Ian Pallister, a Professor of Medicine at Swansea and a consultant at Morriston Hospital, used 3D printing to create a full-scale model of the lower body of a bomb victim in disturbing but potentially lifesaving detail. He designed the model as a training simulator to help military surgeons get realistic, hands-on experience treating someone with severe injuries like those caused by an explosion. The 3D printed victim has lost most of one leg, and actually “bleeds” arterial blood in the form of colored water, allowing surgeons to monitor blood pressure and control blood loss.
Pallister began designing the model in 2014, receiving funding from a competition launched by the Defence Science and Technology Laboratory’s Centre for Defence Enterprise. The competition asked participants to come up with new ideas for the use of simulation in military medical training. It was the perfect opportunity for Pallister, who had already been working on the development of better surgical models.
With the funding he received, Pallister formed a university spin-off company called Trauma Simulation Ltd. and began working on prototype models using the CT scans of a volunteer patient. The scans were used to create 3D printed molds which were then used to cast models in silicone, which resembles human tissue. The bones were fabricated with resin.“I began by making simple models tailored for the MSc Trauma Surgery programme,” Pallister said. “We’ve used simulation for a long time but we tend to rely on plastic bones with a simulated fracture, so we can teach people simple step one-two-three type surgical procedures. That is vitally important but the potential for extending the scope and realism of the simulation into more complex decision-making and time-critical intervention was very clear.”
The 3D printing was done by the National Centre for Product Design and Development Research (PDR) at Cardiff Metropolitan University, and MBI (Wales) Ltd, which makes maxillofacial prosthetics as well as doing special effects work for the film industry, helped create the models.
“I worked with colleagues in Morriston Hospital, who were my sounding boards for advice and help to get the artificial circulation to work and in measuring blood pressure,” said Pallister. “In simulation terms this is very novel. There are other medical emergency simulators but they work purely through computer controls. To be effective in training, the experience must mimic reality, so the participants become immersed in what they have to do.
“The need to control simulated bleeding in this model in the presence of such realistic injuries, while operating on tissues which feel so lifelike, brings a dimension to training which has never been possible before. The goal is to prepare personnel so effectively that when they have to do it for real it won’t be for the first time because the simulation is so true to life.”
Two years later, Pallister’s work has been recognized with the Sun Military Award for Innovation. The Sun Military Awards, which were recently presented in their ninth annual ceremony, were given to British citizens who have made outstanding contributions to the United Kingdom’s armed forces. This year marked the debut of the Innovation Award, designed to honor an individual or group responsible for creating lifesaving or battle-winning technology. Pallister was nominated by Sun readers and selected as a winner by a judging panel of former military personnel and celebrities.
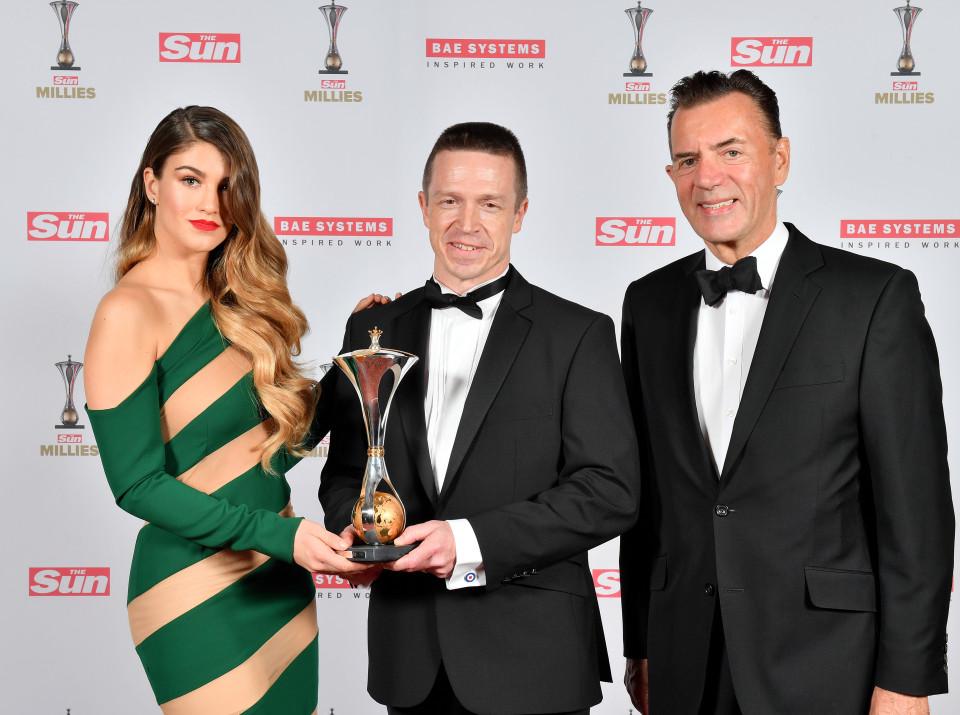
Ian Pallister receives the Innovation Award from former Dragons’ Den star Duncan Bannatyne and model Amy Willerton. [Image: News Group Newspapers Ltd]
“I am humbled to be in the presence of so many brave people,” said Pallister.
Pallister’s work is far from finished – he is currently developing a set of simple models for the National Health Service, and is working towards the creation of a full-body trauma simulator that will allow medical professionals to train in resuscitation and emergency surgical procedures.
“It’s called immersive simulation so the whole environment represents reality as closely as possible,” he said. “Nobody has enough personal experience to learn everything from experience. It’s a bit like landing an aircraft on water. Hopefully you never have to do it, but if you do, you have to know what to do.”
Discuss in the 3D Printed Trauma Model forum at 3DPB.com.
[Sources: Swansea University / BBC]
Subscribe to Our Email Newsletter
Stay up-to-date on all the latest news from the 3D printing industry and receive information and offers from third party vendors.
Print Services
Upload your 3D Models and get them printed quickly and efficiently.
You May Also Like
Making 3D Printing Personal: How Faraz Faruqi Is Rethinking Digital Design at MIT CSAIL
What if your 3D printer could think more like an intelligent assistant, able to reason through a design idea, ask questions, and deliver something that works exactly the way the...
Reinventing Reindustrialization: Why NAVWAR Project Manager Spencer Koroly Invented a Made-in-America 3D Printer
It has become virtually impossible to regularly follow additive manufacturing (AM) industry news and not stumble across the term “defense industrial base” (DIB), a concept encompassing all the many diverse...
Heating Up: 3D Systems’ Scott Green Discusses 3D Printing’s Potential in the Data Center Industry
The relentless rise of NVIDIA, the steadily increasing pledges of major private and public investments in national infrastructure projects around the world, and the general cultural obsession with AI have...
Formlabs Teams Up with DMG MORI in Japan
In late June, Nick Graham, Chief Revenue Officer at Formlabs, announced on LinkedIn that the company had partnered with DMG MORI, one of the world’s leading machine tool companies, to...