UK Business: Innovate 2 Make Merges with Progressive Technology, Creating Manufacturing Powerhouse with Metal 3D Printing & Traditional Processes
Something’s in the air lately for mergers and acquisitions, it would seem, with the 3D printing realm continuing to power up in numerous and surprising ways, growing ever stronger and bigger. Just recently we’ve seen both industry titans GE and HP making major announcements, but plenty more continues on the front for smaller startups and businesses, with the latest coming from the UK as Newbury-based Progressive Technology and Birmingham’s Innovate 2 Make (i2M) merge.
With the intention to create a powerful manufacturing entity in the precision machining and metal 3D printing industry, the two companies have come together this week under the name Progressive Technology. The new team has their eyes on £2 million in new sales for its first year, and they may be adding ten new jobs into the mix as well.
Progressive Technology will create an end-to-end supply solution for customers looking for low to medium volume production of complex components typically used in high performance environments such as Formula 1 and the aerospace sector. The company will also cater to the medical field, allowing clients there to experience higher quality as well as better control over production, and greater speed and efficiency overall.
“The merger is a natural progression of a working relationship that has been in place for a couple of years now,” explained Ross Pinchin, Managing Director of Progressive Technology. “We have a number of shared customers who use us to manufacture parts for F1, with i2M providing the metal 3D printing expertise and our multi-axis machining capability delivering the secondary operation.”
“By bringing the two firms together we’ve created – what we believe – is the largest single source full service machining and metal 3D printing solution in the UK. It’s a bold move, but one that is already creating significant demand from customers who want easier access to this new technology, as well as the ability to reduce logistics costs, minimise supply chain disruption and shorter lead times for parts.”
As the two companies come together, we will see again the idea that traditional fabrication methods don’t have to be thrown out the window—manufacturing revolution or not. And while many heartily embrace 3D printing and all the transformations it entails, they also understand it can’t cover every need.
“When we first started talking about 3D printing, or additive manufacturing as it is sometimes known, it was about replacing traditional manufacturing processes,” said Mike Kelly, Director at Innovate 2 Make. “That’s no longer the case, as on its own it just doesn’t meet what customers are asking for. It is an extremely valuable discipline for manufacturing short batch, complex parts, but will always require secondary operations like CNC machining to give you the tolerance or finish you are after.
“This is why this merger is so exciting. We can now offer the end user a complete service, from using metal 3D printing in the initial production of the component to tapping into Progressive Technology’s fantastic capabilities in Newbury.”
Along with what Kelly describes as ‘one of the largest inspection and quality assurance departments ever seen in a SME,’ equipment at Newbury includes:
- A bank of 5-axis CNC machines
- Two wire EDM machines
- Wire and spark eroders
- State-of-the-art milling technology
Pinchin’s father originally established his small toolmaking business in 1977, establishing a company that Formula 1 teams relied on for important components, supplied ‘eighty percent off the grid.’ That hard work and quality has evolved into today’s Progressive Technology, which is one of the rare companies you will find open 24/7. With millions invested, they are busy creating a composite and world class machining center at their Hambridge Lane address—where the current team says they hope to recruit some of the industry’s ‘brightest minds and budding engineers.’ Last year, they saw sales rise to £6.8 million, with a projection for over £9 million at the end of 2016 (translating to nearly $12 million USD).
The two companies coming together should be a recipe for success, as Innovate 2 Make, founded in 2012, has also been in a state of growth. Founded by Mike Kelly and Ian Campbell, they took what was originally an ‘industrial unit’ in Kings Norton and transformed it into a center for 3D printing with metal. There, they’ve offered both prototyping services as well as low volume production of parts for the aerospace, automotive, defense, F1 and medical sectors. They also have rare equipment on hand in the form of two EOS M280 400 watt laser melting platforms, accompanied by a full materials lab and inspection unit.
