Cancer Survivor with 3D Printed Jaw Prosthesis Feels Good About Life Again, Inspires Doctor & 3D Designer
I’m probably not the only one who as a child more than once shouted, “That’s not fair!” receiving in return the frequent and typical parental response: “Well, life’s not fair.” The gravity of that frustrating statement can’t really kick in, however, until you’ve lived long enough to experience the curveballs, some minor—and some simply terrible—with no magical force holding you in a protective bubble, doling out fairness. Crises and tragedies strike and we cope the best that we can.
For Shirley Anderson, coping has meant focusing on the love he has for his wife of fifty years—and for being one half of one of those few lucky couples that make it that far today. Coping meant being grateful for two kids, three grandchildren—and for being alive. And now, thanks to the persistence and innovation of his doctor forging ahead, seeking new technology and new techniques, his wife is able, with joy, to see him write: “I have my life going just as I want.”
Upon hearing the story of Shirley Anderson and his outcome, this is inspiration in the truest sense. After discovering that fateful tumor on his tongue in 1998, Shirley sought medical treatment and was told that it was cancerous. The typical rounds of surgery and radiation therapy ensued, but it ravaged his lower facial area.
“It’s kind of been one bad thing after another,” says his wife, Della, emphasizing that most of the challenge was indeed a result of the radiation.
Treatments for cancerous tumors often wreak havoc on the rest of the body, and as doctors tried different avenues, not all went well. Shirley’s facial tissue was destroyed after a radium implant in his jaw, and after surgeons removed some of his chest muscle to recreate his face, and failed, there were disappointments and challenges to suffer through—with eating and speaking becoming nearly impossible. Shirley lost 80 pounds because he could not eat solid food, and to communicate he began writing on a small whiteboard.
Years of challenge went on, and then in 2012, Shirley met with Dr. Travis Bellicchi, a maxillofacial prosthetics specialist, and a resident at the Indiana University School of Dentistry. Working with Shirley would go beyond the scope of anything Dr. Bellicchi had ever imagined, or taken on.
Because of the complexity of the damage done to Shirley’s jaw, a prosthetic four times the normal size would be required. Both doctor and patient committed to the process, however, and that meant enduring trial and error along the way. First, he attempted making a cast in plaster. Then, a replica in gypsum, sculpted in clay. Using that, a final silicone model was made and then handpainted to match Shirley’s exact skin tone. While it’s important to point out that this is the general, relied upon method, it was a difficult process all around and the results were less than perfect in terms of comfort. They would have to find another way for Shirley.“The traditional process for impression, sculpting, moldmaking, and aesthetic characterization is a laborious task,” Dr. Bellicchi explains. “The prosthesis was so uncomfortable that Shirley couldn’t wear it for more than four hours at a time, it was so heavy that it often slipped down, and the surface lacked realistic skin details. I knew there was a need for a digital solution.”
And soon, he discovered a much better route via Professor Zeb Wood, a lecturer at the School of Media Arts and Sciences, and a big fan of digital design and 3D printing. He was more than glad to introduce Dr. Bellicchi to the possibilities available via the digital world of scanning, sculpting, moldmaking, and 3D printing. Not tasked with breathing through a straw while plaster dried on his face, Shirley only had to watch on as they made a virtual model of himself, referred to as the ‘virtual patient.’
