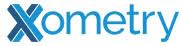
When it comes to custom manufacturing, different industries require prototypes and end-use production parts at a range of speeds and manufacturing standards, and there are many manufacturing processes to consider when designing parts for your projects. Both CNC machining and additive manufacturing techniques can be used by engineers and designers across the industries of aerospace, defense, automotive and consumer goods. Our team of engineers at Xometry has identified some of the common trends that have emerged from each industry.
Aerospace
Many aerospace engineers rely heavily on CNC machining for their custom parts. Most 3D printing for this industry is for prototyping and mock-up models. Depending on size of the design most engineers will use SLS nylon unless a large build volume is required, in which case they may opt for FDM. ULTEM is becoming a top 3D printing material for drones, but nothing rivals the precision of CNC machining for end-use aluminum, steel, and titanium aerospace parts that require very tight tolerances and superior strength to weight ratios.
Automotive
One of the most common custom parts that we see from automotive engineers are end effectors for robotics which could be used on assembly lines. Depending on the specific needs of the manufacturer, these can be 3D printed, CNC milled, or urethane cast parts. Our large scale FDM machine is perfect for making large gauges and assembly fixtures for custom parts with purpose-built contours. FDM can produce parts up to three feet in length, allowing cavities that can fully cradle a part for assembly or inspection. By building with ultralight infill the customer can get the outward geometry they need without the cost skyrocketing.
Consumer Goods & Services
Selective Laser Sintering (SLS) tends to be the most used material for models. We find that most prototyping is done with SLS since it is so commodity-priced. Additive manufacturing provides a fast and affordable solution during the product development stage, allowing for iterations to be made in just days, week after week. Once engineers and designers are ready to move to hard tooling PolyJet (rigid photopolymer) is a popular option for final fit checks in assemblies. And sometimes the 3D printed part is actually used as the final piece!
Medical
Xometry offers spec CNC manufacturing and turning in a variety of metals, including stainless steels and titanium. These tend to be popular options for medical device manufacturing. For those who are prototyping custom surgical components we often see the pairing of SLS printing for bone surrogates and DMLS stainless steel for prototyping implants in a cadaverous environment.
Xometry’s team of engineering experts have created a series of Design Guides to help you optimize your designs for each manufacturing process:
- CNC Machining & Turning
- Direct Metal Laser Sintering (DMLS)
- Fused Deposition Modeling (FDM)
- Metal Binder Jetting
- PolyJet 3D Printing
- Selective Laser Sintering (SLS)
- Sheet Metal Fabrication
Manufacturing has never had so many options, and the combination of 3D printing and traditional subtractive manufacturing methods has created an unprecedented level options and flexibility to move quickly from prototype to production while saving time and money. Xometry.com offers instant online pricing in all their technologies, all that is required is a 3D model.
For more information on Xometry’s Instant Quoting Platform, Manufacturing Partner Network or processes, visit Xometry.com. Discuss in the Xometry forum at 3DPB.com.
Subscribe to Our Email Newsletter
Stay up-to-date on all the latest news from the 3D printing industry and receive information and offers from third party vendors.
Print Services
Upload your 3D Models and get them printed quickly and efficiently.
You May Also Like
Reinventing Reindustrialization: Why NAVWAR Project Manager Spencer Koroly Invented a Made-in-America 3D Printer
It has become virtually impossible to regularly follow additive manufacturing (AM) industry news and not stumble across the term “defense industrial base” (DIB), a concept encompassing all the many diverse...
Inside The Barnes Global Advisors’ Vision for a Stronger AM Ecosystem
As additive manufacturing (AM) continues to revolutionize the industrial landscape, Pittsburgh-based consultancy The Barnes Global Advisors (TBGA) is helping shape what that future looks like. As the largest independent AM...
Ruggedized: How USMC Innovation Officer Matt Pine Navigates 3D Printing in the Military
Disclaimer: Matt Pine’s views are not the views of the Department of Defense nor the U.S. Marine Corps Throughout this decade thus far, the military’s adoption of additive manufacturing (AM)...
U.S. Congress Calls Out 3D Printing in Proposal for Commercial Reserve Manufacturing Network
Last week, the U.S. House of Representatives’ Appropriations Committee moved the FY 2026 defense bill forward to the House floor. Included in the legislation is a $131 million proposal for...