“We are delighted to be joining forces with Progressive Technology and delivering a much sought-after solution to industry,” said Kelly. “In the short-term we will continue to operate out of Birmingham, but there may be opportunities later on to consolidate all of our activities under one roof.
“Importantly, we had seen a huge amount of work offshored due to a lack of capability like the one we’ve just created. We’ll now be working extremely hard to bring those contracts back home.”
The team has already begun work with the cycling sector, and reports that Campbell will be overseeing Mirada Performance Products, launching as a spin-out to bring forth both innovation in design as well as production-grade components. They will combine metal 3D printing along with traditional multi-axis machining for production of bespoke bike frames and components. As they say goodbye to expensive tooling, the team points out that what they are getting ready to do at Mirada would have been impossible previously with just traditional processes in place.
As the companies adjust to their extremely recent merger, they will use their respective strengths and new combined capacity to create additional work in F1, as well as targeting their expanding customer base in industries such as that of automotive, aerospace and renewables. See Progressive Technology for more information on what the companies will be offering to the industry, and if you’d like to discuss this topic further, head over to the Progressive Technology & 3D Printing forum at 3DPB.com.
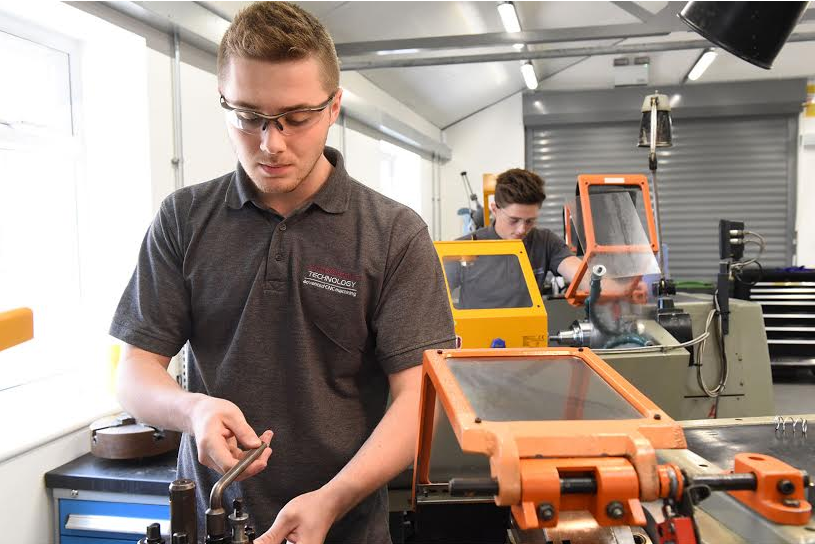
Progressive Technology’s investment in youth includes a dedicated training facility at their Newbury facility.
Subscribe to Our Email Newsletter
Stay up-to-date on all the latest news from the 3D printing industry and receive information and offers from third party vendors.
Print Services
Upload your 3D Models and get them printed quickly and efficiently.
You May Also Like
3D Printing News Briefs, July 2, 2025: Copper Alloys, Defense Manufacturing, & More
We’re starting off with metals in today’s 3D Printing News Briefs, as Farsoon has unveiled a large-scale AM solution for copper alloys, and Meltio used its wire-laser metal solution to...
3DPOD 260: John Hart on VulcanForms, MIT, Desktop Metal and More
John Hart is a Professor at MIT; he´s also the director of the Laboratory for Manufacturing and Productivity as well as the director of the Center for Advanced Production Technologies....
3D Printing News Briefs, June 28, 2025: Defense Accelerator, Surgical Models, & More
In this weekend’s 3D Printing News Briefs, 3YOURMIND was selected to join an EU Defense Accelerator, and PTC has announced model-based definition (MBD) capabilities within Onshape. Finally, a study out...
EOS in India: AM’s Rising Star
EOS is doubling down on India. With a growing base of aerospace startups, new government policies, and a massive engineering workforce, India is quickly becoming one of the most important...