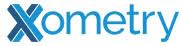
Additive manufacturing is an effective way to produce both prototype and production parts, often at a fraction of the price and much faster than traditional manufacturing processes.
Xometry’s advanced manufacturing platform provides a streamlined way for engineers and designers to get instant pricing, lead times and manufacturability feedback. All it takes is a 3D CAD file.
Xometry uses industrial 3D printing technologies to manufacture custom parts. Unlike the household desktop machines, industrial printers often cost hundreds of thousands of dollars. So what’s the difference?
Director of Project Engineering, Greg Paulsen, says “Consistency and reliability are essential for our customers. I can build one part in a process like FDM, then weeks later the customer can be assured that if they ordered a dozen more they would get the same product they expected.”
Industrial machines are tuned, regularly maintained, and run with standardized materials with reliable material properties. That does not mean that choices are limited though. Industrial 3D printing offers many materials and processes to fit different jobs. Here are few of the most popular additive materials and their common applications:
Nylon – Selective Laser Sintering (SLS)
Xometry calls SLS nylon the 80% material, meaning 80% of the time you will probably be prototyping with this method! SLS builds parts in a heated powder bed where a laser etches the part’s profile, building layer by layer. Nylon itself is heat and chemical resistant and has end-use durability for engineered applications. Recommended build size is up to about a foot, although you can build larger, and since there is no need for support structures the process handles complex parts with ease. Finishes are limited to dyeing in select colors and media tumbling. If you need something mechanically stiff and lightweight you may want to consider the nickel plating option as well!
ABS & ASA – Fused Deposition Modeling (FDM)
Is your part mechanically oriented with walls over 2mm thick? No snap tabs? If that is the case then choosing Fused Deposition Modeling (FDM) could be your go-to material. FDM builds parts by extruding a melted filament which zig-zags back and forth to form the shape of the part. The most common materials are ABS or ASA, which have very similar properties as a general use plastic. The materials allow for a variety of colors as well as a very large build volume to large parts up to 3 feet or production runs of smaller parts. There is even a static dissipative material called ABS-ESD7 which is useful for production jigs.
ULTEM 9085 & 1010 – Fused Deposition Modeling (FDM)
Moving to more advanced materials for tough environments, FDM ULTEM is designed to withstand over 400°F in temperature and is a very strong thermoplastic option for 3D printing. Usually this material is used as part of a manifold or system that is near engine heat. Due to the material’s fire resistance it is also an ideal option for battery housings, robotics, and drone bodies.
Aluminum Alloy – Direct Metal Laser Sintering (DMLS)
Sometimes the part just needs to be metal. Direct Metal Laser Sintering (DMLS) makes parts by melting a powder bed of metal, layer-by-layer, to build a metal geometry from CAD. This is a great way to get a complex part, or something that would eventually be milled from a casting, without major setup and tooling fees. Although Xometry 3D prints several metals, Aluminum has become a favorite because it is lightweight and can be post processed via drilling or tapping. DMLS may also be much more economical upfront than traditional milling if the geometry is complex.
For more information on 3D printing materials and finishes, and to consult with Xometry’s team of expert engineers, visit www.xometry.com. Discuss in the Xometry forum at 3DPB.com.
Subscribe to Our Email Newsletter
Stay up-to-date on all the latest news from the 3D printing industry and receive information and offers from third party vendors.
Print Services
Upload your 3D Models and get them printed quickly and efficiently.
You May Also Like
3D Printing News Briefs, July 2, 2025: Copper Alloys, Defense Manufacturing, & More
We’re starting off with metals in today’s 3D Printing News Briefs, as Farsoon has unveiled a large-scale AM solution for copper alloys, and Meltio used its wire-laser metal solution to...
3DPOD 260: John Hart on VulcanForms, MIT, Desktop Metal and More
John Hart is a Professor at MIT; he´s also the director of the Laboratory for Manufacturing and Productivity as well as the director of the Center for Advanced Production Technologies....
3D Printing News Briefs, June 28, 2025: Defense Accelerator, Surgical Models, & More
In this weekend’s 3D Printing News Briefs, 3YOURMIND was selected to join an EU Defense Accelerator, and PTC has announced model-based definition (MBD) capabilities within Onshape. Finally, a study out...
EOS in India: AM’s Rising Star
EOS is doubling down on India. With a growing base of aerospace startups, new government policies, and a massive engineering workforce, India is quickly becoming one of the most important...