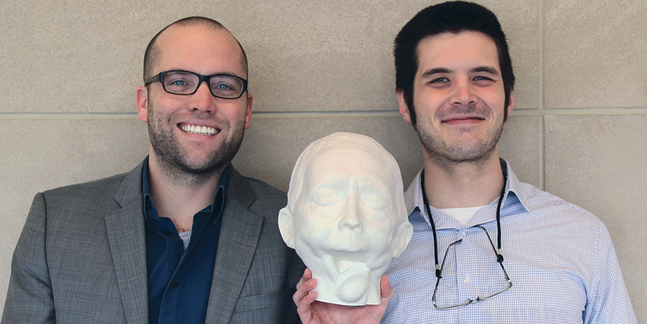
Professor Zebulun Wood (left) and student Cade Jacobs (right) used digital methods to produce 3D models of Shirley’s prosthesis. (Photo: IUPUI)
Cade Jacobs, an IU student, made the design for the facial prosthesis in ZBrush, offering up some of the greatest benefits of the digital world, as 3D sculpting software created the design in just a fraction of the time, and without any of the headache (literally) to the patient. On a Formlabs 3D printer, the team then made the 3D printed mold which was ready for final casting. According to the team, while they did at first attempt to use an FDM printer, with the resin on the Form 2 they experienced better details (right down to wrinkles and pores) and a watertight model.
“They really couldn’t believe how easy it was. They had been struggling to get the same results for a long time when they were using the traditional process,” said Jacobs. “I was filled with half-awe and half-frustration that they’ve been doing it the wrong way for so long.”
And the ultimate result for Shirley? He’s experiencing much greater comforter thanks to the lightweight qualities of the prosthetic, allowing him to breather more easily and wear the mold longer. It features an outside margin with a ‘feather edge,’ tapered in silicon and much more natural all around.
“We’ve used 3D printing to replace about 75 to 80% of the process in traditional prosthetic fabrication,” said Dr. Travis Bellicchi. “We started with Shirley Anderson. And we’ve expanded that workflow to several other patients.”
Dr. Bellicchi was so inspired by the process that they have developed a special team to help others who need prosthetics, and ones that might be challenging.
“It’s a privilege to have an opportunity to work with a patient like Shirley because Shirley makes the process collaborative,” says Dr. Bellicchi. “Shirley participates in my work to improve his prosthesis. Although it’s likely the most significant challenge I will ever face in my prosthetic career, I think it may be the most rewarding.”
Shirley has been able to enjoy wearing the prosthetic now, in place of the surgical mask he was previously wearing to cover up his jaw area.
“In someone’s career—my field—you may never be challenged with a prosthesis of this nature,” said Dr. Bellicchi, emphasizing, however, that as a rule maxillofacial prosthetics requires customized solutions for every patient.
The IU team has applied this groundbreaking method to six other patients, including a patient for whom they have made a prosthetic ear. They continue to seek new candidates as they continue with this very important work. For more details on “the Shirley Technique,” check out the video below from Formlabs. Do you know anyone with a 3D printed prosthetic, or perhaps someone who would benefit from one? Let’s discuss this amazing project further over in the 3D Printed Jaw Prosthetic forum at 3DPB.com.
[Source: Formlabs]
Podcast: Play in new window | Download
Subscribe to Our Email Newsletter
Stay up-to-date on all the latest news from the 3D printing industry and receive information and offers from third party vendors.
Print Services
Upload your 3D Models and get them printed quickly and efficiently.
You May Also Like
Making 3D Printing Personal: How Faraz Faruqi Is Rethinking Digital Design at MIT CSAIL
What if your 3D printer could think more like an intelligent assistant, able to reason through a design idea, ask questions, and deliver something that works exactly the way the...
Reinventing Reindustrialization: Why NAVWAR Project Manager Spencer Koroly Invented a Made-in-America 3D Printer
It has become virtually impossible to regularly follow additive manufacturing (AM) industry news and not stumble across the term “defense industrial base” (DIB), a concept encompassing all the many diverse...
Heating Up: 3D Systems’ Scott Green Discusses 3D Printing’s Potential in the Data Center Industry
The relentless rise of NVIDIA, the steadily increasing pledges of major private and public investments in national infrastructure projects around the world, and the general cultural obsession with AI have...
Formlabs Teams Up with DMG MORI in Japan
In late June, Nick Graham, Chief Revenue Officer at Formlabs, announced on LinkedIn that the company had partnered with DMG MORI, one of the world’s leading machine tool companies, to...