While many people may be ringing in the New Year with some sort of (hopefully legal) fireworks this coming weekend, no one’s display will beat that of NASA, which is saying farewell to 2016 with an appropriately fiery blast. We’ve been following the agency’s endeavor to build a completely 3D printed rocket engine for quite a while now, and our excitement is re-ignited every time NASA announces another successful test of a newly completed component.
The new combustion chamber NASA tested out recently wasn’t 3D printed (yet), but it was a big step forward from the chamber they had been using for previous tests. Those tests were carried out using an ablative combustion chamber, which erodes when burning, changing internal pressures and only allowing for a ten-second firing time. The newly designed combustion chamber used in the most recent tests was a regeneratively cooled chamber, capable of being fired for much longer.
In the latest tests, the engine was fired for 30 seconds (although it could have gone longer), allowing the engineers at NASA’s Marshall Space Flight Center to obtain, for the first time, information about how the engine’s 3D printed components perform together during a longer-duration burn. With the exception of the new combustion chamber, all of the major components in the test engine were 3D printed, including the fuel injector, fuel turbopump, valves, and more.
“A system is not just a sum of parts put together. It’s a product of the interaction of the parts. What we’re trying to do is understand and manage those interactions,” said Nick Case, lead system analyst for the project. “At the same time, we must understand the performance of the individual 3-D printed pieces. That’s what this test allowed us to do.”
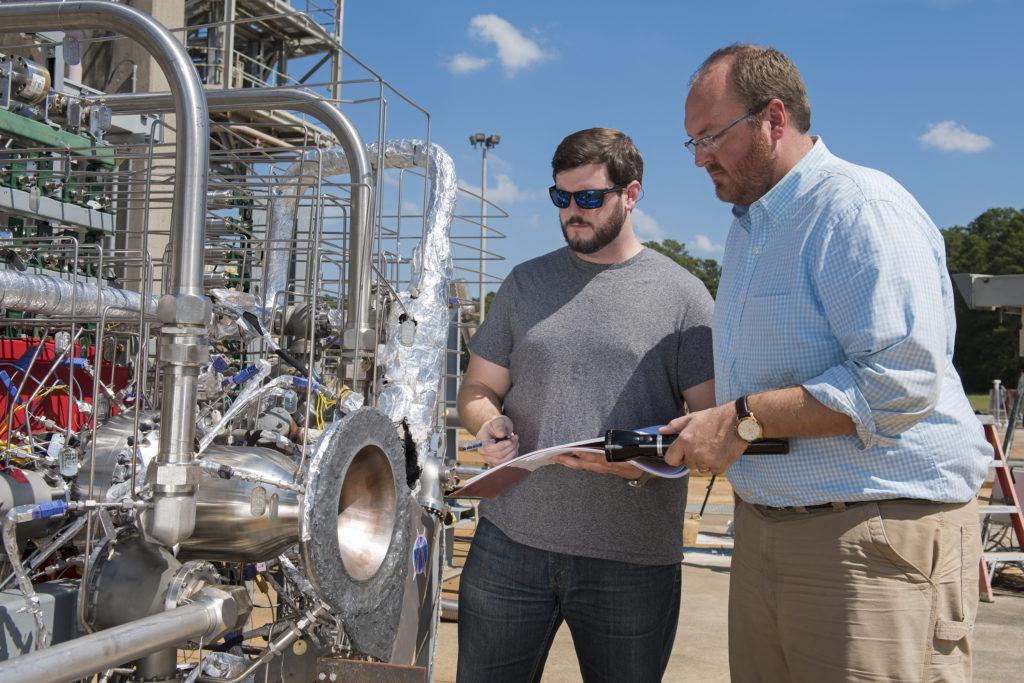
Andrew Hanks (L) and Graham Nelson examine the newest combustion chamber for NASA’s 3D printed rocket demonstrator engine. [Image: NASA/MSFC/Charles Beason]
Testing the new combustion chamber with the 3D printed components was crucial because the chamber is where fuel turns to hot gas and provides thrust – 35,000 pounds of it, which is what the engine is designed to produce. In the most recent set of tests, liquid oxygen and liquid hydrogen entered the chamber at around 400° below zero Fahrenheit and exited it at around 6,000°.
“With our new chamber and the longer firings, we are able to create a test environment that is much closer to our design point for this project,” said test lead Andrew Hanks.
The next step, according to NASA, will be the addition of a 3D printed oxidizer turbopump, created in collaboration with the NASA Space Technology Mission Directorate’s Game Changing Development program, which is also funding the development of a 3D printed combustion chamber. The engineering team hopes to be able to test the 3D printed chamber in the summer of 2017.
While there are no plans to send the demonstrator engine into space, the project will, once completed, show that 3D printed rocket engine components are viable and even preferable to traditionally manufactured ones, and will pave the way for future engines and parts to be fabricated using 3D printing. In addition to developing the next set of 3D printed parts, the engineering team is also working on testing the engine with different propellant combinations, including oxygen and methane. Those two gases are being considered as fuel for deep-space vehicles and landers, as it may be possible to produce them on Mars. You can see a video of the latest test firing below:
Discuss in the NASA forum at 3DPB.com.
[Source: NASA]
Subscribe to Our Email Newsletter
Stay up-to-date on all the latest news from the 3D printing industry and receive information and offers from third party vendors.
You May Also Like
Gorilla Sports GE’s First 3D Printed Titanium Cast
How do you help a gorilla with a broken arm? Sounds like the start of a bad joke a zookeeper might tell, but it’s an actual dilemma recently faced by...
Nylon 3D Printed Parts Made More Functional with Coatings & Colors
Parts 3D printed from polyamide (PA, Nylon) 12 using powder bed fusion (PBF) are a mainstay in the additive manufacturing (AM) industry. While post-finishing processes have improved the porosity of...
$25M to Back Sintavia’s Largest Expansion of Metal 3D Printing Capacity Since 2019
Sintavia, the digital manufacturing company specializing in mission-critical parts for strategic sectors, announced a $25 million investment to increase its production capacity, the largest expansion to its operations since 2019....
Velo3D Initiates Public Offering in a Bid to Strengthen Financial Foundations and Drive Future Growth
Velo3D (NYSE: VLD) has been among a number of publicly traded 3D printing firms that have attempted to weather the current macroeconomic climate. After posting a challenging financial report for 2023,...