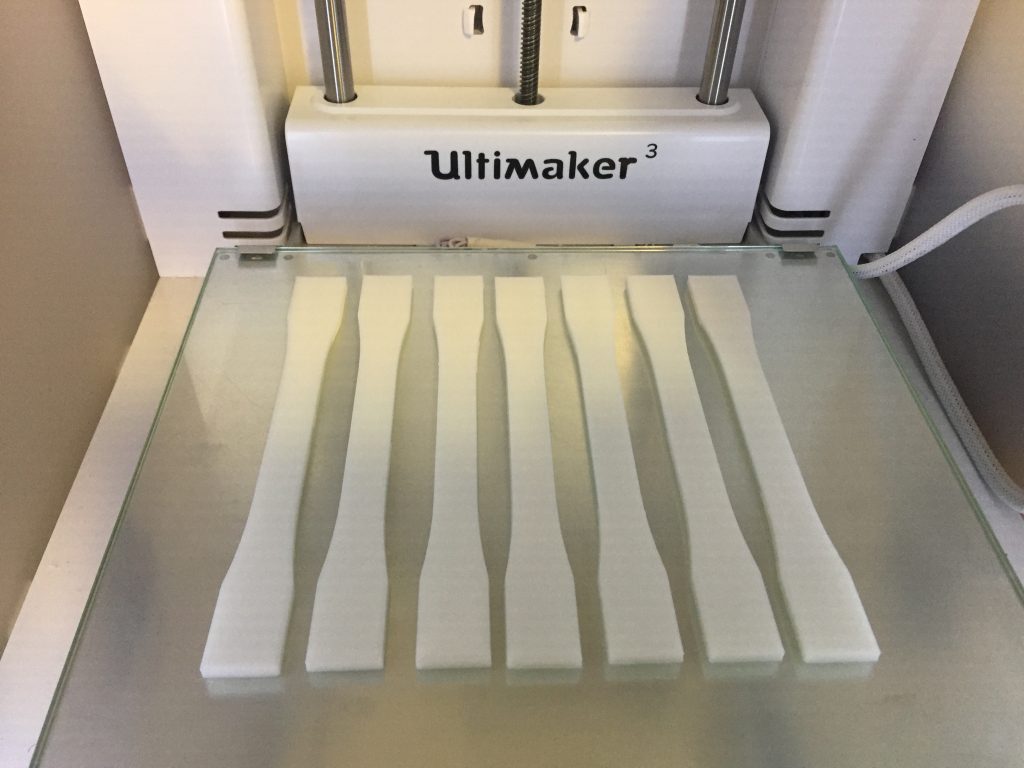
Dogbone Tensile Strength Bars Printed in PVDF on an Ultimaker 3 by Nile Polymers.
Volker Kappius of Convena told 3DPrint.com,
“Actual extrusion of PVDF filament for use in 3D printing is already an art of itself. Virgin PVDF can cause shrinkage voids in the filament under certain circumstances in the cooling after the extrusion. These voids are not only a cosmetic issue but may lead to inconsistent dimensional conformance of the printed layer line. All I can say is that PVDF runs very smoothly in standard temperature 3D printers and flows much better than for example PLA or ABS.”
Bert Ebus of reseller 3Dogg told 3DPrint.com that,
“The PVDF-C (the copolymer) is very easy to print, on practically any 3D printer. There is almost no warping and large objects are also not a problem. The PVDF-H, on the other hand, is much more difficult to print.”
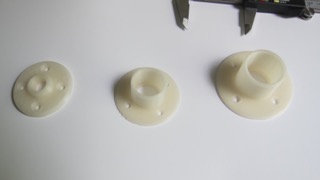
A 3D Print of the PVDF-H made on a Creatbot F160 by 3Dogg.
Settings
PVDF is not a super-high-temperature material, and the point that it can be printed on most open-material consumer 3D printers is an exciting one. It should be extruded at a temperature of 240-260ºC, where a heated bed at 100ºC can help to prevent warpage. The best print surface is generally thought to be a PEI sheet, with the use of a glue stick (But Howard and Bert Ebus print directly on the glass with a glue stick). PVDF works best when extruded relatively slowly at between 10 and 30 mm/s. Bert Ebus mentioned that his best settings on a Creatbot F160 saw him use a “nozzle temperature of 250ºC, a bed temperature of 100ºC at 20 mm/s with a brim and using Elmers Purple for adhesion.
Cost
The downside to PVDF filament is that it’s expensive. It’s not the kind of filament that an average maker is going to buy, though, – it’s much more of an industrially-suited type of material. Its excellent properties should make it worth the cost, as well. Nile Polymers sells 500 grammes Fluorinar-H filament in both 1.75 mm and 2.85 mm diameters for $100. 3DXtech sell what they claim is an ESD safe PVDF for $170 for 500 grammes. Although we’re not sure what the testing protocol is for that in a filament. Also, it is interesting that they didn’t use Quadrant’s Symalit ESD Safe granulate but apparently they opted for Kynar and then made it ESD safe by compounding it themselves? A regular spool of PVDF costs $130 at 3DXtech for 500 grammes. Both of these are Arkema Kynar based. Covena doesn’t publish prices on their filaments site but they also use the Kynar for filament but also have 3M’s Dyneon PVDF which they sell as regrind and virgin granulate. On 3Dogg a 500-gramme spool of PVDF-H and PVDF-C are 125 Euros.
Safety
Another important thing to note is that PVDF should also always be used only in an enclosed 3D printer with filters. The PVDF material should never be heated above 350ºC because then it will release toxic fumes such as hydrogen fluoride. The move towards more industrial materials should be accompanied by industrial safety standards as well.
Conclusion
The development of PVDF as a 3D printing material should open many doors for new 3D printing applications. The fact that it can be 3D printed on an average desktop 3D printer could lead to broad adoption. Industrial firms already used to working with PVDF will welcome this development. The applications that PVDF can be used for are many, and its release as a 3D printing material is another step toward expanding the use of 3D printing for industrial production.
Discuss this and other 3D printing topics at 3DPrintBoard.com or share your thoughts below.
[Images: Nile Polymers]Additional reporting by Joris Peels
Subscribe to Our Email Newsletter
Stay up-to-date on all the latest news from the 3D printing industry and receive information and offers from third party vendors.
Print Services
Upload your 3D Models and get them printed quickly and efficiently.
You May Also Like
Reinventing Reindustrialization: Why NAVWAR Project Manager Spencer Koroly Invented a Made-in-America 3D Printer
It has become virtually impossible to regularly follow additive manufacturing (AM) industry news and not stumble across the term “defense industrial base” (DIB), a concept encompassing all the many diverse...
Inside The Barnes Global Advisors’ Vision for a Stronger AM Ecosystem
As additive manufacturing (AM) continues to revolutionize the industrial landscape, Pittsburgh-based consultancy The Barnes Global Advisors (TBGA) is helping shape what that future looks like. As the largest independent AM...
Ruggedized: How USMC Innovation Officer Matt Pine Navigates 3D Printing in the Military
Disclaimer: Matt Pine’s views are not the views of the Department of Defense nor the U.S. Marine Corps Throughout this decade thus far, the military’s adoption of additive manufacturing (AM)...
U.S. Congress Calls Out 3D Printing in Proposal for Commercial Reserve Manufacturing Network
Last week, the U.S. House of Representatives’ Appropriations Committee moved the FY 2026 defense bill forward to the House floor. Included in the legislation is a $131 million proposal for...